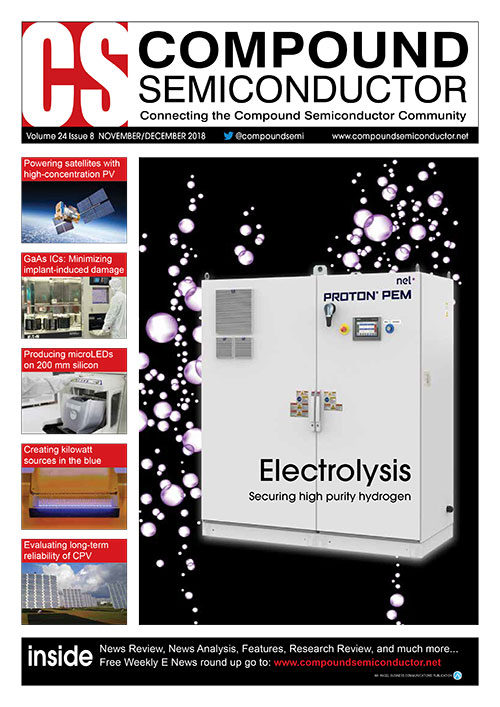
Creating kilowatt sources in the BLUE
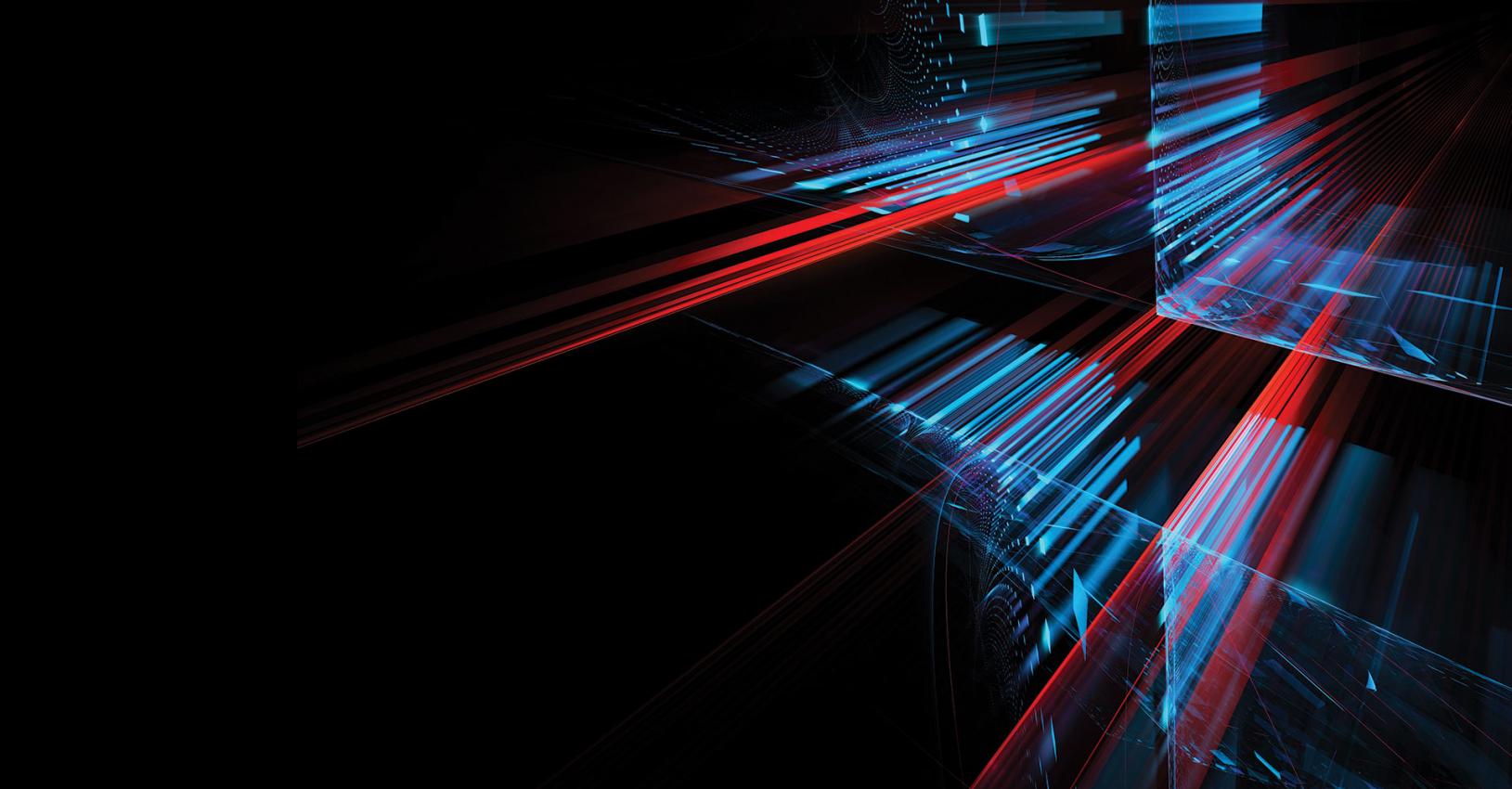
Adopting techniques for improving the performance of the infrared laser creates powerful, reliable blue sources
BY HARALD KOENIG FROM OSRAM OPTO SEMICONDUCTORS
The laser is an ideal tool for efficient manufacturing. It is highly flexible, offers negligible changeover times, and is free from wear, thanks to its non-contact mode of operation. What’s more, improvements in laser diode performance have enabled this source to be efficient, operate either continuously or with a train of pulses that can be as short as a few femtoseconds, and provide such versatility that it can machine nearly every material.
Today, its only significant drawback is its unsuitability for processing highly reflective materials, such as gold, non-ferrous metals and particularly copper. This class of material switches from being weakly absorbing in solid form, to strongly absorbing in a liquid state, causing the melt to blow out in an uncontrollable manner. With copper, an additional issue is that it has a very high thermal conductivity, which makes it challenging to inject enough power into this material to process it. So, in short, processing highly reflective materials with infrared lasers is far from easy – and with copper it is incredibly difficult.
This issue matters, as it is a major impediment to the growth of electric-powered transportation. Manufacturers of electric vehicles need to process copper, including securely joining it to other materials and applying it as a cladding.
The solution is to reduce the wavelength of the laser. At wavelengths below 500 nm the absorption of these highly reflective materials is far higher: in copper, it is 12 times higher, and in gold it is up by a factor of 40.
However, before shorter-wavelength lasers can be used in industry, there needs to be an increase in the power produced by these sources. To realise this, our team at Osram Opto Semiconductors, working in close partnership with colleagues at Laserline, Coherent DILAS Diode Lasers and the Max Born Institute for Nonlinear Optics and Short Pulse Spectroscopy, is developing kilowatt-power direct blue lasers through a project called BlauLas, which is funded by the German Federal Ministry of Education and Research (BMBF, FKZ13N13900).
The successes that we are having will do more than just improve the capability of lasers for processing highly reflective materials. They will also support the development of blue sources for under-water materials processing, and powerful white-light sources based on the pumping of a phosphor with a short-wavelength laser.
From infrared to blue
We have no intention of re-inventing the wheel. Instead, our plan is to replicate the success of infrared laser diodes. When these are in the form of bars, they can produce a 200 W output; and when stacked together for industrial applications, they can form multi-kilowatt sources.
Today, for blue laser diodes, the commercially available sources are limited to single emitters in metal housings. These MOCVD-grown individual laser diodes, manufactured on 2-inch GaN substrates, produce just a few of watts of power in the wavelength range of 450 nm.
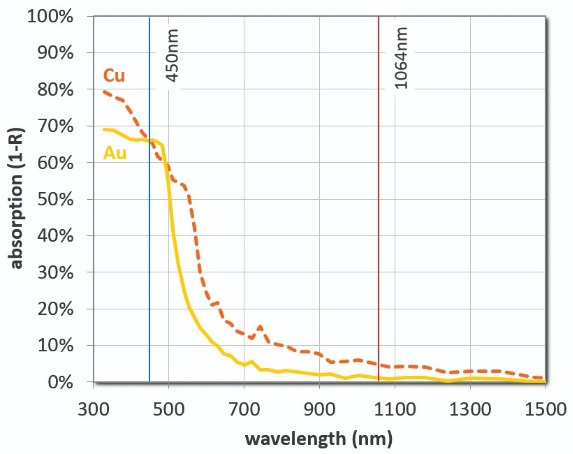
For the processing of copper and gold, it is far better to use a laser that emits in the blue than the infrared, due to the far higher level of absorption at these shorter wavelengths.
It is impractical to refine these single emitters so that they produce far, far higher output powers. Instead, our plan is to produce bars, using them as the basis for developing fibre-coupled laser systems with an output in the range of 1 kW. If we succeed, we will have increased the output power of a blue direct diode laser source by more than an order of magnitude.As a first step towards a kilowatt source, we have targeted the fabrication of a blue, 450 nm laser that continuously emits light and produces an optical output of more than 50 W when mounted on an actively cooled heat sink. To succeed, we had to ensure that the growth of epiwafers led to high-quality, homogenous epitaxial layers. This is not easy – today there exists no commercial blue-emitting laser bar on the market, due to many emitters with poor performance on the chip.
Our epiwafers, which contain as few defects as possible, have been fabricated into a range of ridge waveguide laser bars, using industry-standard chip processes. These bars, which have 23 emitters, are capable of a 98 W output when driven at 60 A. Maximum conversion efficiency is 46 percent at target operation point of 50 W.
Combining bars
To increase the output of the source, we have combined the output of several bars.
Our efforts, led by Laserline, have involved a stack of ten diode laser bars, a beam transformation system, matching optics, a focusing lens and a common fibre. With this set up it is possible to study the optical path of the laser beam from the diode facet to the optical fibre.

Osram is raising the bar for the efficiency of blue laser diodes.
Engineers at Laserline have directed the radiation of two stacks into one fibre, using so-called polarization coupling. The results of this are tremendous: output power can be doubled while maintaining beam quality. Using this approach, the source produces an output of 730 W.This set-up welds pure copper while realising very stable heat conduction. Additional demonstrations have included the welding of gold-plated copper and fibre-reinforced plastic preforms with infrared transparency, and the joining of pure copper and steel and copper to copper.
The feasibility of kilowatt powers is clearly a breakthrough. However, this does not guarantee that the source is suitable for use in industry, which may have requirements related to the size of the source and the quality of the output. To this end, efforts led by Coherent DILAS have been directed at: decreasing the volume of the source; reducing its complexity compared with that of a single emitter; and reducing the beam parameter product, which is a figure-of-merit for the quality of the laser beam – it reveals how well the output can be focused to a small spot. Goals in this part of the project have included realising a source with a high brilliance, so it is capable of efficient coupling into a fibre with a small diameter.
Like the effort led by Laserline, bars have been used to reduce the volume of the source. The alternative – a stack of single emitters – is avoided, because it would lead to a complex, cumbersome system that is challenging to optimally align. However, for Coherent DILAS the requirements, in terms of beam-parameter product, are more challenging. The high output from the Laserline system is capable of coupling to a fibre with a high diameter, but that under development from Coherent DILAS has to couple into a small-diameter fibre high-brilliance sources at lower output power.
Coherent DILAS has much expertise in combining the output of various emitters – at the start of the project it was already capable of using this approach to produce a collimated output power of about 80 W. This power came from using integrated packages with up to 20 individual emitters, and aligning the divergent radiation from each of them with their own aspherical lens. A collimated 80 W output came from polarisation-combining two modules.
Replacing individual emitters with diode laser bars promises to lead to substantial simplification. Rather than using many lenses, just two are needed to adjust all the beams from one bar. However, to ensure success, the laser bars must be specially tuned to the beam quality of the target fibre, so that they can be combined without the need for expensive beam shaping optics. A key requirement is that, for all the emitters on a bar, the collimation of the fast and slow axis is in parallel.
Note that this approach to simplification is not a new idea. It is already used with infrared diode laser bars. Modules are made by mounting several diode laser bars with the necessary optics on a common base plate. Powerful lasers result from combining up to eight base plates in a single unit.
Our team has taken this approach with 450 nm lasers. It reaps rewards: even without additional components for symmetrizing the beam, the emission profile of the blue diode laser is good enough for efficient coupling into a common fibre. Compared with a 25 W module of individual emitters housed in standard housing – so-called TO-cans – volume is slashed by a factor of 25, while power increases from 25 W to 35 W. In addition to these gains, there is greater simplicity. Single-emitter modules require individual alignment of approximately 30 optical elements, while our tailored bar approach only needs three optical elements to be actively aligned.
We have also produced a more powerful module by mounting nine blue-emitting diode laser bars, along with collimation and stacking optics, on a common base plate. The beam quality produced by this source, which produces an output of 160 W, is good enough to efficiently couple into a 200 µm-diameter fibre.
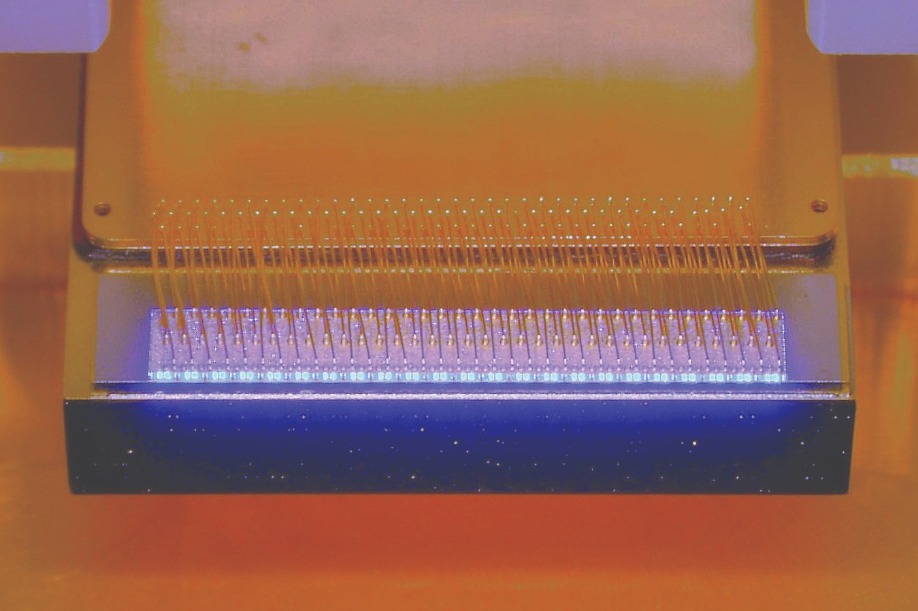
Following in the footsteps of infrared sources, a switch from a single emitter to a bar increases the total output power.
Another strength of this tailored bar is that it is one-tenth of the size of a previous 135 W module based on single emitters. Note that the single-emitter module requires more than 100 optical elements to be aligned individually – that is about five time higher than that for the stacking module.Our next step will be to combine several of these units. A source producing more than 500 W is planned by uniting the output of four 135 W tailored bars.
Ensuring lengthy, safe operation
To win deployment in industrial applications, it is essential that laser systems are reliable and can operate for many, many hours. The primary barrier to realising this is a degradation mechanism known as catastrophic optical damage, which is often fatal. Catastrophic optical damage is a generic, sudden degradation mechanism that occurs when light is locally absorbed, the temperature rises, and this is followed by further increases in absorption and temperature that spiral out of control.
Catastrophic optical damage can initiate at any absorbent point. So it may begin at either of the facets of the edge-emitting lasers, at internal defects within the waveguide, or at absorptive sites in passive waveguides. As blue sources move to a lower cost per watt, these devices will be operated at higher loads, increasing the likelihood that catastrophic optical damage will become a bigger issue in GaN-based devices.
Again, the development and long-lasting experience of the infrared lasers can come to our aid. For GaAs-based devices, there are proven techniques for reducing susceptibility to catastrophic optical damage and degradation. So, in our project we have used these approaches, such as facet coating technologies, and particular chip designs and packaging, to increase the reliability of our blue-emitting, GaN-based lasers. These efforts have paid dividends: in-depth testing by colleagues at the Max Born Institut can expose critical issues related to reliability. First long-term tests at Laserline demonstrate that these laser bars are reliable during a 12,000 hour test. Recent results show a power degradation rate of less than 3 percent per 1000 hours.
Our project is already leading to prototype commercial sources. At Welding and Cutting 2017, Laserline exhibited a demonstrator LDM 500-60 blue: it is a 450 nm blue diode laser with an output of 500 W. More success is sure to follow during our BlauLas project, including the primary goal of demonstrating 1 kW blue laser sources.
Further reading:
H. Wang et al. Optics Letters 42 2251 (2017)
H. König et al. Proc. SPIE 10514 1051402 (2018)
A. Balck et al. Proc. SPIE 10514 1051403 (2018)
Bernd Köhler et al. Proc. SPIE 10514 1051408 (2018)