Supercritical carbon dioxide spawns superior MOSFETs
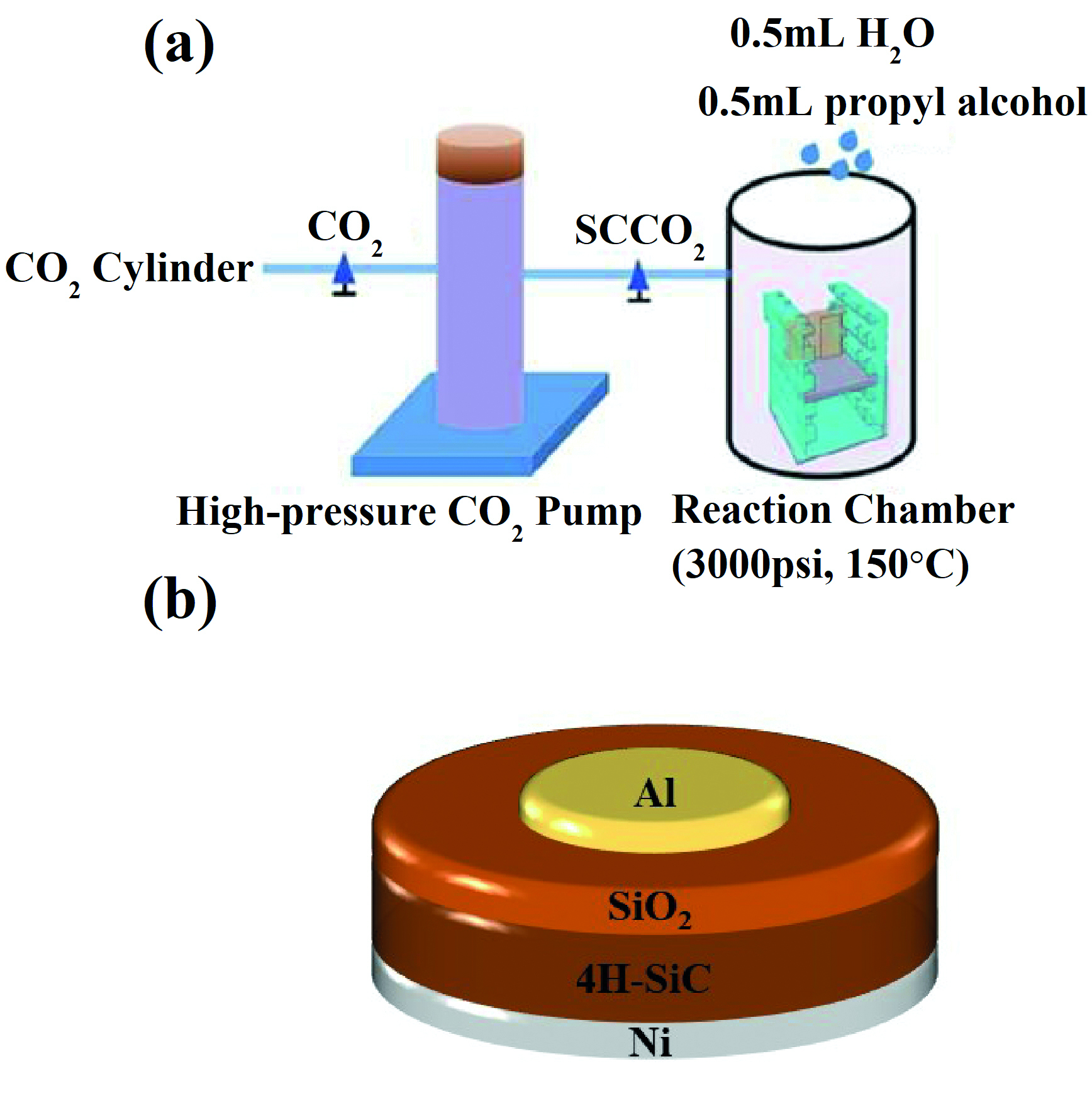
Low-temperature treatment with supercritical CO2 improves the interface between SiC and SiO2
The performance of SiC MOSFETs is held back by the quality of the interface between SiC and SiO2. But this weakness can be addressed with a supercritical CO2 treatment that slashes the density of interface states, claims a partnership between researchers at Xi’an Jiaotong University and Xidian University.
Spokesman for the team, Weihua Liu from Xi’an Jiaotong University, told Compound Semiconductor that in conventional SiC MOSFETs the interface is not optimised by high-temperature annealing, because this can create carbon clusters and other defects.
Formation of these imperfections is quashed with a lower temperature supercritical CO2 treatment that promises higher carrier mobility, a lower leakage current and a hike in the critical breakdown field of the gate oxide.
In a supercritical fluid there is a co-existence of liquid and gas phases. Thanks to this, supercritical CO2 combines gas-like solubility with liquid-like penetration, enabling damage-free diffusion into nanoscale structures.
The use of supercritical CO2 to improve interfaces in semiconductor devices is not new. Back in 2007, reports appeared describing the benefits this can bring to thin-film transistors made from amorphous silicon.
When supercritical CO2 treatment is applied to SiC MOSFETs at temperatures as low as 150degC, it is thought to terminate traps at the oxide-semiconductor interface and supress the interfacial parasitic oxide.
To assess the benefits of the supercritical CO2 process, the team began by producing MOS structures. They took epiwafers with an n-type layer that has a doping concentration of 3.5 x 1015cm-3 and, after applying a standard cleaning process, used dry oxidation to create SiO2 films with a thickness of 55-60 nm.
Some samples were treated in supercritical CO2 at 150degC for 60 minutes, using a pressure of 20 MPa (see figure above). To the process chamber the team added 0.5 ml of water and 0.5 ml of propyl alcohol. The latter acts as a surfactant between non-polar CO2 molecules and polar water molecules, enabling water to be uniformly distributed in supercritical CO2.
To benchmark results, the team did not treat some samples and processed others in a pure water vapour at 150degC for 60 minutes.
Fabrication of MOS structures, featuring aluminium electrodes with a diameter of 300 μm, allowed the team to evaluate the density of near-interfacial oxide traps. Using capacitance-voltage measurements, they found a near-interfacial oxide trap density of 1.62 x 1011cm-2 in the untreated sample, while samples treated in water vapour and supercritical CO2 produced values of 6.63 x 1010cm-2 and 1.84 x 1010 cm-2, respectively. The lowest value is claimed to result from the termination of traps in SiO2 through the creation of Si-O-Si feature bonds.
Additional benefits of the supercritical CO2 treatment are a reduction in leakage current and an increase in breakdown field.
Measurements of the interface state density also revealed the benefit of supercritical CO2 treatment.
Liu says that one of the next tasks for the team is to optimise the experimental conditions, in order to further reduce the interface state density. Another goal is to verify that the supercritical fluid process delivers benefits to 4H-SiC MOSFETs by applying this treatment to those devices.
M. Wang et al. Appl. Phys. Express 13 111002 (2020)