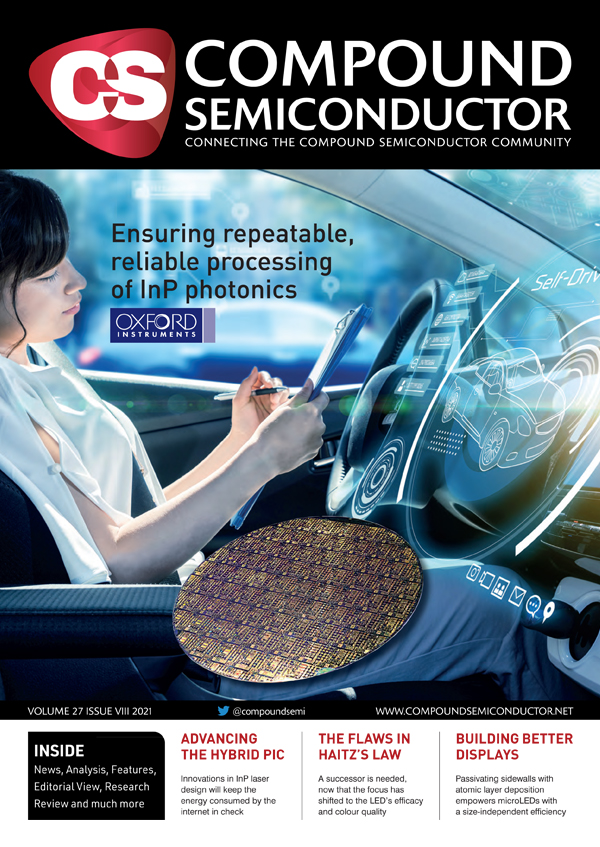
ISLC: Advancing hybrid PICs
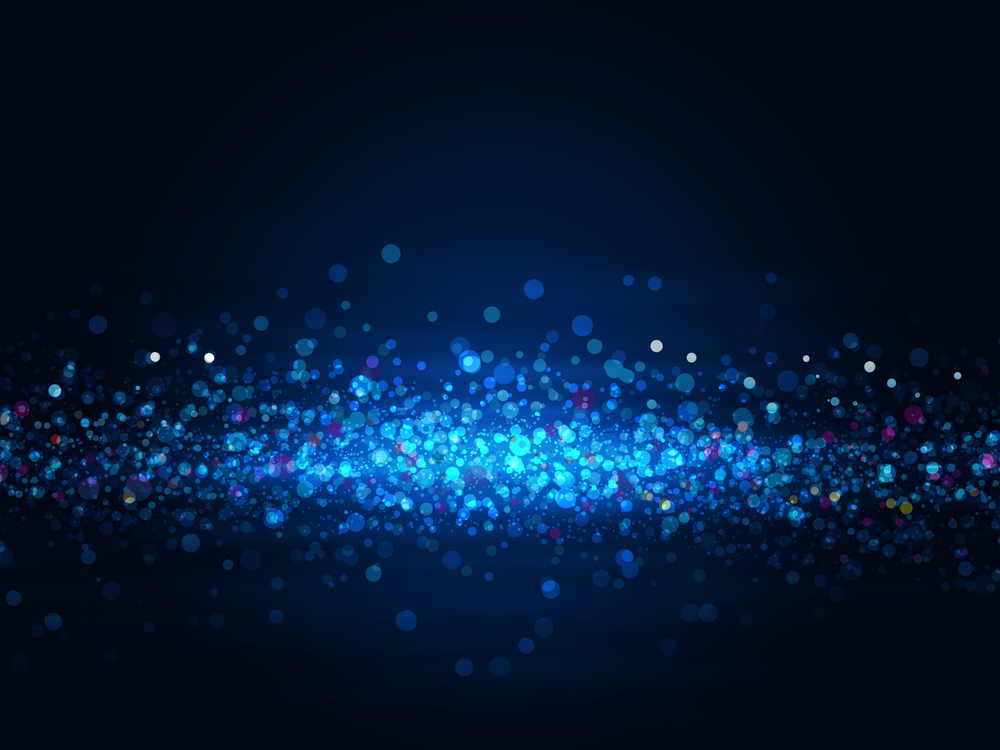
Innovations in InP laser design are destined to keep the energy consumed by the internet in check
BY RICHARD STEVENSON
JUDGED IN TERMS of its impact on our climate, the internet is both a friend and a foe. It has enabled teleworking and the remote attendance of international conferences, leading to a reduction in the number of journeys taken by car and plane; but it is having an impact on the climate that is roughly equivalent to the aviation industry, accounting for around 2 percent of the world’s CO2 emissions, according to the Boston Consulting Group.
With humanity’s insatiable desire for data, there is the threat that the internet’s contribution to the global carbon footprint will rocket. Fortunately, though, gains in the efficiency of infrastructure are offsetting exponential rises in the transmission and consumption of data.
Figure 1. Intel’s hybrid III-V/silicon laser process begins by taking a silicon wafer with a silicon-dioxide layer and defining a waveguide and a grating using deep-UV lithography. Oxygen plasma activation of the wafer follows, along with the bonding of InP chiplets to silicon. The bulk InP is removed to leave behind just the active region, before a III-V mesa is etched and the laser contacts added. The final step involves passivating regions of the mesa with hydrogen-ion implantation to leave a current channel in the centre that overlaps with the optical mode.
To ensure that this equilibrium continues, much effort is being devoted to developing components that set a new benchmark for the energy required per bit. If they are to have a commercial impact, competitively pricing is also essential.
Addressing both of these key requirements is the hybrid photonic integrated circuit (PIC), combining the low cost, large wafer size and high level of maturity of silicon technology with the InP laser, the only realistic choice for a high-performance light source operating in the spectral domains employed for data transfer.
At the 27th International Semiconductor Laser Conference (ISLC), held in Postdam, Germany, from 10-14 October and organised by FBH Berlin, engineers showcased a variety of technologies for forming InP-based lasers on silicon substrates. Triumphs announced at that meeting included an 8-channel transmitter by Intel, featuring distributed feedback (DFB) lasers; a laser with a wide tuning range and a two-storied ridge structure, pioneered by a team led by Sumitomo Electric Industries; and a GaInAsP laser within a buried-ridge waveguide structure, trailblazed by researchers at Tokyo Institute of Technology.
Turbo-charging optical engines
Intel is well-known for its development of optical transceivers for data centres. These products, which first hit the market in 2016, are produced with a 300 mm hybrid silicon photonics platform that features advanced lithography.
At ISLC, Intel’s Duanni Huang outlined to delegates attending in-person and on-line how the deployment of these transceivers will evolve over time. Huang explained that the company’s 100 Gbit/s to 400 Gbit/s transceivers are now being produced in high volume for ethernet-compliant products. These transceivers are based on front-plate pluggable optics and operate at an energy efficiency of 30 pJ/bit. “In these products, the optics is still very far away from the central Ethernet switch,” remarked Huang.
“In 2020, we had a demonstration of so-called co-packaged optics, in which a photonic engine capable of 1.6 terabits-per second is co-packaged with the switch core,” remarked Huang.
This is said to bring the optics much closer to the photonics. With this architecture, optical engines could run at a total data rate of up to 3.2 Tbit/s, while drawing less than 15 pJ/bit.
Looking further ahead, Intel anticipates a time when photonics will be united with the package where the processor sits, using an optimised optical interface. This architecture will operate at a total data rate that could be as high as 16 Tbit/s, and have an energy efficiency well below 5 pJ/bit.
“In order to reach the bandwidth density and energy efficiency needed to make this happen, we utilise wavelength-division multiplexing,” revealed Huang. This approach, similar to that employed in long-haul links, exploits the resonance of silicon micro-ring modulators to select specific wavelengths. At the receiver, a similar approach can be employed to separate the various wavelengths transmitted down the fibre and extract encoded data.
Intel produces its laser by forming a waveguide and a grating on a 300 mm silicon wafer with a silicon-dioxide layer, and then adding an InP chiplet that is subsequently processed (see Figure 1 for details).
To define the laser’s emission wavelength, Intel adjusts the dimensions of the grating. For the 8 channels deployed in the latest generation of technology, there is a 200 GHz spacing, equating to a difference in the grating period between adjacent laser channels of just 0.2 nm. “This is difficult, but something that is achievable with our deep UV-lithography,” remarked Huang.
He and his co-workers have provided a proof-of-concept transmitter. “Only a single indium-phosphide chiplet is used to fabricate all eight lasers, and each laser can be controlled individually,” explained Huang.
An 8-channel transmitter is formed by combining the output from the eight lasers with three stages of multimode interferometer, formed in silicon. This is a relatively easy way to combine eight channels into four, then two, and finally just one. However, it does incur a power penalty of around 3 dB at each stage.
With this approach, the team have fabricated a transmitter with 8 wavelengths spaced apart by 200 GHz ± 13 GHz, centred at around 1305 nm. Driving each laser sequentially with 80 mA produces lasing peaks with a side-mode suppression ratio (SMSR) of 54 dB and an output power of around 1 mW.
“When we turn on all eight laser together, we see a number of side peaks on either side of the eight main laser peaks,” explained Huang. This is attributed to four-wave mixing in the silicon waveguide, which quashes the SMSR to 38 dB.
It is worth noting that changes in temperature do not have a devasting impact on the DFB lasers. While there is a red-shift with temperature, all channels move together, according to measurements at temperatures ranging from 22 °C to 62 °C.
Another encouraging result is that the power and channel uniformity are well within those defied in the CW-WDM-MSA standard. This standard stipulates values of ± 50 GHz and ± 1 dB power imbalance.
Enhanced coupling
One of the downsides of hybrid PICs is that there are coupling losses when light transfers from one material system to another. To minimise these losses, a team led by Sumitomo Electric Industries, and including engineers from Tokyo Institute of Technology, has recently developed a novel hybrid-laser architecture. It features a two-storied ridge structure, employing n-type and p-type tapers to connect a III-V gain section to the silicon waveguide (see Figure 2).
Figure 2. Sumitomo Electric Industries has developed a laser structure with a two-storied active region and n- and p-type tapers, introduced to minimise coupling losses. The laser’s emission wavelength is tuned by heating the ring resonators. Reproduced from the paper MP2.1, 27th ISCL. © IEEE.
Details relating to the fabrication of this laser, along with measurements demonstrating its wide tuning range, were provided in a presentation by Takuo Hiratani from Sumitomo Electric Industries. He and his co-workers are advocating the use of hybrid integration in data-centre optical interconnects, because they can combine the merits of InP-based lasers, photodetectors and modulators with silicon’s strengths, which include passive waveguides with tight bends and the opportunity for large-scale integration.
The team from Sumitomo unite InP and silicon using wafer-bonding. “High density integration and high alignment tolerances are strong advantages,” argued Hiratani, who compared this approach to butt-coupling and micro-transfer printing.
Sumitomo’s latest lasers, emitting at around 1.55 m, are based on an architecture that realises gain within an InP-based section that is positioned in an external cavity laser featuring two silicon ring resonators, a phase-control section and rear-loop mirrors. With this design, controlling the heating of the rings, which have differing dimensions, allows a tuning of the lasing wavelength over 60 nm.
“In this [latest] work we introduced a new optical coupling structure, including a two-storied ridge structure,” explained Hiratani. “This structure enables constriction of the current, plus, by a shallow-ridge-type gain section, a low optical coupling loss, with zero wavelength dependence.” According to simulations, coupling loss at the interfaces is just 0.4 dB across the entire C-band.
To produce their novel laser, Hiratani and co-workers employ electron-beam lithography to prepare silicon waveguides on the silicon-on-insulator wafer. An InP epiwafer, containing the GaInAsP quantum wells, is directly bonded to this patterned surface, before the InP substrate is removed by chemical wet etching. Stepper lithography and dry etching form a shallow ridge structure and the two-step taper structures. To complete fabrication, cladding layers are deposited, electrodes formed by evaporation, and microheaters and anti-reflection coatings added.
By comparing the performance of Fabry-Pérot lasers with and without an optical coupling structure, the team estimated a loss per interface of less than 1 dB. “This low coupling loss is thanks to the two-storied ridge structure,” remarked Huang.
Measurements on the team’s novel laser, which has a 1.1 mm-long III-V gain section and a total device length of 2.5 mm, reveal a threshold current of 32 mA and a maximum output power of 1.3 mW. Kinks appear in the light-output power plot with increases in current, due to mode-hopping associated with phase changes in the gain section. By exploiting the Vernier effect and applying up to 60 mW to the two rings, the laser’s wavelength can be tuned over 56.2 nm. Over this range, the SMSR is at least 41 dB. “These results show that the III-V-silicon hybrid tuneable laser is very promising for next-generation PICs,” concluded Hiratani.
Masterful membranes
The massive microprocessor chips that are produced today suffer from Joule heating and a delay associated with wiring. A promising solution is to switch from electrical wiring to on-chip optical interconnects. But if this is to succeed, the associated light source must draw incredibly little power, be easily integrated with passive devices using an in-plane platform, and produce enough light for a corresponding detector.
“In order to meet these requirements, we propose a membrane laser light source,” explained Naoki Takahashi from Tokyo Institute of Technology, during his talk to delegates at ISLC. He championed this novel form of laser, promoting its strong optical confinement and a high modal gain, realised by essentially replacing an InP cladding with SiO2 or air. “This leads to a reduction in the threshold current, as well as a higher modulation efficiency.”
To place the team’s latest success in context, Takahashi began by sharing the results of previous work. In earlier development, he and his co-workers realised a membrane laser with a threshold current of 0.21 mA, a high differential quantum efficiency – it hit 32 percent – and a high differential resistance of 880 . “This makes an energy cost of 93 femtojoules-per-bit when operating at 20 gigabits-per-second. However, it is estimated that an energy cost of 10 femtojoules-per-bit or less is required to realise
on-chip optical wiring.”
Recently, efforts have been directed at reducing the energy-per-bit by increasing optical lateral confinement through modifications to p-type and n-type structures that surround the active region
(see Figure 3). Calculations suggest that changes to the ridge height, d, in this buried-ridge waveguide architecture can lead to a substantial enhancement in lateral optical confinement.
Figure 3. The performance of the GaInAsP membrane laser produced by the University of Tokyo is improved by introducing a ridge height, d, and reducing the distance D, which is the separation between the p-type electrode and the active region. Reproduced from the paper MP2.3, 27th ISCL. © IEEE.
Another approach to improving this key metric, which also trims differential resistance, is to move the p-type electrode closer to the active region. In a conventional structure, such a move would threaten to interfere with the optical mode; but by optimising the ridge height, this is avoided.
Calculations by the team have determined that a judicious choice for their laser’s ridge height is 50 nm. This can lead to a 40 percent fall in device resistance. To produce their devices, Takahashi and co-workers begin by growing the p-type cladding, active region and an InP cap on an InP wafer. Using a SiO2 mask, photolithography and etching they define a ridge-shaped active region, before re-growing p-type and then n-type layers. A SiO2 layer is grown on top, before this wafer is bonded to a silicon substrate coated with the polymer BCB, and the InP substrate removed and electrodes added.
The benefits of the buried waveguide architecture have been quantified by comparing this device with another that is identical, apart from having a flat structure. Measurements on these devices, which have a 560 m-long cavity and a 1.8 m ridge width, reveal that the introduction of the buried ridge reduces the threshold current from 12.5 mA to 9.8 mA and increases the output power. Investigations have also shown that reducing the distance between the electrode and active region from 1.3 m to 0.8 m drives down differential resistance by 20 percent.
Takahashi and colleagues have also fabricated a distributed-reflector laser with a buried waveguide that has a width of 1.3 m. This 1558 nm laser has a threshold current of 0.24 mA and a differential resistance of 430 . “The threshold current was almost the same as the previous work, and the differential resistance was reduced by about half from the previous work,” enthused Takahashi, adding that the SMSR is 33 dB. “These results indicate that the introduction of the buried waveguide structure can effectively reduce the power consumption of membrane lasers.”
With progress being made by academic and industrial developers on using InP lasers to reach higher data rates without paying a power penalty, there is hope that the internet will not become a major contributor to global warming. And that’s clearly good news, given our increasing dependence on what is the virtual world.