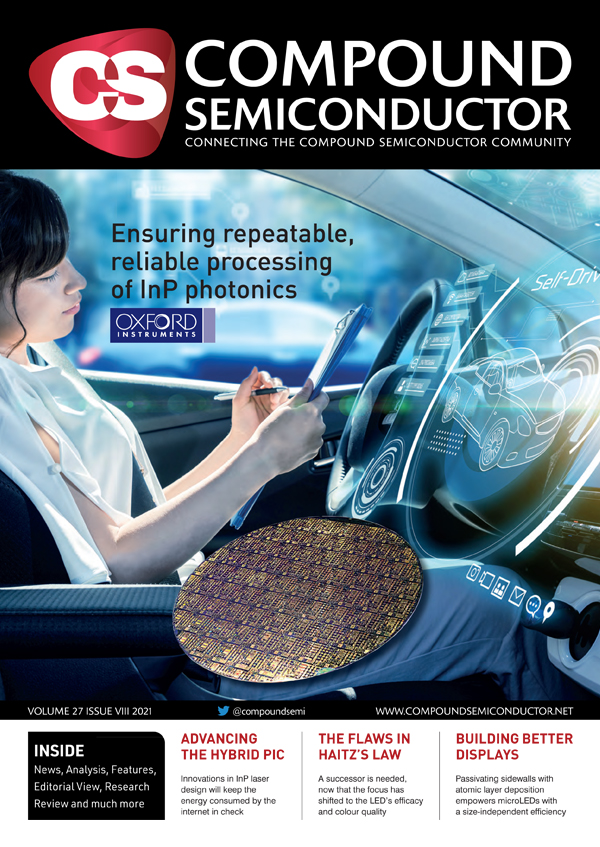
Realising red GaN-based microLEDs with europium-doping
The novel red luminescence provided by doping GaN with europium ions enables the monolithic integration of nitride-based full-colour LEDs for ultrahigh-resolution microLED displays
BY SHUHEI ICHIKAWA, DOLF TIMMERMAN, JUN TATEBAYASHI AND YASUFUMI FUJIWARA FROM OSAKA UNIVERSITY
WE ARE ON THE CUSP of a new era, known as ‘Smart society’, that will see cyber space and the physical space interactively fused. Critical to this is the introduction of a small-size, high-resolution display, which is an essential ingredient in virtual-reality, augmented-reality and mixed-reality glasses.
One candidate for producing these tiny high-resolution displays is the microLED. Screens formed from a vast array of these miniature LEDs have many virtues, including a high efficiency, high contrast and high stability. Fabrication of this class of display draws together devices emitting each of the three primary colours. A very common combination is the use of InGaN/GaN-based LEDs for the blue and green and AlInGaP/GaAs-based LEDs for the red. These devices are brought together to form pixels using a pick-and-place technique. However, there is a problem: when the dimensions of the LEDs are reduced, the efficiency of the red variant plummets, due to an increase in surface recombination associated with the hike in the surface-to-volume ratio.
Figure 1. Europium-doped GaN LED arrays exhibit bright red luminescence.
Several solutions are being explored for reducing the dimensions of the red LED while maintaining its efficiency. One option, receiving much attention, is to use GaN-based LEDs emitting in the blue or ultraviolet to pump red-emitting quantum dots or phosphors. However, while this approach also offers monolithic integration, it suffers from insufficient stability and an inadequate colour-conversion efficiency. What’s more, with this particular technology, there is a need to increase the pixel contrast ratio and enhance the colour purity by suppressing crosstalk between various light emitters. Unfortunately, when black light-blocking partitions are applied between all the subpixels to accomplish this, the effective area of the pixels diminishes, impairing the number of pixels-per-inch (PPI).
Switching to InGaN nanocolumns avoids this issue. It’s an architecture that effectively relaxes material strain, even for the high-indium contents that are necessary for red light emission. But it is challenging to produce nanocolumn structures with a high colour purity – they are held back by large variations in emission wavelength, due to the ensemble nature of these structures and the sensitivity of individual nanocolumns to size fluctuations. Another drawback is the need for electron-beam lithography, prior to epitaxial growth, to precisely control the nanocolumn size and ultimately ensure the desired emission wavelength. Note that for this type of microLED, and also for that based on quantum dots, fabrication requires a lateral integration method.
There is much merit in taking a very different approach, based on the vertical-stacking integration of tri-colour LEDs. Realising this with a single epitaxial sequence eradicates several steps in the microLED production process, such as the mask-patterning prior to growth and the addition of black partitions. What’s more, with this technique the areal density of the microLEDs is only limited by lithography and flip-chip accuracy, so it is possible to integrate these emitters with a PPI beyond 5,000.
Figure 2. Eu3+ ions doped in GaN under current injection deliver a very sharp emission peak, crucial for a high colour purity.
A pioneer of this approach is the group led by the Nobel-prize winning physicist Hirsohi Amano. Recently his team demonstrated the monolithic integration of tri-colour microLEDs using InGaN quantum wells. These devices, with a 100 µm by 100 µm active area, are composed of independent subpixels, which emit in the blue, green and yellow–orange range and have a colour saturation of over 90 percent. However, there are drawbacks: one concern is that the longer wavelength emission is much broader; and another is that its peak position shifts to shorter wavelengths as the injected current increases, due to a reduction in the quantum-confined Stark effect.
Our team offers a way to overcome this issue, drawing on our previous success from more than a decade ago. Back in 2009 we invented a novel red LED, formed by adopting europium-doped GaN. In the intervening years we have continued to refine this device, enabling its output power to steadily increase to the milliwatt level. In the remainder of this feature we will detail this triumph, and how we have used vertically-stacked integration to combine it with conventional blue/green LEDs to create a key technology for the next-generation of microLED displays.
Europium doping
Our approach fulfils the requirement for the vertical-stacking of tri-colour LEDs, which is the monolithic integration of all three colours. We needed to develop and alternative to the more obvious approach of just using InGaN quantum wells, because although blue and green LEDs based on this have been successfully commercialized, a red cousin is lacking. The route to producing red emission with this type of LED is to either increase the indium-content or the thickness of the InGaN quantum well, or to use a combination of the two. But this strategy is precarious: it leads to an increase in piezo-electric polarization fields, and the low miscibility of indium in GaN hampers efforts to realise a sufficient indium content in the well while maintaining sufficient crystal quality. We are able to sidestep these issues by manipulating the emission through the doping of GaN with an intrinsic red emitter, the rare-earth element europium Eu3+.
The Eu3+ ion is no stranger to display applications, having been widely deployed as a luminescent centre in red-emitting phosphors in cathode ray tubes and plasma display panels. In general, rare-earth ions, including Eu3+, are characterized by partially filled 4f shells, which are localized inside completely filled 5s and 5p shells. This localization shields the electrons in the 4f shell from the surrounding environment, allowing rare-earth ions to maintain their atom-like properties and exhibit sharp luminescence bands associated with radiative transitions within the 4f manifold. These transitions are virtually insensitive to changes in current injection and temperature. When Eu3+ ions are incorporated into GaN, they take the place of the Ga3+ metallic cations and occupy sites with reduced symmetry.
Adding Eu3+ ions alters the light-emitting mechanism. Conventional band-to-band transitions are replaced by the transfer of energy from injected carriers in the GaN host material to Eu3+ ions, which are promoted to an excited state that leads to the emission of red light. This energy transfer is strongly dependent on the material properties, and can be enhanced by changing the material fabrication processes, or by intentionally introducing other dopants, which can act as energy hubs.
Eu3+ ions exhibit a sharp luminescence around 620 nm, due to intra-4f shell transitions from the 5D0 to 7F2 states (see Figure 2). This attribute is most welcome, helping to create red-emitting devices with a high colour purity and robust emission wavelength stability. Over the last decade and more, we have developed expertise to epitaxially grow high-quality GaN materials that are doped with Eu3+ ions and are optimised to deliver excellent performance in LED structures. The output power of these devices has exponentially increased over time, and has recently exceeded 1 mW at 20 mA, a respectable figure for mass production (see Figure 3).
Figure 3. Recent progress of the output power of europium-doped GaN-based LEDs produced at Osaka University.
Maintaining efficiency
To enable immersive experiences in entertainment, education and communication, microdisplays need to come as close as possible to matching the human visual system. For a typical virtual-reality headset, this requirement implies that the spatial resolution needs to be as high as 4600 PPI to match the eye’s central field-of-view capabilities. This specification translates to a pixel size of approximately 5 µm, and thus even smaller feature sizes for individual sub-pixels.
Figure 4. A scanning electron microscopy image of 1 µm-sized mesa.
When the dimensions of a microLED are reduced to below around 100 µm, the influence of their sidewalls increases, leading to the introduction of non-radiative recombination associated with imperfections induced by the fabrication process. The upshot is a lowering of the internal conversion efficiency. To address this, engineers are turning to new LED structures, modified chip architectures and better processes to diminish the impact of sidewall defects. With these refinements, blue-emitting microLEDs based on InGaN quantum wells can maintain their efficiency when scaled down to a size of just 5 µm.
With red microLEDs, which are typically based on phosphides, it’s a different story. The issues associated with scaling are not addressed with the approaches that work for their GaN-based siblings, and their efficiency drops quickly when the pixel size shrinks. These devices are hampered by a combination of long carrier diffusion lengths that allow carriers to reach sidewalls from a larger distance, and the high surface-recombination coefficient.
When switching from red LEDs made from phosphides to those employing europium-doped GaN, the carrier diffusion length plummets to a value even shorter than that found in conventional nitrides. That’s because the Eu3+ ions are extremely efficient at trapping injected carriers. Diffusion lengths are typically around 100 nm, a distance so small that carriers are prevented from reaching the sidewalls.
This virtue is at play in our set of square europium-doped structures, with sizes ranging from 1 µm to 100 µm (see Figure 5). We have found that the internal quantum efficiency remains constant down to sizes of 10 µm, and only shows modest decreases at even smaller sizes. For our smallest structure of 1 µm, the internal quantum efficiency is 70 percent of the maximum value. This impressive result is realised without any post-treatment of the sidewalls, so it could be further improved by employing the process optimizations developed for the blue GaN-based LEDs.
Figure 5. Normalized internal quantum efficiency as a function of mesa size for europium-doped GaN-based LEDs. The red line indicates the modelled internal quantum efficiency for a 110 nm carrier diffusion length.
Our results underscore the inherent potential of europium-doped GaN as an optically active material, and they provide much encouragement for using this material in microLEDs. The work has provided us with a platform to investigate the performance of microLED structures based on this material. We hope that we can realise high efficiencies in devices as small as 1 µm.
Monolithic integration
Compared with displays based on conventional liquid crystals and organic LEDs, those employing microLEDs offer an increased pixel density, a higher efficiency and a hike in brightness. However, commercialising this technology in its highest fidelity is not easy, due to complexity in the fabrication of high-resolution full-colour displays that provide a wide colour gamut.
To realize a pixel density beyond 1000 PPI, it is indispensable to employ a growth technique that allows the monolithic integration of the three primary-colour LEDs from the same material system, because this eliminates complications arising from pick-and-place techniques used to transfer ultra-small-sized LED chips. For ultra-high resolutions beyond 4600 PPI, it is also advantageous to adopt a vertical stacking approach for bringing together red, green and blue LEDs, because this minimises gaps between pixels and sub-pixels. Another consideration is to realise a luminance of at least 3,000 cd m-2, as this allows displays to be read outdoors, assuming a typical ambient illuminance of 50,000 lux.
Accounting for all these considerations, we have used monolithic integration to produce vertically stacked full-colour LEDs that feature europium-doped GaN and the emission from InGaN quantum wells (see Figure 6). These integrated LEDs were grown by MOCVD on a single sapphire substrate and did not require any additional preparation. It is possible to select all three primary colours from anywhere in the wafer by controlling the etching-depth and position.
Figure 6. Vertical stacking of red, green and blue LEDs enables a very high pixel density (left). Electroluminescence from monolithically integrated LEDs on the same sapphire substrate under simultaneous operating conditions.
The optimal growth temperature for the europium-doped GaN layer is 960 °C – this is higher than that used for the InGaN quantum wells, which are grown at temperatures between 650 °C and 800 °C.
The europium-doped layer is thermally stable at the temperature employed for its growth, and is better suited for stacked-type integration of red, green and blue devices than InGaN-based red LEDs, which suffer from indium desorption. This desorption is accelerated by temperatures used for the growth of the InGaN layers used in subsequent LEDs.
Figure 7. Individual electroluminescence spectra of red, green and blue LEDs obtained at room temperature under 2 mA current injection.
Room-temperature electroluminescence spectra of our individual devices show a high colour purity. This is valued, as it improves the capability for displays to generate reproducible colours. Driven with a 600 µA injection current, the maximum colour purity for the red, green, and blue emission are 100 percent, 97.1 percent, and 99.7 percent, respectively (these figures are 100 percent, 72.1 percent, and 99.6 percent, respectively, at 2 mA operation). These results demonstrate the extremely high colour purity of europium-doped GaN LEDs under any current injection, due to the stable intra-4f shell transitions in the Eu3+ ions.
The most common approach to evaluating the reproducibility of colours of displays is to consider the space on the International Commission on Illumination (CIE) chromaticity diagram (see Figure 8). Using this metric – and the colour purity efficiencies for our red, green and blue LEDs – indicates that this combination of emitters provides an exceptionally large coverage. According to the Rec.2020 standard, our devices provide 105.5 percent of the area with 91.2 percent coverage; and for the DCI-P3 standard, the corresponding values are 147.0 percent and 96.5 percent, respectively. Crucially, these figures show that our devices fulfil the colour gamut requirement for the Ultra HD Premium TV standard. What’s more, they produce a maximum luminance of around 3100 cd m-2, so they satisfy the minimum requirement for outdoor applications.
Figure 8. The emission colour gamut of red, green and blue LEDs on the CIE chromaticity diagram under 600 µA current injection.
These results show that our technology has a great deal of promise. By adding europium doping to the microLED to aid monolithic integration, we are paving the way for displays with a very high PPI and great colour quality that can serve in virtual-reality, augmented-reality and mixed-reality glasses.
FURTHER READING
† A. Nishikawa et al. Appl. Phys. Express 2 071004 (2009)
† S. Ichikawa et al. Appl. Phys. Express 14 031008 (2021)
† D. D. van der Gon et al. Opt. Lett. 45 3973 (2020)
† B. Mitchell et al J. Appl. Phys. 123 160901 (2018)