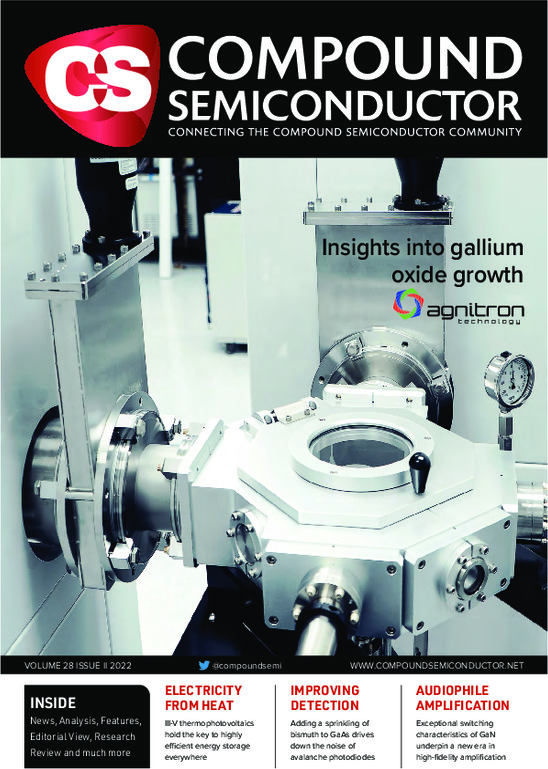
Photodetectors: The benefits of adding bismuth
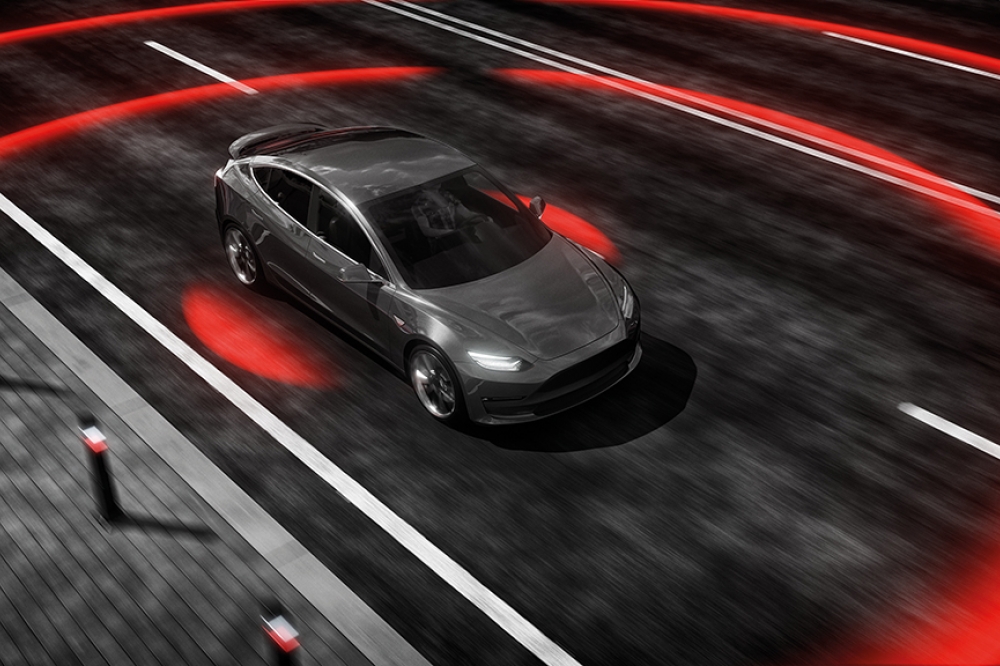
Adding a little bismuth to GaAs drives down the noise of avalanche photodiodes
BY ROBERT RICHARDS FROM THE UNIVERSITY OF SHEFFIELD
There’s far more to setting a new low for the noise of a photodetector than winning bragging rights. Success also aids a number of important applications. Take optical networks, which operate in the O and C bands that are centred around 1300 nm and 1550 nm and incorporate intermittent signal boosters. Slashing the noise in the detectors deployed in these networks increases the efficiency of data transfer, either by allowing a reduction in the power of the transmitter or by trimming the number of boosters. Another example is lidar, short for light detection and ranging. It’s a technology for serving in autonomous vehicles and geospatial mapping – and for this pair of applications, driving down the noise in the detector enables faster, more accurate measurements.
When there’s a need for high speed and high sensitivity, standard photodetectors can fall short. These devices only produce a modest signal from incident light, limiting their signal-to-noise ratio, especially when the measurement time is limited, as is the case with high-speed communications or lidar. While an external amplifier can increase the signal, the noise is also amplified, impairing efforts to improve the signal-to-noise ratio.
A far better option for ensuring both high sensitivity and high speed is the avalanche photodiode. Like a conventional detector, every photon that it absorbs excites an electron to the conduction band, to leave a hole in the valence band – and the internal electric field pulls these carriers in opposite directions. However, in an avalanche photodiode the electric field is far stronger than it is in a standard photodetector, causing the carriers to gain enough energy to excite additional electron-hole pairs, through a process known as impact ionisation. These newly ionised electrons and holes are themselves then accelerated, leading eventually to a large number of electrons and holes contributing to the current, effectively amplifying the original signal.
For most detection below 1000 nm, the incumbent avalanche photodiodes are made from silicon and are well-established commercial products. Silicon is a near-ideal material for making this class of detector because of its technological maturity and because electrons can cause impact ionisation far more readily than holes. This is reflected in the ratio of the electron and hole ionisation coefficients, α and β, which is very large. Thanks to this, the ’excess’ noise due to the stochastic nature of the ionisation process is highly reduced.
Unfortunately, the detection characteristics for silicon photodiodes are far from ideal. Due to the indirect bandgap of this material, thick layers are needed to ensure sufficient absorption of photons. This is particularly acute for detection at the tail end of silicon absorption, at around 1 μm, where to realise a reasonable quantum efficiency the detector must be very thick – a requirement that prevents high-speed operation. Due to this limitation, silicon avalanche photodiodes are unsuitable for optical communication networks and some lidar systems.
Options for the infrared include HgCdTe and InAs. Both have α/β ratios almost infinitely large, but due to their small bandgap, cooling is needed to reduce dark currents. Another alternative is GaAs, along with its related alloys. Unfortunately, this material system has an α/β ratio near unity, leading to a large excess noise. However, by adding a small amount of bismuth to this material system, our team at the University of Sheffield has shown that this difficulty may be overcome, opening the door to a new, highly flexible family of extremely low-noise avalanche photodetectors.
Bismuth benefits
Incorporating bismuth into GaAs has a dramatic effect on the band structure (see Figure 1). When bismuth is added, it takes the place of arsenic and introduces an electronic state that interacts with the valence band edge. This causes the valence band edge to rapidly increase in energy, while the conduction and split-off bands move more slowly. As a result, the band gap reduces by several hundred meV and the spin-orbit splitting (the gap between the split-off and valence band edges [Δso]) increases by several hundred meV with the addition of just a few percent bismuth. Δso is a key quantity, because holes in GaAs have to be in the split-off band to acquire enough energy to initiate impact ionisation. Consequently, as Δso increases, it becomes much harder for the holes to reach the split-off band and impact ionise.
Figure 1. Left: Bismuth (purple) is a large group V atom that replaces arsenic (red) in the GaAs matrix. Right: The addition of even small amounts of bismuth to GaAs has a profound effect on the material band structure.
The bismuth-induced changes to the bandstructure are helpful for realising low-noise photodetectors with desirable characteristics. The reduction of the bandgap propels the cut-off for detection to 1.1 µm and increases the absorption coefficient; and the increase in Δso reduces β while leaving α largely unchanged, leading to an enhancement in the α/β ratio of a factor between 2 and 100.
We fabricated a series of GaAsBi photodetectors on GaAs substrates using the MBE technique. On epi-ready (001) substrates we produced epitaxial structures containing an intrinsic layer of GaAsBi with a bismuth content of up to about 5 percent, sandwiched between doped GaAs cladding layers, and capped with a thin, heavily doped layer. Growth rates were in the range 0.3–0.6 μm/hr.
When producing epilayers of GaAsBi, a major consideration is the appropriate growth temperature. We usually operate between 350 °C and 400 °C, because when the temperature exceeds 400 °C bismuth incorporation becomes very small (less than 4 percent). Identifying the ideal growth temperature for GaAsBi is not easy – high growth temperatures impede bismuth incorporation, while low growth temperatures favour the incorporation of antisites, interstitials and vacancies, leading to poor device characteristics.
A key consideration is the abundance of bismuth on the semiconductor surface during growth. Its presence improves material quality by keeping the growing surface smooth, largely counteracting the effects of low growth temperature. However, if there’s too much there, bismuth droplets form; as well as disrupting growth, these droplets drain the bismuth surface population and impair incorporation of this element into GaAs.
Figure 3. Left: Reducing the α/β ratio (increasing the disparity between a and b) reduces the noise in an avalanche photodiode. Predictions (solid lines) based on the experimental data (data points) indicate a very low noise for thick, high-bismuth-content layers. Right: For 1,500 nm-thick devices, GaAsBi is expected to out-perform silicon for a bismuth incorporation of 4 percent. Excess noise is predicted to continue to decrease at higher bismuth contents.
Another decision facing any grower of GaAsBi epilayers is the appropriate arsenic flux. Set this too high and the excess arsenic will kick bismuth atoms out of the growing lattice, as well as increasing the density of arsenic antisites. To avoid this, it is normal to employ an arsenic-to-gallium atomic flux ratio of between 0.9 and 1.1. There is very much a ‘Goldilocks’ set of growth conditions for good GaAsBi growth, where the temperature, bismuth flux and arsenic flux are all just right – not too big, not too small.
Our range of devices includes a number of p-i-n and n-i-p structures that have a GaAsBi active region with a thickness varying from 200 nm to 1600 nm and a bismuth content from 0.7 percent to 5 percent. From a combination of X-ray diffraction and photocurrent measurements on these samples, we see that the absorption coefficient at 1064 nm is more than one hundred times that of silicon for bismuth contents over about 3.5 percent – a promising result for photodetectors.
We have also undertaken electrical measurements on our devices. They revealed good forward diode characteristics that scaled with device area, and dark currents of below 10 mA prior to breakdown for devices with diameters of 50 µm. We think that a combination of bulk and surface leakage is behind the reverse-leakage currents in these diodes.
The Sheffield dilute bismides team in their MBE lab.From left to right: Matthew Carr (PhD student), Nick Bailey (PhD student), Dr Rob Richards (group lead), Dr Tom Rockett (PDRA), Nada Adham (PhD student) and Shiyuan Gao (PhD student).
Measurements of electron- and hole-initiated photomultiplication have been used to determine values for α and β. This work revealed that increasing the bismuth content only produced about a 30 percent reduction in a values, while yielding an orders-of-magnitude reduction in β at low electric fields (see Figure 2).
Our calculations suggest that the GaAsBi material system can produce avalanche photodiodes with an excess noise below that achievable even by silicon (see Figure 3). While other III-Vs have reached comparably low noise in the past, this is the first time that this performance has been observed in an avalanche photodiode made with such a dilute (about 5 percent) alloy. Given that this work is in its infancy, even better results are likely to follow.
These results illustrate a mechanism for the production of very-low-noise avalanche photodiodes at wavelengths well beyond 1 µm. For many years, there has been a strong desire to have silicon-like detector properties in devices made from III-Vs. Bismuth-engineering of the bandstructure may bring this closer to reality for the manufacture of low-noise detectors that can serve in telecommunications and lidar.
Further reading
Y. Liu et al. Nat. Commun. 12 4784 (2021)