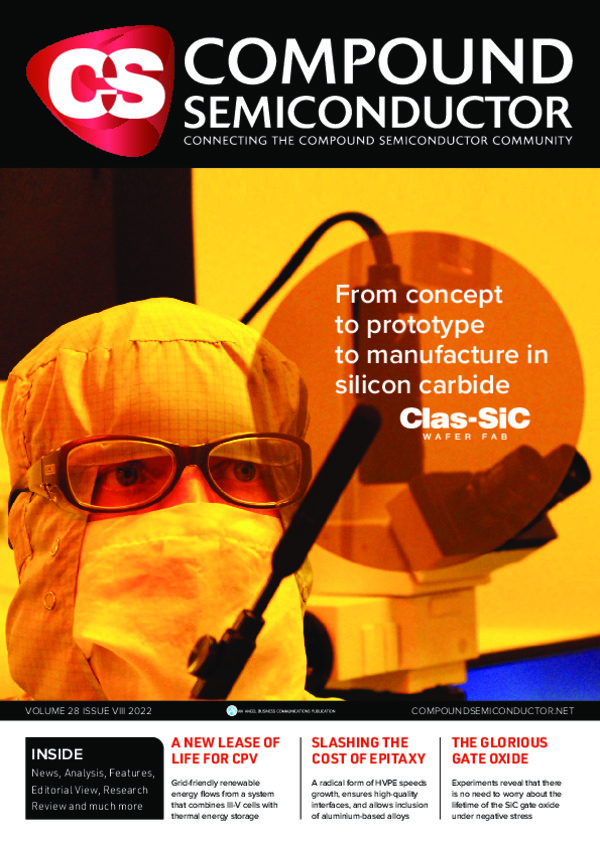
Integrated energy storage unlocks CPV’s full potential
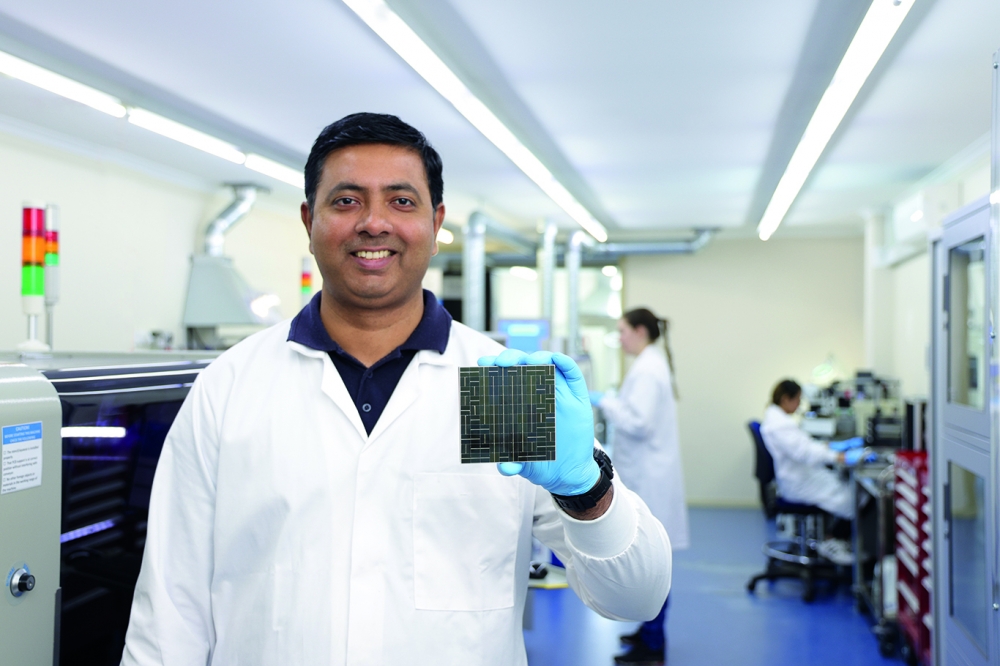
Packed with III-V cells, a small solar module that’s almost two thousand
times more powerful than a typical silicon PV panel holds the key to
grid-friendly renewable energy.
BY JOHN LASICH AND KIRA RUNDEL FROM RAYGEN
A sheep paddock in the Australian outback is the surprising location for the world’s largest next-generation storage project, backed by global energy majors.
Driving this renewable deployment is RayGen, our company that’s located in Melbourne, Australia. We are in the final stages of constructing and commissioning a ground-breaking system that combines electricity generation from 4 MW of solar with a 3 MW / 50 MWh storage facility. Located near the rural community of Carwarp – roughly six hours’ drive inland from Melbourne – this unassuming site hosts the world’s largest next-generation storage project. It is here that we are showcasing a world-leading technology that offers a superior alternative to lithium-ion batteries and pumped hydro.
Rising out of the sheep paddock at this revolutionary site are four solar towers, shining in the summer sky. At the top of each is a dense array of III-V GaAs solar modules, which convert a concentrated solar beam into electricity and heat. Close to the towers sit two large pits; covered, insulated, and filled with water. Between them, they store enough thermal energy to provide 50 MWh of dispatchable electricity – equivalent to a ‘big battery’.
Spurred on by the world’s largest energy companies, we have a growing pipeline of projects approaching gigawatt scale. All these potential deployments offer growing demand and an exciting market opportunity for the compound semiconductor industry.
A band-aid solution
Tending to employ mono- and multi-crystalline silicon photovoltaic (PV) solar panels, today’s solar farms are causing some headaches for global grids.
Due to the tremendously successful cost reduction of silicon PV, its deployment is now so extensive that it has led to market saturation during solar hours. Midday prices have been driven to zero and below, while overwhelmed grids are curtailing solar output. Then, as soon as the sun sets – or even disappears behind a cloud – alternative generation has to kick-in immediately, in order to satisfy demand.
Gas generators or lithium-ion batteries that can quickly respond to changes in grid loads have become the default solution to fixing grid instability issues caused by fluctuations in renewable energy output. However, while power from silicon PV and wind is inexpensive, the cost of open-cycle gas generation and electro-chemical battery storage is certainly not. In fact, the cost associated with solar-PV-plus-batteries is so high that their use alone would likely prevent the mass deployment that is needed for decarbonisation. Or, to put it bluntly, gas generators and lithium-ion batteries remain a band-aid solution suitable for short-term support. In reality, what’s needed to decarbonise the world’s electricity grid is large-scale deployment of renewable energy alongside low cost, bulk storage.
RayGen’s solar-and-storage
Our proprietary technology (see Figure 2) is designed to do just that by addressing the growing need for renewable generation paired with bulk storage. The world-first approach to solar that we are taking – described in jargon as ‘tower-mounted concentrated photovoltaic co-generation’ – is the key enabler for our trailblazing approach to storage, which we describe as water-based electro-thermal energy storage or ‘Solar-Hydro’.
Beneath each solar tower in a RayGen solar system are nearly three hundred wireless, automated, dual-axis heliostats that track the sun’s movements across the sky. These mirrors concentrate sunlight by a factor of almost one thousand onto the receiver that’s positioned at the top of the tower.
The receiver incorporates more than four hundred RayGen modules. The surface of each is just 10 cm by 10 cm in size, less than an inch thick, and populated by one hundred highly efficient III-V triple-junction GaAs-based solar cells. Operating with an efficiency approaching 38 per cent, these cells directly convert the concentrated beam into electricity.
A sophisticated cooling system keeps the cells within their operational limits – and generates 90 °C heat as a by-product. This cooling system includes an electrically insulating, thermally conducting industrial ceramic and a water-cooled heat sink.
Each module produces 2.5 kW of electricity and 5 kW of heat – equivalent to a rooftop of a typical home fitted with silicon PV and solar-hot-water panels. As there are 441 modules in a receiver – just over 4 m2 of active area – this produces 1 MW of electricity and 2 MW of thermal energy. The RayGen solar system has been in operation since 2014. Over the
intervening years there have been multiple iterations to the module, the
receiver, the heliostat and the control system.
Figure 2. (1) A field of mirrors concentrates sunlight onto raised
RayGen solar modules. (These modules are high-efficiency and actively
cooled). (2) RayGen’s solar modules convert sunlight to power with
approximately 90 percent efficiency – 30 percent to electricity and 60
percent to heat. (3) Captured hot water (by-product from the cooling
system of the modules) is stored in a nearby water reservoir. (4)
Generated electricity chills water in a second reservoir or is sold to
the grid. (5) The insulated reservoirs maintain a temperature difference
of 90 °C. (6) The stored difference in temperature is used to drive a
heat-to-power engine. (7) This turbine provides the grid with reliable,
on-demand power and an option for baseload power.
We use a suite of our proprietary IP to integrate some established technologies to create a new product. Tapping the natural synergies between the components delivers a new level of performance. We are the only company that has successfully demonstrated tower-mounted concentrated photovoltaic (CPV) co-generation, which physically separates the concentrator optics (mirrors) from the solar converter (modules), using proprietary software to ensure alignment. We are able to leverage expertise and investment in heliostats from the solar thermal industry, and employ the highest efficiency cells produced for satellites. Like silicon PV – and unlike previous versions of CPV – our system is modular and easy to manufacture, with mass-volume heliostats produced via an established and separate supply chain to our own high-performance PV module production.
Another strength of our technology is that it provides a higher capacity factor for solar generation than most silicon PV projects. Our system is limited to using direct normal irradiance – a measure of cloudless sunshine – but overcomes this restriction with a few innovations. We employ dual-axis tracking to capture more of the sunlight in the morning and afternoon, along with low-cost ‘booster’ heliostats to add extra concentration outside peak sun periods.
The approach that we are pioneering produces electricity with a similar land area and generation profile to silicon PV, but at a competitive or lower cost, and with the added benefit of by-product heat. The heat is crucial to energy storage, allowing our system to shift its electricity production from the middle of the day, when prices are low, to the evening and winter months, when prices are high. RayGen’s ‘water battery’ The surplus energy that’s generated by our system is stored in a ‘water battery’ and subsequently recovered via a heat engine.
We store our by-product solar hot water at 90°C in what is known as a stratified hot-water pit thermal-energy storage system. Such systems were developed for Northern Europe, where they are used to store thermal heat from the summer sun as hot water, which provides hydronic domestic heating during the winter. To maintain the high temperature while limiting water loss, these pits are insulated, lined and sealed. This is very effective, with thermal losses of the stored energy typically less than 10 percent over six months.
Within our system, we also employ a second pit of water, cooled to 0°C via an off-the-shelf electric chiller. The chiller is a standard ammonia heat pump, traditionally used in food and beverage refrigeration. The electricity to run the chiller can be drawn from the generation (PV) part of our system, or imported directly from the electricity grid when wholesale prices are low.
Electricity is then generated ‘on demand’ from the temperature difference in the pits with an Organic Rankine Cycle turbine, of the kind widely used in the geothermal industry. The turbine uses a small amount of ammonia as the working fluid, which boils at less than 90 °C. Heat from the hot water pit boils the ammonia, with the resulting pressurised vapour powering a turbine, before the cold water condenses the ammonia back to a liquid in the closed-loop system.
The modest temperature difference of 90 °C between the two pits limits the heat-to-power efficiency. Simple calculations based on thermodynamics give a maximum theoretical cycle efficiency, based on the Carnot Cycle, of 25 percent, while the practical efficiency is in the 12-to-15 percent range.
On the charging side of the storage cycle, the system has a coefficient of performance of 6 or more. This gives the system an impressive round-trip electrical efficiency of between 70 and 80 percent. That means that for every 1 MWh of electricity used to power the industrial chiller when market prices are low, around 0.7 - 0.8 MWh is produced by the turbine when prices are high.
Additional advantages of the modest temperatures are that the storage medium is low cost and thermal losses are low. In many ways our storage system is analogous to pumped hydro. Round-trip efficiencies are equivalent, and the volume of water required for one hour of storage is roughly the same. One way to think about the two bodies of water separated in temperature by 90 °C is that they are equivalent to a pumped hydro system separated in height by 1 km – but without the physical constraint of finding a geographic location suitable for pumped hydro.
Ultimate grid flexibility
RayGen storage can be charged by the electricity generated by the multi-junction cells or by the grid. The latter option can de-congest the grid, acting as a load during times of renewable saturation. If additional storage duration is needed, it’s simply a matter of digging larger pits and filling them with water.
Further, with our technology, it is easy to co-locate storage within a solar renewable-energy zone. By co-locating long duration storage with solar, we increase the utilisation of grid transmission out of the renewable energy zone, leading to a lowering of the cost of delivered power for customers. The turbine generator set provides natural, synchronous inertia and can participate in voltage regulation and contingency markets.
Another feature of our technology is that it can be independently sized. Working with AGL Energy, we have developed a sophisticated techno-economic linear optimisation model for optimising the configuration and operation of our system for different applications and market conditions.
While our approach to renewables is novel, we have selected equipment of existing technologies, using the best bits for our system. We have drawn on pits from Danish district heating, ORC turbines from geothermal plants, and chillers from food and beverage refrigeration; and our solar system incorporates: the modularity and easy manufacturability of silicon PV; the mirror collectors of concentrated solar power; and the high-efficiency cells from satellites and CPV.
Real-world results
Figure 3. Construction of the 4 MW electricity plus 3 MW/ 50 MWh storage
project near Mildura, Australia, is nearing completion. Each solar
field utilises nearly 300 mirrors to concentrate light onto a central
receiver. (The cold and hot water pits can be seen behind the fields of
mirrors.)
Last year we closed a US$40 million Series C funding round to demonstrate the technical feasibility of our proprietary Solar Power Plant. Strategic investments came from global energy majors Chevron, Equinor and Schlumberger; Australia’s largest utility, AGL; listed renewable developer Photon Energy; and the Australian Renewable Energy Agency (ARENA). This financing supported the construction of our grid-connected flagship power plant at Carwarp (see Figures 3 and 4). Following the breaking of ground in the third quarter of 2021, this project is now nearing completion, with commercial operation expected by early 2023.
The Carwarp project is likely to be the first of many by us that will spring up in Australia and, ultimately, the world. Following the successful delivery of this flagship deployment, we will be completing much larger projects that are already in development.
Scaling system capacity is relatively easy, with larger projects simply requiring more solar fields and larger, off-the-shelf turbines. This will involve scaling the 3 MW turbine used in the Carwarp project to the typical 25 MW turbine used for geothermal applications. Future projects will likely be deployed in ‘blocks’ of 50 MW of solar plus 25 MW of storage, with storage capacity scaled to fit a project’s specific requirements.
Targeting high-volume deployment, we are focused on developing utility-scale projects with our strategic investors. One example is our partnership with Photon Energy, which has secured land in the Eyre Peninsula, South Australia, for a project that combines 300 MW of solar with 150 MW of storage, backed by 3.6 GWh of storage capacity. This project, on track to receive development approval in 2023, will be larger than any battery project in construction or operation.
Figure 4. Four RayGen solar towers during commissioning. RayGen’s
storage construction is nearing completion and will be operating
commercially in early 2023.
The challenge ahead
Over the coming years the deployment of renewable energy is sure to grow, which will increase the need for long-duration storage. This expansion has exciting implications for epiwafer capacity within the compound semiconductor industry.
To remain competitive, we will need to keep pace with cost reductions in the incumbent technology, silicon PV. This will be supported by a move to higher-volume, lower-cost III-V cells, which will hinge on modifications to the existing epitaxial approaches for higher-volume throughput per reactor, such as the Dynamic HVPE technology pioneered by NREL (see p. 26 in this issue), alongside automated cell processing.
With ample headroom for further enhancement in III-V multi-junction cell performance and cost, the future looks bright for both ourselves, and for the compound semiconductor industry.
Main image:
Figure 1. Srinivasa Balamurugan, module manufacturing expert, holds a solar module, fabricated at RayGen’s automated module manufacturing facility in Melbourne, Australia. The small 10 cm x 10 cm module produces 2.5 kW of electricity and 5.0 kW of heat under 750x concentration.