Precitec launches Flying Spot Scanner
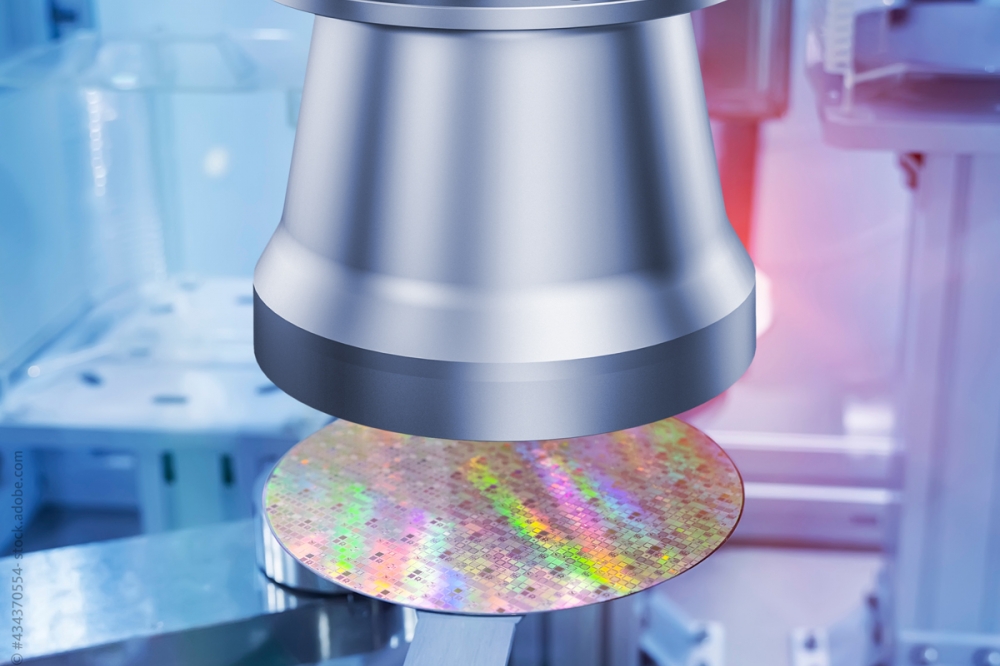
Features include flexible scan trajectories, the ability to measure 12 inch wafers and a Z resolution in the nm range
Precitec, a German manufacturer of sensors and optical probes, has launched the ultra-fast Flying Spot Scanner (FSS) 310 for bow, warp, TTV and quality inspection of semiconductor wafers in shorter cycle times. Its features include flexible and highly efficient scan trajectories, the ability to measure 12 inch wafers and a Z resolution in the nm range.
The FSS 310 combines OCT with wide field-of-view scanning and solves the issue of ultra-precise measuring systems normally working very slowly and being extremely expensive. According to Precitec, this scanner’s flexible and fast-moving measurement point within a wide field of view enables non-contact ROI inspection in much reduced cycle times – with no comprises on accuracy.
Thanks to its scan area of 310 mm, the FSS 310 will measure the total thickness variation (TTV), bow and warp of an entire 12-inch wafer and detect any voids in a single scan – and do it in as little as 10 seconds per wafer for standard applications.
The FSS 310 enables a throughput of over 300 wafers per hour (including handling time). The key to such speed is the FSS 310’s in-built scanning system which allows the long paths of linear axes to be replaced by short rotary movements. This significantly reduces measuring times and does away with the need for a precision axis.
When combined with devices from the Precitec CHRocodile 2 IT family, the FSS 310’s fully variable scan trajectories, which the user can program, enable thickness and distance measurements of, for example, Si, doped Si, GaAs and SiC wafers. The FSS 310 can also measure the thickness of semiconductor component coatings (e.g. partial foliation of wafers) as well as measuring the bow of individual dies on wafers prior to further processing.
Secure Your Hydrogen Supply
A study supply of high-purity hydrogen is critical to semiconductor fabrication. Supply chain interruptions are challenging manufacturers, leading to production slowdowns and stoppages. On-site hydrogen generation offers a scalable alternative for new and existing fabs, freeing the operator from dependence on delivered gas.Plant managers understand the critical role that hydrogen plays in semiconductor fabrication. That important job includes crystal growth, carrier gas, wafer annealing, and in the emerging Extreme UV Lithography (EUV) that will enable new generations of devices. As the vast need for semiconductors grows across all sectors of world economies, so does the need for high-purity hydrogen.
Take control with Nel on-site hydrogen generation.
Read more