World's first monolithic InGaN RGB LED for µLED displays
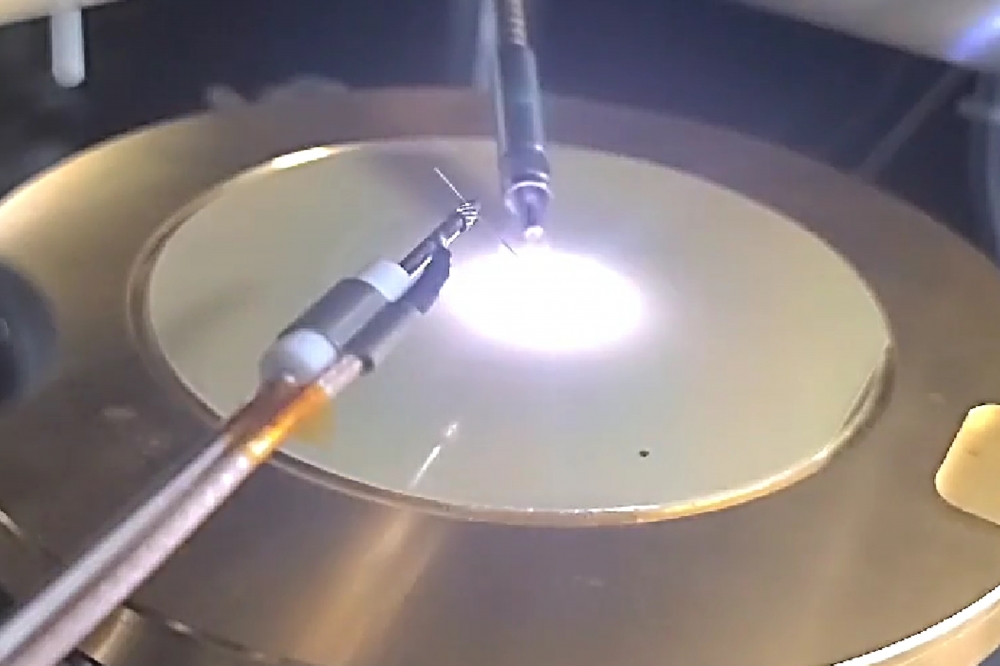
Soft-Epi and Sundiode develop RGB stacked epi wafer for µLED
In a World first, Soft-Epi and Sundiode have jointly developed a monolithic red, green and blue (RGB) stacked epi wafer for micro LED displays using only InGaN materials without wafer bonding. This is another big step for micro LED displays after the development of an InGaN based red LED last year.
South Korean-based Soft-Epi has a unique GaN epitaxy technology, with a focus on manufacturing InGaN epitaxial growth for visible light including nitride-based red LEDs. Sundiode is a US Silicon Valley based company that develops micro LED technology for display applications including augmented reality (AR) and mixed reality (MR) as well as heads-up displays (HUDs).
In order to realise a next-generation full- colour micro-LED display with ultra-high resolution (5000 PPI), it's necessary to go through a very complicated process of using wafer bonding technology and removing the substrate after individual epitaxial growth of R, G and B on each wafer. This process has been the biggest problem in implementing full- colour micro LED displays.
The two companies have realised the world's first RGB epitaxial layers with independent pn junctions on a single substrate with a single epitaxy growth without additional wafer bonding process. This new development has been made through Soft-Epi's epitaxial growth technology and Sundiode's design technology.
This is completely different from the previous conventional method, wafer bonding technology, or colour control method using wavelength shift according to current density change. It is a monolithic stacked RGB structure that can drive RGB colours independently. This is regarded as an ideal RGB pixel structure for manufacturing high-resolution micro-displays.
Above is a schematic diagram of the RGB LED epi structure (left) and its emission image (right). The RGB layers are connected in series through a tunnel junction. The final structure to be used as an actual micro display has added current blocking layers to the epi structure and RGB is driven independently.
Monolithic RGB epitaxial growth technology has the advantage of greatly simplifying the process of manufacturing high-resolution full- colour micro-display compared to the existing conventional method of bonding individual red, green, and blue wafers or the method of implementing RGB by repeating epitaxial growth several times using selective growth technology.
It is also expected to greatly contribute to the manufacturing process of micro LED displays for large screens (signage, TV, etc.). Compared to the existing method, the number of chips used can be reduced by a third, and the chip transfer process can be reduced to a third or less, which will lead to manufacturing costs reduction significantly.
This development is expected to be an important milestone in manufacturing technology for high-resolution, full- colour micro displays based on micro-LEDs. An expert in Micro LED said for this development, "Soft-epi has cracked the code for micro LED, and it's an important milestone for high-resolution, full- colour micro displays."
Soft-Epi and Sundiode are now developing a monolithic RGB micro display prototype as the next step. They expect that this successful development of the monolithic RGB epi wafer is significant in that it has secured an important basic technology that enables high-resolution micro-displays suitable for AR and MR as well as HUD devices.
The following link is a video of 'the monolithic vertical RGB LED.
Secure Your Hydrogen Supply
A study supply of high-purity hydrogen is critical to semiconductor fabrication. Supply chain interruptions are challenging manufacturers, leading to production slowdowns and stoppages. On-site hydrogen generation offers a scalable alternative for new and existing fabs, freeing the operator from dependence on delivered gas.Plant managers understand the critical role that hydrogen plays in semiconductor fabrication. That important job includes crystal growth, carrier gas, wafer annealing, and in the emerging Extreme UV Lithography (EUV) that will enable new generations of devices. As the vast need for semiconductors grows across all sectors of world economies, so does the need for high-purity hydrogen.
Take control with Nel on-site hydrogen generation.
Read more