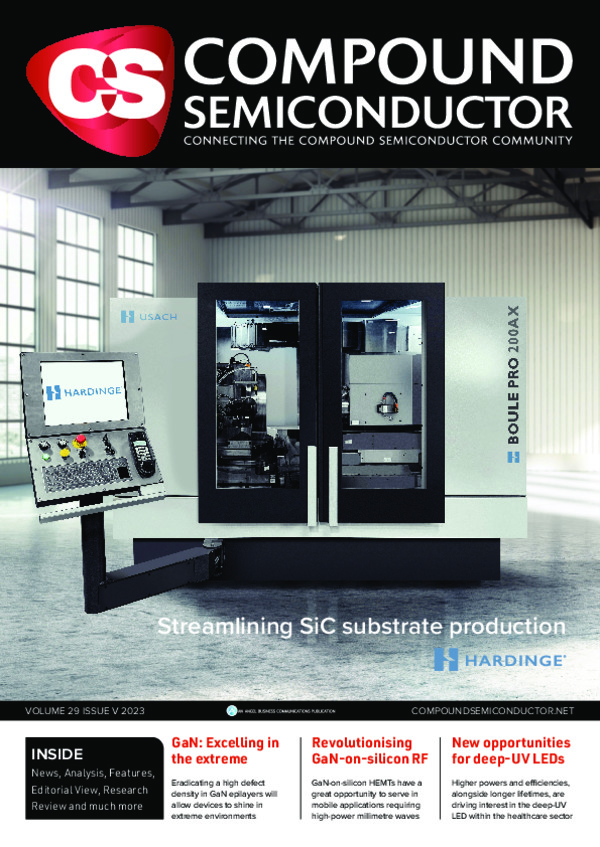
Streamlining SiC substrate production
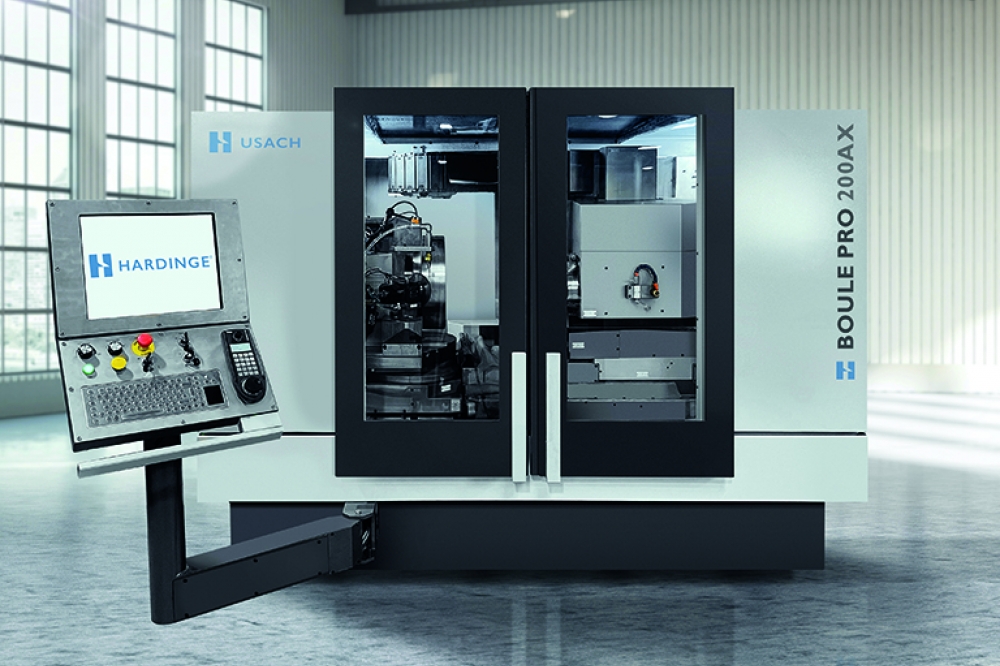
A breakthrough tool delivers pinpoint accuracy when producing wafer-ready SiC pucks.
BY JEFF GUM FROM HARDINGE.
Inefficient and costly. It is those two words that best describe the traditional approach to shaping SiC boules.
However, there’s now a new era for producing the wafer-ready SiC crystals. It began in late 2022, when our team at Hardinge introduced the BoulePro-200AX. With its single step dual-plane compensation capability, it is streamlining the SiC industry’s process for transforming an as grown boule to a wafer-ready puck. Our launch of the BoulePro could not have come at a better time, given the incredibly high level of demand for SiC, which is the vital semiconductor material for the advancement of electric vehicles and other high growth markets.
There are a number of reasons behind the SiC industry’s need for a new method for boule shaping. Concerns come from the inefficiencies of using multiple tool sets to perform different functions, as well as the need to employ several operators to work these tool sets; the time lost to gluing and de-gluing boules to carriers for different steps; the increased process variation that comes from manual material handling and setups; and a lack of best practices driving optimisation and improvement.
With 130 years of grinding and materials knowledge, our development team, supported by key SiC industry experts, has addressed all the inefficiencies of SiC boule processing by creating a comprehensive and cost-effective package. Our process optimisation enables significant cost reduction across the board, including consumables, OpEx, and CapEx.
For the last couple of years, we have been collaborating with a handful of SiC raw material suppliers to optimise the production process for fabricating a wafer-ready SiC puck. Drawing on deep experience in grinding, turning, milling, and workholding, we have slashed costs through the optimisation of the right processing speeds, angles, workholding and machining tool types, as well as the incorporation of X-ray metrology into the machine.
Figure 1. The general process flow for producing a SiC puck is: boule
load (manual or automated); application of the initial outside diameter
(OD); rough dome grind; XRD taken; finishing the dome grind to the
correct orientation; handoff to secondary workhead; seed side removal;
XRD to confirm; a final OD and flat/notch; and removal of the
wafer-ready puck (manual or automated).
Efficiency improvements
Our BoulePro 200AX, with its manufacturing capabilities, checks all the boxes for improved process flow. This fully automated, self-contained machine tool can process as-grown SiC boules to wafer-ready pucks with no gluing/fixturing, external material setup or manual intervention.
Another strength of our BoulePro is its single step, dual plane compensation capability, enabled by inclusion of integrated X-ray diffraction. Thanks to this feature, the BoulePro carries out all the steps of the boule-to-puck conversion process in a dramatically shortened period.
The traditional process flow for transforming a boule into a SiC puck can be adjusted from customer to customer, and from boule to boule. However, in general it begins with a manual or automated boule load, followed by machining the initial outside diameter, applying a rough dome grind and assessing the crystal orientation with X-ray diffraction. After this, a finish dome grind corrects the orientation, prior to handoff to a secondary workhead, seed side removal, a confirmation measurement by X-ray diffraction, the application of a final outside diameter and flat/notch, and finally manual or automated removal of the wafer ready puck (see Figure 1 for an illustration of this process).
The BoulePro slashes the time it takes to process a boule into a puck. While traditional approaches take over 24 hours, with the BoulePro it’s just 2-3 hours, using an automated single setup solution. This saving in time contributes to a total cost reduction of nearly 70 percent, when taking labour, manufacturing footprint, scrap, capacity efficiency, and consumables into account (for details, see Figure 2). This gain will play a key role in helping SiC producers to reduce their production costs and grow the industry utilisation of this wide bandgap material.
Figure 2. The use of the BoulePro-200AX slashes CapExc, OpEx and costs associated with consumables.
The secret sauce
Without an industry standard Process of Record to produce wafer-ready SiC pucks, manufacturers have turned to individual approaches. In all cases, they employ a five-step process that begins by using X-ray diffraction to determine the crystal structure for the correct surface orientation, before applying a flat or notch. Outside diameter grinding follows, and then the removal of the seed side and the dome side.
Our experts have evaluated the steps in this process and their inherent inefficiencies. Drawing on our background as an international provider of customised grinding solutions, we have embarked on a clean sheet approach to an all-in-one solution, leveraging core expertise from more than a century of grinding experience.
The result of this effort, the BoulePro, is built on our industry leading USACH grinding machine platform. It features an integrated X-ray diffraction tool and a 5-axis capability, which enables it to orient, X-ray, grind, and/or cutoff the part to the customer’s desired specifications. This is accomplished with full automation. Note that the BoulePro is capable of handling all current relevant sizes of SiC boule, including 100 mm, 150 mm and 200 mm material.
Key to the exceptional efficiency of our tool is its advanced workholding of the SiC boule. There is no longer a need to glue and de-glue the boule to fixtures throughout each of the process steps – that is a major, incredibly time-consuming issue that current SiC producers face. In addition, the BoulePro eliminates the removal of the boule from one machine, along with its preparation for the next step and its installation in another tool.
An imperative component of the BoulePro is the integrated X-ray diffraction system. It’s essential to identify the crystal orientation, which is needed to ensure the proper placement of the primary flat or notch, and to machine the puck with the correct compensation in all planes. By taking this approach the full puck, from end to end, yields wafers with the correct orientation and geometry. With the BoulePro, the output from the X-ray diffraction system informs the tool of the location of the flat or notch, and how much of an adjustment must be made to crystal surfaces when final machining.
Another advantage that results from having the ability to perform X-ray diffraction analysis in situ, at any step the process allows, is the opportunity to switch the order of the process steps. One consequence is that the flat or notch can be applied later in the process, ensuring its orientation is highly accurate.
The Boule in the workholding on the left and the XRD (X-ray) machine on
the right. The XRD is measuring the crystal orientation so that it is
known and can be corrected in subsequent grinding steps.
Additional capabilities
There’s more to the BoulePro than what meets the eye. Along with its featured proficiencies, additional capabilities can be included upon request.
One of these is the identification of foreign polytypes by UV light inspection. When SiC boules are placed under UV light, certain foreign polytypes, such as 6H, show up as a different colour. Identifying the location of the 6H inclusions allows their removal by the BoulePro, ensuring that the final SiC puck contains only the desired 4H polytype.
It’s also possible to add the capability to apply a laser scribe to the surface of the finished SiC puck. This allows customers to track the lot number, the boule number, and so on. It is a feature that is valued for material tracking purposes.
Another capability that can be included within the BoulePro is a vision system. This can take high end photos of the boule or puck at any stage of the process, a feature desired by some customers.
The prototype machine in Elgin, IL that is being used for further development and customer demonstrations.
Embracing the BoulePro
This year customers from all over the world have been visiting our facility in Elgin, Illinois, to see the BoulePro in action. This facility is home to our USACH brand of specialised application grinding machines. Our team of engineers and application specialists at this facility drew on their expertise to quickly get a prototype BoulePro up and running to demonstrate this machine’s capability. Visitors to the facility are now seeing how the production of SiC pucks can be undertaken with the final design of this machine, which we expect to ship later this year.
Even in its prototype form, customers are eager to see the BoulePro in action, given the market’s rapid expansion. These visitors want to see first-hand how the BoulePro can accommodate their unique boule geometry through a full production process. After seeing what it can do for them, they leave with a spring in their step, excited by both the flexibility of the BoulePro, and how well our engineering and application experts adjust to their demands.
One area that has amazed our customers is the precise accuracy of the BoulePro, with its built-in X-ray diffraction machine. Due to the flexibility in the order of operations for the BoulePro’s process, and as all parameters are controlled extremely tightly, our machine produces the angular correction on crystal orientation up to 100 times more accurately than the manual process currently used today. What this means for SiC producers is that they can meet and even exceed customer expectations and requirements as specifications evolve.
The BoulePro’s bright future
Exciting times lie ahead. We have expansion plans underway to cater for increased volumes, given the market’s overwhelming excitement for the BoulePro. Demonstrations are ongoing throughout 2023, with the first batch of customer machines scheduled to ship before year-end. We will utilise our global footprint to meet customer demand and aftermarket need, to ensure that our BoulePro supply and support services match customer requirements.
SiC presents unlimited opportunities in many other growth markets as well, and our BoulePro’s general configuration and capabilities enable it to be a solution for these applications. We are excited to be at the forefront of this revolution, and viewed as a reliable trusted manufacturing partner that global SiC producers can count on for their fabrication needs.