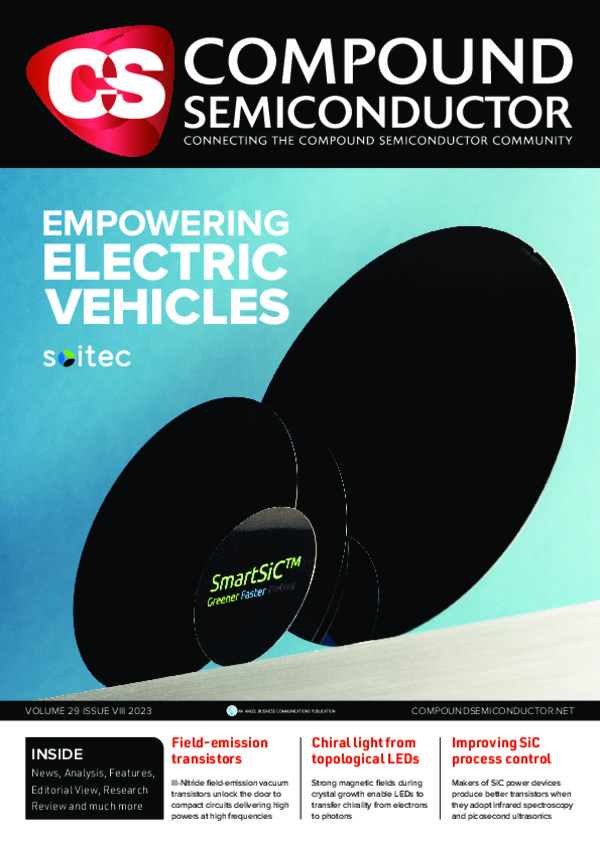
Antimonides enhance avalanche photodiodes
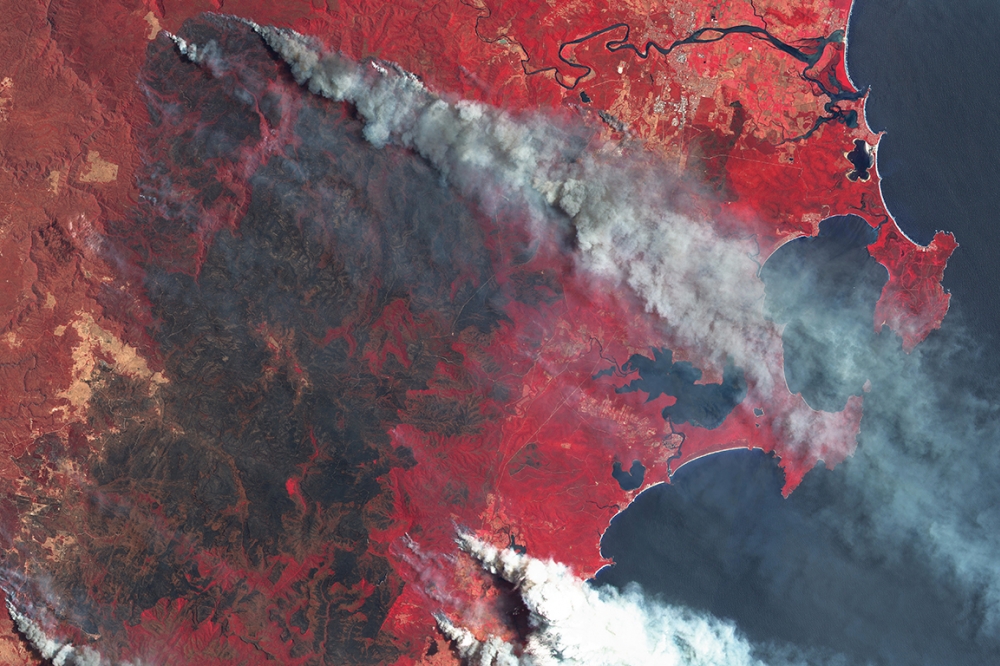
Turning to antimonides for the fabrication of avalanche photodiodes
delivers high gain in the infrared, while quashing excess noise.
BY SANJAY KRISHNA FROM THE OHIO STATE UNIVERSITY
In days gone by, we had the weather after the news. But now the weather is the news – well, to be fair, not all of it, but certainly more than ever before. Take this year, for example. During the summer the various social media platforms focused coverage on exceptional heat waves in the US, central Europe and China that sparked substantial wildfires. More recently, it’s pictures of floods that fill our screens, with torrential rain causing bursting of dams in Libya.
A contributing factor behind all these extreme weather events is global warming, fuelled by ever higher greenhouse gas emissions. In order to tackle climate change, it is crucial to monitor these emissions as we implement emissions reduction efforts.
One option for observing the emission of gases that contribute to global warming is the deployment of instruments on the ground. But this is incredibly time-consuming, expensive, and provides only limited coverage. Far better is to equip satellites with suitable remote sensing instruments, which gather timely and continuous data as they orbit the globe.
A suitable technology for observing the Earth’s greenhouse gas emissions from space is lidar. Lidar, which stands for light detection and ranging, is similar to radar but uses lasers and optics instead of microwave radiation. Lidar instruments can be fitted onboard satellites, including the International Space Station, allowing measurements at an altitude of 400 km.
Lidar is now a reasonably mature technology, in part due to its recent proliferation in self-driving cars and autonomous airborne drones. Regardless of application, lidar systems consist of a laser, transmission optics, receive optics, an infrared detector and backend electronic circuits, and an optional display for the user interface. However, the range and range resolution of the lidar system on a self-driving car is very different from that required on a satellite.
Figure 1. Room temperature measurement of high gain, low excess noise
and large spectral quantum efficiency in the short-wave infrared (SWIR)
using a GaAsSb/AlGaAsSb heterostructure design on an InP substrate (Lee
et al, Optica, 2023).
Designs for lidar
The detector is just one of key components in any active sensing and imaging system. In such systems, including lidar, there are five key components. The first of these is a transmitter, usually either a laser or an LED, that provides an incident beam. The light source is either focused at a particular target, flood illuminated or flashed across a field of view, or scanned across a scene in one or two dimensions to generate a cloud point image. The second component is the optics, which can be divided into front-end transmission and back-end collection. Depending on system design, the optics may use a single aperture (mono-static) or two separate apertures (bi-static) for illumination and collection. The third component is the back-end receiver, based on a photodetector that converts collected photons into electrons to create a photocurrent; and the fourth element is a back-end electronic circuit, which converts the photocurrent into a photovoltage, using an analogue-to-digital converter to generate digitized bits of information. The fifth component is the software and an optional graphical user interface (GUI) for applications in which there is a human-in-the-loop for decision making. The software provides the timing for the front-end transmission and the back-end information processing. The GUI serves as the interface for the user to customise the system to extract the relevant information pertinent to their application. To meet customer performance targets and price points, system-level integration of these five components demands a careful architectural design.
One key consideration facing the designers of lidar systems is the operating wavelength. Today’s systems are limited to near-infrared wavelengths of around 1 µm or less, primarily because the photoresponse of mature, inexpensive silicon-based detectors and arrays falls off dramatically at longer wavelengths. Similarly shorter wavelength lasers are cheaper and more mature than their longer wavelength counterparts. However, there is much merit in extending lidar systems to longer wavelengths, such as 1.55 µm. Systems operating around that wavelength are inherently eye-safe, since any reflected or scattered light that enters the eye is absorbed by anterior portions, mainly the cornea, so never reach the retina. Infrared wavelengths also undergo far less absorption in the atmosphere, thereby extending the range of the lidar system, an asset for gathering data from space. Moreover, the infrared wavelength is sensitive to vibration of the hydrocarbon atoms, ensuring sensitivity to greenhouse gases such as methane and carbone dioxide. Key to extending the capabilities of lidar to longer wavelengths is to replace silicon, which is held back by the intrinsic physical limitation of its bandgap, with compound semiconductor materials with a narrower bandgap.
Lidar system engineers must ask themselves several key questions, which form a ‘decision tree’ determining the selection of various key components, but especially the detector. One crucial decision is whether the application is for sensing/imaging, or for ranging. Photon budget calculations are also required, determining whether the detector should be an avalanche photodiode (APD), which has a higher sensitivity, or a p-i-n diode. Here we discuss the later, a linear-mode APD. Our focus is on our advances in the figures of merit of this critical component by our team at The Ohio State University.
APDs provide internal gain using impact ionisation and this increases the sensitivity of the receiver. When increasing the reverse bias of a photodiode close to its breakdown voltage, impact ionisation may be realised by optimising the doping, bandgap and thickness of the semiconductor heterostructure stack. Note that impact ionisation occurs when a primary electron, or hole, gains enough energy under a high electric field – the energy must be far more than the bandgap of the material – to knock off secondary electrons or holes. When this occurs, a multiplication process results that provides internal gain, increasing the photocurrent (and unfortunately the dark current too).
Figure 2. Variation of the impact ionisation ratio of electrons and hole (α/β) versus spin-orbit energy for various compound semiconductor materials from nitrides, phosphides, arsenides and antimonides to bismides. This trend seems to suggest that there is an interesting correlation between the size of the atom in the periodic table and the spin-orbit/impact ionisation mechanisms.
APD architectures
APDs fall into two categories: those that operate in linear mode, and those that are referred to as Geiger mode.
For linear-mode APDs, as the name suggests, the multiplied photocurrent is proportional to the primary photocurrent, with the proportionality constant a figure of merit called multiplication gain. Unfortunately, due to the stochastic nature of the impact ionisation process, there is an excess noise that also arises – and it is dependent on the gain. In other words, excess noise increases as the gain is increased.
Geiger-mode APDs operate in a markedly different manner, delivering a large burst of current when detecting incident photons. For this class of APD, output is not proportional to the number of incident photons, and a quenching circuit tends to be incorporated to limit the current in the circuit. In Geiger mode configuration, it’s possible to produce single-photon APDs, offering ultimate sensitivity. However, Geiger mode devices requires more complex circuitry, and they are susceptible to damage from stray light.
For the linear-mode and Geiger-mode APDs, the key figures of merit are very different, as well as the semiconductor heterostructure architecture and design. The focus of our team has been on short-wave infrared linear-mode APDs, formed by growing antimonide-based heterostructures on InP substrates.
To optimise the performance of linear-mode APDs, one should maximise the quantum efficiency and gain, while minimising bulk dark current, surface dark current and excess noise. While optimising these five parameters, there’s a need to adhere to constraints placed by the system designer and the application engineer, such as those relating to size, weight, power, cost, operating temperature, allowed bias voltage, radiation hardness and environmental stability. For a given linear-mode APD technology, the device designer must also understand the component that is limiting the signal-to-noise ratio and optimise the device architecture and material stack accordingly.
Our research group takes all of these considerations into account when developing antimonide-based APDs on InP substrates that incorporate a separate absorption charge and multiplication design. Note that this foundation makes a lot of sense for our devices, given that InP substrates are available in large diameters, and there is significant development of silicon-based photonic devices using InP substrates. With our design we have realised the highest reported gain and the lowest excess noise factor at room temperature in the short-wave infrared region (see Figure 1).
While our antimonide-based APDs demonstrate promising performance, we still need to address several challenges in semiconductor design, epitaxial growth, surface passivation and radiometric testing.
There are two directions of research with these material systems. One is toward the understanding of the underlying physics of the multiplier portion. We are now reaching the point where we need to go beyond the McIntyre model, which provides a well-known analytical formula for the excess noise factor associated with avalanche photodiodes, to models offering a true deterministic gain. Taking this step would allow us to pinpoint the location of the impact ionisation event and the value of the impact ionisation coefficient. Our initial experiments and modelling with antimony-containing compounds suggest that they have increased spin-orbit coupling, leading to alloy scattering as the dominant scattering mechanism. This has important consequences, such as low excess noise factors and a low breakdown voltage coefficient – both require further investigation.
Members of the Krishna Infrared Detector (KIND) laboratory at Ohio State University.
Our second direction of research is the pursuit of higher sensitivity and speed. Applications such as lidar, remote sensing, and 3D imaging are going to push the limits of the performance of the APD, so choices must be made related to device optimisation parameters. The use of antimonide materials in Geiger-mode APDs could also be interesting. However, this will require careful understanding of the defect states in these materials, as well as the carrier dynamics that limit after-pulsing and dead time. Finally, if true photon resolving detectors are developed, this could unleash new frontiers for APDs and create new applications in areas like quantum information sciences and long-range remote sensing.
For the latter, progress can’t come fast enough. While it’s a step too far to suggest that humanity depends on better detectors, having them will improve the monitoring of greenhouse gases, a crucial first step to curbing global warming, undoubtedly the biggest issue facing us all in the twenty-first century.
•We would like to acknowledge our group members and our collaboration with Prof. Joe Campbell, Prof. John David and Prof. Grein’s research groups. We acknowledge the support of Directed Energy–Joint Technology Office (DE- JTO) and NASA’s Earth Science Technology Office (ESTO).