CPV: Is a resurgence inevitable?
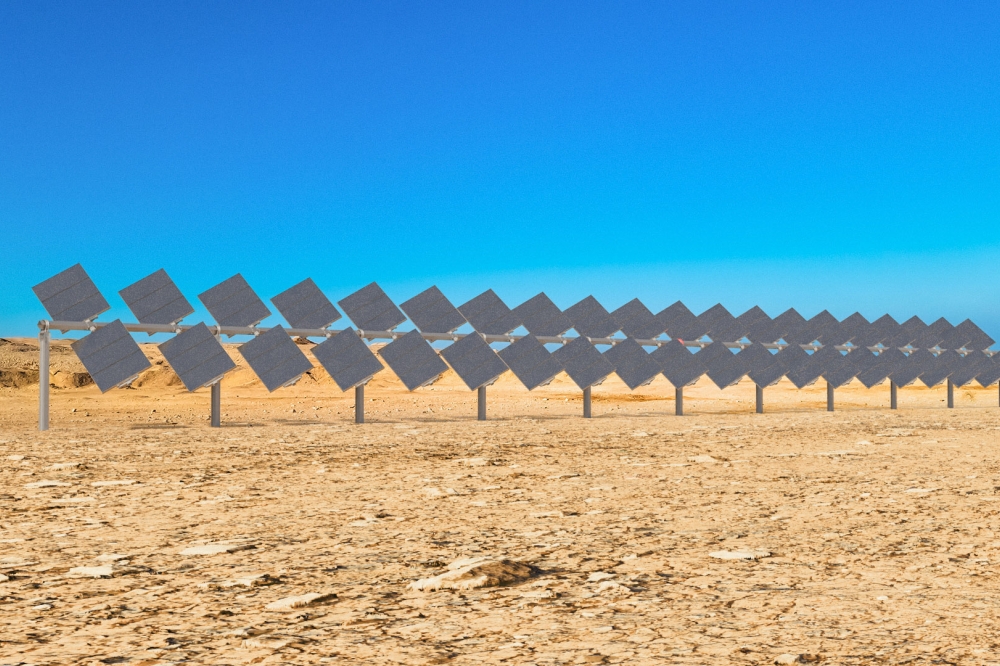
With record-breaking efficiencies and frugal materials usage, can concentrating photovoltaics (CPVs) succeed in tomorrow’s solar sector?
BY RICHARD STEVENSON, EDITOR, CS MAGAZINE
Silicon is the entrenched technology for photovoltaics. Sales of panels made from this material are continuing to soar, supported by decades of high-volume production that cause prices to fall and ensure that this technology is ever more competitive. It’s a direction of travel that leads many to assume that silicon will always hold a vice-like grip on the solar market.
But it’s not a narrative everyone espouses. Calling it into question is Fraunhofer ISE academic Frank Dimroth, who is helping to commercialise a refined and superior design of CPV.
He argues that alternatives to silicon with superior efficiencies have good long-term prospects, based on the premise that investors in solar technology will always seek higher performances and a good return on the land they are using for power generation. Consequently, these investors will want to select the solar technology that delivers the highest level of energy generation per unit area, a metric where silicon struggles.
The thought of shifting away from silicon will surprise many, given the vast amount of land that is unsuitable for the likes of farming and building dwellings.
“But even in the deserts, [land is] not really always available, because there are constraints in terms of not having a huge impact on the environment,” counters Dimroth, who points out that governments only permit a certain amount of land to be transformed into industrial renewable-energy fields. Conversations Dimroth has had reveal that in countries such as the United Arab Emirates, where the land that’s available is quite limited, there is a strong desire to produce a lot of renewable energy, making high-efficiency PV very attractive.
Against this backdrop, today’s silicon solar panels are already encroaching their efficiency potential. Due to this, there is motivation a switch to an alternative materials technology that will deliver a significant boost in the power generation density. While this transformation will not happen overnight, and the rise of any alternative will be far from easy, Dimroth believes that there is good reason to believe that silicon’s dominance will diminish eventually.
The two leading candidates for delivering higher power densities are III-V multi-junction solar cells under high concentration (CPV) and tandem solar cells made of perovskite absorbers.
The latter already achieves high efficiencies in the laboratory but there are concerns over its capability to maintain a high performance over many years.
According to Dimroth, the stability of perovskites used in high efficiency solar cells is a major challenge. “There is interaction with moisture which is a fundamental problem,” argues Dimroth, who points out that ion migration also takes place in this class of materials and has been found to accelerate degradation.
Due to this instability, it is not clear whether these cells will ever reach the 30-year lifetime that silicon has today.
“In terms of cost structure, you want to have a very reliable technology that keeps going over 30 years, because then you can depreciate your power plants over 25 or 30 years,” explains Dimroth.
Modules that degrade before then are failing to be commercially attractive, even if they offer gains in efficiency over silicon.
With CPV, cell efficiencies are ground-breaking – the current world record, held by Fraunhofer ISE, is 47.6 percent – and there are no concerns relating to the robustness and the reliability of this technology which is quite similar to the solar cells used in space satellites for decades.
What’s more, with CPV, volumes of materials required for power generation are relatively low. That’s a big deal, argues Dimroth, given that solar deployments are forecast to climb substantially over the coming years, before plateauing at around 3.4 TW per annum in 2037. To put that figure in perspective, all the PV deployed until now stands at around just 1 TW.
If 3.4 TW were to be deployed using today’s silicon PV, that would equate to 8.5 billion modules, covering an area of 15,600 km2 – that’s roughly half the size of Belgium. The resources consumed for this level of production are considerable, says Dimroth: “15,600 square kilometre would use all of the glass that is produced by the industry today, and, just as an example, three times more silver than is available on the market today.”
While it is possible to increase production, using less material is more attractive, with CPV excelling in this regard.
Dual-axis CPV systems developed by Fraunhofer ISE and Soltec, and incorporating five-junction cells from Azur Space Solar with an efficiency of around 44 percent, are designed to minimise both the bill of materials and production costs.
A superior solution
Working with partners of the German government funded project micro-CPV and the Spanish firm Soltec, which has tremendous expertise in tracker technology, Dimroth and his colleagues at Fraunhofer have developed a new generation of CPV that boasts a module efficiency of 36.5 percent.
At its heart is a five-junction cell in pilot production at Azur Space Solar. Sunlight at a concentration of 500 to 1000 suns is focused onto the cells, just 750 µm by 750 µm in size, using a combination of a Fresnel lens and a glass ball that’s approximately 1 mm in diameter and sits on top of the photovoltaic cell.
One of the merits of this design is that by using such a small cell – leading to the phrase micro-CPV – active cooling is not required. Helping to aid the thermal management is a printed metal circuit with traces transferring the heat away from the cell.
Much effort has been directed at minimising the assembly cost of these micro-CPV modules, which are similar in size to silicon panels, and have all the components sandwiched between a pair of glass sheets.
Contributing to a trimming of the costs is the use of glass balls for secondary optics that are enabling concentration levels of 1,000 suns. These balls are already produced in high volumes, for example for reflectors in road networks.
As well as a minimised bill of materials, this micro-CPV design promise low assembly costs, realised by exploiting synergies with the emerging microLED display industry. To produce micro-CPV panels and microLED displays, myriad devices have to be transferred onto backplane, with a low cost for the panels key to commercial success. While Dimroth has not come up with all the solutions just yet, he’s working on it, and looking to draw on what’s been developed for the display industry.
Another lever for increasing the back-per-buck is to move to an even higher concentration. “I'm quite confident we can go to even 2,000 suns in the future,” says Dimroth.
To help to refine, assess and validate their cutting-edge form of CPV, Dimroth and his co-workers are evaluating the tracker technology at the manufacturing site of Soltec, in Murcia, Spain.
"We want to demonstrate that this new tracking unit can fulfil the promises in terms of precision and economics,” says Dimroth. There is hope that these efforts, involving dummy modules, will also attract investors keen to support the development of this micro-CPV technology and its tracking unit.
Looking further ahead, Dimroth hopes that in the next 18 months or so, the team will have a fully equipped prototype that fulfils expectation, in terms of power generation. This could provide the foundation for increasing manufacturing capacity for larger scale projects.
It’s a sound plan that will hope to improve the prospects of CPV, which is the ultimate form of solar power generation, in terms of energy yield from a given area.