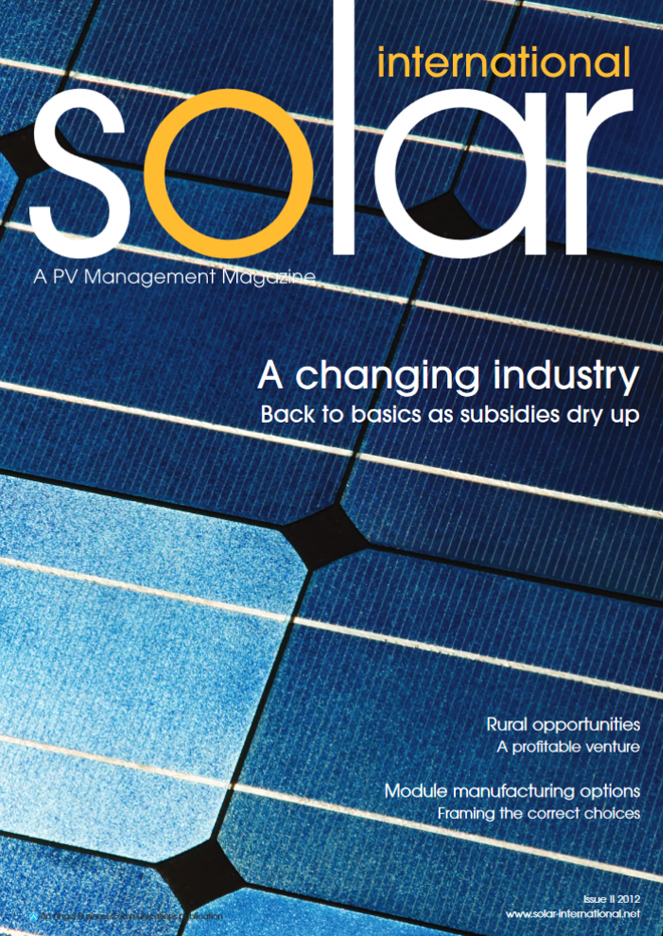
Plessey eyes microLED opportunities
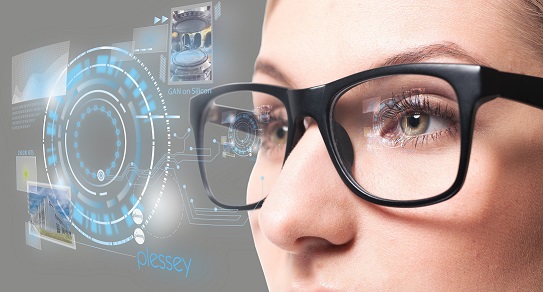
As Apple and Sony turn to microLEDs to deliver next-generation displays, Plessey readies to capture market share with its GaN-on-silicon technology, reports Rebecca Pool.
As Apple, Sony, Foxconn and more embrace microLEDs for spectacularly high resolution, high brightness, low power displays, industry analysts predict the market will explode.
Yole Développement expects more than 300 million displays, based on microLEDs, to be shipped by 2025, dwarfing today's relatively negligible sales. Meanwhile, Research and Markets puts compound annual growth at 53.2%, with the global market reaching $19.89 billion by 2025.
One company intent on capturing market share is Plessey. Having supplied GaN-on-silicon LEDs for several years now, the UK-based LED manufacturer has made a success of growing structures on silicon instead of sapphire.
With its relatively high thermal conductivity, a silicon substrate enables devices with smaller heat sinks and small-scale formats. Factor in the tantalizing prospect of using relatively cheap, large silicon wafers on depreciated CMOS lines, and progress has been quick for Plessey.
Launching LED production at its Plymouth facility in 2010, the company unveiled industry's first commercially available GaN on six inch silicon LED in 2013. Single chip, high power packaged LEDs and horticultural lighting units followed in 2016.
Now, with new market growth in mind, Plessey has revealed its intention to deliver the industry's first monolithic microLED displays by 2018. The company's micro-LED arrays comprise highly efficient emitters that are as small as a micron and provide some 100,000 nits at 1 W, television-equivalent brightness at only 5 mW. Crucially, using these arrays can overcome the tortuous fabrication issues that plague the lion's share of microLED displays.
Today's microLED displays are assembled on a CMOS backplane, one sub-pixel at a time. A 4K television has some 25 million sub-pixels, going some way to explain why most microLED displays have been limited to smartwatches and smartphones.
But as Plessey marketing director, Myles Blake, points out, an array of Plessey GaN-on-silicon microLEDs can be mass transferred onto the CMOS backplane, dispensing with the pick and place minefield and delivering a cheaper, higher yielding manufacture process.
"Display size is purely limited by the size of the silicon, and we are producing our own backplanes that are scalable to any size we like," highlights Blake. "This allows us to perform rapid custom development, and we can develop a custom backplane in just weeks."
"Also, due to the capability of the [pick and place] handlers, the size of today's [emitters] is limited to around 50 microns pixel pitch... but we've proven pixel production to one micron, and theoretically we can go down to sub-micron pixel sizes," he adds.
Blake won't yet reveal display yield figures, but has announced Plessey's intention to license its GaN-on-silicon technology to microLED manufacturers. The company is also working with UK-based optical thin film coating supplier, Artemis Optical, to develop very high brightness, low power head-up displays that are said to be smaller and cheaper than today's devices.
"We really need to get ourselves out into the microLED market place and build up partnerships throughout the supply chain as quickly as possible," he says.
Indeed, it's no secret that the complex and lengthy microLED display supply chain is rather fragmented as bringing together LED production, display manufacturing and assembly isn't easy.
Still as Blake points out: "We are already talking with a large number of display manufacturers and it is never too early to do this. The manufacturing chain is now coming together."
Plessey would like to ramp up UK production, but according to marketing director, Myles Blake, this is unlikely 'as investment appetites stand'.
So what next for Plessey? Right now fabrication takes place on six inch wafers and looks set to remain on this wafer size for the foreseeable future.
"We have proven the capability of GaN-on-silicon on eight inch wafers with our existing MOCVD reactor stacks but we don't yet have the full equipment set beyond epitaxy to run this wafer size," says Blake. "And we have yet to start on twelve inch production."
Plessey also hit the headlines earlier this year with its plans to move towards an intellectual property licensing model rather than ramping UK production. At the time, Plessey chief executive, Michael LeGoff, cited a lack of investment funds, and according to Blake, the company would 'love to scale production' but adds that "˜as investment appetites stand, this almost definitely won't happen in the UK'.
According to Blake, the Plymouth facility currently has two reactors, with associated processing equipment, and could eventually house 14 reactors. Given each reactor can churn out some two million 1mm2 die every week, the potential increase in output rates is significant.
"We will use and also expand this manufacturing capability within the bounds of the current facility," says Blake. "This will be for research and development, and will include a level of manufacturing... but this is small compared to the [multi-billion dollar] microLED market predictions." Clearly the marketing director has high hopes for microLEDs. As he asserts: "I believe that augmented reality and virtual reality will go bonkers during the next few years, with microLEDs providing the foundation to supply the anticipated spike in demand."
But we may yet see more from the UK LED manufacturer. "MicroLEDs will be a key market for us, high brightness LEDs will also be key, but I don't think we have seen the end of our portfolio," says Blake.