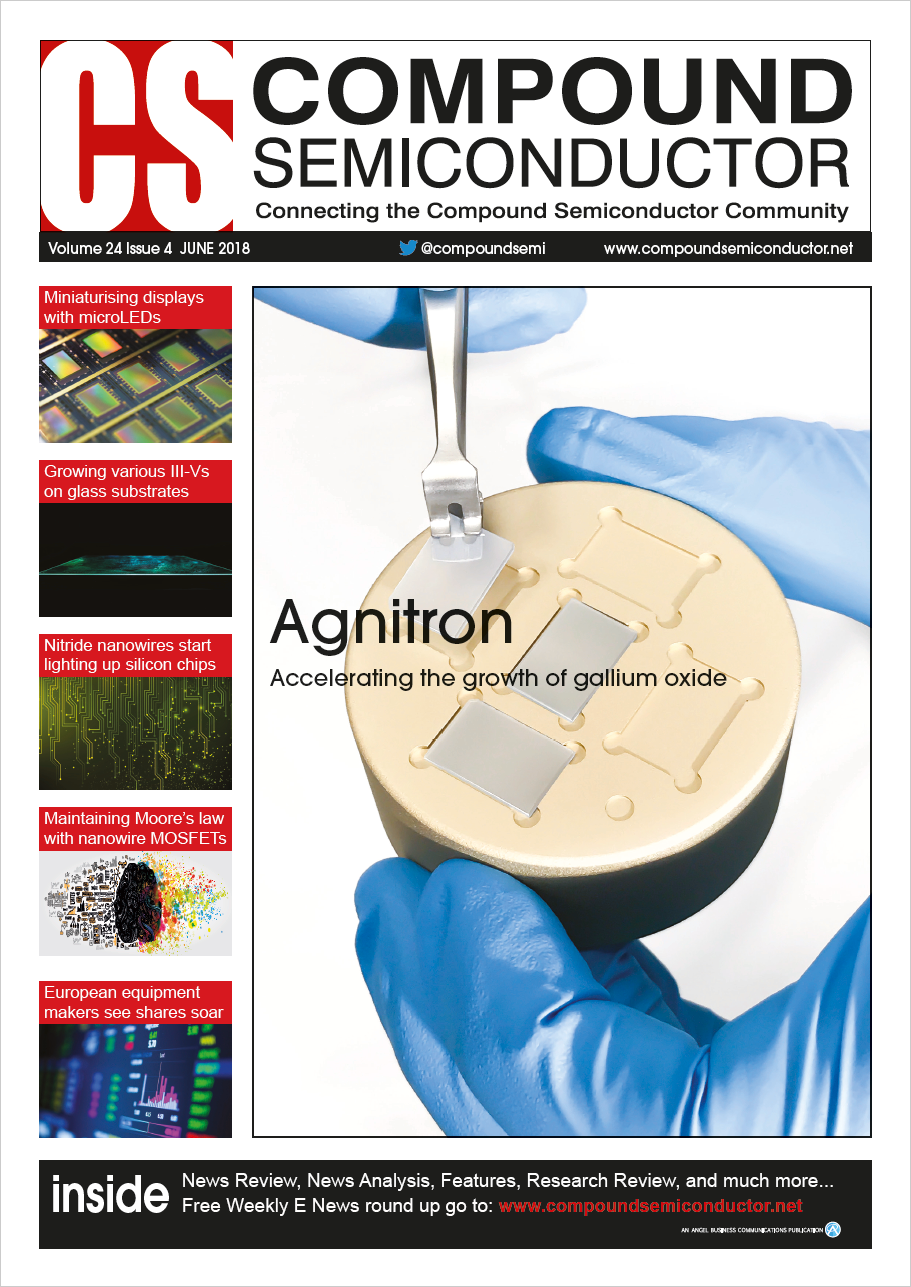
Mastering the manufacture of microLED micro-displays
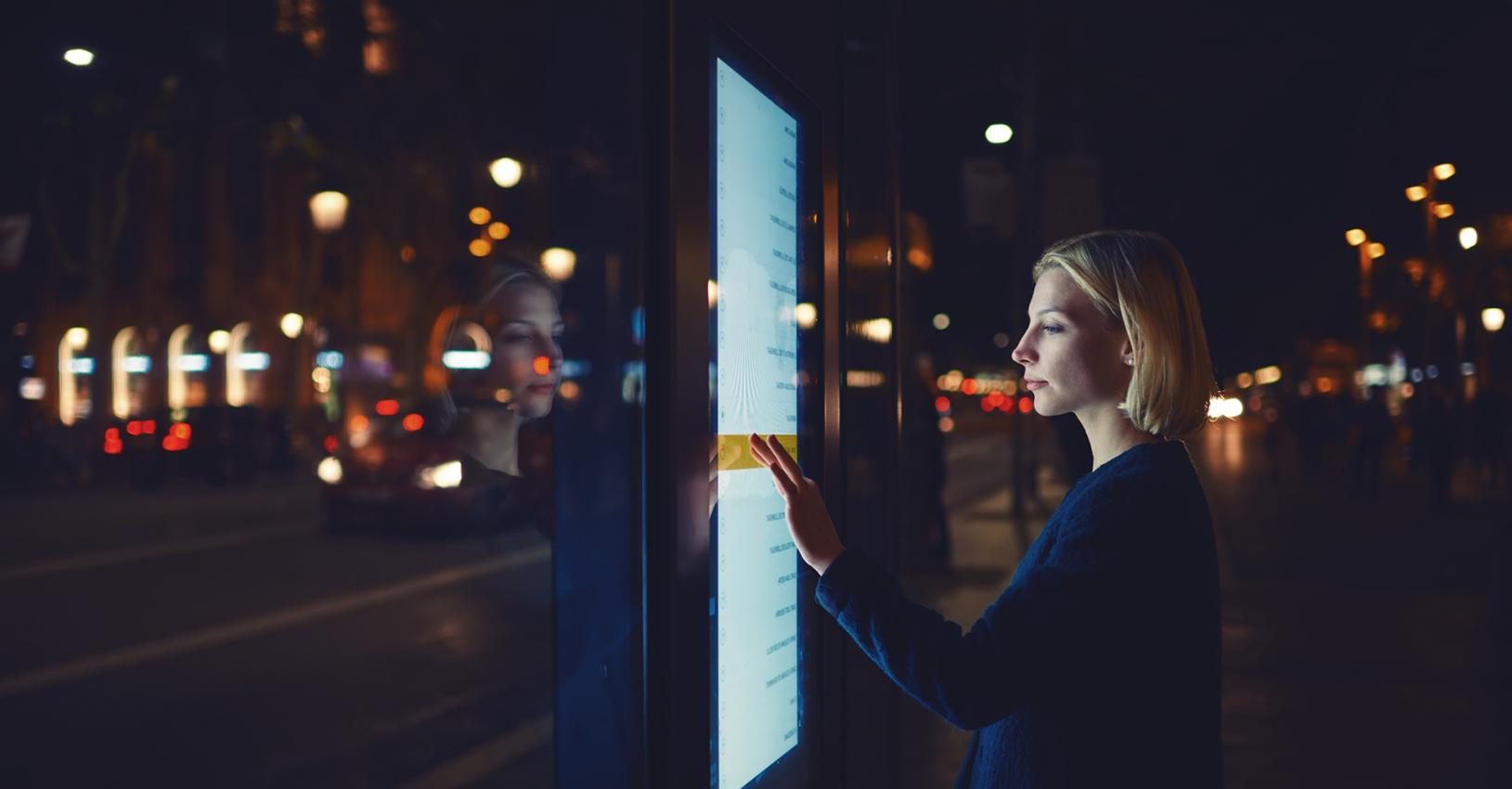
A revolution is now underway in micro-displays. Demand for this technology is rising fast, due to a range of emerging applications that include wearable electronics, head-up displays and augmented reality. However, to succeed in the marketplace, these miniaturized displays, which typically have a diagonal screen size of no more than an inch, will have to meet stringent technical requirements that are not fully satisfied by current technologies.
One of the most promising technologies for forming these micro-displays is based around the microLED. This tiny device "“ the LEDs have dimensions on the order of microns "“ are directly integrated as pixel elements onto the silicon driver IC backplane.
Taking this approach allows the excellent light emission capabilities of compound semiconductor devices to be paired with the unsurpassed functionalities of the ICs. The displays that result outperform those based on liquid crystal and organic LED technologies, by having the upper hand in terms of brightness/contrast, power efficiency, response time and device reliability. However, their manufacture is far from easy, due to the tremendous challenges associated with the integration of compound semiconductor microLEDs and silicon-based ICs "“ devices with vastly different material properties and fabrication processes.
Overcoming these obstacles has been the goal of many researchers in academia and industry, who have been spurred on by the alluring market potential of microLED micro-displays. And many have turned their attention to flip-chip technology, which is the most common method for integrating compound semiconductor functional device arrays with siliconbased ICs.
Flipping the chip
The starting point for the flip-chip approach is the design and fabrication of microLED arrays on one substrate, and the design and production of siliconbased pixel driver ICs on another. Crucially, the geometric layouts on both these entities must be identical.
Chip-level fabrication follows, with the individual chips that contain microLED arrays diced and separated from the original wafer. Using a high-precision alignment bonder, microLED arrays are then flipbonded to silicon ICs using an array of solder bumps. This provides an electrical connection to the pixel driver circuit array.
Aided by good progress in flip-chip technology, some groups have recently reported demonstrations of GaN-based active-matrix microLED micro displays. However, one should note that there are inherent drawbacks associated with flip-chip technology "“ and they limit the performance and cost of microLED micro-displays.
One significant drawback is that as the fabrication process is at the chip level, it requires precise alignment, which hampers throughput and increases cost. In addition, often transparent substrates are essential, because the microLED growth substrate tends to remain after hybrid integration. And yet another issue is that there is a significant thermal mismatch between the compound semiconductor device substrate and the silicon substrate. This difference introduces built-in stress in the microdisplay chips, compromising manufacturing yield and long-term reliability.
What's more, there is limit to how small the pixel size of the microLED can be. It is determined by the capability of the manufacturing equipment and the flip-chip process. Today, there are efforts in industry to realise a pixel size as small as 20 μm, but there is not a foreseeable, clear path with the flip-chip process to shrink this to less than 10 μm while maintaining a reasonable yield and cost. That's a big issue, because microLEDs with a pixel size of less than 10 μm are needed to make displays for augmented reality.
At Jade Bird Display (JBD), a start-up founded in 2015 and headquartered in Hong Kong, we are addressing all the drawbacks of conventional flipchip technology for the microLED micro-display with a novel, wafer-scale technology. At its heart is the transfer of entire compound semiconductor epitaxial layers onto a silicon IC wafer. This is accomplished by wafer bonding and substrate removal. By adopting a wafer-level epi-transfer process, we eliminate the need for precise alignment, a pre-requisite for flip-chip technology, and we are ultimately able to turn to a high-throughput, wafer-scale fabrication process.
Figure 1. JBD's wafer-scale monolithic hybrid integration technology.
Once we have formed our epi-on-IC templates, we use standard semiconductor device fabrication processes to produce our hybrid chips with different functionalities. With high precision photolithography equipment and processes well established in the semiconductor industry, we can fabricate our compound semiconductor functional device arrays on top of pixel driver circuit arrays with sub-micron alignment accuracy. This holds the key to hybrid integration of fine pitch device arrays on silicon ICs with pixel sizes that can be as small as a few microns (see Figure 1).
Another considerable advantage of our technology is that it can utilize well-established infrastructure. Working with equipment sets and semiconductor processes developed by the silicon-based IC industry, we can draw on low-cost mass-production techniques to produce integrated functional hybrid chips, including our high-performance microLED micro-displays.
Figure 2. Packaged red, green, and blue active matrix microLED micro-displays.
Promising prototypes
Armed with our technology, we have already made significant strides in the development of microLED micro-displays. Effort began in early 2016, and we realised our first milestone later that year: our first micro-displays. They exhibited exceptional device performances, combining excellent brightness/contrast with power efficiency and a small device footprint. Even with our first attempt, our prototype outperformed existing micro-display technologies by a substantial margin (see Figure 2).
These first monochromatic red, green and blue micro-displays were made in a VGA format and had a standard definition display resolution of 640 pixels by 480 pixels. The green and blue microLEDs were made from InGaN/GaN-based materials, while AlInGaP/GaAs-based materials were used for the red. All these LEDs had a circular geometry, with a diameter of just 6 μm, and they formed a microdisplay with a pixel pitch of 20 μm, which corresponds to a resolution of 1,270 pixels per inch. Driven at a peak current per pixel of 20 μA, the brightness of the green LEDs in this display can exceed 5x105 nits "“ that's over 500 times that of existing, OLED-based self-emissive micro-displays.
Figure 3. A pixel array with a 20 µm pitch on an active matrix microLED micro-display.
To construct a full-colour micro-display, we could combine three monochromatic microLED microdisplays with external optics, such as a cross dichroic (X-cube) prism. Although this option will appear to lead to increases in the size and volume of the overall display, that's not necessarily the case, because our technology is capable of producing very small microLED micro-displays.
In addition to this approach, which is our current front-runner, we are considering the use of multiple epi transfer processes, which could produce different colour microLED arrays in different layers on the same driver IC substrate. If we were to pursue this, we would expect to use a pixel pitch that is larger than that for our monochromatic displays, as pixels of microLED arrays with different colours will have to be arranged next to each other. Another potential drawback is a reduction in brightness, because light may be blocked by this structure.
To commercialise our core technology, the monochromatic micro-display, we are pursuing a distributed manufacturing strategy. We buy our LED epiwafers, from which microLEDs are made, from conventional LED chip manufacturers. Epiwafers with different substrates can be used to make our displays, so long as the substrate can be successfully removed after the epi-wafer is bonded to the backplane wafer. In most cases, this can be accomplished by making a minor alternation to the fabrication process.
Figure 4. 4-inch wafers of active matrix microLED micro-display chips fabricated using JBD's monolithic hybrid integration technology.
For the backplanes, we outsource the design of the driver IC to firms with extensive expertise in this area, while the tape-out of driver IC backplane wafers is undertaken on a standard 8-inch CMOS line through a foundry service. We use 4-inch LED epiwafers for our demonstrations. To accommodate their size, we tailor 8-inch CMOS IC wafers to 4-inch for subsequent device processing. This part of the production process has been performed at a pilot plant operated by one of our strategic partners (see Figure 4). Note that it is easy to scale production to larger diameters than 4-inch, by switching to larger LED epiwafers.
A major benefit of our manufacturing process is its high degree of flexibility. We can make choices that are influenced by epiwafer availability, IC design capability, and the services provided by a CMOS foundry. Ultimately, by outsourcing, we reduce costs associated with capital investment.
Following on from our initial success with microLEDs in late 2016, we have made further progress in two key areas: brightness and resolution. Success on both fronts increases the competitiveness of our technology for projectors and augmented reality, respectively.
Ultrahigh brightness
One of the significant market opportunities for the microLED micro-display is in various forms of projectors, including portable projectors and rear-projection televisions. For these applications, a high luminance of the micro-display panel is essential. Fulfilling this requirement with microLED micro-displays is challenging, with success hinging on various factors, including LED epi-quality, the particular device structure of microLED pixels, and the fabrication process.
Drawing on our extensive R&D experience in the semiconductor industry, we have undertaken a wideranging effort, considering modifications to the device structure, optimisation of the fabrication process and the selection of high-luminance LED epiwafers. The fruits of this labour include a reduction in the carrier leakage and the optical loss of microLEDs, and an optimisation of their light extraction efficiency. The devices that result are brighter and more efficient, and have enabled an increase in the brightness of green LEDs on our micro-displays "“ fabricated on the same driver backplane as those in the initial demonstration "“ to more than 106 nits. For the red, green and blue microLED arrays, external quantum efficiencies are 9 percent, 12 percent and 18 percent, respectively.
In parallel, we have scrutinized the spatial emission properties of our microLEDs, to see whether it is possible to improve brightness in projection applications. Many forms of LED have an inherently large divergent angle that pegs back the optical efficiency for projection systems.With many microLEDs, the root cause of this inefficiency is that a large proportion of light that's emitted from the device is outside the acceptance angle of the projection system, so it is wasted. However, with our novel technology, we overcome these issues. That's because our technology does not have a growth substrate covering the microLED arrays. Instead, micro-optic arrays are added on top of the microLED arrays, to reduce the divergence of the emitted light and enhance light projection efficiency.
Figure 5. Micro-optics integrated on an active matrix microLED micro-display panel and the measured angular distribution of emission with/ without microoptics.
Using this approach, we have fabricated microdisplays that feature both micro-reflector and microlens arrays. These modifications deliver a six-fold increase in brightness in the normal direction, propelling brightness in the green to in excess of 3à—106 nits (see Figure 5).
"¦ and resolutions
An even larger market for micro-displays "“ and possibly the biggest of all for this technology "“ is that of augmented reality. For this application, the requirements for high levels of brightness and contrast, which are needed for outdoor operation under a strong ambient light background, are joined by the need for high resolution. The latter is crucial, because it allows a micro-display panel to achieve a large field of view without compromising the image quality and system compactness.
Figure 6. Wafer-level test of active matrix microLED micro-displays with a resolution that is higher than 5,000 pixels per inch.
Our technology is well-suited to meeting these requirements. To showcase its potential for augmented reality, we have produced micro-displays with more than 5,000 pixels per inch (see Figure 6).
We believe that this feat "“ employing microLEDs with a diameter of just 2 μm, separated by a pixel pitch of 5 μm "“ sets a new benchmark for high-resolution active matrix microLED micro-displays.
Even higher resolutions should be possible. We believe that the pixel density can exceed 10,000 per inch, through refinements in device design and the fabrication process. When combined with luminance level well above 105 nits, this could result in ultra-high resolution active matrix microLED micro-displays that are the most desirable, promising solution for augmented reality.
To make this happen, we will now focus on converting our micro-display prototypes into products, and bringing them to market. While we work on this, we will respond to market demand by continuously pushing the limits of micro-display technology, and dedicating ourselves to the perfection of highperformance microLED micro-displays.