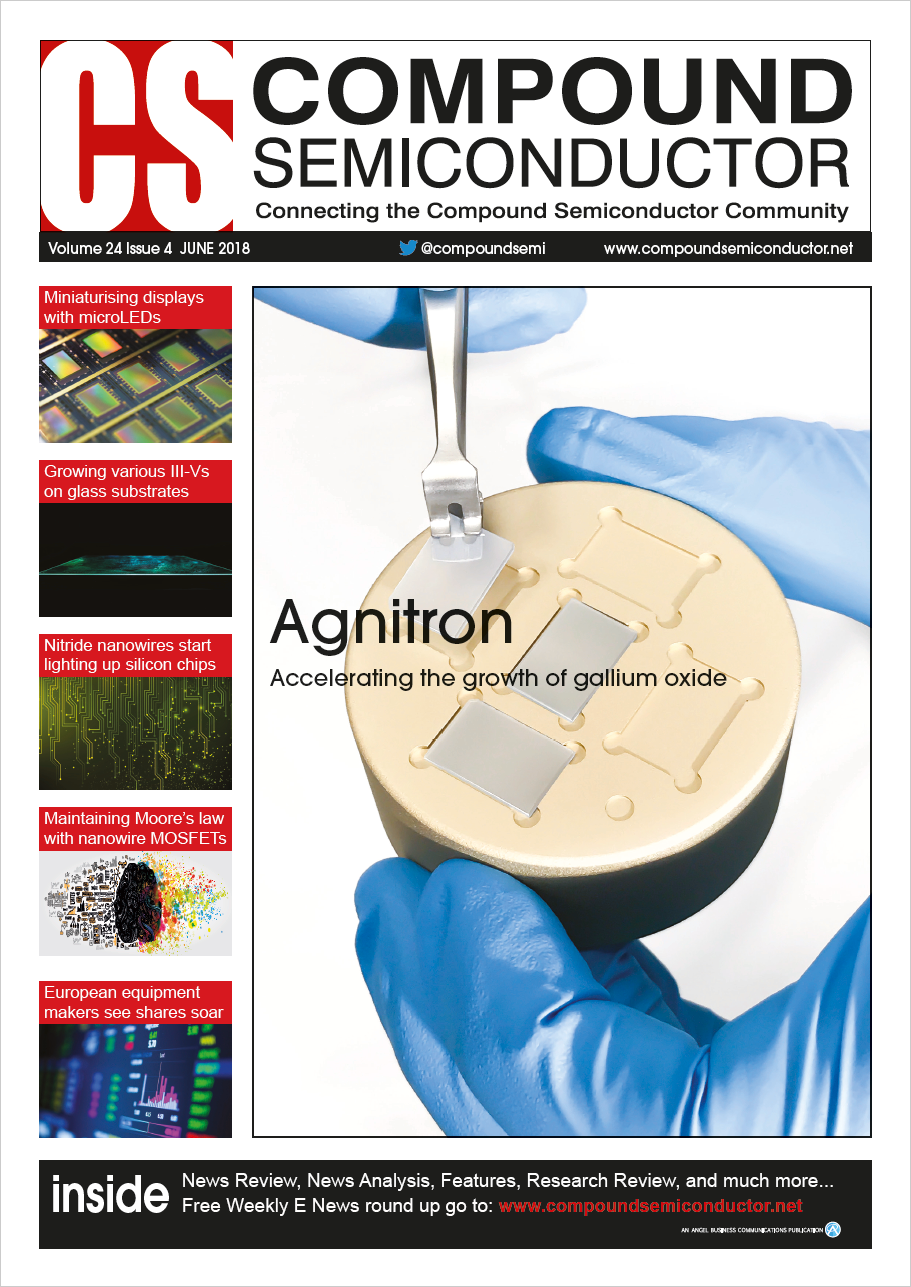
CS High-Volume Manufacturing Award
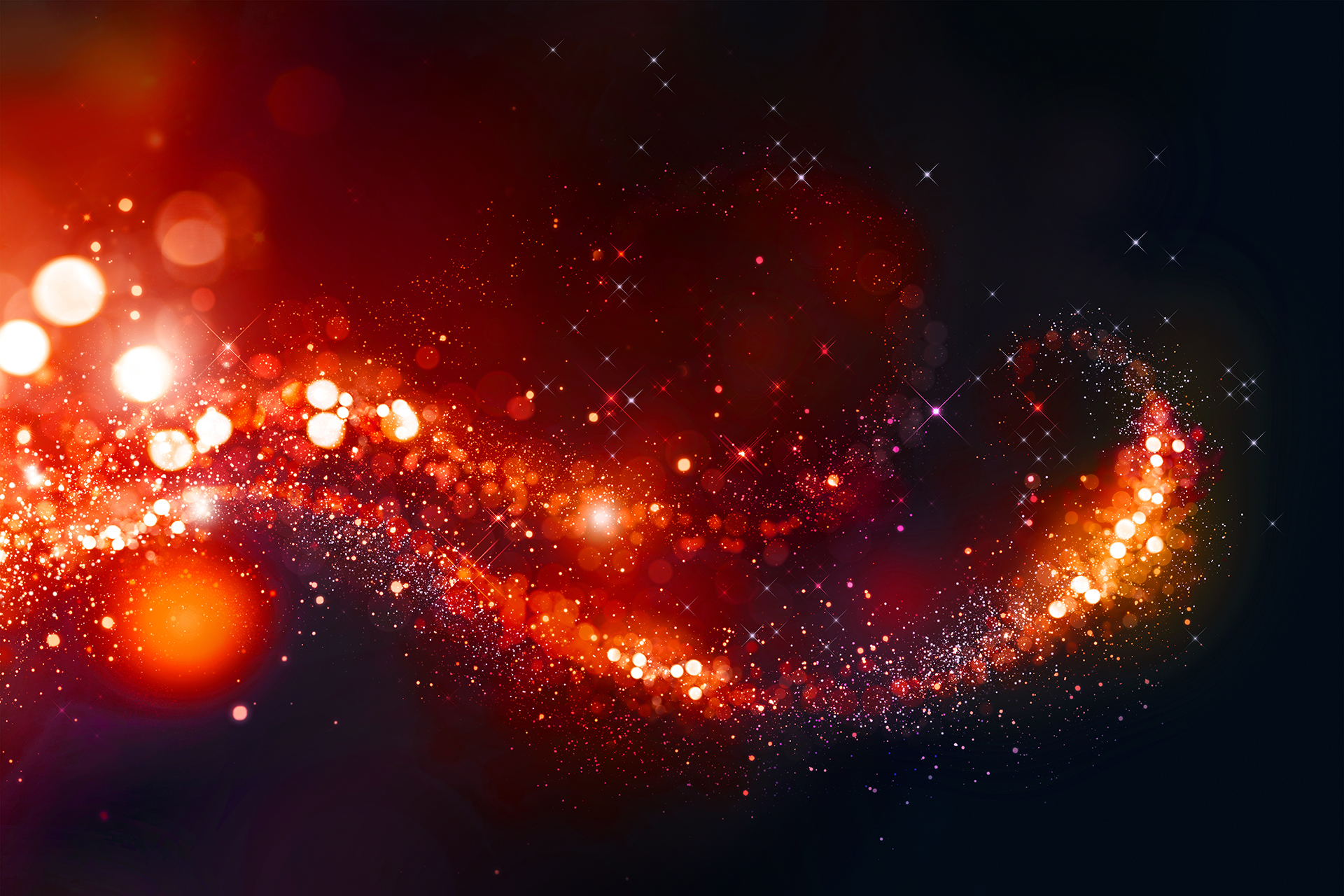
The CS High-Volume Manufacturing Award received by Beneq recognises success in high-volume manufacture, including the tools delivering high throughput with high yields and milestones in product manufacture
Winner: Beneq Oy
Beneq C2: ALD solution for automated batch wafer equipment for high volume manufacturing
BENEQ C2 is a brand-new Atomic Layer Deposition (ALD) solution for automated batch wafer equipment for high volume manufacturing. It offers a combination of high capacity batch ALD processing and standard cassette-to-cassette automation.
Beneq C2 provides a solution for high performance ALD on wafers in industrial applications, such as optical coatings, insulators and barriers, and highvolume manufacturing of wafer coatings in the semiconductor and MEMS industry. The new product has been designed with special focus on power and RF devices, RF and Piezoelectric MEMS, MEMS sensors and actuators, image sensors, LED and OLED. The thermal batch ALD process of Beneq C2 is ideal for oxide and nitride processes used for dielectric, conductor, barrier and passivation purposes.
The new automated cluster solutions have been designed for industrial ALD applications where high capacity is needed. The number of wafers that can be processes with the new tool is massive compared to traditional ALD equipment. It brings both the speed and operation costs of ALD to a completely new level that makes full-blown wafer ALD production possible. Beneq's high-capacity ALD solutions have enabled completely new innovative products and coatings that have not been possible in industrial scale before. The Beneq C2 ALD equipment has taken deposition speed, capacity and throughput of ALD equipment to a completely new level.
When we talk about ALD throughput in industrial wafer manufacturing, we must consider many different factors of the production setup. There is of course the deposition rate of the actual ALD process in the chamber (in nm/min), but you should also consider the capacity of the chamber (the batch size) and the automation solutions around the ALD equipment. Things like heating the wafers to the process temperature and the cooling time after the processing matter a lot when we count the total throughput. When the target is a thin (for example 10-nanometres) ALD film on a large number of wafers, the wafer handling, heating, cooling, etc. takes much more time than the actual ALD deposition. To increase throughput, one then must optimize all the auxiliary equipment around the ALD tool.
Let's compare for example the effect of pre-heating wafers in a traditional ALD tool that uses batch heating in the reaction chamber to the advanced pre-heating system that we use on the Beneq C2 ALD equipment: A typical case of a temperature sensitive ALD process, such as TiO2, in batch heating in the ALD tool itself: 25 wafers, loading at room temperature, heated in the ALD reaction chamber "“ pre-heating time 120 min to reach uniform temperature.
Single wafer heating of Beneq C2: same 25 wafers, pre-heated wafer-by-wafer, 10 s/wafer, total pre-heating time 25 times 10 s = 250 s = 4 minutes and 10 seconds. This combined with the speed of the actual ALD process results in a unique combination of high capacity batch processing and standard cassette-tocassette automation. Beneq C2 can process up to 20000 semiconductor wafers per month (10 nm of Al2O3 ALD coating on 200 mm wafers).