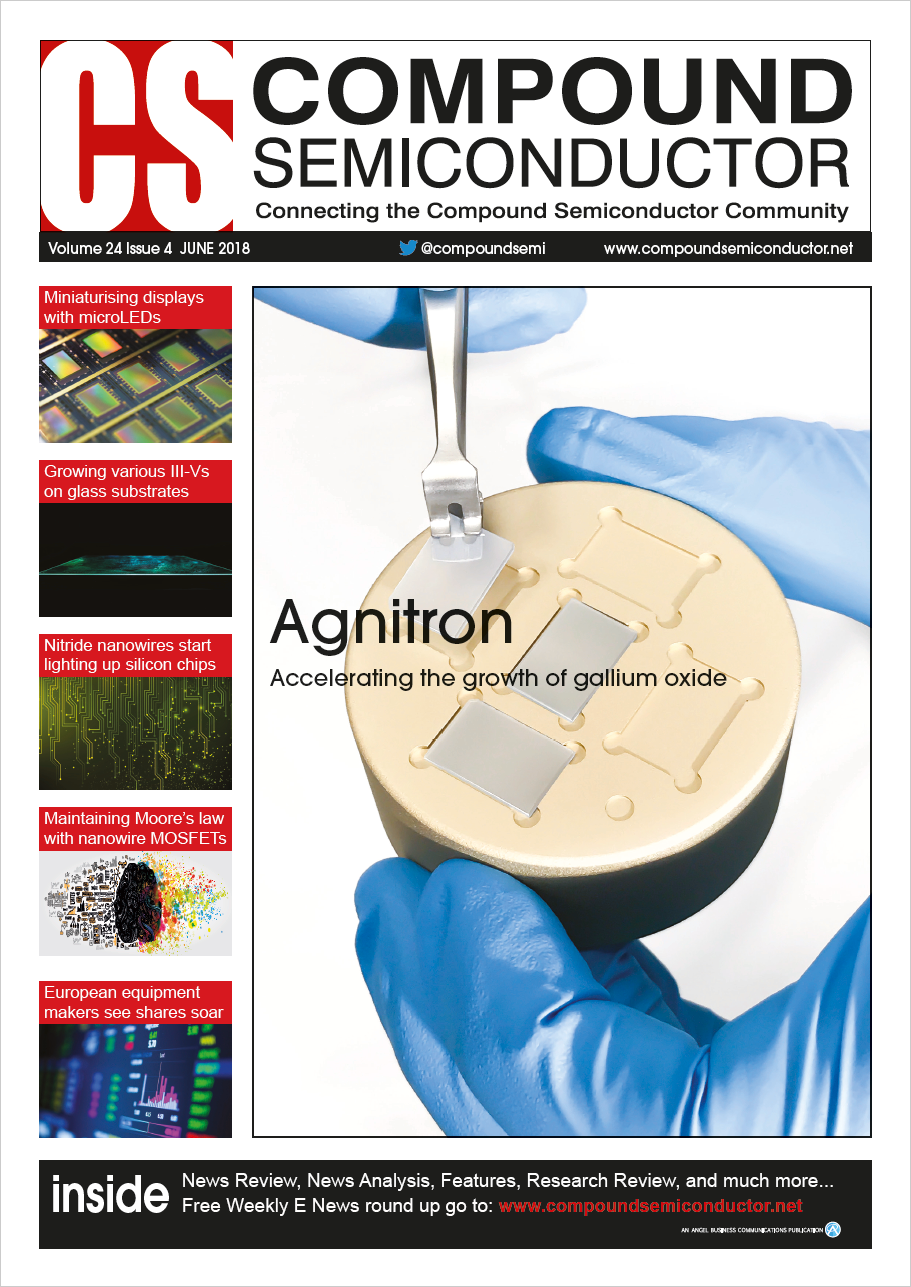
Constructing interconnects with nitride nanowire arrays
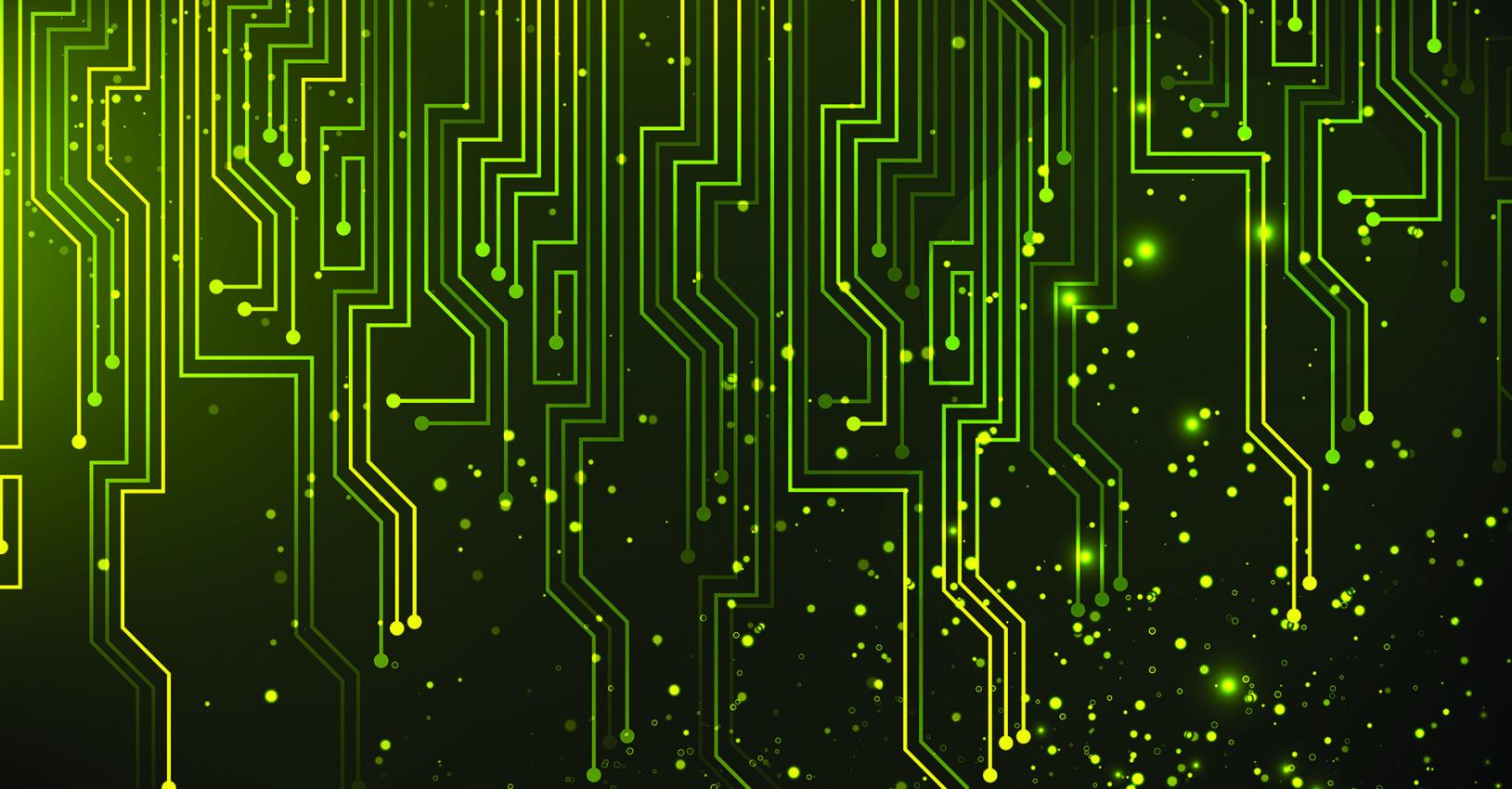
Throughout the twentieth century, engineers improved the performance of the silicon IC by simply reducing the size of the transistors. But in recent times, progress has been far harder to come by. It has hinged on the introduction of exotic materials and architectures to ensure that the miniaturisation of the transistor does not produce dire consequences "“ and it will not be long before there is a need to add light-based communication, to enable faster transfer of information within and between CMOS chips.
The latter technology, often referred to as silicon photonics, has much promise, because light travels far faster than electrons (see Figure 1 for an example of a simple photonic circuit). Due to this hike in speed, circuits that incorporate photonics can operate at far higher communication rates than their electronic cousins, shortening on-chip and off-chip delays.
Fulfilling the promise of the optically equipped IC is not easy, however. Silicon will undoubtedly remain the material for the electronics, but its indirect bandgap hampers its use in the components needed for optical communication. While impressive progress has been made in research and commercial development of silicon-based detectors, modulators and passive waveguides, III-Vs are the essential ingredient for making a light source.
The current solution is to bond either GaAs-based or InP-based lasers to the silicon wafer. That's not ideal, though, because it creates thermal issues: the silicon gets hot, pegging back laser output and efficiency. A far better approach is the epitaxial growth and fabrication of a diode laser on silicon. Ideally, this source must emit at around 1.3 μm, the zerodispersion wavelength for the SiO2 waveguide. Note that another advantage of this spectral range is that it is in the regime of eye-safe operation.
Unfortunately, success with this approach is hampered on three fronts: there is a large lattice mismatch, giving rise to a high density of dislocations; there is a thermal expansion coefficient mismatch that can cause strain in the device; and there is the potential for unwanted antiphase domains, which can be created during the growth due to the polar/non-polar nature of the epitaxial layers and the substrate.
Despite all these drawbacks, encouraging progress has been made by using devices that sport suitable buffer layers. At the University of Michigan, we have led the way, demonstrating the first InAs/GaAs quantum dot laser that is grown directly on silicon. And other groups are now following in our footsteps, improving the performance of this device on (001) silicon substrates.
However, progress is slow, and problems remain. The silicon that's used as a foundation for the lasers is offcut at 4° towards the (011) direction in order to avoid anti-phase domains and resulting defects.
Meanwhile, CMOS circuits are formed on (001), a situation that's not going to change. In addition, fabrication of the lasers involves the growth of complicated buffers and intermediate layers, making the whole process cumbersome.
Switching to nitrides
Our view is that instead of trying to address all of these problems, it is far better to switch to another material system. We chose the nitrides, because they combine tremendous tunability of the bandgap with growth on a variety of substrates, such as sapphire, SiC and silicon "“ including the form that's used for CMOS circuits.
Figure 1. The simplest example of a photonic integrated circuit on a silicon platform. At the University of Michigan, diode lasers and photodiodes are fabricated with III-nitride heterostructure disk-in-nanowire arrays grown directly on silicon by MBE. The waveguide is formed by dielectric deposition.
One distinguishing feature of GaN and its related alloys is its large, intrinsic polarisation. The fields that result aid the design of HEMTs, but are a drawback to LEDs, hampering radiative recombination efficiency and limiting the thickness of the quantum well. A further complication is that increasing the indium content of an InGaN well to propel its emission from the blue to the green creates compositional inhomogeneities. This makes it very challenging to produce light sources with acceptable efficiency beyond the blue. And magnifying this issue is the high density of defects, arising from the substantial lattice mismatch with the substrate.
To sidestep these issues, we are avoiding planar III-nitride semiconductors, and instead working with nanowires. Arrays of these nanowires can be grown directly, without masks or catalysts, on various substrates including CMOS-compatible (001) silicon. The density of the nanowires in these selforganized random arrays may range from 108 cm-2 to 1011 cm-2, and their diameter can be between 20 nm and 80 nm (see Figure 2).
Figure 2. (a) Scanning electron microscopy and high-resolution transmission electron microscopy images of a disk-in-nanowire array on silicon; (b) an illustration of a disk-in-nanowire edge-emitting diode laser; (c) output emission characteristics of a green-emitting laser below and above threshold injection.
Issues related to high polarisation fields are greatly diminished in these wires, thanks to radial relaxation of strain during epitaxial growth. The nanowires also suppress extended defects, thanks to the larger surface-to-volume ratio; and emission can span a far wider spectral range through the insertion of lower bandgap disks, such as those made from InGaN, into larger bandgap GaN or AlGaN nanowires. Note that emission from the structure may be tuned by tweaking the composition of single or multiple disks.
Another benefit of the nanowires, which we realised soon after embarking on this effort, is that the indium incorporation in the InGaN disks can be far higher than it is in planar quantum wells, without any adverse effects. And we can realise quantum efficiencies of more than 50 percent.
We have used these disk-in-nanowire arrays to produce green- and red-emitting LEDs "“ and more importantly, diode lasers for the first time. Note that our edge-emitting nanowire array lasers (see Figure 2) appear exactly like planar devices after fabrication on the (001) silicon substrate. To realise emission in the green and red, the InGaN disks that form the active (gain) media within the GaN waveguide and AlGaN cladding have an indium content of 34 percent for 534 nm emission, and 51 percent for 630 nm emission.
Hallmarks of these emitters include the absence of reflections, scattering and distributed feedback, due to the wavelength associated with the emission being far larger than the diameter of the nanowire (the polymer parylene surrounds the wires, creating a structure that behaves as a composite medium with a refractive index of 2.1). Characteristics associated with photonic crystals are also avoided, due to the randomness of the array.
Typical output powers for these lasers are 10 - 15 mW. The threshold current densities are fairly insensitive to temperature variations (To >200K), and have a typical value of about 1 kA cm-2. Electrical modulation indicates that the modulation bandwidths reach 3 GHz without implementing any special designs to the nanowire heterostructures.
Realising the near-infrared
To propel the emission of our lasers from the visible to the near-infrared we have had to crank up the indium content in the InGaN disks. Following careful optimization of the MBE parameters, metal fluxes and growth temperature, we have incorporated multiple In0.85Ga0.15N disks in our GaN nanowires. Encouragingly, these structures produced strong, room-temperature photoluminescence at the desired wavelengths. We are thankful for the assistance of Millunchick's research group at the University of Michigan "“ they offered an insight into the quality of our nanowires, by undertaking detailed imaging with a transmission electron microscope.
We have fabricated lasers from these heterostructure nanowire wafers at our university's Lurie Nanofabrication Facility. Production of the devices involved a series of steps that included photolithography, etching, metal deposition, planarization and the addition of the polymer parylene. Fabrication is not easy, because rough laser facets that result from dicing the nanowire array/parylene composite reduce reflectivity to such an extent that it prevents the necessary cavity feedback. To overcome this, we smooth the facets with focused ion beam etching. A further enhancement to facet reflectivity comes from the addition of multiple periods of ZnSe and MgF2, which together form a distributed Bragg reflector. This enables a hike in reflectivity to around 90 percent, and ultimately the fabrication of lasers with an emission peak of 1.2 μm and a room-temperature output of around 7 mW. These first-of-a-kind, nearinfrared, III-nitride-based diode lasers are transparent to silicon, thereby making it possible to realize low loss photonic circuits monolithically on silicon.
In these devices, there is a large polarisation field, revealed by the blueshift between the electroluminescence peak below threshold and the coherent lasing peak above threshold. Nonetheless, these fields are far smaller than those in planar quantum wells.
Other encouraging attributes of these lasers are: the absence of any significant material segregation in the active disks; a low threshold current; a high degree of temperature stability of the threshold current (T0 >200K); a high differential gain; and good modal characteristics.
In our quest to realise a laser emitting at 1.3 μm "“ the sweet spot for silicon photonics "“ our only remaining option to red-shift the emission was to attempt to incorporate binary InN disks in the GaN nanowires. This is a far better approach than forming thicker InN regions along wires, because the disks provide quantum confinement, and tend to have a lower dislocation density.
Epitaxial growth of InN disks is far from easy. It is critical to determine the optimum growth temperature, which was an unknown parameter. We were also hampered by the low sticking coefficient of indium. If we selected too high a substrate temperature, this would enhance indium desorption; and if we chose too low a value, the heterostructure would be plagued by poor crystalline quality and defects. Following some optimisation, we selected a substrate temperature of 489°C.
We were delighted to discover that our InN/GaN disk-in-nanowire arrays could produce strong photoluminescence and a high radiative efficiency. The latter is 67 percent, a value exceeding that for ternary InGaN disks of all alloy compositions, before or after passivation with parylene. Photoluminescence intensity peaks at 1.6 μm, an extremely encouraging result.
Figure 3. A 1.3 μm disk-in-nanowire array diode laser on (001) silicon. (a) a nanowire heterostructure with InN disks; (b) output light-current characteristics; (c) mode propagation and confinement calculated by the finite-difference timedomain technique.
To improve the performance of our edge-emitters, we adjusted the design, introducing a waveguide with a graded refractive index that has various compositions of InGaN. The device that resulted, which has multiple 6 nm-thick InN disks incorporated in the middle of the waveguide region, produces very promising output powers, good modal characteristics, extreme temperature stability (T0 ~220K) and a large differential gain, all at room temperature (see Figure 3 for details of the output light-current characteristics). With the emission peak at about 1.3 μm, our device is a promising candidate for silicon photonics.
Collaborators have simulated the performance of our lasers. Using the finite-difference time-domain method, Junseok Heo at Ajou University, South Korea, has studied the characteristics of the propagating mode (see Figure 3). Meanwhile, John Dallesasse and his group at the University of Illinois, Urbana-Champaign have calculated the strain distribution and bandstructure in the disks. Both studies have helped us to increase our understanding of the electronic and structural properties of the InN disks and the characteristics of the lasers made with them.
Figure 4. (a) Scanning electron microscopy image of a fabricated nanowire photonic integrated circuit on (001) silicon; (b) photocurrent response of integrated photodiode; response of photodiode to increasing injection current applied to the laser. The peaks and shoulders in the responsivity spectra result from interband transitions in the InN disks and other regions of the nanowire heterostructure.
To determine the usefulness of our lasers in communication-based applications, we have undertaken high-speed measurements on these devices. Using small-signal modulation measurements, we have found that our lasers can be modulated at frequencies of up to 3 GHz. This is by no means the limit of their capability: refinements to the design will increase this bandwidth.
Producing photodiodes
Another key component in even the simplest conceivable communication link is the photodetector. Success with our lasers has motivated us to investigate near-infrared guided wave photodiodes fabricated with the same nanowire array. This effort draws heavily on our previous work, because the only difference between the fabrication of our lasers and our photodiodes is that the reflective mirrors on the laser facets are replaced by anti-reflective dielectric coatings, made from SiO2.
Our photodiodes, which are typically 50 μm-wide and 1 mm-long, have been characterized under reverse bias. Dark currents are a few tens of nanoamperes. Meanwhile, responsivity is 0.1 A/W at 1.3 μm, according to measurements that use spectrally filtered light from a broadband source, directed through a monochromator and collected by a fibre that is focused on a facet of a photodiode (see Figure 4).
Following the fabrication of these devices, we have realized and tested an entire photonic integrated circuit consisting of a laser, photodiode and a waveguide. For the latter component, we have turned to an InN/InGaN/GaN heterostructure disk-in-nanowire arrays, identical to the one used for the fabrication of the 1.3 μm laser and photodiode (see Figure 3). Again, growth was by MBE, on a (001) silicon substrate.