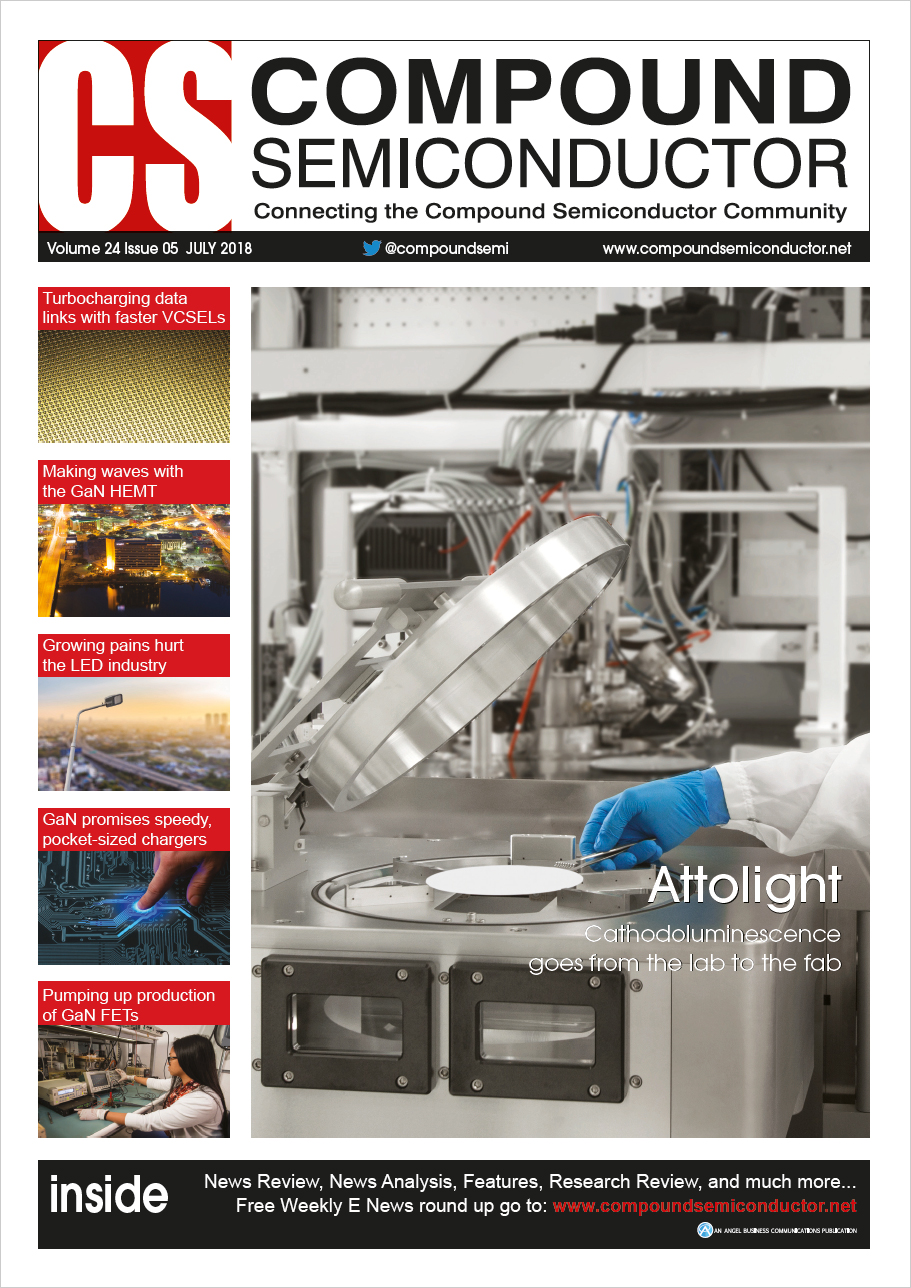
Making waves with the GaN HEMT
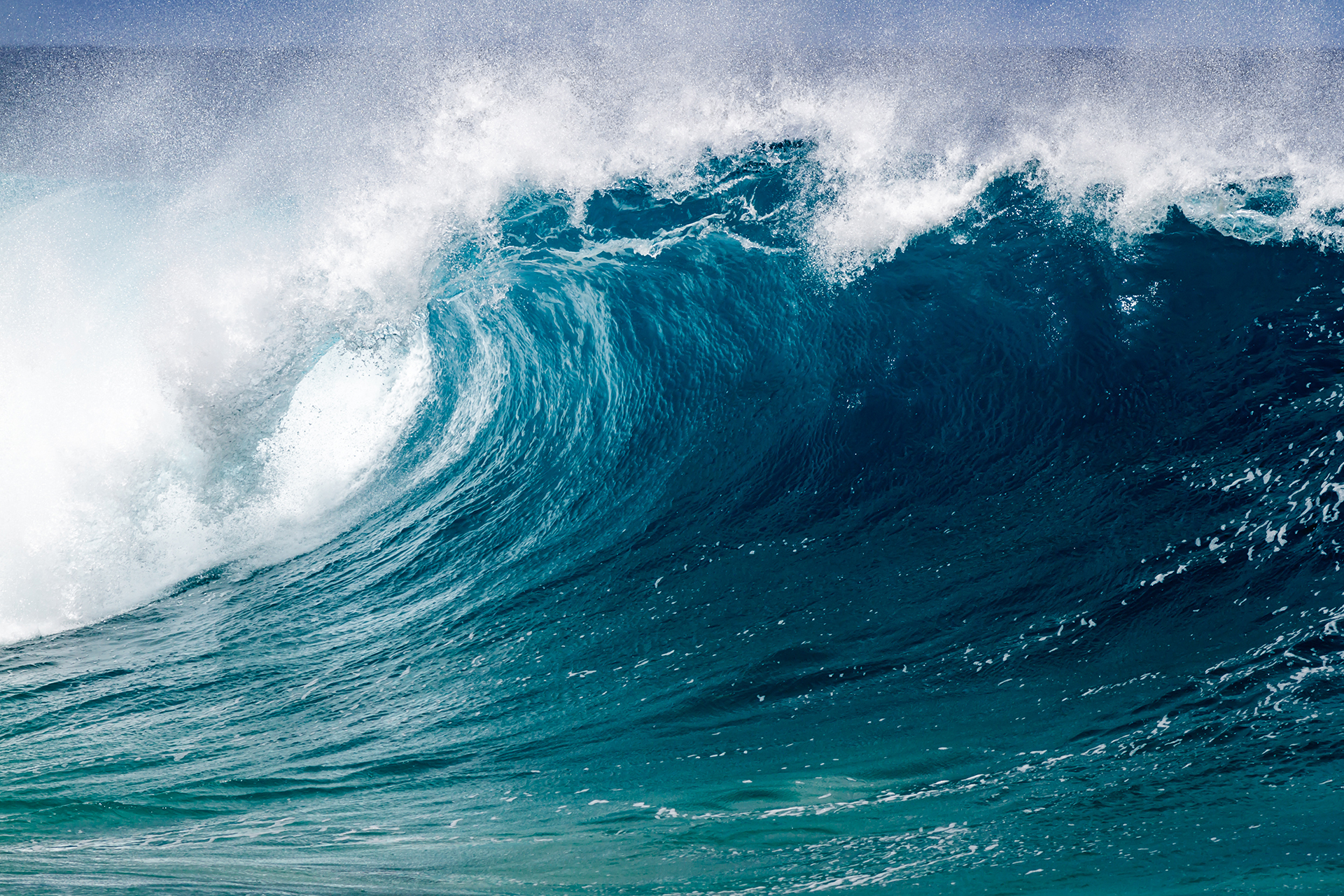
If you spend all of your time looking forward it's easy to lose sight of how far you've come.
That's a trap that many of us can fall into when we are considering the variant of the GaN HEMT that operates in the RF domain. Often, the future is the focus "“ sales are tipped to rocket to more than a billion dollar per year by the start of the 2020s.
Take that perspective and it's easy to forget the progress that has been made to date. It is now more than a decade since the launch of the first GaN HEMT operating in the RF, and over that timeframe devices have been deployed in many different applications. And now, revenues are significant. According to market analyst Yole Développement, GaN RF device sales to the military will net $201 million this year, while those for base stations and satellite communications will accrue $150 million and $29 million, respectively.
A snapshot of how far the GaN RF industry has come, and the challenges that lie ahead, was provided at this year's CS Mantech, held at the Hyatt Regency in Austin, TX, from 7-10 May. That meeting featured a session on RF devices that included presentations detailing: the creation of E-mode and D-mode HEMTs, via variations in the form of stress in the device; the development of an efficient 15 W/mm GaN technology for serving pulsed radar in the C-band; improvements to a 0.25 μm process for radar and 5G applications; and opportunities to refine the mass production of high-reliability GaN HEMTs for wireless communication.
The benefits of stress
One of the biggest weaknesses with GaN technology is the lack of truly normally-off enhancement mode and depletion mode integrated devices. Due to the chemical inertness of GaN and its alloys, etching is not easy, and it often leads to an increase in the gate leakage in enhancement-mode devices. An alternative, fluorine implantation, also introduces damage to the semiconductor material, thereby impairing reliability.
A very promising solution, described by Konstantin Osipov from Ampleon, involves the addition of a SiN passivation layer. This applies stress to the AlGaN barrier "“ which is under tensile strain due to lattice mismatch "“ and it ultimately controls the density of the two-dimensional electron gas under the gate region (see Figure 1). Armed with this lever, the team can realise either partial or complete depletion of the transistor channel, and thus fabricate enhancement and depletion mode devices on the same wafer.
According to Osipov, introducing the SiN layer also produces a reduction in the gate leakage current and the elastic energy stored in AlGaN at the drain side of the gate. "So theoretically, [our technology] should lead to significant reliability improvement."
Development of the technology can be traced back to efforts by Osipov to reduce the gate leakage current with SiN layers with different compositions. This trial revealed that differences in SiN composition led to variations in the threshold voltage.
"I've tried to understand the physical reason behind this phenomenon," explains Osipov. "The only reasonable explanation that I've found is internal compression in the silicon nitride layer that is transferred to AlGaN."
After confirming this assumption with simulations, Osipov went on to create a simulator virtual enhancement-mode device that featured highly compressive SiN. After this, he developed an experimental process for making integrated enhancement-mode and depletion-mode devices.?
Figure 1. Adjusting the strain in SiN can lead to depletion in the channel of the GaN HEMT, and a shift in the threshold voltage by more than 1 V.
Note that the use of external stressors is actually a tried and tested technology. "In silicon technology, external stressors are used for electron and hole mobility enhancement, despite the fact that silicon is not even a piezoelectric material," says Osipov.
Fabrication of the team's devices began by loading 4-inch, n-type SiC substrates into an MOCVD reactor and growing an iron-doped buffer layer, an unintentionally doped GaN channel, and a 10 nmthick Al0.26Ga0.74N channel. After adding a Ti/Al metal stack to form ohmic contacts, a 300 nm-thick SiN passivation layer was grown across the whole wafer (see Figure 2(a)).
The next steps involved: using photolithography and etching to open windows in the passivation layer where enhanced-mode HEMTs would be formed; depositing a compressive SiN layer over the whole wafer, before using photolithography and etching to remove this at locations where depletion-mode devices would be added; and then using a sputtering process to compete fabrication of 100 nm gates.
Measurements of DC characteristics revealed that there is a threshold difference of more than 1 V between the enhancement mode and depletion mode devices. For the enhancement mode HEMTs, DC performance is claimed to break new ground, in terms of on-resistance, peak transconductance and gate leakage.
The researchers attribute this success to their technology. One of its merits is that it produces a "˜virtual' gate recess effect, while maintaining the thickness of the AlGaN barrier. Another virtue is that the sputtered iridium process, developed at FBH, avoids damage to the semiconductor surface during fabrication. Thanks to this, the devices exhibit ideal normally-off behaviour and avoid any trade-off between AlGaN thickness and threshold voltage "“ that can lead to low parasitic input and output resistances.
Figure 2. The team from Ampleon and FBH Berlin have produced E-mode and D-mode HEMTs side by side with a process that includes the deposition of tensile and compressive layers of SiN.
One weakness of the enhancement-mode devices is that they can be compromised by back etching of the tensile SiN layer. However, this issue can be avoided.
"Technically it's not a problem to leave a few tens of nanometres of tensile silicon nitride and cover it with a compressive film," says Osipov. "In this case, compression from the thicker layer will easily overcome the tensile stress of silicon nitride underneath, and the overall stack stress will be compressive."
The team have made some RF measurements. "The damage from tensile silicon nitride removal negatively influenced RF performance of E-mode transistors," admits Osipov. However, the cut-off frequency for these devices is still higher than that for depletionmode variants.
Figure 3. Scanning electron microscopy images of Integra Technologies' 0.25 μm GaN die design that has a breakdown voltage of more than 250 V.
Empowering pulsed radar
For radar systems used for weather, air traffic and the military, the most desirable attributes for an amplifier are a high output power and a high efficiency. While those made from GaN HEMTs are already delivering a performance that is good enough to serve in many of these applications, there is demand for an even higher efficiency "“ this could trim the size, weight and power dissipation of the electronics, and lead to smaller, lighter and more efficient systems.
The key figure of merit for the HEMT is its power density, which is the product of its current density and the bias voltage. For AlGaN/GaN HEMTs, for typical bias voltages of 28 V to 50 V, the current density tends to peak at around 1 mA/mm. This can be doubled by switching to more novel material combinations, such as InAlN/GaN, InAlGaN/GaN and N-polar GaN. However, due to the conservative nature of the radar industry, it can take more than ten years to transform a laboratory technology into an approved product. Given that hurdle, there is much to recommend to any approach that offers a shorter path to technology maturity.
At Integra Technologies of El Segundo, California, they are adhering to that view, and using voltages of up to 100 V to increase the power density.
At CS Mantech, company spokesperson Gabriele Formicone provided an update of the company's latest progress. He argued that two of the most important breakthroughs have been the higher power densities and the higher impedance, aiding broadband matching. However, the pinnacle of the team's success, according to him, is the realisation of a power density of 15 W/mm at C/X-band, using a production-ready GaN-on-SiC technology. "[This] is much more cost effective compared to alternative approaches, among which is GaN on diamond."
Migrating to higher voltages will not be an issue in the radar sector, which has traditionally used travelingwave tubes. "100 to 150 volts is still orders of magnitude safer than 10,000 volt traveling-wave tubes supplies," says Formicone. "Therefore, we do not see any downside in migrating from the nominal 28 volt to 50 volt power supply to 100 volts to 150 volts in high-performance radar, electronic warfare and industrial, scientific and medical applications."
The team's latest results were obtained with its 0.25 μm GaN-on-SiC HEMT process, which produces devices with a breakdown voltage in excess of 250 V. Chips are housed in a ceramic package, and performance evaluated at 7.9 GHz using 35 μs pulses and a 10 percent duty cycle "“ these operating conditions are claimed to be of interest in some radar remote sensing applications.
Using a 90 V bias, devices can deliver 150 W with 11 dB of power gain. Operating in this manner, drain efficiency is 50 percent, corresponding to a power-added efficiency of 46 percent. Crank up the voltage to 100 V and there is little improvement in output power, but drain efficiency still exceeds 40 percent.
Figure 4. Measurements were made on three of Integra Technologies' 9.6 mm GaN-on-SiC HEMTs, operated under 90V bias. Testing took place at 7.9 GHz, using a pulse width of 35 μs and a duty cycle of 10 percent.
The lack of improvement is explained by the 100 V device being a first iteration. "An improved design would show good performance at 100 volts too," argues Formicone. "Additionally, as voltage increases to 100 volts, load impedance tends towards 50 ohm, which requires a more careful test fixture/circuit design to properly match, given the narrow width of the transmission lines."
Integra will extend this technology to even higher voltages. Benefits will not be limited to a smaller, lower cost die for a given power level, but will extend to improved broad band matching.
The move to higher voltages should not prove too tricky, as Integra is not heading into uncharted territory "“ at lower frequencies, it has already produced parts that operate at 150 V and offer efficiencies of 80 percent. "At higher frequency it is always a bit harder," says Formicone, "but Integra has been pursuing this technology roadmap for a few years already with very interesting results."
Integra's AlGaN/GaN X-band FET.
Refining the process
At WIN Semiconductor, efforts have been underway to improve the performance of GaN-on-SiC MMICs fabricated on a dedicated 100 mm line. These devices are targeting radar and 5G applications.Refinements to the company's 0.25 μm process, described to delegates at CS Mantech by Yi-Wei Lien, have increased small signal gain by 1.8 dB to 20.3 dB and driven up the power-added efficiency at 10 GHz from 59.6 percent to 64.7 percent.
Higher levels of performance are claimed to result from a combination of a superior epitaxial process and optimisation of the processing. Thanks to these advances, there are reductions in gate-lag and drainlag by 25 percent and 11.6 percent, respectively. That's a big deal, because it implies that there are fewer traps, and ultimately a reduction in the current collapse of the transistors.
GaN MMICs produced with the latest process are also free from a kink-effect that plagued the previous generation. The kinks, seen in DC measurements of the source-drain current as a function of drain-source voltage, are associated with hot electrons "“ they are trapped at a low drain-source voltage and de-trapped at a higher voltage.
Another improvement in WIN's technology has been the integration of the RF power amplifier with an RF switch, in the form of a symmetric transistor with a 0.25 μm gate located at the centre of the source-drain region. Testing, using a pulse width of 50 μs and a duty cycle of 10 percent, reveals a rise time of 36 ns and a fall time of 13 ns.
In addition to these impressive switching speeds, the switch is reliable. High-temperature reversebias testing at -50 V and 150 °C reveals that during 1000 hours of operation, the switch's on-resistance, threshold voltage, and the saturation drain current vary by less than 12 percent.
High-volume manufacturing
From the perspective of Sumitomo Electric Device Innovations, the GaN HEMT is now, without doubt, a device in mass production. At CS Mantech, company spokesman Fumikazu Yamaki emphasised this point by reporting developments in robustness and packaging.
To ensure that a product can offer many years of service, it needs to combine high reliability with a high degree of ruggedness "“ a capability to cope with operating conditions beyond those that were intended. Yamaki and co-workers have devoted much effort to realising this, evaluating progress in terms of increases in the safe operating area. For a GaN HEMT with an intended drain-source voltage of 50 V at 2.1 GHz, the peak drain voltage during operation can hit 160 V, but the breakdown is still far higher: it is 220 V. Thanks to this margin, it is argued that the device has sufficient ruggedness for mismatched and unexpected load impedances.
Reliability of the company's HEMTs is also very high, with DC high-temperature operating life tests revealing a mean-time-to-failure of 23 million hours at a channel temperature of 200 °C. Note that in base stations, high power amplifiers may have channel temperature this high.
One recent development at Sumitomo is the housing of devices in plastic packages, which are needed to meet the cost and size requirements associated with 5G. In these packages it is essential to include die level humidity protection. An improved surface passivation film can provide this, according to Sumitomo's 200 hour tests at 130 °C using relative humidity of 85 percent.
These efforts at Sumitomo underline the progress that has been made with the GaN HEMT. It is a fully fledged commercial device, and with further progress being made by not only this Japanese outfit "“ but also the likes of Integra, Ampleon and WIN "“ there is good reason to believe the positive forecasts of the market analysts.