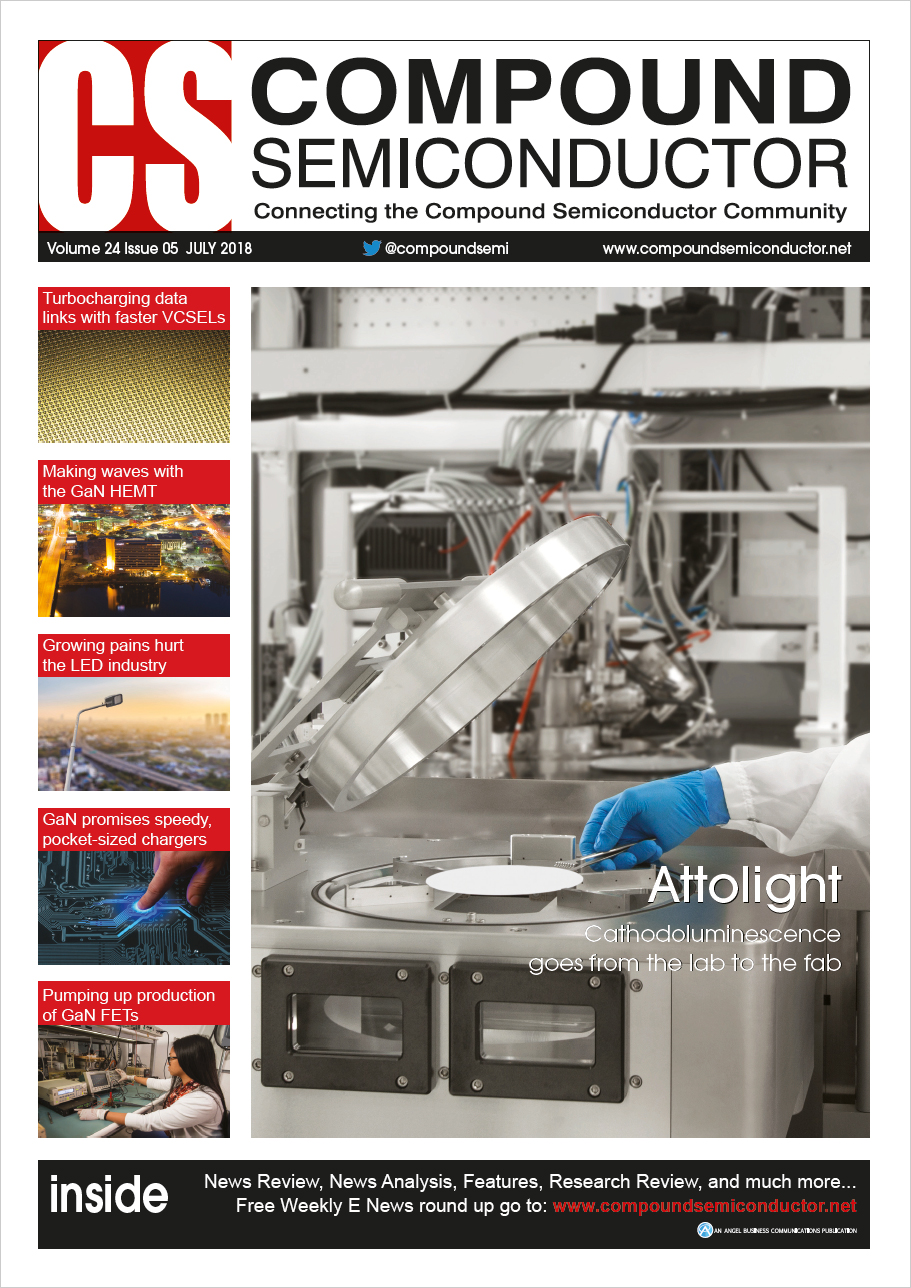
Meeting the need for the specialised testing of SiC devices
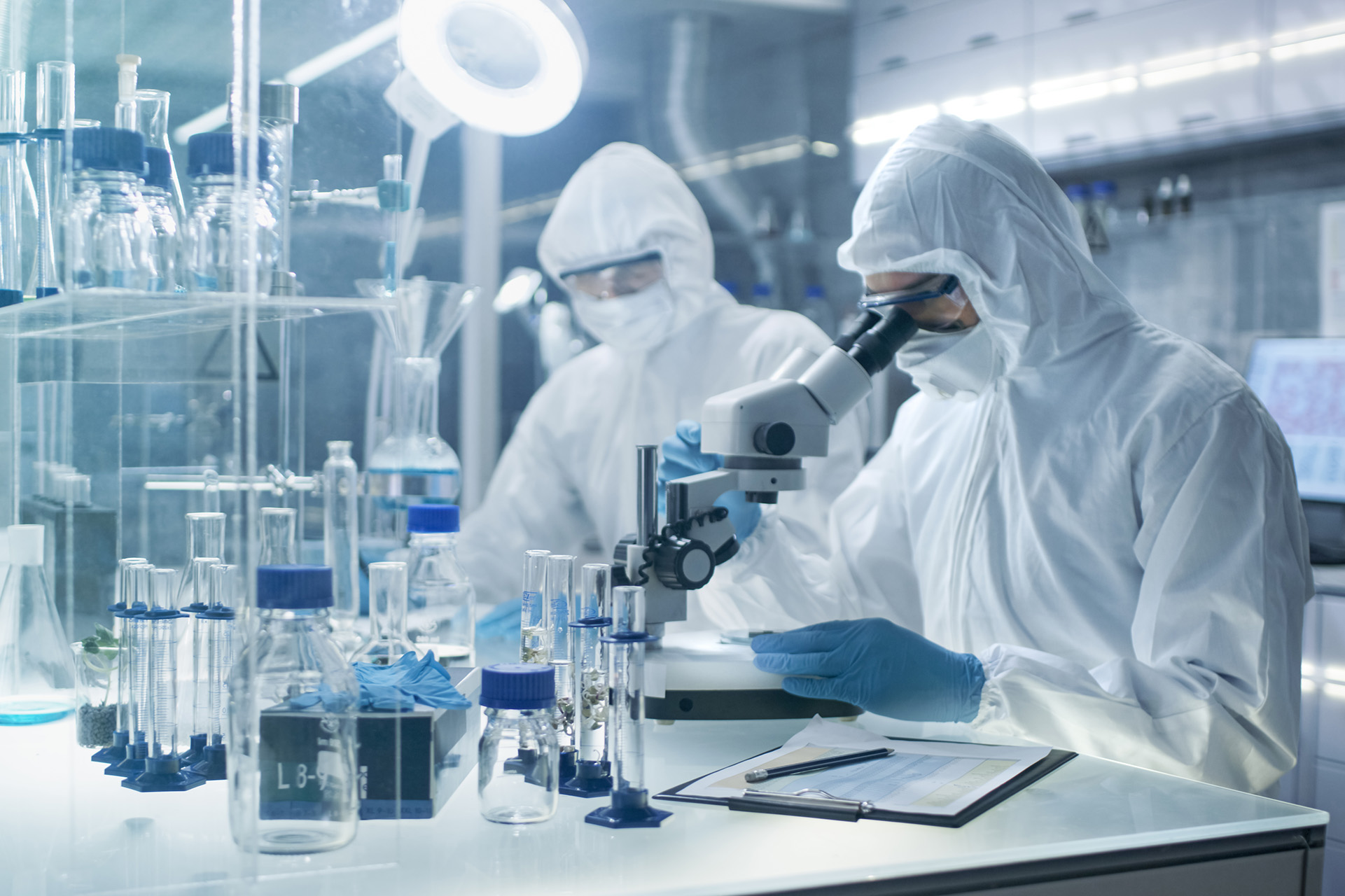
Power Semiconductors are cropping up everywhere. They are being deployed in electric vehicles, charging station infrastructure, solar and wind power plants, and industrial machinery.
One of the key requirements for every power device is that it complies with energy efficiency requirements. To ensure that this is the case, the devices "“ either forms of diodes, transistors or thyristors "“ are tested and validated at an early stage of development. This testing is evolving, due to the introduction of everhigher switching rates and operating voltages.
The cnages in the switching rates and operating voltages are playing into the hands of SiC devices, which have the upper hand over silicon incumbents. But the faster switching speed has a challenging consequence: a need for specialised testing. To meet this requirement, dedicated test setups are needed to deliver the precise results that are desperately wanted by those that will design products with these devices.
At Rohm Semiconductor, a market leader in SiC technology, we are striving to provide our customers with the best possible support. To that end, earlier this year we opened a 300 m2 "˜Power Lab' for the analysis of power devices and systems. This facility is located in Germany, at our European Headquarters in Willich-Muenchheide, which is just outside Duesseldorf.
The primary purpose of our lab is to help our customers realise the benefits of power devices, and to go on and make great products that generate great sales. Our lab can be used to test devices, or systems such as inverters, which may be formed from SiC devices, or a mix of SiC and silicon. One option for our customers is to tell us what testing they require, and trust our engineers to make these measurements "“ alternatively, they can visit our lab, and use our specialised equipment to carry out the tests themselves.
We know that the engineers that purchase our power devices, or consider doing so, face many challenges. These engineers are under pressure to comply with the current trend of making products that combine higher efficiency with higher power density and higher reliability. Succeeding in this endeavour is not easy, because it brings its own challenges, such as thermal management. Making the engineer's task even harder, system requirements are getting ever more complex, while the time to complete the project is limited, and it must be accomplished within its financial constraints.
Given this scenario, it's hardly surprising that many of today's system engineers are choosing the easiest way to design their circuits. Going into their products are tried-and-tested reference designs, likely to be dominated by silicon chips.
Figure 1. ROHM Semiconductor's new "Power Lab" aims to provide customers with the best technical support at an application level when using wide bandgap power devices.
To help these engineers make the switch to SiC devices, they need data for these wide bandgap power devices that demonstrates how to use them in applications in the best possible way. Ideally, this data will aid the building of products that are reliable, low in cost, and easy to use.
Makers of SiC power devices, including ourselves, must do more to help every engineer that is considering to use these chips. It is not enough to simply provide a datasheet for each device and system requirements for each power board. Why? Because, for example, the operating points of the final application are not always covered in the datasheets.
Simply adding a few more numbers to the datasheet is not going to address this issue. The reality is that power semiconductors serve in many different application fields, where they operate in many different manners. Depending on the application, there can be different loads, such as DC motors, AC motors and batteries; and there can be different power sources, such as batteries and the grid. The products that are built with these diodes and transistors could be deployed all over the world, so they need to operate over a range of temperatures and humidity levels "“ and if they are powered by the grid, they need to be compatible with the local power supply.
What the engineers that are building products with power electronics need is technical support. And that is what we can now give them, by making the specific measurements that they need in our new Power Lab. Here, we can test discrete devices under a range of conditions, and also power systems, which may contain a mixture of silicon and SiC components.
The Power Lab project began with a detailed, structured-use case analysis. Throughout the whole project, it was crucial to never lose focus of either the target application or the customers. While making these the priorities, time is taken into account, along with internal and local safety standards.
All these projects benefit from drawing on the great experience of our team, which has many years of experience in power electronic applications and the testing of power devices. The project's success also results from modern measurement techniques and equipment.
Figure 2. The power test bench feeds energy back into the grid to minimize the energy consumption.
Creating the Power Lab
When we started to plan for the build of our power lab, we had to evaluate the relative importance of many factors. We decided that when we were putting together test benches with state-of-the-art and advanced technologies, emphasis had to be on safety and the quality of the equipment. We also placed a premium on flexibility of usage.
We decided to deploy a flexible, modular design for our test set-ups, because this enables us to provide fast, high-quality support to our customers. What's more, this gave our Power Lab the capability to be prepared for future products and market trends.
It didn't take us long to realise that our Power Lab would not be an off-the-shelf product. After specifying the test benches, we had to decide whether we should design the Power Lab ourselves, or hand this task over to an experienced design house. Following careful consideration, we decided on the former. Taking this approach would help to ensure the high quality and reliability of the test benches "“ and by keeping our know-how in-house, we could ensure that any future modifications would be easier.
After several months of construction, we started using our Power Lab in late 2017 (the official opening followed in 2018). In this purpose-built facility, we can carry out tests on SiC MOSFET transistors, SiC diodes, IGBTs, silicon power MOSFETs and gate drivers at DC voltages of up to 8000 V. These measurements can be carried out in a designated high-voltage room, equipped with several test benches.
The primary purpose of our test benches is the electrical characterization of MOSFETs and IGBTs. For these devices, we can use voltages up to 1500 V to measure switching times and losses, conduction losses and short circuit behaviour. Thanks to the high flexibility of our modular approach, testing is possible on various packages, such as THD, SMD, modules and customer boards.
In our lab, we have converters that can accommodate every configuration of AC and DC input and output, and put devices through their paces under realworld conditions of up to 15 kVA. Our test bench features an AC power supply (grid emulator) and various electronic loads, both in AC and DC form, with maximum voltages under test of 1500 V DC and 400 V AC. In addition, we can provide high-precision measurements of efficiency and losses. And to trim the carbon footprint of our facility, a regenerative function allows us to feed part of the energy that we use back into the grid, reducing our total energy consumption during testing.
The thermal analysis of modules, discrete devices, electronic boards, and even complete power electronics systems can be undertaken on our calorimetric test bench. It features continuous power supplies with a high current level, and a climatic chamber that can range in temperatures from -40 °C to 180 °C and provide humidity levels from 10 percent to 98 percent.
On another test bench, engineers can evaluate the isolation of in-house developed circuits, PCBs and reference designs. For these studies, the power supply enables a programmable output ramp up to 6 kV and 10 mA. For example, this setup can test the clearance and creepage distances of isolated gate driver boards.
Following the opening of our Power Lab, we are strengthening our relationship with our customers, who appreciate our insightful, prompt support at the application level. As well as providing this service, we are starting to undertake our own internal projects. Our aim with these test boards is to put power devices through their paces at the system level. Evaluations will be from a customer perspective. The results of these efforts will soon be published, in the form of application notes and reference designs.