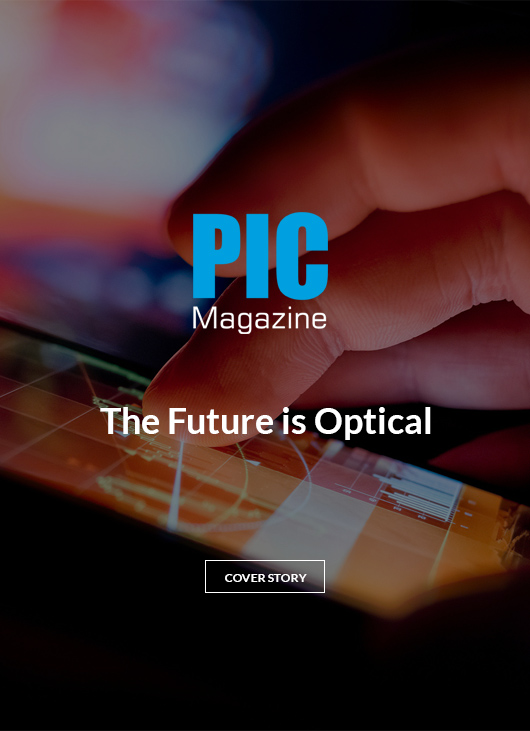
This article was originally featured in the edition:
PIC Magazine Issue 8 - March 2018
Nitride Semiconductor enters micro-LED display market
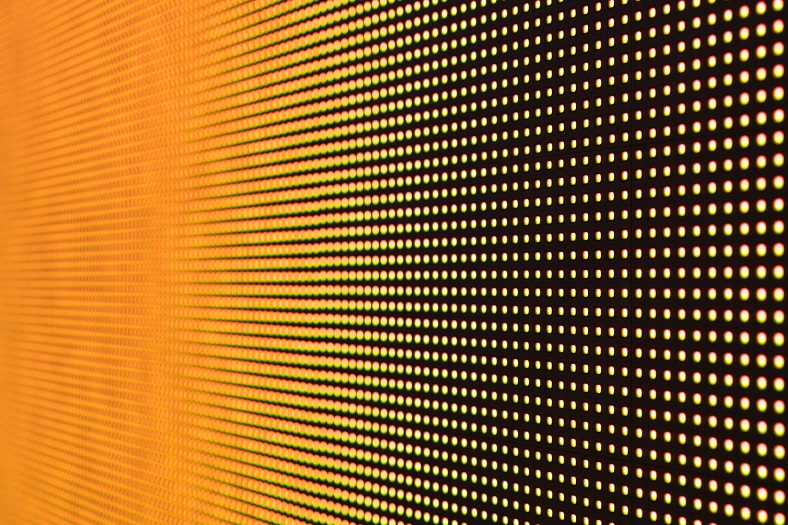
In early November, Japan-based UV LED manufacturer, Nitride Semiconductors, set-up a 100% owned subsidiary, Micro Nitride, to develop and manufacture micro UV-LED chips for micro-LED displays.
Initially targeting flexible displays for next generation smartphones, Nitride Semiconductors is ploughing 100 million yen - nearly £700,000 - into its new venture and expects displays to reach commercial markets come 2020.
"LED prices are coming down and down, and Chinese companies are getting bigger and bigger," says Nitride Semiconductors president and chief executive, Yoshihiko Muramoto. "Japanese LED makers are now in a difficult situation and need to add value, we need to make displays and not just LEDs, so we have established our new company."
Nitride Semiconductors unveiled its first UV LED in 2000 and has since delivered myriad wafers, chips and modules, to UV LED markets worldwide. Its new subsidiary will now produce micro UV-LED chips that comprise the micro UV-LED and a red, green, blue (RGB) phosphor to generate 'natural' white light.
Importantly, Muramoto reckons this UV-LED and RGB phosphor approach eases chip manufacture and leads to better-performing displays than existing methods. Today's fledgling micro-LED displays have typically been manufactured with red, blue and green LEDs or a blue LED that excites red and green phosphors.
However, many issues have stymied development. Take the RGB microLED array; mounting different semiconductor structures at high density isn't easy. What's more, current, voltage and response speeds vary from LED to LED, complicating chip control.
Meanwhile, for the micro blue LED excitation method, only the blue light is directly emitted while the red and green light result from phosphor conversion with an associated time lag. "Synchronising the colour response can be very complicated and we just don't have to manage any time lag," says Muramoto. "Our micro UV LEDs are also easy to mount and we have a fifty year history of using phosphor; it is very natural for us to used UV LEDs for displays and lighting."
The new subsidiary will focus on technology development, rather than manufacturing. As Muramoto puts it: "Japanese companies should aim to develop strong technologies and patents... there are many big LED manufacturers around the world and we can outsource our technology to them."
And with the technology in tow, the chief executive says his company's micro UV-LEDs are ready for mass manufacture, claiming fabrication is 'not so difficult'. Importantly, his company is also working with Japan-based display supplier, V Technology, on display manufacture.
Pick and place pains
MicroLED displays have been notoriously difficult to manufacture, using traditional pick and place transfer processes in which each sub-pixel is placed onto a CMOS backplane one at a time.
Given this, many companies have been working on mass transfer manufacturing processes, including V Technology. In such a process, thousands of sub-pixels are simultaneously moved from a sapphire or silicon donor carrier to the display substrate. While Muramoto will not disclose details of V Technology's mass transfer process, he emphasises: "[The company] can manufacture these displays relatively easily and they will be ready for market in two years."
In the meantime, the chief executive is confident that come mass production, final display costs will appeal. "We are going to need huge volumes of UV LED chips... but with our micro UV-LED method, we can simplify the structure of the display and the mass transfer process will be relatively easy."
Importantly, Nitride Semiconductors is also in close contact with smartphone manufacturers, which is where Muramoto is certain the micro-LED display action first lies.
He reckons the final cost of a display panel for a smartphone will be around US $50. In contrast, he claims the cost of a similar panel, made using other methods, will be as high as US $400.
"The merit of the micro-LED display is that it is flexible," he says. "So microdisplays should be used for wearable applications and we are talking with smartphone manufacturers about this [for next-generation devices]."
"Our technology is not so complicated and has been very easy to realise," he adds. "Our competitors have been struggling but we can get good results."