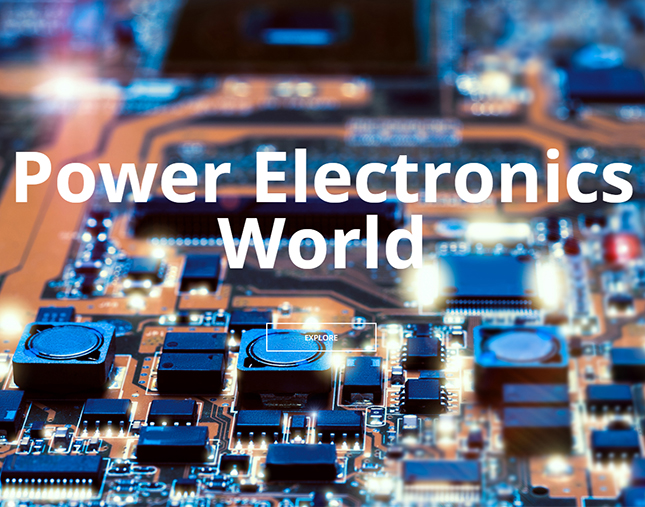
Infineon: SiC modules and more
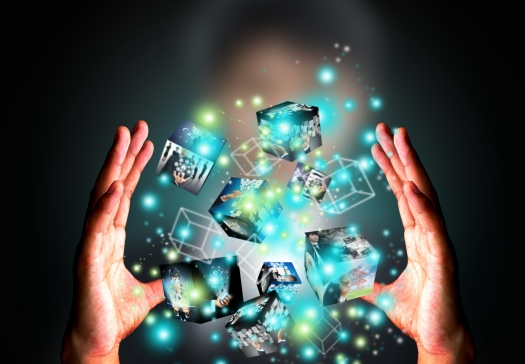
With volume production of SiC devices underway, what next for Infineon and compound semiconductors, asks Rebecca Pool.
What does the future hold for SiC device manufacture at Infineon?
It's no secret that higher efficiency, increased power density and a smaller footprint are just a few advantages that SiC MOSFETs offer over the silicon IGBTs. So as photovoltaic inverter, uninterruptible power supply and electric vehicle charging markets finally look set to adopt the technology, industry players have a raft of products ready.
Rohm recently unveiled an all-SiC, 1200V, 600A power module optimised for inverters and converters in solar power conditioners, UPS, and industrial power applications, just as Wolfspeed claimed its all-SiC 1200V power model had met harsh environment qualification tests.
In the last two years, STMicroelectronics has delivered a series of 650 and 1200 V SiC MOSFETs. And last month, Infineon revealed it had started volume production of its full-SiC module while delivering new module platforms and topologies for its 1200 V CoolSiC MOSFET family.
For Peter Friedrichs, Senior Director of silicon carbide at Infineon, the time is right to ramp up production. As he puts it: "We are definitely seeing a tipping point for certain applications - solar power conversion, UPS and electric vehicle charging - thanks, in part, to a very attractive total system cost."
Peter Friedrichs, Senior Director of silicon carbide at Infineon: "We believe that the playground for GaN HEMTs 600 V while SiC can compete with silicon IGBTs at 1000 V and above."
According to Friedrichs, inductive components make up a relatively large part of the bill of materials in many applications, including solar power conversion.
However, silicon carbide enables higher switching frequencies, allowing the use of smaller external components including inductors and capacitors, saving board space and overall component cost.
"This reduction in the bill of materials was the tipping point for the use of SiC Schottky diodes more than fifteen years ago," highlights Friedrichs. "And these SiC devices were extremely highly priced at the time."
But looking beyond system costs, the time is also right to ramp up production as the industry transition from 100 mm to 150 mm SiC wafers is well and truly underway.
In May, last year, STMicroelectronics announced it was scaling up its production of SiC MOSFETs and diodes on 150 mm wafers, predominantly to drive down manufacturing costs and deliver volume to automotive industry.
Now, Friedrichs confirms that Infineon has made the transition from 100 mm to 150 mm wafers for SiC diode production.
From word go, the company has also developed its SiC MOSFETs on 150 mm wafers, forging a strong connection between technology development and wafer availability.
And right now, the company is sourcing its 150 mm wafers from a handful of vendors worldwide - 'the known companies' says Friedrichs - that can offer volume capability.
"The move from 100 mm to 150 mm is a major change and as always, some customers are more reluctant than others to change their products, but we are nearly there," he says.
"For 150 mm, we still see slight quality differences from supplier to supplier, whereas with 100 mm wafers quality is comparable," he adds. "But we believe we will move beyond this very soon and it isn't a sticking point at all."
Chasing markets
Infineon now intends to ease its first full-SiC module based on 1200 V MOSFETs - Easy 1B - into volume production this year. This module will target solar, UPS and charging applications.
Meanwhile, a larger module - Easy 2B - will follow, and this version is designed for higher power ratings in target applications. Friedrichs reckons the latest module configurations will also soon be used in industrial drives, medical applications and auxiliary power supplies for the railway sector.
"We have already seen our hybrid modules - which combine silicon IGBTs with silicon carbide diodes - being used in solar power conversion applications, and these will now be partially replaced with the silicon carbide switch," explains Friedrichs. "Silicon carbide is also going to be highly appreciated in the emerging electric vehicle fast-charging infrastructure market, but we do not expect to see modules in actual electric vehicles until at least 2020."
Easy2B in half-bridge topology targets solar inverters, quick-charging systems and uninterruptible power supply applications.
For now, customer acceptance is not a huge issue. According to Friedrichs, some customers are more conservative than others and wish to see field data first, which can be difficult with a new technology. And while faster switching devices bring EMC issues, the Senior Director is confident the necessary support can be offered here.
Crucially, Friedrichs reckons the company can keep pace with future leaps in demand.
"We expect market growth to be around 20% [year-on-year], which is a lot greater than total power semiconductor growth," he says. "But we have good flexibility regarding volume manufacturing. We already have three and a half million SiC modules in the field - hybrid modules dominate so far - but we expect similar figures for the full-SiC modules as well."
Manufacturing aside, Friedrichs is also certain that SiC very much has its place amongst the rise of silicon semiconductor alternatives.
"We believe, for example, that the playground for GaN HEMTs is very much 600 V while SiC can compete with silicon IGBTs at 1000 V and above," he says.
And looking to the future, Infineon has a roadmap in place for higher voltage systems; Friedrichs expects demand for 1700 V full SiC MOSFET modules to be driven by solar power conversion and traction applications, and eventually 3.3 kV modules will follow.
"We have frequent discussions about 10 kV and 15 kV parts but are still in 'observation mode' for such devices," he says. "We want to understand that there is a real market here, and that this [development] wouldn't be an academic exercise to simply achieve a world record."