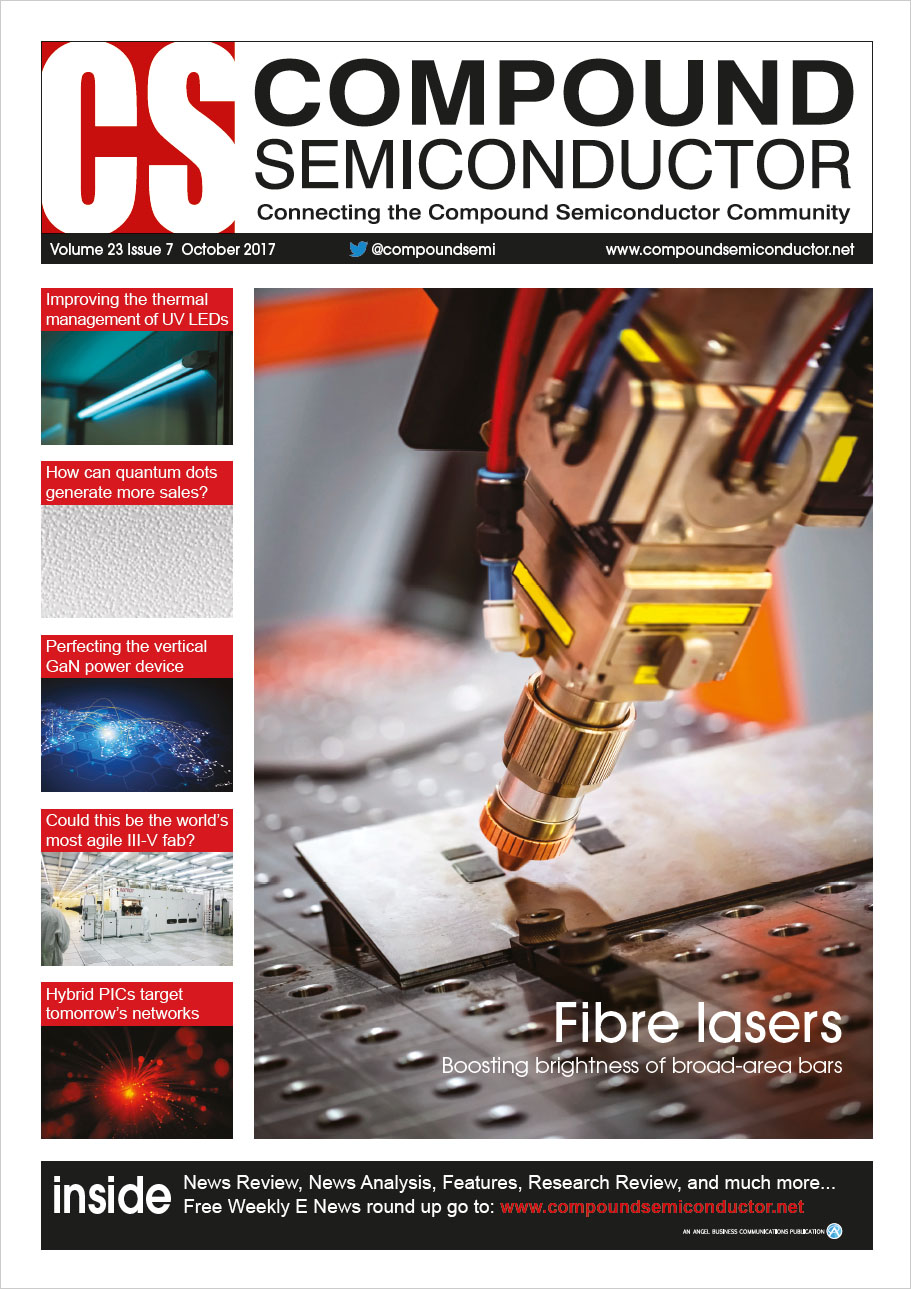
Setting a new benchmark for brightness
Reducing thermal lensing boosts brightness of broad-area laser bars by Christian Lauer from Osram OPTO Semiconductors
For any manufacturer, the ideal product is one that increases its share in a growing market. That's the case for the high-power laser diode, which serves a variety of applications from pumping fibre lasers to laser cutting and welding. It lies at the heart of fibre lasers and fibre-coupled diode lasers, which are taking market share from carbon dioxide and flashlamp-pumped, solid-state lasers, thanks to compelling attributes that include lower operating costs, greater efficiency and a smaller form factor.
Figure 1. Osram's high-power diode laser products have undergone a tremendous increase in output power since the 1970s.
Commercial opportunities for the high-power laser diode are increasing, driven by new additive manufacturing techniques, such as laser metal deposition, laser metal fusion and laser sintering. These laser-based technologies are laying the foundation for automated, and thus cost-effective, production of a handful of parts "“ and in some cases single entities. Rapid growth for additive manufacturing systems is predicted, due to the move towards digitalized, highly connected smart factories. In Germany this new era in manufacturing is known as Industry 4.0.
As Industry 4.0 takes off, the deployment of high-power diode lasers will become even more widespread, placing cost under an even more intense spotlight. This scrutiny will crank up the pressure on the bang-per-buck of all the components, including the most important of all, the laser diode.
In fibre lasers, laser diodes tend to be in the form of broad-area laser bars "“ these comprise several wide emitters and deliver a very high optical power. CW outputs of hundreds of watts to a few kilowatts are possible, using industrial diode lasers based on multi-bar stacks.
One option for lowering the cost of the fibre laser system is to increase the output power and the efficiency of the laser diode, and ultimately trim the number of chips. Success in this endeavour would have additional benefits, as it would simplify cooling and reduce the complexity associated with the coupling of the laser beam into the fibres. Further gains could result from improvements to the beam quality of laser diodes, as this can increase the coupling efficiency into the fibres.
Figure 2. A highly elliptic beam is produced by individual laser diodes and the emitters of a laser bar.
Material processing
At Osram Opto Semiconductors of Regensburg, Germany, we are making progress on all these fronts, and are setting a new benchmark for brightness, a figure of merit that is critical to evaluating the capability of a laser when deployed in a fibre-laser system.
Our efforts draw on more than 40 years of experience in producing and developing infrared laser diodes and laser bars based in AlGaInAs and GaInP, two alloys that can deliver emission at around 1 μm, an ideal wavelength for materials processing (see Figure 1). Since the 1970s, the output of our lasers has increased from just a few watts to 250 W, with the efficiency of power conversion climbing to now exceed 60 percent. Further improvements will follow: by 2020 we expect to produce 400 W laser diodes with an efficiency of more than 70 percent.
Figure 3. Osram's SPL BF98-40-5 laser bar was specifically developed for efficient coupling of light into fibres.
Increasing power and efficiency are not our only objectives "“ we are also improving the beam quality of the laser, because this determines how efficiently light is coupled into a fibre. Today, our efforts are focused on a mini-bar, known as the tailored bar, or T-bar for short. This architecture has been developed to support a relatively recent move by manufacturers of high-power diode lasers; namely, designing a laser bar for a certain type of fibre, to reduce the complexity of the light incoupling optics. With a wavelength of 976 nm, our T-bar is specifically designed to pump ytterbium-doped fibre lasers.
Beam quality is a measure of how well a laser beam can be focused. It is defined by the product of the divergence half-angle and the radius of the beam in the focus point, known as the beam parameter product (BPP). Note that the beam quality is closely connected to the brightness of the laser, that is, its optical output per unit of area and solid angle. To realise a high brightness, a high proportion of the light emitted by the laser has to be coupled into a fibre in an efficient manner.
The beam quality of the laser decreases with its output power, thus setting an upper limit to the suitable output power of the whole system. Or, in other words, if a laser system is to operate as cost-efficiently as possible, the optimum beam quality for each fibre must be realized with the highest possible optical power.
Coupling the output from a laser diode into a fibre is not that easy. Ideally, the beam would be circular. However, it is actually elliptical (see Figure 2). This means that the beam parameter product of the laser diode has different values in the vertical and the lateral directions (referred to as the fast and slow axes, respectively). Along the fast axis, the beam angle is typically 40°, while it is just approximately 10° along the slow axis.
The tremendous difference in the beam divergence along the fast and slow axes stems from the geometry of the active region: it is just a few microns thick, but around 100μm wide. Due to these dimensions, in the vertical direction the standing light wave in the resonator develops just one optical mode and provides diffraction-limited output, enabling easy coupling, while in the lateral direction there are a large number of higher order modes and the emission exceeds the diffraction limit by far. Trimming the width of the emitter could cut the number of modes, but the price to pay for this is a cut in output power. However, optimisation is still possible, and great strides could be made, as today's values for beam quality fall far short of what is theoretically possible. In the vertical direction it is a different story as this "optimisation" is inherent to the vertical waveguide design.
Figure 4. (a) Characteristics of Osram's SPL BF98-40-5 bar. Up to approximately 70 A, the output power remains linear with the current at a slope of around 1.08 W/A. Efficiency exceeds 60 percent up to 65W. (b) Dependence of the lateral beam angle, and thus beam quality, on output power. The target value of 7° or 15.5 mm-mrad is achieved at 44 W. This corresponds to a brightness of 2.8 W/(mm-mrad).
We have optimised the design of our T-bar "“ the SPL BF98-40-5 "“ for coupling into fibres with a diameter of 200μm wide. However, the development of this chip, as well as the measurements on it, can be directly applied to other designs of laser diodes.
Our T-bar chip is 5 mm wide, 4 mm long and comprises five 100-μm-wide emitters, arranged side by side in parallel (see Figure 3). The fill factor, that is the percentage of space taken up by the emitters over the entire edge area, is only 10 percent. The advantage of using a small fill factor is it largely avoids thermal crosstalk between the emitters. To keep the operating temperature of our device as low as possible, we hard-soldered it, using a gold-tin alloy, to copper-tungsten sub-mounts with microchannel coolers. A common weakness for the edge-emitting laser is the mirrors on the facets, which are exposed to very high power densities. However, this is not an issue for our chip, as there are no signs of catastrophic optical damage, even at a current of 100 A (see Figure 4 (a)).
Figure 5. Increase in optical output power for a beam parameter product of 15.5 mm-mrad, based on the SPL BF98-40-5 (black), with a longer resonator (grey) and with narrower emitters (orange).
When the current is this high, our device is hampered by thermal roll-over. In this regime, the chip is so hot that any further increases in current do not lead to a higher output, but just impair efficiency. Due to this, lasers are typically operated well below the thermal rollover point. For the SPL BF98-40-5, operation at an output power of below 65 W is to be recommended, as this produces a power conversion efficiency in excess of 60 percent.
The optimal beam parameter product for the laser is governed by the value for the corresponding fibre. The fibre we are using has a core diameter of 200 μm, a numerical aperture of 0.22, and a beam parameter product 22 mm-mrad.
Based on the latter value, we calculate that the most efficient optical incoupling will occur when our laser has a beam parameter product of 15.5 mm-mrad. This corresponds to a lateral divergence angle of 7° "“ at this angle, the beam area contains 95 percent of the output power.
Measurements on our T-bar laser show that the target value of 7°, or 15.5 mm-mrad, is reached at 44 W (see Figure 4 (b)), resulting in a brightness of 2.8 W/(mm-mrad). Crank up the power beyond this and beam divergence increases, preventing full coupling of the light from the bar into the fibre. We can conclude from this observation that it is the beam quality of the chip that limits the efficiency of the entire system.
Figure 6. Thermal lensing of a single emitter as a function of pulse length and current.
Longer resonators, narrower emitters
We can be sure that it is the beam quality that is holding back system efficiency, because extensive reliability tests show that chips can deliver significantly higher output powers while maintaining long lifetimes. Our goal, therefore, is clear: to increase beam quality or vice versa achieving a higher output power at the beam parameter product of 15.5 mm-mrad.
Efforts have kicked-off with an increase in the length of the resonator from 4 mm to 5 mm. Switching to the larger chip enhances heat dissipation, and ultimately allows the laser to operate at a cooler temperature while its current is maintained. Thanks to this refinement, the output power at 15.5 mm-mrad increases to 52 W, and the resulting brightness improves to 3.4 W/(mm-mrad).
Our second modification to the T-bar laser has led to a reduction in the number of high lateral modes. As the number of these modes increases with the width of the emitter, we made it narrower, trimming it from 100μm to 80μm. This enabled an output of 60 W and a brightness of 3.9 W/(mm-mrad) at 15.5 mm-mrad (see Figure 5).
Unfortunately, the lengthening of the resonator and the reduction in the emitter width don't just lead to a substantial increase in output power at 15.5 mm-mrad. They also have undesirable consequences: they increase chip size, due to the introduction of a longer resonator, and this increases costs; and a narrowing of the emitter increases the power and current densities within the chip, raising reliability concerns. One upshot is that additional quality tests are needed to ensure safe operation at maximum operating conditions.
Trimming thermal lensing
These downsides have prompted us to search for a way to improve the beam quality while retaining the standard chip geometry, which is the 4 mm resonator length and 100 μm emitter width.
We have focused our attention on thermal lensing, which is associated with a lateral gradient in the refractive index. This occurs because there are electrical resistances and optical losses present during device operation that cause the active region to heat up, heat to flow to the heat sink, and a non-uniform temperature profile to appear across the chip.
The lateral gradient in the refractive index resulting from the non-uniform temperature profile causes the diffraction of light beams towards the centre of the emitter, resulting in a large number of lateral modes and a higher divergence angle.
Measurements on our T-bars reveal the impact of current and pulse length on thermal lensing (see Figure 6). With very short pulses the chip barely heats up and the beam angle remains more or less constant as current increases. Lengthen the pulses, however, and higher beam angles are seen at higher currents. When the pulse lasts forever "“ in other words, the device is operated in CW mode "“ the beam angle starts increasing at just 5 A. So, for a bar with five emitters, the threshold is only 25 A.
Turning to a new chip structure has reduced the lateral temperature gradient in the active region, reduced the divergence angles, and delivered a clear drop in the beam parameter product at a given output power (see Figure 7). What this means is that our laser can now deliver about 15 percent more power for the same beam parameter product. For the target value of 15.5 mm-mrad, the optical power has increased to 50 W and the brightness hits 3.22 W/(mm-mrad).
Today we are manufacturing extremely efficient, bright laser bars for coupling into fibres. These bars, which combine a high brightness of just under 3 W/(mm-mrad) with an efficiency of over 60 percent, can improve the overall system performance of industrial fibre and diode lasers. Thanks to this, costs are lower, as they employ fewer chips that require less cooling.
One promising option for increasing the performance in the future is to reduce thermal lensing. This will open the door to further increase in the output power at a given beam quality, while not compromising chip cost or reliability.
We have already achieved promising results with this approach, and over the next few years we will optimise this technology and transfer it to the production stage. Our goal is to take optical power to a new high while maintaining high beam quality, so that diode laser systems are more cost-efficient than ever before.
Figure 7. Reducing thermal lensing increases the optical power by around 15 percent at a constant lateral beam parameter product.