
Propelling the GaN VCSEL to the green
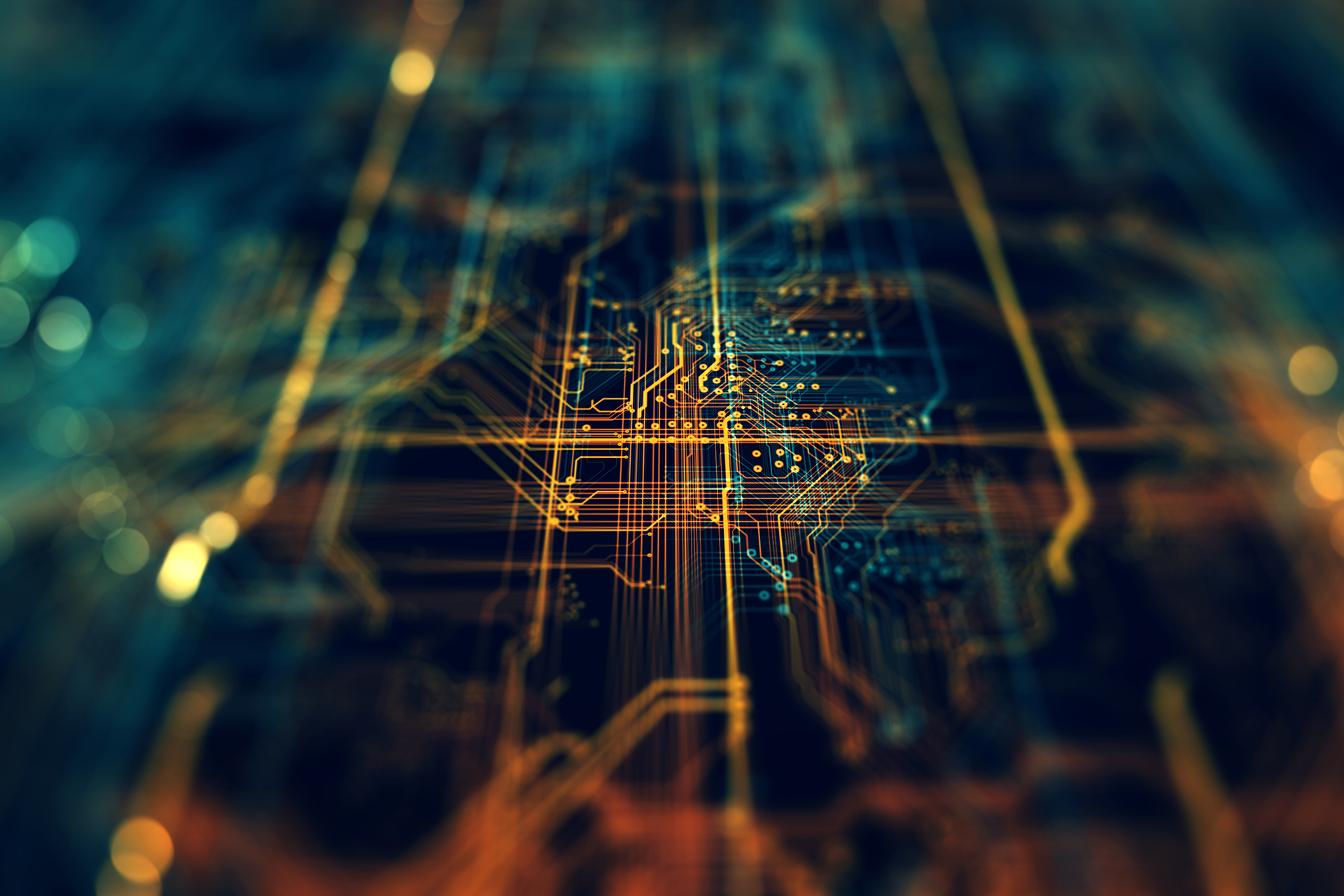
Introducing quantum dots enables GaN VCSELs to penetrate the "˜green gap' by Baoping Zhang from Xiamen University
What do you believe is most desired in a laser? Is a high modulation speed? Or is it a low-threshold, a high efficiency, or a circular emission profile that tops your wish list?
The good news is that there is a class of laser that can fulfil all of these attributes and more: the VCSEL. Thanks to its all-round capability, sales are flourishing, with devices based on GaAs being deployed in optical mice, sensors and optical networks.
To grow revenues even more, this device must serve even more applications. That's possible by broadening the range of VCSEL emission wavelengths. When GaAs VCSELs emitting in the red and infra-red are joined by GaN-based cousins covering the blue and green, VCSELs can be used in projectors, displays, and solid-state lighting.
Unfortunately, making a GaN-based VCSEL is far more challenging than making a GaAs-based one. That's not to say that there has been no success "“ several groups have reported electrically driven GaN-based VCSELs that have InGaN/GaN quantum well active layers and produce room-temperature, continuous-wave emission in the near ultra-violet and the blue. But in the green, only Nichia of Japan has made any significant progress. Its team of researchers has succeeded in producing pulsed emission from a VCSEL emitting at 503 nm. However, even this is not true green, but cyan.
The green gap
Propelling InGaN-based devices from the blue to the green is not easy. The problem is well known, and has been given the moniker "˜the green gap'.
One of the reasons why it is so difficult to produce efficient emitters between 500 nm and 600 nm is that there is a lattice mismatch between InGaN and GaN. This gives rise to strain during epitaxial growth of InGaN on GaN, and culminates in the creation of a piezoelectric field. This causes band inclination, and pulls apart electrons and holes to different sides of the quantum well, reducing their chances for radiative recombination. Efficient emission is also impaired by defects in the InGaN layer. These imperfections, which are prevalent when the InGaN layer is too thick or the indium content is too high, can capture freely-moving carriers.
Another impediment to producing a high-performance, green-emitting VCSEL is the large effective masses of the carriers in the GaN-based material system. With InGaAs and its related alloys, carrier masses are far lower, leading to a lower transparent carrier density and a lower threshold current.
Due to all the issues detailed above, the threshold current in the GaN VCSEL is relatively high. But it doesn't need to be. Efforts by our team at Xiamen University, China, have shown that green GaN VCSELs can produce a great performance when their active region is made from quantum dots, rather than quantum wells. Note that this idea is not new, and has already led to some very impressive results with GaAs- and InP-based lasers.
In the GaN material system, the introduction of quantum dots transforms the device. Formation of these structures undergoes strain relaxation, leading to the elimination of electric fields that peg back radiative recombination. What's more, the dots tightly freeze the carriers, so they are no longer captured by defects; and their energy is quantized into restricted values, so the issues associated with a large effective mass disappear. And last but by no means least, the dots have a far higher differential gain than the wells do. The upshot of all these factors is the promise of low-threshold lasing.
VCSEL designs
VCSELs are formed by surrounding an active region with a pair of mirrors, in the form of distributed Bragg reflectors, which are capable of a reflectivity in excess of 99 percent. The production of GaAs-based VCSELs involves the epitaxial growth of the mirrors, which are based on the pairing of GaAs and AlGaAs. This duo is very good, combining lattice matching with a significant difference in refractive index.
Fabricating GaN-based VCSELs is far more challenging. The only option for making a lattice-matched distributed Bragg reflector with the nitrides is to pair GaN with an AlInN alloy with a specific indium content. This combination is not ideal, however, because the mirrors that result have a narrow stop band, due to the small difference in refractive indices. In addition, it is not easy to control the alloy content in the whole of the distributed Bragg reflector. Note that switching to the combination of AlGaN and GaN only makes matters worse, as it leads to strain accumulation, which causes defects.
In our view, it is better to form mirrors from dielectric materials, such as SiO2, Ta2O5 and TiO2. These oxides are well used in optical coatings, and they can be deposited by mature methods, such as electron-beam evaporation and magnetron sputtering. In addition, the stop band of reflectivity of a dielectric distributed Bragg reflector is much broader than that of GaN-based variant, making it much easier to achieve optical alignment.
Incorporating the dielectric distributed Bragg reflectors into the VCSEL requires a thinning of the wafer. For the team at Nichia, which grows the epitaxial layers on a native substrate, GaN must be thinned from a few hundred microns to just a few microns. This is a very complicated task, and it is easy to cause damage to the active region.
We employ an alternative approach, growing epilayers on sapphire, before removing this substrate by laser lift-off. To liberate the GaN epistructure, light from a violet laser impinges on the epiwafer through its backside. This radiation is absorbed at the interface with GaN. Thanks to a very high photon density, GaN is heated beyond its melting point, allowing the epitaxial layers to detach from sapphire.
One of the merits of this approach is that the liberated structure is just a few microns thick. As that's close to the thickness of the cavity, there is no need to undertake a complicated thinning process.
Figure 1. (a) InGaN quantum wells contain defects that can trap freely moving carriers. (b) The radiative efficiency in InGaN quantum wells is impaired by the internal electric field, which pulls apart electrons and holes. (c) Although there are defects in quantum dot structures, radiative recombination can still be high, thanks to strongly localized carriers. (d) InGaN quantum dot devices have a band structure that is free from an internal electric field.
A key step in the fabrication of our green VCSELs is the growth of a quantum-dot-based active region. Our approach for this draws on the work of Jianping Liu's group from Suzhou Institute of Nano-tech and Nano-bionics, Chinese Academy of Sciences. This team produces its green-emitting quantum dots via MOCVD at relatively high temperatures, which lead to superior material quality. The dots that self-form along step edges on the surfaces of the c-plane GaN show no evidence of internal electric fields, indicating that they are free from strain. Due to its absence, internal quantum efficiency is as high as 41 percent.
The efficiency is not the only merit of these dots. They also provide far greater carrier confinement than the wells, with an estimated localization energy of 105.9 meV; and the density of the non-radiative recombination centres in the dots is far less than it is for wells emitting at the same wavelength.
Cutting losses
Key device characteristics, such as threshold gain and current, are determined by the optical loss within the cavity. For GaN-based planar cavities, the optical loss is caused by a combination of mirror loss, absorption loss and scattering loss. Mirror loss results from imperfect reflectivity of the distributed Bragg reflector, while absorption loss comes from the indium tin oxide and multi-quantum well regions, and scattering loss is associated with dislocations and surface/interface roughness.
Figure 2. Distributed Bragg reflectors formed from Ta2O5/SiO2 have a better stop bandwidth and a higher maximum reflectivity than those made from AlN/GaN. Note that both reflectors are formed from 15 pairs.
The importance of absorption in the indium-tin oxide layer has been highlighted by Shing-Chung Wang's group from National Chiao Tung University, Taiwan. This team reported the first GaN-based VCSEL lasing under continuous current injection at low temperature, using a VCSEL with a 240 nm-thick indium-tin oxide layer. By trimming this thickness to just 30 nm in a subsequent device, they obtained continuous-wave lasing under current injection at room temperature.
Loss in the multi-quantum well region results from a non-uniform carrier distribution. This state-of-affairs is also seen in LEDs, where the carrier density is not uniform, and hole concentration is highest in the well nearest to the p-GaN region. This inhomogeneity contributes to efficiency droop in LEDs driven at high injection currents. In VCSELs, this mechanism for efficiency loss is even more prevalent, due to the need for even higher injection currents.
When it comes to scattering loss, the dislocations in GaN play a dominant role. The density of these imperfections is particularly high in GaN-based VCSELs with dielectric mirrors. In this class of device, which involves the growth of epitaxial layers on sapphire substrate, the large lattice mismatch leads to a high density of dislocations that cause significant scattering loss.
To minimise all these losses, we have investigated the performance of four different devices. This study revealed that a thin indium-tin oxide layer and a coupled quantum well active region are the key ingredients for forming a low loss, high Q-value cavity. Using this combination, we could form devices with a Q-value as high as 3570. These efforts also revealed that a low-loss quantum well design is particularly important in fabricating high-Q value, GaN-based planar cavities, and in reducing the threshold current of GaN-based VCSELs.
Figure 3. Laser lift-off can separate sapphire from the nitride epilayers of the VCSEL. A key merit of this approach is that it avoids the complicated, damaging, thinning process that is required when using a thick GaN substrate.
Keeping cool
As VCSELs operate under high current densities, inadequate thermal management can lead to overheating. That's highly undesirable, as it leads to degradation of device threshold and power, and can ultimately impair device performance and restrict the number of applications that the VCSEL can serve.
To ensure that our VCSELs can dissipate the heat they generate efficiently, we transfer them to a silicon substrate via metal bonding. Sample degradation is prevented by our use of a low-temperature, tin-fusion bonding technique.
Studying the emission of quantum wells bonded at various temperatures reveals that if this step is undertaken at 250 °C or less, there is no degradation to the optical properties of the wells. We use tin for bonding, because this melts below 250 °C, while other metals used for bonding have higher melting temperatures.
Figure 4. (left) Lasing spectra obtained from different VCSELs made from the same quantum dot wafer. Wavelengths can be controlled by the cavity length, which modulates the profile of the optical field in the cavity and the interaction between photons and electrons. (right) Threshold current as a function of wavelength reported by different groups.
To further improve the thermal dissipation, we replace silicon with a copper plate. This not only enhances the efficiency of thermal diffusion, and in turn significantly reduces the threshold current "“ it also simplifies the fabrication process for these VCSELs. Adopting these technologies has enabled us to produce a portfolio of VCSELs with emission wavelengths of 479.6 nm to 565.7 nm. Note that this range, which covers a substantial proportion of the green gap, uses the same quantum dot active region, but different cavity lengths. That's a much neater solution to realising lasers with different wavelengths than that employed for edge emitters, which use differences in material growth to tune the wavelength.
Our next step is to optimize our VCSEL architecture and our fabrication process. Success on both these fronts should lead to practically usable green VCSELs that can serve many applications.