
Refining CPV
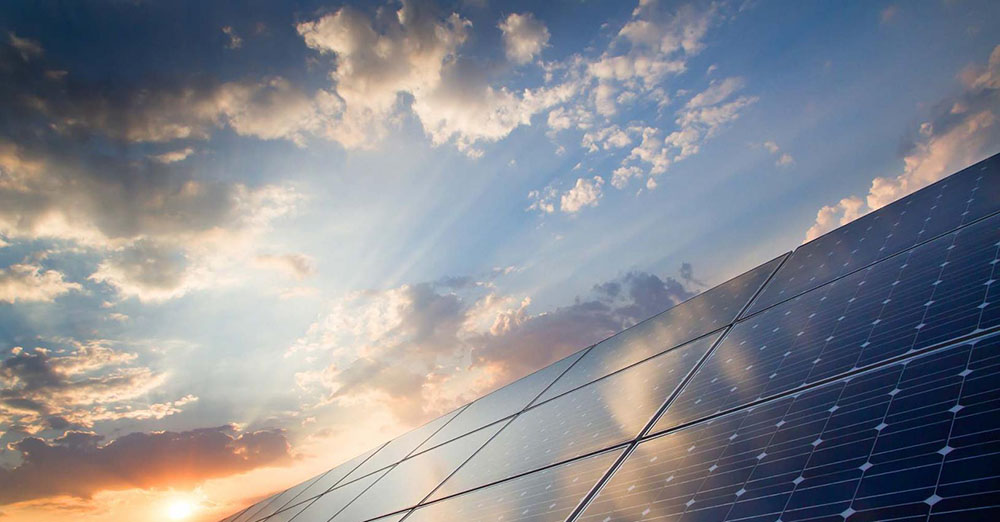
Employing the mass production techniques of the optoelectronic industry will increase the bang-per-puck of CPV by Richard Stevenson
It would be easy to think that the CPV industry has completely disappeared. Deployment of this technology has fallen through the roof, with many big names having filed for bankruptcy over the last few years.
However, there is still activity "“ and with that comes hope. Early last year STACE "“ Saint-Augustin Canada Electric Inc., a supplier of large electrical equipment in the power generation industry "“ acquired Soitec's CPV technology; and in Europe, a collaboration between several companies is currently developing a lower-cost, highly efficient CPV system that borrows high-volume manufacturing techniques from the optoelectronics industry.
The latter project was detailed at Advances in Concentrator Photovoltaics for Space and Terrestrial Applications, held at Cardiff University on 8 March. Spokesman for the project, entitled A low Cost, High Efficiency, Optoelectronic HCPV Module for 1000 Sun Operation, was Andy Johnson, IQE's Solar Business Unit Leader and CPV Technology Director.
According to Johnson, the focus of the €1.24 million project is to improve the performance of the FullSun CPV modules. The starting point is a design that has a concentration of 625 suns, and produces an efficiency of 30 percent by harnessing concentrated sunlight with cells that have a 36 percent efficiency. The targets are to increase efficiency to 1000 suns, and to realise a 37 percent module efficiency using triple-junction cells with a higher efficiency than before.
Three different triple-junction cells are being evaluated in the project: a generic, lattice-matched design from IQE that has an efficiency of 39 percent or more at 1000 suns; an Azur Space 3C44 cell, which has an inverted metamorphic architecture with an efficiency in excess of 42 percent at 1000 suns; and a latticematched device made by Solar Junction, which features a dilute nitride for the low-energy junction. "Solar Junction's materials was grown by MBE," said Johnson.
The philosophy behind the module, made by FullSun, is to adopt best practice from the optoelectronics industry, including the use of surface mount technology. This approach, which drives down capital costs, involves the use of cells that are just 1.3 mm square. These cells, which are covered by a silicone lens and packaged on lead frames, are sparsely arranged on an aluminium back plane. "There is no need for additional heat sinking," explained Johnson.
Benefits of this design of module include reduced maintenance and purchase costs. What's more, the units have a low mass "“ they are less than 4 kg "“ and a thickness of just 48 mm, making them easier to transport; and installation is straightforward, trimming labour costs.
Johnson explained that a team at Fruanhofer ISE is behind the changes to the optical design of the module that is propelling the concentration from 625 suns to 1000 suns. Given a target area of 1 mm by 1 mm, the team retained the secondary optical element "“ that is, the silicone lens on top of the cell "“ and just adjusted the primary optical element, the Fresnel lens. Its focal length could be changed.
Another partner in the project is the III-V Semiconductors Group at the Solar Energy Institute of the Technical University of Madrid (IES-UPM). This team have worked on optimising the grid on the 1.3 mm by 1.3 mm cells, by evaluating the impact of varying grid line width and the number of fingers. They considered using between 12 and 25 fingers, and found a sweet spot of 14 to 18. The team's next step is to compare the performance of different grid structures.
These researchers only have a few more months to work on this. Assembly of the 1000 sun modules is slated for the third quarter of this year, and testing is scheduled to follow in quarter four.
These field tests will take place at the University of Cypress, an ideal location for putting any photovoltaic system through its paces. It is hoped that this design, which will be mounted on a two-axis tracker, can get close to a cost of €0.35/W to €0.45/W.
Ensuring reliability
This metric is widely used. However, its validity was questioned in a talk given by Carlos Algora, head of the group at IES-UPM. He championed the use of the levelised cost of energy, which is equal to the total lifecycle cost, divided by the total energy generated over the lifetime of the system. According to Algora, this is a superior figure of merit, because as well as including the initial purchase price of the system, it accounts for maintenance and operational costs and the lifetime of the system.
Algora went on to point out the importance of the reliability of the cells "“ this impacts degradation, operation, maintenance and system lifetime. He stressed that reliability is different to qualification. According to him, the purpose of qualification is to try and give confidence to customers, and to avoid infant mortality, while any assessment of reliability ideally involves field tests. However, as deployments of CPV systems are recent, reliability has to be gauged with accelerated lifetime tests.
"The purpose [of the reliability tests] is to find out how, when and why failure will occur," explained Algora, adding that the right approach is to stress one parameter while leaving all others unchanged.
Tests were undertaken on 45 commercial, latticematched, triple-junction cells with dimensions of 7 mm by 7 mm. Standard operating conditions for these cells are a concentration of 820 suns, and a device temperature of 80 °C. To accelerate degradation, cells were stressed at 119 °C, 126 °C and 164 °C, while driven at a forward current of 3.2 A to emulate the intensity of illumination of sunlight on the device. Measurements of current-voltage characteristics offered an insight into degradation.
Using an Arrhenius-Weibul model, Algora and coworkers determined that the probability for cell failure after 25 years is only around 0.1 percent, and that the warranty time for a 5 percent failure rate is more than 110 years, assuming 5 hours of operation per day.
At first glance, that looks like a great result. However, Algora warned against getting too excited, because cells don't work at a constant temperature. He argued that the key question is this: "How long will they work in real conditions?"
Advances in Concentrator Photovoltaics for Space and Terrestrial Applications, was held at Cardiff University on 8 March.
To try answer this, he and his co-workers have carried out calculations for a cell operating in a CPV system featuring a Fresnel lens. They determined operating temperatures for different ambient temperatures and wind speeds, for cells in CPV systems situated in Madrid, Denver and Tuscon.
For Madrid, the mean temperature is an encouraging 67 °C, while the figure for the mode is 78 °C. However, there are times when the cell exceeds 100 °C.
"When the temperature is greater than 100 °C, this has a tremendous impact on solar cell performance," revealed Algora, who explained that this shortens the warranty time from over 100 years to just 35 years.
In Tuscan, the cells could get even hotter, spending some time above 110 °C. This slashes the warranty time for the system to 15 years. Meanwhile, in Denver, where it is cooler, the warranty would be 60 years.
Obviously, it is critical to prevent the cells from running at high temperatures. One option is to increase the thickness of the back plane to enhance heat dissipation, but this adds not only to the weight, but also the bill-of-materials and the shipping costs. Reducing the concentration would also lead to lower chip temperatures, but at the expense of less generated power.
Better still, argued Algora, is to use smaller cells, as they are better at dissipating the heat. It's a point that Johnson and his partners would have delighted in hearing, as this is the route they have adopted.
During Algora's talk, delegates were reminded of the insights that can be made by modelling the performance of the CPV module. Up until very recently, the barrier to this had been the need to write code to simulate a CPV system "“ but that's no longer the case, thanks to the release into the public domain over the last few months of a model developed at Imperial College London.
Diego Alosno-àlvarez highlighted the capabilities of this software. The code, which has been developed by the team at Imperial over many years, has been released as an open source this year. The current form, Solcore 5, builds on its predecessors by including tunnel-junctions in device design.
Features of this open source, which is considered to be both a teaching and a research tool, include: a database for the properties of III-V, silicon and germanium; and an option to select either a laser, an LED, a form of Blackbody radiation or a standard solar spectrum as the illumination source.
A limitation of the current model is that it is not equipped with ray-tracing for micro-textures, such as plasmonic structures. Addressing this could be one of the goals for the future, explained Alosnoàlvarez, along with improved documentation and benchmarking of the software.
The insights provided by this tool, by the work of Algora, and by the IQE-led team developing a 1000-sun concentrator should improve the competitiveness of CPV. But there is no doubt that this elegant form of photovoltaics still has a long way to go before it can slacken the vice-like grip that silicon has on this market.