
IQE: 30 years of growth
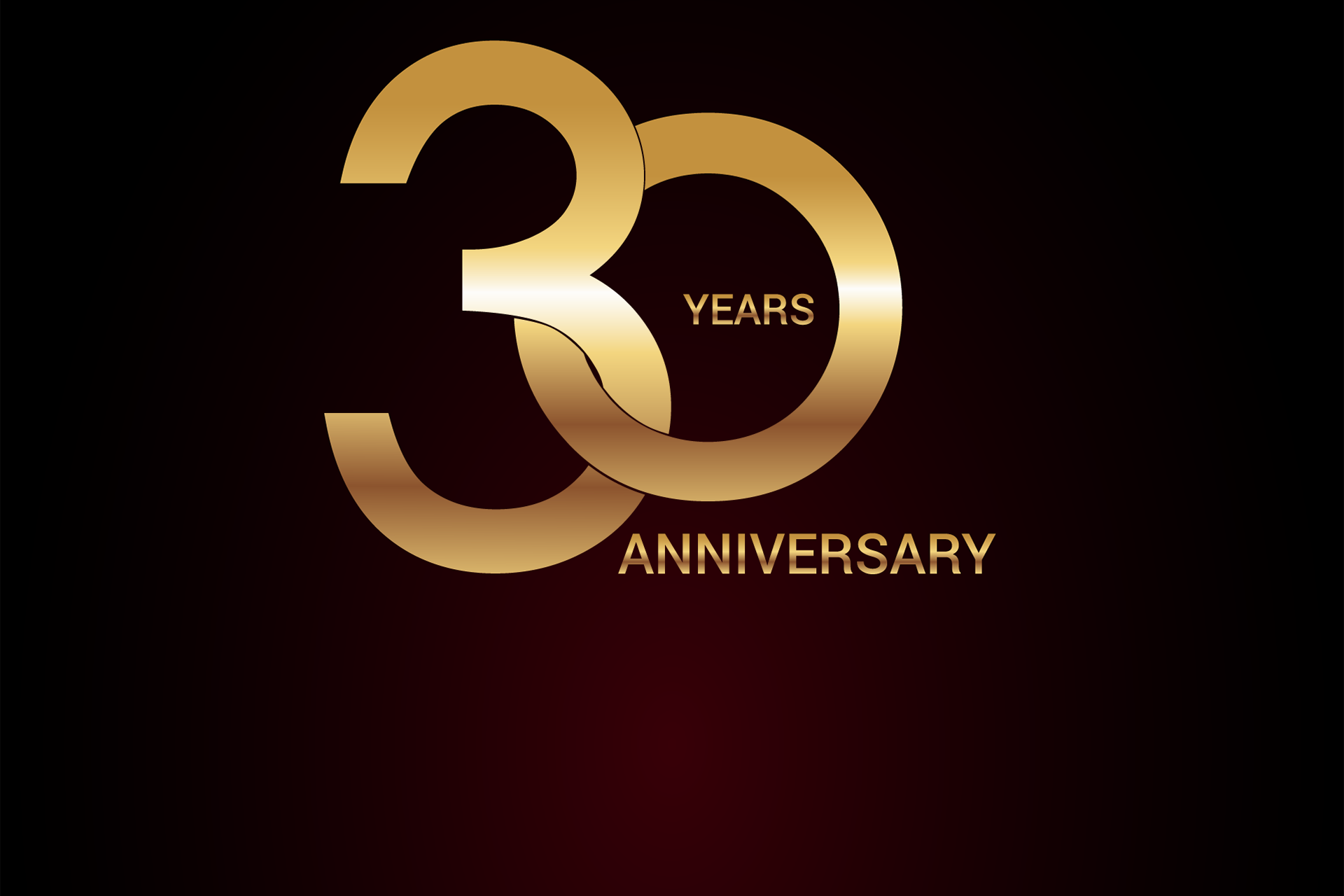
At the beginning of 1980s, companies making InP chips for the fibre-optic industry had a broad range of expertise. Their skillsets included the design of the device, its testing, and its production "“ including the most challenging aspect of all, the epitaxial growth of the heterostructure.
But in 1988, this situation changed irrevocably. From then on, those chipmakers could choose between adopting a vertically integrated approach, or outsourcing epitaxial growth to a new start-up. Now known as IQE, this epitaxial specialist launched under the name Epitaxial Products International (EPI), reflecting its desire to serve a global industry.
Over the last thirty years the company has increased in size, to have manufacturing facilities on all three major continents; and it has expanded its portfolio, by diversifying its range of epiwafers, and adding substrates and material technologies to the mix. What's more, it has become the driving force behind the development in the world's first compound semiconductor cluster, which is making much headway in South Wales.
At the helm of the company since its formation is its co-founder Drew Nelson. After gaining a doctorate at Sheffield University "“ where he developed microwave devices, grown by LPE and MOCVD "“ in 1981 he joined British Telecom, where he led a group developing epitaxial technologies for detectors, lasers and modulators. But that was never going to be his long-term career "“ he had always wanted to run his own company.
The spark for fulfilling this dream came through his involvement in the Joint Opto Electronic Research Scheme, an initiative sponsored by the UK government. This programme, which focused on developing the technology for optoelectronic applications such as fibre-optic networks, brought many of the nation's biggest technology companies, such as BT, Plessey, GEC and STC, together with several smaller organisations and universities.
Through JOERS, Nelson met Mike Scott, who shared his vision for launching a supplier of epiwafers. "We gauged the level of appetite, and we were encouraged to set up the business," says Nelson.
Nelson had no intention of going to his bosses, to see if BT would fund this venture: "It definitely wasn't the right culture." Instead, he crafted a business plan with Scott and tried to secure backing from venture capitalists. "It wasn't easy at times, but eventually we were put in touch with Shell Ventures."
This introduction led to funding from Shell Ventures, a part of the Shell Group that had been created following encouragement by the then Prime Minister, Margaret Thatcher."
She basically said to them, you've gained a huge amount of revenue from North Sea oil, and you should plough some of that back into British technology. We ended up being their keyhole on the semiconductor industry."
Coming to Cardiff
Backed by "a couple of million pounds", Nelson and Scott decided to build their facility on a brown-field site on the outskirts of the Welsh capital, Cardiff.
"The Welsh Development Agency were the premier agency in the UK industry for attracting inward investment, and we were able to get some capital grants to help the company," says Nelson.
That wasn't the only benefit of this particular location, however: the Electronic Engineering Department at Cardiff University had tremendous expertise in building and testing lasers. "We thought that would be a good source of skilled labour and engineers."
Once the fab had been built, it was kitted out with equipment to grow and characterise epiwafers. While MOCVD tools were by no means as advanced as they are today, at least they didn't have to be home built.
"We could have systems built for us, to our very specific designs, which we did," recollects Nelson. "So we started with one MOCVD system from Thomas Swan, and one MOCVD system from CVT."
His Royal Highness, the Duke of Edinburgh (right), unveils a plaque to mark the opening of the extension to IQE's St Mellon's facility.
Substrates were sourced from AXT, and some suppliers in Japan. "Two-inch substrates were the norm, and even at BT we had been using even smaller substrates than that," says Nelson. One of the benefits of the JOERCs initiative is that it helped to create a UK manufacturer of metal-organic source materials, Epichem. EPI used this supplier, which had commercialised some of the technology developed at Queen Mary University of London.
IQE CEO Drew Nelson shows His Royal Highness, the Duke of Edinburgh an MOCVD reactor during a visit at the start of the millennium.
To characterise the epiwafers, Nelson and Scott invested in microscopes to assess morphology; X-ray diffraction tools to determine crystallinity; and an electrochemical capacitance-voltage tool, known as a post-office profiler, to determine the doping levels in the epilayers. A home-built photoluminescence kit enabled the evaluation of the optical properties of the epiwafers.
As the facility took shape, Nelson and Scott started to put a team together, while securing their first orders. "I looked after the technology and production side of things, and Mike was more focused on sales," explains Nelson.
Winning the first orders is never easy, particularly if the business is global. For EPI, they needed to target companies in Japan, as many of them were at the forefront of InP optoelectronics. To this end, EPI employed a local agency. This move paid dividends, with good sales obtained through them adding to successes in the US and Europe.
Initially, EPI only produced material for optoelectronic applications "“ principally detectors, modulators and lasers. But it did not take long before the portfolio broadened, first with the addition of InP for microwave systems, and then a family of GaAs products: initially lasers, then HBTs and pHEMTs.
These new products gave the industry a broader choice of suppliers of GaAs epiwafers. EPI now offered an alternative to: the French start-up PicoGiga, which had been offering merchant epi since 1983, and specialised in GaAs pHEMTs for direct broadcast TV; and to Quantum Epitaxial Designs (QED) of Bethlehem, PA, that started producing GaAs pHEMT and MESFET epiwafers in 1989.
EPI grew quite quickly throughout the early 1990s, while broadening its product base. "We ended up getting some pretty big contracts, and companies," remarks Nelson. "We were recognised as the expert company for InP-based materials."
As epiwafer sales blossomed, fortunes for the company's backer, Shell, declined. All the big oil companies that had diversified in the 1980s went through a lean patch, leading them to focus on their core business. This led to a management buy-out of EPI, funded by a bank loan and company cash.
Rising sales continued through the 1990s, and by the end of the decade EPI needed to expand its capacity to fulfil demand. "The route to that was a stock market listing," explains Nelson. "We also wanted to make sure that we were capturing as much of the wireless market that was emerging. So we negotiated a deal to join forces with Pennsylvania based QED."
Floating in the summer of 1999 at $12.50 per share on the EASDAQ, the European version of NASDAQ, the new venture raised $70 million. This provided much needed funds for capital equipment for the Cardiff and Bethlehem facilities.
The new entity needed a new name. To come up with one, management quizzed staff for ideas by running a competition. The winning entry came from putting EPI and QED together, and taking letters three, four and five: IQE.
Nelson says that the merger was one of "roughly equals". However, EPI owned 55 percent of the shares, and with IQE listed in London, it made sense to have the headquarters in Cardiff. Due to this, IQE's core of the management team were those that had led EPI.
At the turn of the millennium, sales were flourishing, with the company continuing its drive to expand its business. It bought UK substrate supplier Wafer Technology, and set up a new facility, IQE Silicon. Situated right next to its Cardiff fab, this arm focused on the growth of silicon and SiGe.
Bursting the bubble
Good times rarely last forever. And they didn't at IQE. Rising revenue had been fuelled by the rapid growth of the fibre optic industry, and when this went into rapid decline "“ associated with the well-documented bursting of the dot.com bubble "“ sales of InP wafers plummeted from around £3 million per month to just £300,000.
"We had to lay off a lot of staff," remarks Nelson. "It's always painful to lay off staff when you have recruited and trained them. But we did everything we needed to survive."
In these tough times, IQE started to lay the foundations for the success that followed. Valuations for all III-V firms had fallen massively from giddy heights, and the time was ripe for further acquisition.
In 2006, IQE acquired the epi business of Emcore; the following year it bought MBE Technologies of Singapore; and in 2012 it acquired the epi business of RFMD.
"We ended up being consolidators of the industry," says Nelson. "That gave us scale, which was critical, and gave us the biggest customers in the industry." These customers were confident in working with IQE, because they knew it would be a long-term deal; and they valued the multi-site manufacturing, as this mitigates risk. From IQE's perspective, more facilities enabled higher volumes, and greater purchasing power with its suppliers.
Further acquisitions and investments have broadened the portfolio. In 2009, the buying of NanoGaN of Bath, UK, added technology for realising high-quality GaN; purchasing Galaxy Semiconductor of Spokane, WA, in 2010, equipped IQE with capability in antimony substrates and infra-red technology; the investment in 2012 in Solar Junction strengthened IQE's expertise multi-junction solar cells; and this year's acquisition of Translucent's technology has provided a capability in crystalline rare earth oxides (cREO).
Together with development and acquisitions of advanced nanoimprint lithography, and a broad portfolio of quasiphotonic crystal patents, IQE has developed a unique and very powerful set of complimentary technologies which will play a major role in the company's future.
All the acquisitions are playing a crucial role in IQE's strategy to evolve from just being an epiwafer foundry to a business that offers a broad range of innovative and in many cases unique materials solutions to its customers.
"Some, like cREO, facilitate putting compound semis onto silicon wafers, which allows us to get into a much larger market place," enthuses Nelson. "You get the technical benefit of the advanced properties of compound semiconductors, and the almost infinite variety of properties you can engineer, with the cost and scale of the silicon industry, where you can manufacture with substrates up to 300 millimetres."
Championing the cluster
The future looks very bright for IQE. But that's not just due to the growth of IQE "“ it is also because the company is sitting at the heart of the world's first compound semiconductor cluster, which Nelson has been instrumental in forming.
Nelson started thinking about this at the start of the decade, as a way to address the weaknesses in the UK's compound semiconductor industry. "In 2011, I approached the economic minister for Wales at the time, to try to persuade them that there needed to be a much stronger infrastructure supporting compound semi. IQE was manufacturing wafers here, but we had virtually no customers in the UK."
IQE joins the FTSE on 19 May 2000. Left to right are Chris Meadows, Investor Relations Manager at IQE, the CEO of the FTSE, IQE CEO Drew Nelson, and Howard Williams, Operations Director.
Illustrating this point is the re-shaping of Nelson's former employer, BT, which made many great contributions to the development and manufacture of fibre-optic networks. "Today British Telecom imports 100 percent of its fibre-optic systems from China," says Nelson. "And ironically, we probably build a significant amount of the InP chips that end up in those systems here in Cardiff."
Nelson's efforts at helping to develop a Compound Semiconductor cluster in South Wales also involved working within a group set up by the European Commissioner for Technology for the Digital Economy. Involved in a team looking at key enabling technologies, Nelson focused on how to rebuild the continent's manufacturing capability in compound semiconductors. His solution: construct a sovereign capability for compound semiconductors in South Wales. "It seemed a very good way to provide a more competitive edge for the UK, and for Europe."
The next step involved lobbying the Welsh Government and Cardiff University to invest in an Institute for Compound Semiconductors based at the University's new innovation campus. Persuading them wasn't easy, but collectively they ended up investing £75 million, which has since leveraged £17 million from the Research Partnership Investment Fund, and spurred the setting up of an EPSRC Manufacturing Hub for Compound Semiconductors, backed by £10 million.
"The vision there is to create an institute which will have capability to go up to 8-inch materials, compound semis on silicon, and to do early stage research across a broad range of materials," explains Nelson. Some of the funding has been used to construct a new building, which could be ready as early as the end of next year. Until they move in, the researchers are working in a cleanroom that has been upgraded for 6-inch processing.
"The big difference now with the approach of the university is that they want to build the cleanrooms and use the tools with industrial discipline," says Nelson. "So rather than just having labs that any student can come in and play with, the equipment is being run on a much more industrial-like and professional basis."
This new approach may assist the efforts of the researchers, according to Nelson. As experiments require a change to one parameter while keeping all the others the same, the greater rigour of all the processes in the cleanroom should make it easy to identify the reason behind a change.
To take the best ideas that come out of the University and provide a pathway to commercialisation, IQE and the University have set up a joint venture, known as the Compound Semiconductor Centre (CSC). With funding from Cardiff University and some equipment from IQE, CSC, which is now in its third year, has more than ten significant collaborative research projects underway.
Another key partner in the cluster is Newport Wafer Fab. This 200 mm silicon facility passed into the hands of Infineon in 2015, when the German powerhouse bought International Rectifier. Infineon decided that it had more global fab capacity than it needed, so it would either sell or close the Newport fab by the end of 2017.
"I ended up leading a private equity buy-out for Newport Wafer Fab," explains Nelson. "The direction of travel for that as part of the compound semi cluster is to transition from 100 percent silicon to building compound semi-on-silicon chips at 200 millimetre." The later could include power and RF devices made from GaN-on-silicon, silicon photonics incorporating III-V devices, and structures that feature an intermediary layer of crystalline rare earth oxides.
Other key players in the cluster include: SPTS, a provider of etching and deposition equipment to the compound semiconductor industry; packaging expert Microsemi; and Swansea University, which has a large nano-health centre, and is setting up a centre for Integrative Semiconductor Materials.
Last but by no means least is the Compound Semiconductor Applications Catapult, an open access R&D facility focused on helping UK businesses exploit advances in compound semiconductor technologies.
IQE's facilities have grown over 30 years, and now include fabs in Greensboro, North Carolina (bottom left) and Singapore (top left). In Cardiff, capacity is increasing with the a new fab being built (bottom right) that will complement the one at St Mellons (top right).
The CS Catapult is moving into a building initially constructed for LG Semicon. "The main fab is now used as what I believe is Europe's largest data centre, and the building next to it is package-andtest, which is highly suited for fitting out as an epi facility."
That is the plan for this building, which is being re-purposed with support from Cardiff City Region. Other cluster partners will share this with IQE, which is setting up a compound semiconductor epifoundry there. "This is going to be, we believe, the biggest in the world for outsourced epi," says Nelson. "It has the capability of housing 100 MOVD tools." The Catapult will be located in a separate part of the building.
Working together, those within the cluster are covering all aspects of production, from wafers to chips, package devices and equipment. "So anyone can interact with the cluster at any point they wish, whether it is for production, for R&D, or for development," say Nelson. With such a hubbub of activity, those wishing to work with the cluster may be unsure who to approach. To address this, a brand name has been set up, CS Connect, which can provide a point of contact for all interested parties.
The impact that the cluster is having is delighting Nelson, who is clearly passionate to see more high-tech manufacturing within the UK: "We've even got examples of fairly significant companies in Asia outsourcing high-tech manufacturing to the Cluster. This is a complete, 180-degree turnaround for the cluster from what you would expect "“ UK companies outsourcing all the hi-tech manufacturing to Asia."
Thirty years on from the launch of his epiwafer company, it is clear that Nelson is not resting on his laurels. He is as enthusiastic as ever to drive success at IQE, but now this mission extends to triumphs for the cluster.