Taking the heat
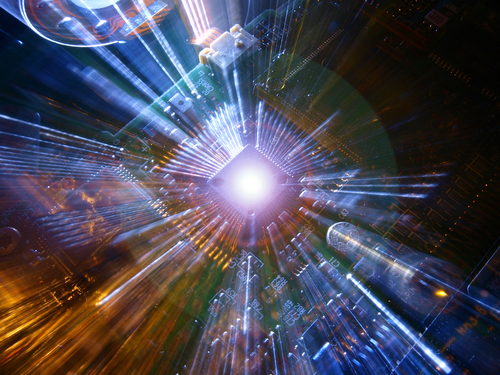
Could a new design of thermally integrated photonic system deliver the massive bandwidths datacommunications crave, asks Compound Semiconductor
Novel intelligent circuits under development by the Tyndall National Institute, Ireland, and partners are set to make photonic devices up to five times more efficient.
Earlier this month the Ireland-based Tyndall National Institute unveiled bold plans for a €5.2 million three-year project to develop high bandwidth, thermally integrated photonics systems.
Funded by the EU and with myriad industry high flyers in tow, including III-V Lab and Alcatel-Lucent Bell Labs, the "Thermally Integrated Smart Photonics Systems" project aims to take the heat off datacomms networks by solving the thermal issues that accompany intense integration in these ICs.
"Data traffic is predicted to grow by up to eighty times come 2020," highlights Kafil Razeeb, leader of nano-interconnection research at the Tyndall National Institute.
"Photonic integrated circuits are used in optical switching but we have found that existing devices incorporate many lasers working at different wavelengths and suffer from huge thermal issues," he adds, "Data is no longer transmitted reliably, and these circuits just aren't fit for purpose anymore."
Kafil Razeeb (left) and colleague emulate the impact of increased internet traffic on a transmitter. Their research will develop an intelligent circuit that can regulate its own temperature making it up to 5 times more efficient.
From a thermal perspective, silicon photonics - in which III-V photonics devices are integrated on a silicon-on-insulator substrate - can be a nightmare. As part of any package, the temperature of the lasers must be kept within ±0.1°C of operating temperature to maintain emission wavelengths and ensure reliable transmission of data. And herein lies a list of problems.
For starters, removing heat from a junction-side-up architecture is difficult, and to make matters worse, the oxide isolation layer on SOI wafers separates the device from its heatsink.
In addition, ridge-like wave guides raise thermal spreading resistance and the temperature control demands of photonic and electronic devices are incredibly different.
To tackle these issues and keep lasers transmitting data smoothly, today's state-of-the-art devices use several thermal control devices. A large solid-state macro-thermoelectric cooler sits on the backside of the chip to cool the lasers.
Meanwhile many intermediary thermal spreaders connect the massive heat load to the photonics package, which is also air-cooled by an external heat sink.
But with all the excessive heat sucked away by these devices, resistive heating elements are then placed aside each laser to fine-tune its temperature for data transmission.
Clearly this counter-intuitive arrangement is complex, expensive, and worse still restricts further components integration; bad news for tomorrow's extravagant bandwidths.
As Razeeb puts it: "You are cooling down the whole system just to heat it up again, which from an energy point of view is very inefficient. So we have said, this is 'old style', let's do something different."
Which is where the latest Tyndall-led project comes in. Building on a wealth of integrated photonics research carried out by Tyndall, Bell Labs' III-V research arm and other partners, Razeeb and colleagues intend to remove the large-footprint macro-thermoelectric and individual resistive heaters from a photonic integrated circuit (PIC), and integrate miniature versions to the SOI substrate.
Microthermoelecric coolers will be integrated around each laser, and microchannels will also be etched into the wafer, carrying fluid to cool the hot side of the microthermoelectric coolers and other chip level components.
Micropumps and valves will also be integrated into the package to pump and regulate fluid flow around the microchannels.
An enhanced thermal spreader - possibly fabricated from AlN - could also replace the poorly thermal conducting polymer currently used as waveguide cladding in today's hybrid laser designs.
"The microchannels will be part of the wafer, and the thermoelectrics, heatsink and lasers will all be integrated onto the wafer, rather than say, using different components coming from different vendors," says Razeeb. "Right now we see the micropump sitting in the vicinity of this, but we do have a vision to integrate it to the wafer as part of the back-end process."
Crucially, as Razeeb adds: "The whole system will work autonomously, so a small programme will control the temperature of your individual laser and automatically maintain it's operating temperature."
Under test
So what will the project achieve in the next three years? According to Razeeb, the TIPS team intend to deploy a demonstrator before project-end.
"Alcatel-Lucent, France, will test the system and compare this with the existing state of the art [InP-based] system," he says. "This will tell us how far we are from the product line, which of course is the acid test for anything."
The intentions are bold, but clearly many barriers lie ahead. The integration of microthermoelectrics and integration of microfluidics will be breaking new ground. Design rules need to be formulated while device fabrication must be developed. And, for example, thermoelectric material and electrical contact processing should be optimised for maximum performance.
But Razeeb isn't fazed. "Yes there are lots of issues but we are materials scientists and we have been working on these since 2005."
"Project partners have already developed these materials on different substrates," he adds. "And in the wake of Internet of Things, we've discovered that this is a nice solution to what the world needs."