LEDs: beyond the chip
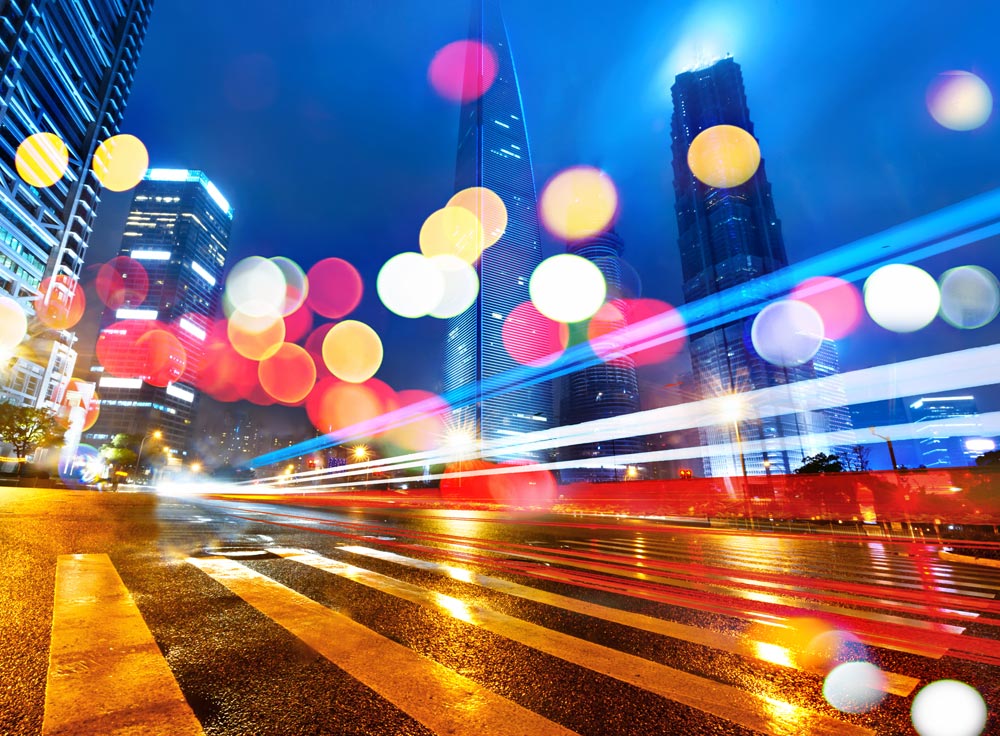
SemiLEDs talks to Compound Semiconductor about flip-chip packages, high power lighting and success during tough times.
Delivering vertical architecture LEDs, and now devices in chip-scale and enhanced flip-chip packages, SemiLEDs hopes to make life easier for today's lighting designers.
Perhaps best known for its highly successful, vertical architecture, high power LEDs, SemiLEDs, Taiwan, recently joined the growing pack of LED manufacturers to offer flip chip devices.
The company's recent line of white LEDs in enhanced flip-chip, chip-scale packages are based on a horizontal chip structure, and have been developed to capture a greater portion of the ever-growing lighting market.
As part of the flip-chip construction, the chip's electrical contacts are moved to the bottom of the chip, eliminating the need to run failure-prone bonding wires from the top of the chip to the package.
As a result, the chip is more robust, fully compatible with surface mount processes and can be very closely mounted to other chips, opening the door to densely packed LED arrays for higher Lumen density applications.
"We've spent a lot of time developing our chip-scale packaging," highlights SemiLEDs' executive vice president of operations, Mark Tuttle. "Our flip chip was originally developed as a standalone version, but has been predominantly used in a chip-scale packaging formula and in terms of chip-scale packaging, we have a very small package."
While common surface mount device (SMD) LEDs come in at 3.5 mm by 3.5 mm, the chip-scale package dimensions are only 1.4mm by 1.4 mm. And as Tuttle is keen to highlight, the emitters in its package have already been phosphor-coated, using its 'Ready White' proprietary coating process.
Crucially, for the lighting manufacturer, this step removes the need to apply phosphor at the package-level, a complex and time-consuming process.
"There's a lot of technology in phosphor and companies just don't want to invest and maintain this if they don't have to, so this shortens design time and time-to-market [for these manufacturers]," he says.
"So, with the chip-scale package and phosphor intact, they are already buying the correlated colour temperature and colour index that they need for a given application," he adds.
So with potential space savings and cost savings, SemiLEDs chip-scale packaged LEDs clearly offer new options to time-constrained lighting designers after more for their money, be it more Lumens per dollar, or even more Lumens per unit area.
As Tuttle's colleague and sales manager at SemiLEDs, Frank Wu, points out: "Right now, many in the industry are working at a systems level, so when you can pack LEDs closer together, you reduce the amount of material you need at the fixture or module level, reducing total cost of ownership here."
"We've seen key players in the market talk about Lumen per Watt, then Lumen per dollar and now we're seeing Lumen per unit area," he adds. "This is something we're very much working towards increasing."
Vertical designs
But what of SemiLEDs well-established vertical LEDs? In Tuttle's words, while the flip chip LEDs have, 'been a very different project', its focus is also firmly on a growing fleet of vertical LEDs.
Earlier this year, the company introduced its phosphor-converted LED chip series, a range of LED chips coated with the 'ReadyWhite' phosphor to emit red, green and amber light.
The LEDs join a family of white phosphor-coated LEDs, and in each, the vertical structure consists of a GaN layer coated with a mirror and then copper alloy, which acts as an anode, reflector and thermal conductor
Crucially, ditching the typical sapphire substrate for a copper alloy base boosts heat dissipation through the chip and out of the heat sink while the vertical architecture enables a vertical current path to prevent current crowding. The end result is a high power LED with high efficacy and long lifetime.
"If you want the highest power output and to deliver the highest current in, and also get rid of the heat, then the vertical structure is still the best," highlights Tuttle. "Even though we now offer chip-scale packaging, the power is higher in the vertical architecture, it really is king of the hill."
But while SemiLEDs set out to develop its high power LEDs for general lighting markets, its choice of applications has changed.
"We've been producing high power LEDs from the beginning but the general lighting has gone in a different direction, demanding lower power, and at most, medium power LEDs," says Tuttle. "So when the general lighting market moved away from high power, then of course it moved away from us as well. We've been focusing on other markets for many years now."
One up and coming application is high-bay illumination - be it in a warehouse or stadium - where high power lighting with a focus is key. Agricultural settings, from dairy barns to storage facilities, are also beginning to demand LED high-bay lighting systems.
But without a doubt UV LED applications are very critical to SemiLEDs right now. The company has already delivered LEDs for the industrial curing of adhesives and coatings, and is developing shorter wavelength LEDs for purification applications.
Crucially the relatively low adoption of UV LEDs in industrial settings has been attributed to system integration issues, but SemiLEDs is hoping to change this. In recent years the company has moved from simply being a chip developer to manufacturing modules, and is now looking to provide ODM/OEM services to produce entire systems.
As Wu highlights: "When we started out with just chips, we had a lot of customers asking for an optmised package, so along the way we acquired companies to do packaging for us. Now we have people asking us to build an entire lamp."
Indeed, as Tuttle emphases, simply being a chip developer isn't a strategy for success any more. "The margins are just too small with chips, even custom chips," he says.
So what is? "We started with the LED and built on that," says Tuttle. "Our vertical structure had proven itself all the way through and is still the architecture of choice for high power."
"But in recent years, we have been looking more into modules as well as systems integration, so we're not just reliant on the fundamental core of the LED," he adds. "Like many other companies, we have known that you need to get away from the chip on its own and be involved with the whole integrated system."