Putting CPV on Rooftops
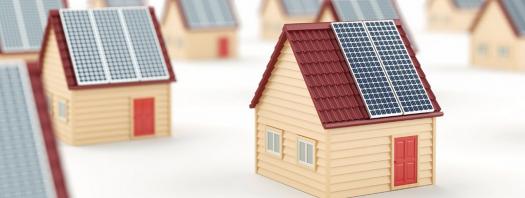
High-efficiency CPV could become a reality for rooftops by uniting microscale solar cells with a planar microtracking concentrator technology
BY JARED PRICE AND CHRIS GIEBINK FROM THE PENNSYLVANIA STATE UNIVERSITY AND XING SHENG AND JOHN ROGERS FROM THE UNIVERSITY OF ILLINOIS AT URBANA-CHAMPAIGN
PROSPECTS for concentrating photovoltaics (CPV) are at an all-time high. Driven by a maturing industry and increasing emphasis on the value of high efficiency, the global installed capacity of CPV is forecast to triple to 1 GW over the next five years.
None of this capacity, however, will be installed on rooftops, which is where a significant proportion of solar panels are being deployed by the broader PV industry. Amidst this growing trend toward decentralized power generation, the conspicuous absence of rooftop CPV begs the question: Is CPV missing an opportunity?
Creating a viable CPV technology for rooftops is not trivial because it requires overcoming both practical and aesthetic challenges. While standard PV panels are compact and can mount flush with the roof, CPV modules are traditionally bulky, requiring a precision tracking system to orient each module toward the sun throughout the day. These aspects are not problematic for ground-mounted systems where there is ample space to move and prevent shading. But on rooftops they are a non-starter: Space and structural support are limited, and there is a need to preserve aesthetic appeal, because few of us would want to have the equivalent of an array of mini satellite television dishes scattered across our roof.
A radically different CPV architecture is therefore needed, which must deliver the efficiency of a traditional system, but do so in the form factor of standard, fixed-panel PV.
Our team at Penn State University and the University of Illinois at Urbana-Champaign is making progress on this front by combining a translation-based tracking technology with microscale photovoltaic cells embedded inside the concentrator optic itself. The result is a quasi-static CPV panel less than 1 cm-thick that operates at fixed tilt with an imperceptible amount of movement. Over the course of a sunny day, such a panel could deliver 50 percent more energy than a state-of-the-art silicon equivalent.
Embedded microtracking
To accomplish solar tracking without reorienting the panel, we have adopted a planar translation-based approach, with optics that remain fixed while PV cells slide laterally to follow the moving focal spot (see Figure 1).
Figure 1. Moving the cells relative to the lens ensures that sunlight is concentrated on the device throughout the day.
This type of design is not a new idea. The performance of various forms of translational tracking have been explored before, but their utility has been limited by image field curvature, which degrades the focal spot in the solar cell plane for light incident at oblique angles beyond about 20°. This is a substantial drawback, because a latitude-tilted panel sees sunlight incident at angles of up to 60° over the course of 8 hours. Consequently, previous translational tracking schemes could only operate efficiently for a few hours each day.
We resolved this problem by adopting a folded optical path. With this configuration, light is refracted by a top lenslet, reflected by a bottom lenslet and finally focused on an intermediate plane − a sheet of glass patterned with a corresponding array of solar cells. The interfaces between this plane and those of the top and bottom lenslet arrays are lubricated by optical oil, which also serves to eliminate parasitic reflections.
Tracking is achieved by sliding the middle solar cell sheet laterally. Sunlight is focussed on cells that have an area of less than 1 mm2, enabling the size of the associated lenslets and the thickness of the overall concentrator stack to be kept small. By employing this design, cells are embedded in a "˜microtracking' panel that can accept light over a 120° full field of view, which corresponds to operation for more than 8 hours per day. Incoming radiation is focused by a factor of more than 200, and daily average optical losses are kept below 15 percent.
Figure 2. The transfer-printing process that is used to produce microcell arrays has a very high throughput

Microscale cells
The benefits of the microcells are more than just enabling a compact panel. Thanks to their small size, the power delivered to each of these cells is orders-of-magnitude lower than that impinging on a conventional CPV cell, which is typically around 1 cm2 in size. This simplifies thermal management to such an extent that, according to our work and that of others, the cell does not require active cooling.
Another advantage of working with microcells is that they have a lower series resistive loss. This leads to a more robust performance when the cell faces the inherent illumination non-uniformity of the microtracking concentrator focal spot.
Our fabrication of the microcell sheet begins with the growth of the device structure on a GaAs substrate by MOCVD. Inserted between the device stack and the substrate is a lattice-matched AlGaAs sacrificial layer, which is removed by wet etching to separate the cells from the substrate.
The resulting chips, which are only a few micrometers thick, are picked up with a soft elastomeric stamp and placed precisely on a glass (sliding middle sheet) substrate with a high-throughput process, known as micro-transfer printing. This process can print millions of cells per hour with a yield exceeding 99.5 percent while producing micrometre-scale placement accuracy (see Figure 2). Following transfer of the cells, metal interconnects are deposited to create a network that optimizes the power produced by the module.
We evaluated our microtracking design by fabricating a small-scale prototype incorporating seven, series-connected GaAs microcells. These were sandwiched between a pair of custom, 3D-printed, plastic lenslet arrays made by our collaborators at LUXeXcel, Inc.
Figure 3. Outdoor testing of a small-scale prototype using three-dimensional-printed lenslet arrays.

Testing involved measurements in the lab, and then outdoors during several sunny days in central Pennsylvania, where the panels were held at a fixed tilt (see Figure 3). Despite a relatively large surface-form-error in the printed lenslets, for over 6 hours we could maintain a factor of 100-150 increase in the short-circuit current compared to that of an adjacent bare cell. Turning to commercial off-the-shelf planoconvex glass lenses improved the concentration factor to 200 suns and extended the operating time to 8 hours.
Taken together, these initial results have validated the basic microtracking concept and set the stage for testing at a larger scale. When this is carried out, we will improve the concentrator performance by optimizing the lenslet optics for higher concentration and by applying an anti-reflection coating to improve their optical efficiency.
To higher efficiencies
In addition to improving the optical performance of our concentrator system, we are also pursuing ultra-high efficiency cells by moving to quadruple junction, four-terminal devices. By transfer-printing different sub-cells on top of one another, we avoid the current- and lattice-matching issues that have challenged monolithic four-junction cells to date. This approach expands the range of feasible sub-cell materials and opens up the possibility of increasing the number of junctions to five or more.
We have used transfer printing to combine a InGaP/GaAs/InGaAsNSb top cell with a germanium bottom cell. The resulting four-junction photovoltaic delivers a total efficiency of
44 percent at 1000 suns (see Figure 4). Extrapolating our concentrator performance together with these high efficiency cells suggests that a microtracking CPV panel could deliver
50 percent more energy over the course of a sunny day than a state-of-the-art silicon module of equivalent size.
Delivering high-performance is no guarantee of success for rooftop CPV − modules will also have to deliver long-term operational reliability, while retailing for a price that makes them competitive with existing PV panels. It is likely that the key to reliability will be environmentally-robust plastic or glass lenslet arrays, since all the cells, moving interfaces and lubricating oil are sealed and protected within the concentrator stack. Making meaningful cost projections at such an early development stage is tricky, but the combination of wafer recycling, high-throughput transfer printing and inexpensive injection-moulded optics indicates that the ingredients are there for a low-cost system.
It is important to emphasize that microtracking CPV complements − rather than competes with − conventional CPV. The latter is ideal in applications where space and movement are not constrained, while our microtracking approach opens up an opportunity to deliver a step-change in the efficiency in constrained-space rooftop and urban installations. This expands the number of markets that CPV can serve, and we hope that it will accelerate the broader adoption of this technology.
Figure 4. A mechanical assembly approach can create four-junction microcells that deliver a higher efficiency than their triple-junction predecessors at a range of concentrations.