Ascatron: hefty funds for high voltage diodes
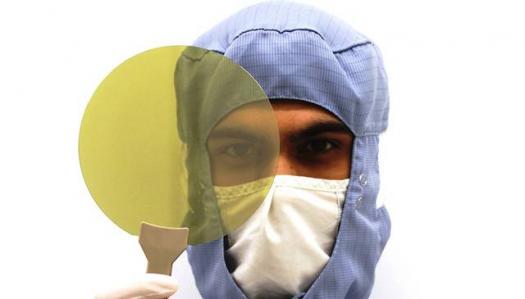
Following €4m investment, SiC player, Ascatron, aims to deliver very high voltage diodes to market in a year. Chief executive, Christian Vieider, reveals plans.
Ascatron is heading for high voltage markets with its epitaxy expertise [Ascatron].
Just last month, Sweden-based SiC power semiconductor developer, Ascatron, revealed it had raised a hefty €4 million in financing from investors in Italy and China, as well as reactor supplier, LPE, Italy.
Now intending to complete development of its initial SiC devices - the first of which will be a high voltage SiC diode - the company will split funds between materials production and product development.
As Ascatron chief technology officer, Adolf Schöner, said at the time: "Forty percent of the market for power electronic components is in China and we see a lot of interest in SiC for energy saving."
"We've already started to implement our advanced material technology in production equipment for SiC epitaxy," he adds. "The next step is to optimise device design and outsource the remaining manufacture of the chip to a foundry with capacity for volume production."
Burying issues
From the late 1990s, researchers at Swedish research institute, Acreo, had been developing SiC epitaxy, spinning out Ascatron in 2011. During this time, Acreo had offered SiC epitaxy as a service, providing multi-layer structures and re-growth on non-planar surfaces.
At the same time, development of SiC device concepts, including a normally-off SiC JFET rated to 1.2 kV and 50 A, was well underway. And collaborations with HOYA, Japan, had led to a 3C-SiC process for power MOSFETs.
Fast-forward to today and progress has clearly continued. Ascatron has developed myriad processes for manufacturing SiC semiconductors for power electronics, including substrate buffers, SiC epitaxy, deep trench etching and more.
At the heart of these breakthroughs lies so-called 3DSiC technology, based on embedded epitaxial growth methods that replace the conventional process of doping with ion implantation during SiC device fabrication.
When fabricating SiC devices, doping via ion implantation can bring problems. Ion diffusion is slow, preventing healing of defects, and inhibiting current density and high voltage performance. And in a separate issue, electric fields at Schottky contacts and MOS interfaces also stymy device performance.
To side-step these issues, Ascatron epitaxially grows doped material within etched 3D structures, such as trenches, producing high performance, high voltage SiC devices.
For example, when fabricating a Schottky diode, a p-type grid is first fabricated on the substrate surface, via trench etching.
Epitaxial re-growth and planarisation is then applied to fill up the trenches with p-type material. And, in a final step, the grid is buried by another re-growth step of a thin n-layer.
Crucially electric fields at field-sensitive areas of the device are reduced, high electric fields are shifted into the SiC bulk and ion doping implantation damage simply doesn't exist.
As Ascatron's managing director, Christian Vieider says: "We've been working on this technology to make very efficient doping structures which replace ion implantation with epitaxy."
"Losses are much lower in our devices and we can design [structures] to handle very high voltages in an efficient way," he adds.
So with the process honed and cash in hand, Ascatron is currently working with pilot customers and intends to deliver its first device - a high voltage buried grid SiC Schottky diode for industrial process markets - in a year.
"We're targeting high voltage applications - 10 kV devices - for industrial processing as we see some specific needs that we think we can fulfill," says Vieider. "We've identified that IGBT [modules] are available up to 6.5 kV, but above this there are no real switching power devices, so we think this is a good place to start our product range."
But how exactly will Ascatron compete with the likes of Infineon, Cree, ST Microelectronics and Rohm? Vieider reckons his company's technology can provide advantages at the higher voltages that competitors' devices haven't yet reached.
"We already have a customer that is looking for high voltage devices, but just can't find a device," he adds. "Silicon devices can be coupled together in series perhaps, but right now there is really nothing on the market, so this is where we are starting."
And with higher voltage devices in place, the company will then look to broadening applications to lower voltages. Indeed, Ascatron recently bought shares in Italy-based start-up, PileGrowth Technology, to develop MOSFETs based on cubic SiC grown on silicon.
The move could open up markets for 300V to 600 V applications and also allow Ascatron to compete with rival technologies including GaN-on-silicon.
"We had a choice and could have targeted lower voltages from the beginning but there are already competitors in this market," says Vieider. "So once our technology has been adopted at the higher voltages, then we will move to lower voltage applications."
To kick-start its journey to commercial devices, the company recently bought a single-wafer, six inch production reactor system, manufactured by investor LPE. Past development has centred around several reactor systems, including two, prototype, four inch Aixtron hot-wall CVD reactors, initally pioneered by Sweden-based SiC CVD reactor supplier, Epigress.
According to Vieider, the systems were flexible and produced good material quality, but turnaround times weren't fast enough, so a production upgrade was critical. "We're now ready to scale up our fabrication processes for production," he says. "Our latest reactor has load lock, a good turnaround time and very short cooling times"
"We need to do very thick epitaxy - from 0.1 micron to 100 micron - and have an epitaxy process for advanced grid doping," he adds. "This system produces [structures] with good doping, uniformity and performance."
Past company plans had included the purchase of a multi-wafer reactor system, but Vieider reckons his team will get better material quality with a single wafer system. "In principle you can buy three single wafer reactors for one multi-wafer reactor," he explains. "So, as our needs arise we can add more reactors to production."
The company currently buys in substrates from commercial suppliers, and going forward, will keep fundamental epitaxy processes in-house while outsourcing remaining production to a commercial foundry.
"In two years we will have a product on the market and will target more and more applications from higher to lower voltages, addressing broader and broader markets," says Vieider. "Beyond this, our target is to be a supplier of SiC power devices for broad applications."