Technical Insight
Mist Epitaxy: The key to a great gallium oxide power device
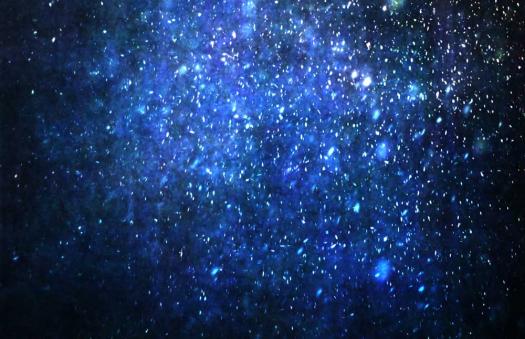
Growing gallium oxide on sapphire can fulfil the promise of cheap, efficient, high-voltage power devices
BY MASAYA ODA, TOSHIMI HITORA AND NAONORI KUROKAWA FROM FLOSFIA





In power conversion systems, the key components for transferring electricity between its AC and DC forms and changing its voltage and frequency are the power transistor and the diode. For this pair of semiconductor devices, silicon dominates, generating sales of more than $20 billion per annum.
Yet despite this success, these silicon power devices are far from perfect. When deployed in power systems, 10 percent of electrical energy can be wasted as heat − and addressing this weakness is not easy, because silicon devices are approaching their theoretical limit.
Moving to higher efficiencies requires the radical step of building devices with new materials with a higher bandgap. This move, which also unleashes higher operating voltages, has already delivered some success. GaN and SiC transistors and diodes are now on the market, with sales on the rise. However, the gains in performance that they are delivering go hand-in-hand with higher prices, and this is hampering a substantial increase in shipments of these wide bandgap power electronic products.
Another class of materials that has been attracting attention from the electronics industry is the ceramic oxides. Thin-film transistors made from InGaZnO are already being used in flat panel displays, where they offer low power consumption; and single crystals of LiTaO3 and LiNbO3 are being used as piezoelectric materials in surface acoustic wave devices, where they form filters in smart phones. There is also Ga2O3, a very promising material for power devices, thanks to its ultra-high bandgap of 5 eV.
This really high bandgap "“ it dwarfs those of SiC and GaN, which are 3.3 eV and 3.4 eV, respectively "“ is a tremendous virtue for any power device. It is not just that a wider band gap can withstand a stronger electric field, and ultimately enable a thinner device for a given operating voltage; it is also that a thinner device has a lower resistance, and thus a better conversion efficiency.
Another attractive feature of the Ga2O3 power device is that it can address the cost concerns that plague its SiC and GaN cousins. Very strong electric fields can be accommodated by this oxide, enabling a step-change in current density for a given footprint. So, for a given operating current, the footprint of a Ga2O3 power device can be substantially smaller than an equivalent made from SiC or GaN "“ and far, far smaller than a silicon variant. Thanks to this, Ga2O3 diodes and transistors have the potential to be cost-competitive with silicon incumbents, while delivering much higher performance.

Figure 1. Flosfia's proprietary mist epitaxy technology, using a corundum-structured sapphire substrate, enables the growth of a high-quality, corundum-structured monocrystalline film of α-Ga2O3. Process steps that follow, which lead to the production of a Schottky barrier diode, include the removal of the insulating sapphire substrate.
An alternative way to view the extent of the superiority of Ga2O3 over other semiconductor materials is to consider Baliga's figure-of-merit (see Table 1). The on-resistance of a Ga2O3 device is more than 3000 times lower than that of a silicon equivalent, and one-tenth of that made from SiC. The Ga2O3 device can also be smaller, with values for resistance suggesting a footprint that can be one-seventh of SiC.
An alternative way to view the extent of the superiority of Ga2O3 over other semiconductor materials is to consider Baliga's figure-of-merit (see Table 1). The on-resistance of a Ga2O3 device is more than 3000 times lower than that of a silicon equivalent, and one-tenth of that made from SiC. The Ga2O3 device can also be smaller, with values for resistance suggesting a footprint that can be one-seventh of SiC.
One of the pioneers of Ga2O3 power devices is the National Institute of Information and Communication Technology (NICT), Japan. It has produced Schottky barrier diodes and MESFETs using the oxide's β-phase (this is one of five phases, the others being α, γ, δ and ε). By fabricating these devices, NICT is helping to transform the potential of Ga2O3 power devices into a reality.
Another promising phase of this material is the corundum form, α-Ga2O3. It is this variant that we are using at Flosfia, a start-up in Kyoto that is collaborating with a team at Kyoto University lead by Shizuo Fujita and Kentaro Kaneko.

Figure 2. The turn-on voltage of Flosfia's α-Ga2O3 Schottky barrier diode is a little higher than that of an equivalent made from SiC. Lower values should result from an optimised contact.
Sapphire: A fine foundation
We begin device production by growing a-Ga2O3 epilayers on sapphire with a novel deposition process known as mist epitaxy, which has been developed by ourselves and by the team at Kyoto University. Although sapphire is an unusual choice of substrate "“ many researchers prefer Ga2O3 "“ there is much to recommend it. First, α-Ga2O3 and sapphire share a trigonal (hexagonal) corundum crystal structure, and thanks to a lattice mismatch of just 3-5 percent, it is possible to form epilayers that combine excellent crystal material with an absence of fatal dislocations. In addition, due to sapphire's widespread use in the LED industry, it is affordable, well developed, and available in a variety of diameters, including 4-inch and 6-inch. Attractive pricing is very important, because it helps our devices to realise cost parity with those made from silicon.
Unfortunately, sapphire fails to excel in all areas. Its greatest weakness, when it comes to providing a platform for the α-Ga2O3 power device, is its poor thermal conductivity. That flaw can cause devices to deteriorate and even malfunction. To address this critical weakness, we have developed a proprietary technology that allows the α-Ga2O3 power device to be lifted off of the sapphire substrate and transferred to a metal support with good thermal conductivity (see Figure 1 for details of our manufacturing process). This improves thermal management, increasing heat extraction from the device, so that the chip can run at a lower temperature. What's more, by adopting this approach, it is possible to avoid the high series resistance that plagues SiC and GaN power devices that are compromised by their thick native substrates.
Along with the use of sapphire, the other key to our realisation of cost-competitive, high-performance Ga2O3 power devices is our proprietary growth technology, mist epitaxy. This novel deposition technology, developed by Fujita and co-workers at Kyoto University at first, involves a carbon-free gallium halide source. It is in the form of a water and/or alcohol solution.
Prior to deposition, this gallium halide source "“ it could be gallium chloride, gallium bromide, or gallium iodide "“ is atomised by ultrasound to form a mist. A carrier gas sweep this into a reaction chamber, which contains a heated sapphire substrate. Here, the constituents of the mist, particles with diameters of typically several microns, undergo a pyrolytic reaction with an oxygen source. This may be water, alcohol, or oxygen gas.
A merit of this process is that it takes place under atmospheric pressure. This eliminates the need for expense monolithic vacuum systems, thereby reducing equipment costs and slashing process times. Such gains are enviable, because they are impossible to realise for semiconductor crystal growth under a high vacuum. The idea of growing semiconductor crystals under atmospheric pressure, particularly in the presence of water, is incredibly counter intuitive. It raises concerns over impurities and crystal quality. However, we have shown that these concerns are addressed by fine-tuning the process. For example, the residual impurity concentrations are beyond the lower detection limit of secondary ion mass spectroscopy (SIMS), while the X-ray rocking measurements of a film of α-Ga2O3 deposited on 4-inch sapphire produce a peak for the (0006) plane with a full-width-at-half-maximum of less than 50 arcsec. Morphology is also excellent, with atomic force microscopy revealing a one-monolayer step and an atomically flat terrace on the surface of this oxide.

Table 1 Material properties of various semiconductors highlight the superiority of Ga2O3 over SiC, GaN and silicon.
The production process
Production of these diodes begins with the growth of a thin film of α-Ga2O3 on sapphire (see Figure 1). We use our proprietary lift-off technique to separate this film, which had a thickness of less than 20 μm, from the sapphire substrate. After transferring this free-standing film to a metal support, we complete the fabrication of a vertical α-Ga2O3 Schottky barrier diode with the likes of etching and metallization.
The current-voltage characteristics of our diodes compare favourably with commercial equivalents made from other materials (see Figure 2). Although the turn on voltage of 1.5"“1.6 V is slightly larger than equivalents made from both β-Ga2O3 and SiC, lower values should be possible by optimising the contact metals.
Our devices excel in their on-resistance, with values ranging from 0.1 mΩ·cm2 to 0.4 mΩ·cm2. SiC, in comparison, has a typical value of 0.7 mΩ·cm2. Thanks to an on-resistance that can be as low as one-seventh of that of SiC, there is a promise of a reduction in footprint by a similar factor, enabling cost-parity with the silicon Schottky barrier diode.
Despite a lack of passivation, our pair of α-Ga2O3 Schottky barrier diodes produces impressive breakdown voltages of 500 V and 855 V (see Figure 4 for a benchmarking of the performance of our devices and those made from SiC, along with the theoretical limits for various materials). These values, when considered in tandem with the on-resistance, are very encouraging. Compared to a commercial SiC diode, one of our devices has a superior on-resistance and breakdown voltage and the other device is even more impressive: it has an on-resistance and break down voltage that surpasses the limit of what is possible with SiC. All these results stem from the combination of the ultra-high bandgap of α-Ga2O3 and an architecture that is made possible by our lift-off approach.

Figure 3. Flosfia's α-Ga2O3 Schottky barrier diode has an on-resistance that is one-seventh that of SiC. That's a significant advantage, because there is the promise of a reduction in footprint by a similar factor, enabling cost parity with the silicon Schottky barrier diode.
Our work has shown that it is possible to tackle the Achilles heal of the Ga2O3 power device "“ its low thermal conductivity "“ and target cost-parity with silicon, thanks to a footprint that can be one-seventh that of SiC. Our next steps on the road to commercialisation are to increase the breakdown voltage and the stability of our device by improving the metal contact and introducing a passivation technology. We plan to sample α-Ga2O3 Schottky barrier diodes in a standard power package later this year, and then increase our portfolio, by developing and launching power transistors.

Figure 4. Flosfia's best device delivers a performance that is not only superior to a commercial SiC device, but also better than its theoretical limit. The unipolar limit is set by the physical properties of the material, and by a limit that is related to the resistance of the base material (substrate, film). Flosfia's prototyped SBD1 realized the world's smallest on-resistance of 0.1 mΩ·cm2. The breakdown voltage exceeded 531 V, while the SBD2 realised an even higher breakdown voltage of 855 V. Note that: (1) It is assumed that electron mobility is 300 cm2/Vs, breakdown voltage is 8 MV/cm, and relative permittivity is 10; (2), the film thickness is 20 μm, and resistivity is assumed from measured values of mobility and carrier concentration; and (3), it is assumed that resistivity of the SiC wafer decreases by half by being thinned.