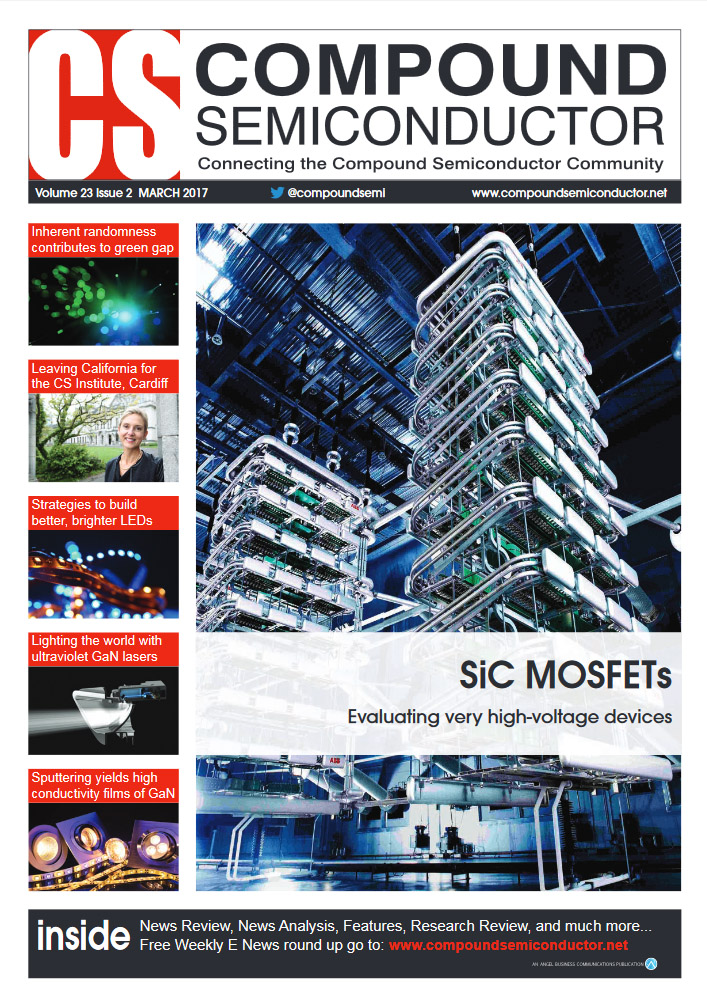
Strategies for better brighter LEDs
Diminishing droop and enhancing extraction efficiency help to build better, brighter LEDs
BY ASHISH TANDON, TONI LOPEZ, OLEG SHCHEKIN, ISAAC WILDESON, PARIJAT DEB, HENRY CHOY AND JY BHARDWAJ FROM LUMILEDS
The LED is a highly versatile device which has transformed solid state lighting in the last decade. This device is best known for its high efficiency and long lifetime, which have helped to drive its adoption in general lighting. The efficiency has continued to improve at an astounding pace, which is resulting in accelerated adoption as well as reducing cost, by not only reducing the LED count for a given application, but also reducing hardware system costs, by allowing the use of smaller heat sinks and direct attachment to board. This efficiency gain also allows high luminance die shrink that enables a new class of applications based on densely packed arrays to create an addressable matrix that is well-suited for automotive headlight dynamic beam steering. The inherent high speed switching of InGaN LEDs makes them ideal for visible light communications or LiFi, which can be dual function alongside lighting.
Figure 1: (a) Breakdown of efficacy components for typical cool white, warm white phosphor-converted high power illumination LEDs at J = 350 mA/mm2 and Tj = 85 °C, as well as for a typical high power automotive front-lighting LED at J = 1000 mA/mm2 and Tj = 100 °C; (b) a typical high power general illumination LED; (c) a typical high power automotive lighting LED. With these products, the package is constructed for efficient dissipation of heat and extraction of light. To ensure this, the phosphor is positioned in proximity to the emitting surfaces of the pump LED chip, with the latter placed on a ceramic sub-mount and encapsulated in a silicone dome. Note that high power automotive LEDs are designed with emphasis on source brightness. Such LEDs feature pump chips with high extraction efficiency, ceramic sub-mount and proximity phosphor, but forgo using domes to keep source étendue small at the expense of package efficiency.
The wide penetration of LEDs into various markets has been enabled by massive strides in blue LED wall-plug efficiency, white conversion efficiency and the ability to precisely tailor and control the colour point. In this article, our team from Lumileds, San Jose, CA, discusses the technology breakdown for LEDs and compares different architectures, thus highlighting opportunities for future improvements. In the following sections we cover various aspects: White LED efficiency breakdown pareto "“ typical losses (ranges); epitaxial considerations for high-power LED multi-layer stacks "“ internal quantum efficiency versus droop trade-off, polar versus semi-polar versus non-polar GaN; carrier spreading and light extraction in devices "“ patterned substrates; die architecture comparison; photo-thermal quenching of phosphors; and we conclude with some ideas for next-generation LEDs.
Excelling in efficacy
The luminous efficacy of an LED "“ essentially a measure of efficiency, evaluated in terms of the response of the human eye "“ is commonly represented by the product of four factors: the internal quantum efficiency of carrier recombination in the active region; the extraction efficiency of photons in the blue LED; the electrical efficiency of the injection of carriers into the active region; and the efficiency of converting blue photons into the desired LED spectrum. In Figure 1, typical values for all these efficiencies are given for two classes of LED, a typical InGaN-based device for high-power illumination and an automotive LED. Note that in this figure the conversion efficiency is sub-divided into: the package efficiency; the Stokes shift penalty, which is referred to as the quantum deficit; the luminous equivalent of the emission spectrum; and the quantum efficiency of down conversion by phosphors.
A quick glance at that breakdown reveals that the internal quantum efficiency of the multi-layer epi stack offers the greatest potential for improvement. Addressing this is not trivial, because it involves combatting droop within the active region. Next on the list are the extraction efficiencies out of the pump chip and the package.
In some instances, an area of concern is the quantum efficiency of the down-conversion of blue light by the phosphor materials. This can be very high, but may decline at high drive currents, due to photo-thermal quenching. The loss can be a significant impediment in devices designed to have a high colour rendering or warm colour temperatures, because they require red nitride phosphors that quench more easily.
Figure 2. One-dimensional device simulations of LED active regions with different carrier distributions and material quality (a), and corresponding internal quantum efficiency (IQE) curves (b). The different scenarios of carrier spreading and material quality are achieved by adjusting the input heterostructure design and non-radiative recombination lifetimes, respectively, into the simulation. Moving from a poor carrier spreading structure (red lines) to an improved carrier spreading structure, but with poorer material quality (black dashed lines), provides gain at only very high current densities. In comparison, an improved carrier spreading structure with no material quality degradation (green lines) offers significant high current gains over the poor carrier spreading baseline.
Combatting droop
As LED luminance requirements rise, operating current densities are increasing, with traditional values of typically 35 A cm-2 extending to 100 A cm-2 or more. This change has a profound impact on epitaxy, as the focus for increasing the internal quantum efficiency at 100 A cm-2 differs significantly from that at current densities of 10-20 A cm-2.
At the lower current densities, increases in internal quantum efficiency come from material quality improvements. That's because Shockley-Read-Hall recombination dominates at low current.
In stark contrast, when LEDs are driven harder, the focus has to be directed at combatting droop, which is the reduction in internal quantum efficiency with increasing current density. Today, there is widespread support for Auger recombination as the dominant cause of droop in state of the art industry devices [2-3]. Auger losses are significant at high drive currents, due to the increasing carrier densities within the quantum wells, which bolster the likelihood of this three-particle recombination process.
An obvious candidate for mitigating Auger recombination is the introduction of active regions with more wells, as this promises to reduce the carrier density in each of them. But this has limited success. Asymmetry in electron and hole effective masses results in the carrier density in the p-side of the active region being higher than it is in the n-side, and that leads to variation in carrier recombination. So adding quantum wells produces diminishing returns "“ and then none at all.
Figure 3. A comparison of thin-film (TF) and flip-chip (FC) designs: (a) thin film, (b) flip-chip based single-side low étendue emitter, (c) flip-chip based five-side emitter. Note that the drawings are not to scale: the epitaxial growth is typically 5-10 mm, the phosphor layer typically ranges from 40 mm to 100 um, and the sapphire thickness is 100-200 mm
A far better approach is to use band structure engineering. This can promote better carrier distribution and ensure a lower carrier density per quantum well. Accomplish this and the operating point for the device is higher on the efficiency curve (see Figure 2).
Although active regions designed for low droop are generally able to realise an even distribution of carriers amongst the quantum wells, they do so at the expense of material quality "“ and this increases non-radiative Shockley-Read-Hall recombination. Often, it is the increase in the indium content in the low-droop active region designs that contribute to the degradation in material quality. Clearly, an optimal LED must combine combatting droop with high material quality that ensures a low Shockley-Read-Hall recombination (see Figure 2 for details)
Another option for negating droop is to increase the radiative recombination rate via greater overlap of electron and hole wave functions. Today's LEDs are produced on the c-plane and plagued by internal electric fields, which pull apart the electrons and holes and impair radiative recombination. Improvements are promised by switching to semi- and non-polar substrates that would reduce or eliminate polarization-induced electric fields within the active region. Benefits are not limited to a higher radiative recombination, but extend to a reduction in Auger recombination rates at higher drive current, thanks to the intrinsically lower quantum well carrier density that stems from the shorter radiative lifetimes. What's more, as the carrier overlap constraints on the quantum well thickness are far weaker in semi- and non-polar devices than in their conventional cousins, wells can be thicker, driving Auger recombination even lower.
Fulfilling all this promise is not easy. Today, semi- and non-polar devices are held back by their short non-radiative recombination lifetimes, and substrates are very pricey, with no commercial volumes. In addition, although progress is being made on these alternative crystal orientations, they are chasing a moving target, as performance of c-plane, high-current devices continues to improve, thanks to refinements in carrier spreading and material quality.
Enhancing extraction
One route to optimizing the light extraction in modern, high-power LEDs involves reducing the number of pump photon bounces "“ that is, the number of round trips that a pump photon typically undergoes inside the die cavity before it escapes "“ and cutting the pump absorption within the die cavity.
These two key characteristics "“ the number of pump photon bounces and the pump absorption "“ can be markedly different in two common architectures: the flip-chip and the thin-film (see Figure 3 for diagrams of the device architectures). Thin-film designs provide a smaller source size, and they are preferred in highly directional applications, whereas flip-chip designs allow direct attach onto boards, without the use of an interposer. Common to both are high current densities and a low thermal resistance, which enables high density arrays.
In addition to these two designs, there is a third, which is a variant of the flip chip: it redirects photons through the top side of the die by blocking the sides of the sapphire substrate (see Figure 3 (b)). Merits of this design include: a smaller source size and tighter angular radiation pattern, leading to a smaller étendue; a more efficient coupling efficiency; and greater flexibility in design.
Judged in terms of photon bounces, both of the flip chip designs, which have a strong dependence on sapphire thickness, outperform the thin-film architecture (see Figure 4). With the flip-chip geometry, the sapphire needs to be thick enough to prevent a high number of photon bounces "“ for example, at least 100 mm for a 1 mm2 chip.
There are two characteristics of flip-chip architectures that lead to a significant reduction in the number of bounces, thereby facilitating extraction. The first is the reduced index contrast at the escape GaN surface relative to the thin-film, due to the high refractive index of sapphire. And the second is that once light has transitioned into the sapphire cavity, it can propagate out through the side-walls, thus reducing back scattering into the GaN area. For a typical sapphire thicknesses, side-wall radiation may account for 30 percent to 40 percent of the extracted power (see Figure 5).
One downside of this geometry is that the potential flux gain goes hand-in-hand with a hike in the étendue, which increases proportionally with the effective emitting area. Coating the sides of the flip-chip die with highly reflective scattering material, such as a TiO2-loaded silicone, can minimise the étendue by ensuring single top-surface emission that maximizes luminance levels. However, the price to pay is inferior light extraction, particularly at high sapphire thickness levels when using highly scattering coating materials.
In general, the number of photons bounces depends on the angular direction of photon emission from the active region, and is highest for angles near grazing incidence. But the relationship between angle and photon bounces is not simple, with valley curves appearing between 15° and 40°. This feature is seen in all three designs of the LED, and is associated with the complex transmission characteristics of the patterned sapphire surface interface. As will be shown later (see Figure 9), such transmission does not necessarily peak at normal incidence, and may do so at a significantly different value. Note that for higher photon emission angles, the average number of photon bounces takes a sudden step-up, coinciding with the critical angles of either the GaN-sapphire or the GaN-silicone interface. Side-coating of the chip has a significant impact on the number of photon bounces.
For a flip-chip die without a side-coat, the bounce number increases rapidly at higher angles around the GaN-sapphire critical angle as opposed to that for GaN-silicone. This is consistent with our understanding, as any total internal reflection at the sapphire-silicone top surface will have a second chance to escape from the sapphire side-walls. Side-coating the flip-chip die is a game changer, leading to a hike in back-scattering into the GaN, with the consequent increase of bounces shifting to lower angles near the GaN-silicone critical angle.
The extraction efficiency from the different types of designs can be explained within this framework (see Figure 6, which plots the gain in extraction efficiency for the flip chip design, compared with that for the thin-film architecture). For the flip-chip, extraction improves rapidly with sapphire thickness up to a relative a thickness level of around 0.25, and then it reaches a plateau. Side-coating is detrimental, failing to deliver any increase in extraction efficiency, even if the coating is considered lossless. When poorly reflecting coatings are used in conjunction with high sapphire thicknesses, extraction efficiencies may plummet.
For outright efficiency, the five-side emitting flip-chip excels, because the sapphire cavity can reduce the interaction of the backscattered light with the lossy areas of the chip. However, the net reflectance gain over the thin-film designs may only be significant for relatively high sapphire thicknesses. Typically, it must be well above 0.1, in consistency with the dependency on the number of bounces.
Our approach to improving light extraction focuses on reducing pump absorption. For the flip-chip, attenuation of the recirculating pumped radiation as it propagates inside the die cavity is typically 7 percent per round trip. This leads to an extraction efficiency of around 85 percent when there are, on average, eight photon bounces.
The greatest contributor to this absorption is the GaN-Ag interface. One way to address this weakness is to switch to a composite structure, formed by interposing a sufficiently thick, low-index oxide layer between the metal and the semiconductor (see Figure 7). Selecting SiO2 prevents light incident within a critical cone angle of approximately 40° from interacting with the metallization. The reflector loss contribution can then fall from 50 percent to just 20 percent, according to our simulations.
Superior current spreading also results from the composite structure, as it is possible to ensure that injection into the active region predominantly takes place away from the n-GaN vias (see Figure 8). This is especially beneficial under high drive conditions.
The three-layer mirror is not without fault: weaknesses include additional absorption in the ITO layer, a reduction in enhancement of the internal quantum efficiency associated with the Purcell effect, and a more pronounced angular side emission from the active region. It is challenging to uncover the sweet spot with all these factors at play, and to help in this endeavour we use our proprietary advanced multi-physics models and design tools. An example of our efforts with this high accuracy approach is shown in Figure 8.
Another measure taken to increase light out-coupling via a reduction in the number of photon bounces is to optimize the scattering features associated with patterned sapphire substrates. If plain sapphire were used, this would be detrimental on two fronts. Firstly, there would be a lowering of the optical transmittance at the exit surface in the angular range of maximum incident radiation, which is closer to grazing than normal incidence. And secondly, there would be a reduction in the cancelation of guided modes, due to light becoming specular-reflected rather than diffracted.
Using wave optics, we have simulated the external extraction efficiency from a typical patterned sapphire texture design. These calculations, which uncover the impact of diffraction optics, reveal that sub-micron features only produce modest enhancements in light out-coupling. What's needed are micron-size features that can optimize scattering and transmission characteristics at the surface interface (see Figure 9).
Diminishing phosphor droop
Mirroring the reduction in internal quantum efficiency of the InGaN active regions, the quantum efficiency of the luminescence in phosphors decreases non-linearly with excitation density. However, the extent of photo-quenching varies between phosphors, being strongly pronounced in Eu2+ doped nitride red phosphors, and far weaker in the yellow-emitting Ce-doped aluminium garnets. The level of quenching also depends on temperature. For the Eu2+ doped nitride red phosphors, the efficiency decrease has a quadratic dependence on the concentration of excited europium activators. For warm-white, high-power LEDs requiring a red-emitting phosphor to produce the necessary colour temperature, photo-thermal quenching can account for a quarter of the total drop in efficiency with increasing drive current. This is a major impediment to the brightness of white LEDs.
A true fix for photo-thermal quenching can only come from innovation at phosphor material level. But while we wait, practical approaches can be taken to mitigate this effect, such as optimizing the converter and introducing different architecture. The key is to minimize the concentration of excited activators in the phosphor, while meeting the requirements for LED performance.
One option is to lower the activator concentration at the material level. Take this route and a larger volume of material is needed to convert a desired fraction of pump light. In high brightness applications, where lateral source dimensions are kept to a minimum, the upshot is the need for thicker converting layers above the LED pump chip. This is bad news if the phosphors are embedded in silicones, because thicker converting layers lead to greater scattering of photons back into the chip, as well as higher phosphor operating temperatures. Fortunately, switching to ceramic phosphors can trim scattering while increasing thermal conductivity. It may also be possible to increase the converting volume laterally, if the source étendue can be relaxed for a given application.
Examples of practical approaches to reduce photo-thermal quenching include: mid-power LED architectures, where a small die is immersed in a large volume of phosphor slurry; and remote phosphors, where a large area of phosphor is illuminated by pump LEDs. In both cases, the emitting area of the optical source increases, hampering its capability to address high-luminance applications.