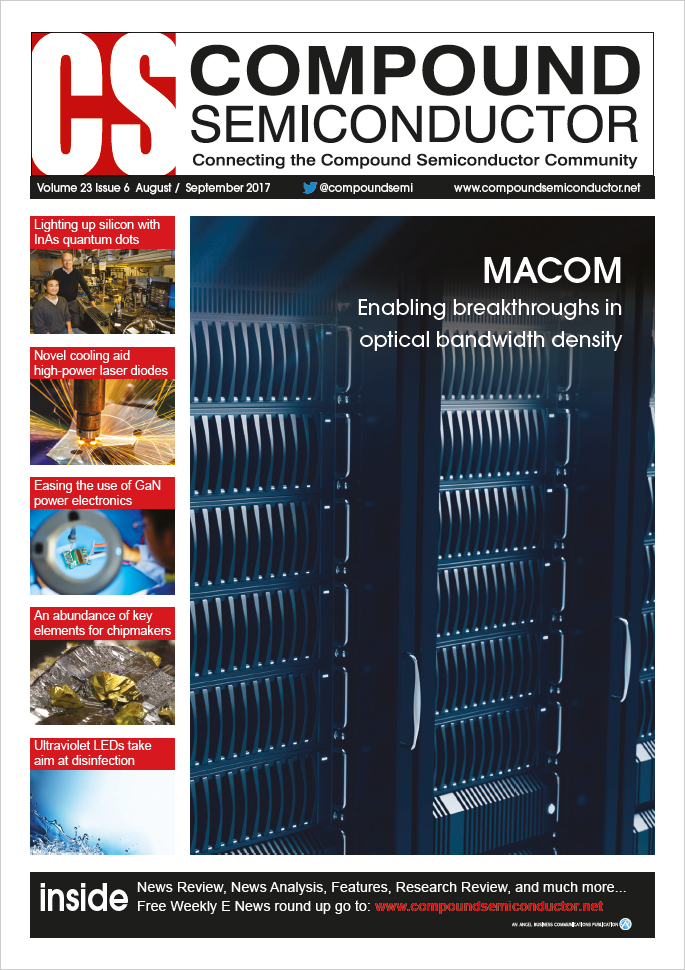
Novel cooling aids high-power lasers
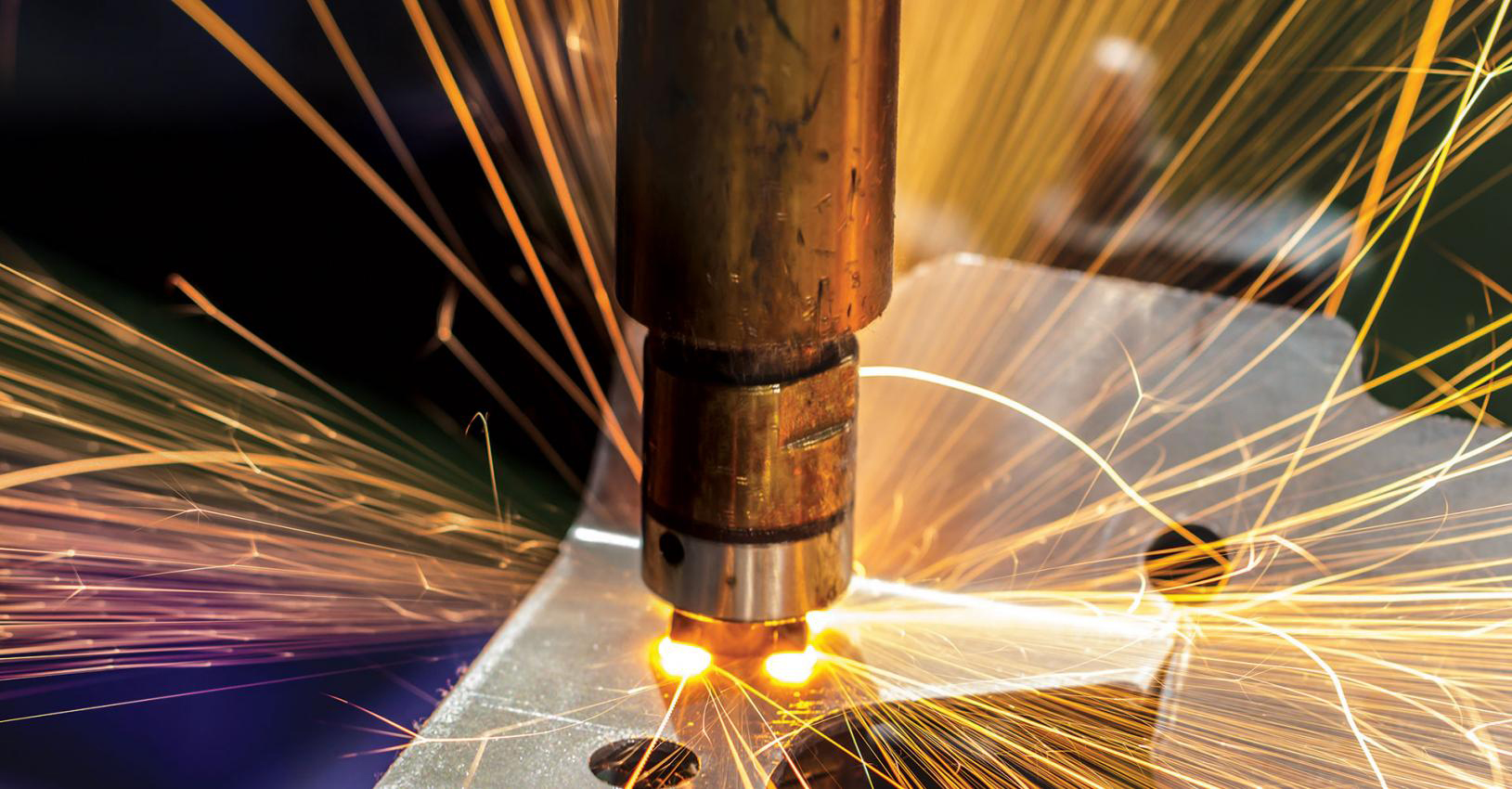
An efficient cooling architecture holds the key to trimming the size, weight and power of diode-pumped laser systems
BY JENNA CAMPBELL, PAUL LEISHER, MILAN MASHANOVITCH AND DANIEL RENNER FROM FREEDOM PHOTONICS AND TADEJ SEMENIC AND AVIJIT BHUNIA FROM TELEDYNE SCIENTIFIC COMPANY
A variety of applications are served by high-power solid-state lasers, pumped by diode laser arrays. They include a wide range of commercial and military uses, from the welding and cutting of materials to the enabling of precise surgery.
As well as delivering a high output power, many applications require the laser systems to have a low size, weight, and power consumption (SWAP). To realize this, diodes have to operate efficiently, so they generate less waste heat; and it is helpful if they operate at elevated temperatures, because this eases cooling demands.
When diode lasers are cooled with a liquid coolant, the diode's operating temperature is directly proportional to both the coolant temperature and the heat generated during lasing. Operation at a high coolant temperature is advantageous from a thermal management perspective, but there is often a downside "“ an excessive diode temperature.
Addressing this weakness is our team from Freedom Photonics of Santa Barbara, CA, and Teledyne Scientific Company of Thousand Oaks, CA. Working together, we have developed a technology that involves a low-thermal-resistance cooler with industrial coolant, and high-performance laser diodes operating at a higher temperature. This combination slashes the SWAP.
To illustrate the advantage of high temperature diode operation, imagine the following scenario: a 50 percent efficient diode pumping a solid-state laser with 50 percent efficiency. For this system, wall-plug efficiency is 25 percent. So, if the system provides a 10 kW source and uses batteries and a closed-loop chiller, both the batteries and the chiller will be tremendously heavy.
Increasing the coolant temperature is a good solution. When it is higher, the chiller, which is very heavy and consumes a lot of energy, can be replaced with a lightweight heat exchanger and a fan. Further gains are possible with an increase in the efficiency of the diode laser, because this decreases the number of batteries required to power the laser and reduces waste heat, allowing the use of a smaller cooling system. Realizing these improvements in performance hinges on careful engineering of the laser chip and the thermal management system. Within the high power laser community, it is well known that the laser's heatsink is a significant barrier to power scaling in high-efficiency, broad-area semiconductor laser arrays. An ideal heatsink is one that delivers a minimum temperature rise between the coolant and the laser diode emitter at a given heat load.
For diode laser bar arrays, state-of-the-art technology is based on microchannel cooling. A liquid coolant flows along the underside of a thin metal layer in narrow fluidic channels formed between layers of copper or copper tungsten alloy sheets. The diode laser is soldered to the thin metal layer, and cooled during its operation. This approach, which allows for compact cooling and is scalable through stacking in two dimensions, produces a low thermal resistance "“ it can be below 0.2 K/W for a 1.0 cm wide bar with a 3.5 mm resonator length.
Figure 1. The conceptual design of the cooling system for diode laser arrays. On the left is a zoomed-in picture of an individual laser array, with cooling jets of propylene-glycol-water impinging on the p-side of the diodes. On the right is an illustration of a cooling manifold for a two-dimensional stack of laser bars. Each bar contributes 100 W of output power.
Unfortunately, there are several drawbacks associated with microchannel coolers: small channel dimensions place strict requirements on coolant filtration and the working fluid viscosity; delivery of an adequate coolant flow demands a large pressure drop, and therefore a high pumping power in scaled-up systems; and erosion of the cooler limits the lifetime of microchannel-cooled lasers to about 5000 hours. Due to all these issues, during the last decade there has been a drop in the number of diode laser vendors using this cooling technology. In its place are conductively cooled approaches, which have inferior thermal management and significant weight and size penalties.
Different fluids
With our novel semiconductor laser cooling approach we are able to deliver greatly improved performance while avoiding issues that plague conventional microchannel coolers. Out goes the deionised water coolant and in its place is an industrial fluid, such as a refrigerant or a corrosion-inhibiting glycol-water mixture. These alternatives are preferred to deionized water in many applications, because they operate over a wide temperature range and are less prone to corroding the cooling system. Due to the higher viscosity of glycol-water fluids than water, we replace the small micro-channels with macro-channels that have diameters of hundreds of microns. To aid cooling, these channels are brought very close to the emitters "“ they are separated by a gold-plated copper wall that is as thin as it possibly can be while maintaining structural stability.
Another innovation of ours is that instead of having the coolant flowing parallel to the laser array, we employ a jet impingement technology, with the coolant impinging perpendicularly. This approach has the edge over the conventional one, producing the highest possible heat transfer coefficient and ensuring the minimum temperature rise from the coolant to the laser emitters. Reducing the temperature rise, in conjunction with enabling chip operation at a high junction temperature, allows pump operation at high heatsink temperatures. Operated in this regime, the laser chip is cooled effectively by liquids at a relatively high temperature.
Figure 2. Images of laser devices.On the left is a photo of a laser bar on a sub-mount, attached to the liquid manifold, and installed in the thermal management test setup. On the right is a microscope image of a laser diode with multiple emitters.
We have fabricated and verified our thermal management architecture with laser systems based on one-dimensional laser diode arrays. However, our approach is scalable, and could be used to cool a two-dimensional stack of high-power laser diode arrays, such as those used in a diode pump module (see Figure 1 for an outline of our cooling architecture with diode lasers, using high temperature propylene-glycol-water). Our team optimises the laser structure and the cooler using an opto-electro-thermal-fluid co-design approach. Applying an iterative sequence, we feed results from semiconductor laser simulations into thermal and fluid simulations, and vice versa.
This allows us to fully customize each component for a specific application. When designing the cooler geometry, we explore different jet impingement patterns and channel sizes via extensive thermal modelling simulations. These impingement patterns and channel sizes are modified, depending on the laser array geometry.
We have focused our efforts on the development of improved 976 nm laser chip architectures that combine a high junction temperature with high efficiency. Benchmarking these chips is relatively straightforward, because semiconductor laser pumps for solid-state systems have been studied for several years. The pumps span 800 nm to 2100 nm in wavelength, and can achieve electrical-to-optical efficiencies in excess of 70 percent. However, these record-breaking efficiencies have been realized with a deionised water coolant at a temperature of less than 6"…°C, and such a low operating temperature is impractical for many laser system applications, because it requires large chillers.
Figure 3. High-power laser test data. Left: Optical output power and electrical-to-optical (E-O) conversion efficiency as a function of drive current. The device under test shows more than 90 W of output power at 57 percent efficiency and a 22"…°C coolant temperature. As the coolant temperature is increased to 35"…°C and 50"…°C, power and efficiency decrease. Top right: Example spectrum from a laser array. Light emission is at a peak wavelength of 976.7 nm, with a full-width-half-maximum (FWHM) of 2.5 nm. Bottom right: Table of peak E-O efficiency for different coolant temperatures. As the coolant temperature is increased from 22"…°C to 50"…°C, peak efficiency decreases from 57 percent to 52 percent.
To optimise our epitaxial structures and laser designs for high-efficiency performance at elevated temperatures we employ phenomenological laser modelling tools and rigorous full-physics simulations that utilize the finite-difference-time-domain method. In modern high-power diode lasers, free carriers in the active region are the primary culprit for optical absorption loss. To cut this loss, we engineer the optical mode "“ and this leads to higher device efficiency. Note that our laser designs are based on best practices employed by the high-power diode laser community, but we use additional optimization for our specific application.
Once we have finalized our laser designs, we grow the device's heterostructures on GaAs wafers in an MOCVD chamber, and then fabricate the devices using standard semiconductor processing techniques. Chips are cleaved into 19x1 emitter array bars, before high-reflectivity and anti-reflectivity coatings are applied to back and front facets, respectively. A typical device geometry has a 100 mm emitter width and a fill factor of 20 percent.
Following wafer fabrication, we flip-chip mount 19-emitter bars p-side down onto sub-mounts. Multiple wirebonds connect the back n-side of the laser bar to the n-electrode of the sub-mount. The resulting structure is attached to the jet impingement orifice plate and fluid manifold before high power, high temperature testing begins (see Figure 2 for the test set-up).
Higher powers
We have evaluated many of our 976 nm, 19-emitter laser bars, using coolant temperatures from 22"…°C to 50"…°C (see Figure 3 for some examples of our data). Tests involve driving lasers in continuous-wave mode and using a thermopile to measure the output power as a function of drive current. Spectra are captured with a fibre-coupled spectrometer positioned at an oblique angle from the laser output.
Figure 4. Data comparing different cooler types. The jet impingement cooler pioneered by Freedom Photonics and Teledyne is compared to two state-of-the-art (SOA) commercial coolers: one compatible with industrial coolants and one that requires deionised (DI) water only. Data was collected using a 10 mm x 4 mm uniform heat source that mimics the footprint of the 19-emitter laser diode array. The jet impingement cooler produced by Freedom Photonics and Teledyne (green triangle curve) shows 3.6-times lower thermal resistance at the operating point compared to a conventional commercial micro-channel cooler designed for industrial fluid (blue diamond curve). Both coolers can be used with industrial fluids, so they have 150-200 µm filtering requirements, which would be a robust and reliable design for use in a harsh environment. The jet impingement cooler also performs slightly better than a commercial micro-channel cooler for DI water (red square curve), even though the cooling mechanisms are quite different. The DI water cooler has a very strict 15-µm filtering requirement and is not suitable for many applications, due to its susceptibility to freezing, corrosion and clogging.
At a 50 °C coolant temperature, one of our 19-emitter laser bars produced an output in excess of 73 W and a peak electrical-to-optical efficiency of 52 percent. Reducing the coolant to room temperature propelled the output power to over 90 W, with electrical-to-optical efficiency climbing to 57 percent. Output is produced from a single emission peak with a full-width-half-maximum of just 2.5 nm.We have also tested our cooling technology using laser bars from commercial suppliers. The good
news is that our technology has a universal benefit, with lasers from these suppliers showing a comparable performance at these elevated coolant temperatures to those that we have designed and fabricated at Freedom Photonics. Future design improvements are planned, which promise to spur another hike in the high-temperature efficiency of laser bar arrays produced by ourselves and other manufacturers.
The key result of our work is that our jet impingement cooler delivers a superior performance over commercial state-of-the-art microfluidic coolers, when industrial fluids or deionised water is used (see Figure 4 for a side-by-side comparison of cooler performance using a 10 mm by 4 mm uniform heat source that mimics the footprint of the 19-emitter laser diode array). This is highlighted by a measurement showing that our jet impingement cooler, filled with industrial fluid coolant, has a thermal resistance at the operating point that is more than three times lower than that of a commercial cooler designed for industrial fluid.
It is significant to note that our jet impingement cooler using industrial fluid also outperforms a commercial micro-channel cooler using deionised water "“ it requires only half the pumping power to achieve the same thermal resistance. This benefit of a lower fluid pumping power is magnified in larger multi-array diode pump systems. As discussed previously, the deionised water micro-channel cooler is not a good choice for many applications, due to its susceptibility to freezing, corrosion and clogging.
Our results show that our jet impingement cooler technology can achieve a lower thermal resistance than commercial state-of-the-art coolers, allowing for high-efficiency laser diode performance at elevated coolant temperatures. This technology enables diode pump systems with low size, weight, and power consumption, which target commercial and military applications requiring a broad range of high power lasers.