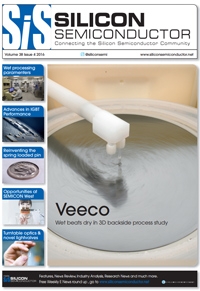
Productively Managing Equipment Relocations
Manufacturing consolidations have led to industry-wide change. When fabs open or close, relocating valuable process tools is a key consideration. As specialist NSTAR explains, making a move productive and efficient takes a trusted partner.
Over the past few years, the secondary market for 200mm semiconductor manufacturing equipment has been on a roller coaster ride. First the market declined, causing as many as two hundred 200mm fabs to close, resulting in an estimated 6,000 used semiconductor tools coming onto the market. This was followed by a resurgence in added capacity driven by new applications related to mobility, sensing and the Internet of Things (IoT) as well as refurbishment of 200mm fabs to leverage legacy node silicon and alternative materials process tools to build devices that do not require the capacity of 300mm wafers. Industry consolidation has further added to the number of high quality process tools moving across regions and to different countries.
Many plant owners are outfitting 200mm and other fabs with refurbished tool sets purchased on the secondary market. Considering that a large number of these tools are located at manufacturing facilities scattered across the globe, removing process equipment from a particular factory"”either to relocate the asset, resell it, or scrap the tool"”can be a monumental logistical nightmare if not handled correctly. This article discusses the complexity of semiconductor equipment relocation, using two case studies to illustrate best practices.
Decontaminating, decommissioning and relocating complex process tools is a highly specialized business that requires very specific skills, and considerable expertise. There are two paramount concerns: to protect the value of the asset, and, to ensure that the decommissioning and relocation is conducted safely. A third element"”time"”also drives some moves when relocating assets to another facility is done because the receiving fab operator needs the tool to be brought up to full capacity as rapidly as possible.
Semiconductor chips are built in fabs and foundries that use extremely sophisticated equipment requiring a variety of toxic gases, chemicals and high electrical power. The decommissioning and relocation process is built around safety as the primary concern. The process for de-installation starts with "˜fingerprinting' the tool so that its as-is condition is documented, recording the system functionality, the last qualification records and creating a ghost image of the tool software. Then, the system is decontaminated: chemical and physical hazards are removed, and any process gases or liquids are flushed/purged. The system is next disconnected from all utilities, all lines are capped or plugged, and any loose parts are individually labelled, wrapped and packed into shippable containers along with necessary documentation. Finally, the process tool itself is rigged, packed and crated for transport, and the site is remediated for any environmental impacts resulting from prior manufacturing operations.
At every step along the way, the de-installation process is documented; following proper safety protocols is critical. (For example, in some cases, the use of hazardous material suits and self-contained breathing apparatus are required.) The key to successful equipment relocation is meticulous planning, rigorous project management and adherence to best known methods (BKM), all with a strong overlay of "˜safety first.' Depending on the project size, teams should include a project manager, a safety manager and enough engineers/technicians to execute the project, along with any specialized equipment for loading, delivery and on-site setup if the tool is moving to a new operational location. The complexity of the project is also determined by whether the tool or tools are in a working fab"”if manufacturing operations are ongoing, the decommissioning and relocation project must be designed to not impact ongoing production.
Case studies
One recent case involved decontaminating, decommissioning, disassembling, moving out/crating, shipping, uncrating and installing over 70 semiconductor process tools, and ancillary and support equipment within live production environments across the globe at different integrated device manufacturer (IDM) locations. The IDM contracted M+W Group as the general contractor and NSTAR Global Services as the project management team to handle the relocation. It began with the de-install process in Israel and concluded with installation in Singapore.
The relocation team provided technical resources who liaised with the client's tool owners to provide a concise snapshot of the tools' fingerprint prior to decommissioning (which included functionality audits, making ghost images of hard drives, and last qualification records). Following the steps previously outlined, and using BKMs, the tools were disassembled and loose parts were individually labelled, wrapped and packed into shippable containers. Each tool travelled with a complete parts inventory assembled prior to crating, with all pertinent shipping documents provided.
At the time de-installation was taking place in Israel, the team was simultaneously preparing the receiving site facility in Singapore to reduce tool downtime, enable full integration and ensure a smooth transition of the production process. The same engineers and technicians who handled the de-installation performed the reinstallation to ensure continuity of tool knowledge. Most importantly, the entire project was achieved with zero safety incidents.
A second relocation case study involved moving tools from a deactivated facility, with tools destined for installation in multiple locations for reinstallation. One hundred semiconductor process/metrology tools required decontaminating, decommissioning and rigging-out from a facility in Taiwan that had closed and was no longer in production. This situation creates an entirely different set of challenges and site restrictions. The tool inventory had been sold to various companies and brokers with the understanding that a single general contractor (GC) would control the overall site management. The GC mandated that all documentation and discussions be conducted in Taiwanese. To facilitate these conditions, the company assigned a bilingual Asia project manager who assembled a team of Taiwanese resources comprising a safety officer, lead engineers, engineers and technicians. All team members were involved in daily meetings with the safety officer during the ongoing tool removal, and site walks were conducted three times a day. Throughout the project, safety protocols were strongly emphasized. Even under drastically different conditions, the project was successfully completed without incident.
Conclusion
As illustrated in this article, managing the logistics of semiconductor equipment relocation is an extremely complex process, with many and varied challenges that differ from one situation to another"”all depending on tool locations, conditions at both originating and receiving sites, government restrictions, etc. Relocating semiconductor equipment requires a specialized skill set, and should not be undertaken in an ad hoc manner. Rather, for optimal outcome in semiconductor, flat-panel display and solar manufacturing industries it is best to contract with a company specializing in equipment decommissioning, decontamination and relocation services such as NSTAR Global Services (M+W Group).