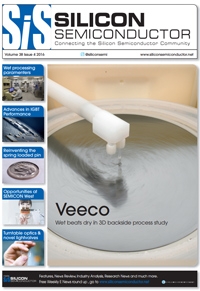
Elastomer Seals: Purity Or Plasma Resistance? Can You Have Both?
Reducing cost in semiconductor manufacturing is a constant way of life and reducing cost of consumables (CoC) is just one of many ways in which the industry can become more competitive and hence, more profitable.
The seal type or material is an integral part of this cost equation. Knut Beekmann, Market Manager for Semicon and Dr Murat Gulcur, Senior Scientist at Precision Polymer Engineering (PPE) explain.
In semiconductor manufacturing, particle contamination throughout the whole process flow is a significant threat to yield and hence profitability. It's also not just a matter of limiting the total number of particles but, particle size can also be a critical factor. Key manufacturing technologies include vacuum processes such as dry etch and deposition, all of which require elastomer seals to maintain the vacuum integrity. Seals in critical locations, meaning in direct contact with the process and in relatively close proximity to the substrate being processed, are often exposed to extremely aggressive chemistries and variable temperatures.
The net effect is always some kind of physical degradation of the seal over time, the most obvious being erosion. The seal needs to be compatible with the maintenance period of the tool and should not be the limiting factor in determining mechanical intervention or labour intensive additional down time. Furthermore, the seal should not contribute to yield loss through whatever erosion by-products may be formed.
Reducing cost in semiconductor manufacturing is a constant way of life and reducing cost of consumables (CoC) is just one of many ways in which the industry can become more competitive and hence, more profitable. The seal type or material is an integral part of this cost equation.
Background
The choice of seal materials available to end users can be bewildering. Without the luxury of having test chambers or fab production equipment dedicated to testing a multitude of seal materials in the various applications, the choice becomes a potentially risky one, which involves making a change and running live product using a new seal.
The effort must therefore be rewarded with a cost saving that is commensurate with the risk or resource required to carry out such a test. Such a saving can be achieved either through an extension of the uptime cycle, a reduction in the part cost or, a combination of the two. In order to greatly alleviate the risk of incorrect seal choice, potentially leading to scrapped product or wasted test resource, a comprehensive study has been carried out to benchmark seal materials from the leading elastomer O-ring suppliers. The creation and maintenance of such a database serves to greatly offset the risk associated with changing a seal material in order to reduce CoC and increase profitability or competitiveness.
Methodology
End users often run processes that are tuned to individual needs. It is also normal practice for manufacturers to keep such detailed process information confidential. To test every seal material in every process would be an impractical task. There are however, common chemistries used in plasma etch and deposition and this study was designed to test the various different elastomer materials in the more aggressive chemistries and plasma conditions. The process chemistries chosen are commonly used for etching of silicon, metals, compound semiconductors, dielectrics, resist ashing and particularly aggressive deposition chamber etch. Various different plasma modes were also employed, reflecting a variety of different process requirements. This included direct parallel plate, high density remote inductively coupled plasma (ICP) and sources specifically designed to create high radical and in particular, high fluorine radical content.
In all cases, elastomer materials were placed on the substrate holder on a carrier and subjected to the various process chemistries and plasma sources for fixed periods of time. The substrate holder was not biased to more closely represent the case where a seal would sit within a groove or retaining feature and as a result, would not normally be subject to significant ion bombardment. Materials were evaluated for their relative erosion rates or, mass loss and observation of surface particle formation. TGA spectra were also carried out in order to determine the nature of the material compound and in particular, whether the material was purely organic and filler-free, contained an organic filler or, contained an inorganic filler. The process chemistries chosen were:
O2 in a direct parallel plate plasma system
O2 in a remote ICP system
Cl2, BCl3, HBr in a remote ICP system
SF6, O2 in a remote ICP system
SF6 in a low volume ICP optimized high radical plasma system
The fillers used in the compounding play an important role in the plasma resistance of the elastomers. Most organic polymers have higher etch rates than the fillers. In order to achieve optimum, etch resistance, organic polymers are usually compounded with various types of fillers. The filler particles shield the organic backbone of the elastomer from erosion and therefore improve the plasma resistance of the elastomer material.
The filler particles which are dispersed and trapped within the polymer matrix, however; can become free after the polymer matrix is etched away. These free particles on the elastomeric seal can cause contamination and therefore reduce product yields in chemically aggressive processes. In order to minimize the risk of particle contamination and decrease erosion rates, some advanced filler systems can be used in the plasma resistant elastomeric material formulation. Minerals, metal oxides, and synthetic fillers are some examples of advanced filler systems. In general, the fillers can be classified in two groups as organic and inorganic fillers. Inorganic fillers provide better erosion resistance when compared with organic fillers because of their rigid crystal structure and relative chemical stability. The chance of contamination, however, is generally lower when organic fillers or no fillers are used in the elastomer formulation, with the disadvantage that erosion rates are considerably higher than their inorganic filled counterparts.
Results
The Thermogravimetric Analysis (TGA) curves in Figure 3 show the differences between the elastomer formulations with different filler types. A pure elastomer formulation with no fillers decomposes completely at around 500°C leaving no residue (Figure 3A). Similarly, a formulation prepared using an organic filler also fully decomposes at around 600°C without leaving any residue. In this case, the decomposition of organic filler can be observed in the TGA by a characteristic shoulder at slightly higher temperature than the polymer degradation (Figure 3B).
A residue is observed in the inorganic filled elastomer even at high temperature after the organics in the formulation are fully decomposed (Figure 3C). The amount of remaining residue corresponds to the amount of filler used in the formulation. As mentioned above, the chance of particle formation and hence contamination, by using an unfilled or organic filled elastomer is lower than that from a traditional inorganic filled material but the etch rates of inorganics are lower than the organic filled or the unfilled polymers.
This paradox can be resolved by using an advanced inorganic filler system which also significantly minimizes the risk of contamination. The use of lower amounts of filler with maximized surface area is an ideal solution. A filler system with a very high surface area has very small particles, ideally in the nanometer size range and they need to be well dispersed. In Figure 4, the plasma erosion rates of several different fluoroelastomers are graphically presented. Perlast® G67G and Nanofluor® Y75G have been found to provide very good plasma resistance in a variety of chemistries. These grades have been uniquely compounded with relatively low levels of an advanced, non-metal oxide, nano-filler system which has an average particle size of 25-40 nm.
The dispersion of nano-fillers1 in the elastomer formulation is another very important factor for determining the plasma etch resistance and potential for particle contamination upon plasma exposure. Nano-fillers must be perfectly dispersed in the polymer matrix to achieve maximum plasma etch resistance and minimum chance of contamination of the wafer or substrate being processed.
Nanoparticles have very high surface energy and very large surface area. In order to diminish this energy, they naturally prefer to form agglomerates or clumps which consist of several or up to several hundreds of individual nanoparticles.2 These agglomerates must be broken into single nanoparticles when compounding and dispersed uniformly in the polymer matrix.
If this is not achieved, these agglomerates will behave as macro-sized particles and can be released as micron-sized defects upon plasma erosion. This phenomenon can be seen in the cross-sectional SEM image of an unused sample, Figure 5A, which is a very good example of poor filler dispersion. As can be seen in Figure 5B, Nanofluor® Y75G however, exhibits excellent Nano filler dispersion and therefore provides significantly reduced chance of contamination or, generation of killer defects.
Providing a smooth surface after plasma erosion is also very important for critical sealing applications. Excellent dispersion results in a smooth surface even after plasma exposure. Poor dispersion causes a rough and uneven surface as a result of inconsistent etch rates on the surface (Figure 5). The TGA analyses of grade B2, Perlast® G67G and Nanofluor® Y75G in Figure 7 shows that the amount of nano-filler used in grade B2 is 20-35 percent higher than in either G67G or Y75G respectively. This therefore leads to a higher risk of particle contamination from grade B2.
Summary
During aggressive vacuum wafer processing, elastomer seals in key tool locations will be subject to wear during normal operation and will expose the wafer to the degradation by products of the elastomer material and also to any compounded materials contained within the elastomer. As evidenced by the erosion rates, there is inevitably a compromise between using seal materials that are completely free from any filler and organic fillers and those that use inorganic filler systems although some overlap between materials can be seen.
The best solution is generally to use inorganic materials which have well dispersed nano-fillers in the compound, which therefore offer optimized erosion and hence seal lifetime and greatly reduced chance of yield limiting particle contamination.