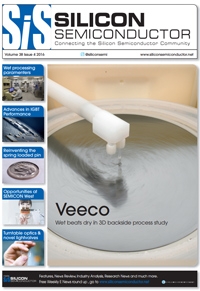
Acoustic Screening Reveals Component Defects
Plastic encapsulated microcircuits (PEMs) are mainstays of consumer, defence and commercial electronic products. Tom Adams, consultant at Sonoscan, explains how to safeguard your bottom line with optimized acoustic screening.
Imagine a typical plastic-encapsulated microcircuit (PEM) component. Inside this particular PEM lies an area of electronic mold compound that is separated from the die paddle by a gap. This very thin gap may be called a delamination, suggesting that the two materials were once bonded but later separated; or it may be a "˜non-bond,' suggesting that the two materials were never bonded. One side of the gap borders the die attach, but the gap does not extend under the die.
Regardless of its specific defect, this PEM poses a risk to any system in which it is installed. If the die must dissipate significant amounts of heat, the chief risk is that the gap will expand laterally under the die as a result of thermal cycling. There it will reflect heat being dissipated from the die back into the die. In time it may cause the die to overheat and fail electrically.
If the PEM is to be used in a low- or medium-priced consumer product, such failure may not be of critical concern. But if the PEM is to be used in a higher-level product (automotive, medical, military, aerospace, and some commercial products), such an internal gap-type defect is of considerable concern and should be found before the PEM is mounted on a board.
The PEM itself may be inexpensive, but if it is going into a critical application it should be screened acoustically for internal structural defects before use. Undiscovered defects can cost the manufacturer time, money and even its priceless brand reputation.
The most effective non-destructive means of finding gap-type defects is an acoustic micro imaging tool such as a Sonoscan C-SAM system. Laboratory, semi-automated and automated versions (Figure 1) all use a scanning transducer that pulses very high frequency or ultra-high frequency (ultrasound) into the PEM or other sample thousands of times per second. A pulse that encounters a gap-type defect is virtually 100 percent reflected by interface between the solid material and the air in the gap, even if the gap is as thin as 10 nm.
There are two widely used modes of acoustic imaging for screening PEMs:
Reflection mode imaging. A pulse striking a well-bonded interface is partly reflected to the transducer and partly transmitted across the interface. A "white" pixel in the acoustic image is made by a pulse striking a gap-type interface; a "gray" pixel is made by a pulse striking a well-bonded interface between solids. Pixel colors are sometimes altered for viewing.
Thru-SCAN imaging. The echoes are pulsed into the sample, but the reflections are ignored by the transducer. Pulses that exit the bottom of the sample are recorded by a separate sensor. In a THRU-Scan acoustic image, exiting pulses are typically gray, while locations where the pulse was blocked by a gap above are black because no ultrasound was detected.
Either reflection-mode or Thru-SCAN can be used in screening parts. Where it is useful to see a defect in detail and to know the approximate depth of a defect or feature, reflection mode is employed. If the goal is simply to identify a defect at any depth, Thru-SCAN is used.
Reflection mode was used in Figure 2, which shows a portion of a JEDEC-style tray of small PEMs. In these images, red indicates internal gap-type defects. Here the defects are delaminations between the die face and the mold compound. These are particularly risky defects because they can shear off wire bonds on the chip. In this image there are probably no acceptable components.
Whichever imaging mode is used, the acoustic data and images will identify the gap-type defects in all of the components in the lot, whether the lot consists of a handful of components or tens of thousands. Imaging can also reveal some non-gap defects, such as a die that is tilted or rotated from its intended position.
Clear definitions of acceptable and non-acceptable structural anomalies should be made before screening is performed in order to determine which components to scrap and which to use in production. The overall goal is to achieve the highest product reliability without scrapping components with internal defects that are probably harmless. It is easy enough to look at an acoustic image and examine a bright white feature that indicates a gap on the die paddle or in the die attach. But how do you accurately evaluate the risk this gap presents? The results of acoustic imaging are easier to interpret if they can be compared to an existing standard.
Several industry standards are available that can be used for comparison. One is Application of Scanning Acoustic Microscopy to Plastic Encapsulated Devices, Basic Specification No. 25200 of the ESCC (European Space Components Coordination). This standard provides guidelines for determining reject of components having defects of specific sizes. For voids in the die attach material of plastic packages, this standard would reject a component where more than 50 percent of the die attach area is occupied by voids. It would also reject components where a single void occupies 15 percent or more of the die attach area, or a void in a corner than occupies 10 percent or more of the die attach area. Finally, it would reject any plastic encapsulated component where 70 percent or more of any one quadrant is occupied by voids. These are straightforward values that are measured and reported automatically by C-SAM tools.
But for a specific lot of a plastic encapsulated components, these guidelines may not be a perfect match. There are simply too many attributes that can vary from one component type to another. IPC/JEDEC J-STD-020 E, Moisture/Reflow Sensitivity Classification for Nonhermetic Surface Mount Devices, lists more than 20 critical attributes. If even one of these attributes is changed in the redesign of a component, the component may need to be requalified for moisture sensitivity. The critical attributes include items such as die thickness, die passivation, wafer fabrication process, die attach process, and lead frame finish.
J-STD-20 is an industry standard, but was not designed for predicting overall reliability. It measures the ability of a given lot of plastic encapsulated parts to survive exposure to atmospheric humidity during assembly. A component's moisture sensitivity level is related to overall reliability, but generally does not accurately predict that reliability. It is not uncommon for engineers arranging for the acoustic inspection of one or more lots of components at one of Sonoscan's applications laboratories to mention that they would like to use J-STD-20. It may be an appropriate choice, or lab personnel may suggest a standard more directly related to reliability. If the customer is concerned about die attach defects, a good choice may be MIL-STD-883 Method 2030, Ultrasonic Inspection of Die Attach, or PEM-INST-001: Instructions for Plastic Encapsulated Microcircuit (PEM) Selection, Screening, and Qualification.
The customer's goal typically is to screen out those components whose internal structural defects are very likely to cause defects - multiple long delaminations on the top side of many of the lead fingers, for example, or voids that occupy 70 percent of the die attach. The more critical the application, the less risky will be the defects that can be accepted. Since each component has its own profile of attributes, finding an industry standard that is, without modification, a satisfactory match for a given component can be difficult. Often a standard needs to be altered to fit well with a particular component; even J-STD-20 is used, with appropriate modifications. The odds of successful acoustic screening can be improved if the customer acquires more information about the component to be screened and its application.
Customers can acquire this information by performing some form of life test on the component in question. Depending on the particular hazards the component will face in service, the user might employ thermal stress testing, mechanical shock testing, radiation testing, or another test type. Putting the results of testing together with an industry standard should bring the user closer to achieving optimal results from acoustic screening. Life testing might reveal, for example, that thermal stress causes small delaminations between the die attach and the die, but that additional thermal stress does not greatly enlarge these delaminations.
Additional insight is available from Sonoscan's test lab personnel, who have imaged thousands of different plastic encapsulated microcircuits, and who can help with modification of standards. The lab references about a dozen military and industrial standards for screening PEMs, but these are often just starting points. Many companies that use the lab have developed and maintain their own standards. Standards can be modified in any way that will benefit a particular application. If, for example, there is a hot spot on the die, instructions can be written to reject a component having any heat-blocking anomaly at the same x-y coordinates.
Occasionally an acoustic imaging mode other than reflection or THRU-Scan modes is used for specific purposes. If a component is likely to have structural defects at multiple depths (a TO-220, for example), an imaging mode can be used that scans multiple depths. There is no reduction in scan speed, and each depth produces its own acoustic images.