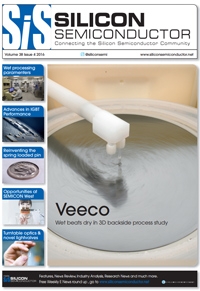
Improve Deposition & Process Control With Minimal Metrology Overhead
"Run-to-Run control can significantly improve process performance, but often at considerable time and cost. Taking a higher level view that applies novel methodologies can increase performance and savings with minimal metrology burdens." Says Joerg Reichelt, Yulei Sun "“ Rudolph Technologies, Inc. Tilo Bormann, Andreas Gondorf "“ Vishay Siliconix Itzehoe GmbH.
Semiconductor manufacturing is arguably the most sophisticated and unforgiving volume production technology ever developed [1]. It consists of a complex series of hundreds of unit process steps. The technology continues to evolve; it becomes more complex as device sizes and associated manufacturing tolerances shrink, which is aggravated by increasing layer and mask quantities as well as introducing new materials and process steps when manufacturers seek to accommodate a greater mix of products at higher volumes and efficiencies. R2R process control is a strategy that seeks to optimize process performance by tuning the operating parameters for the next cycle based upon previous cycle result measurements.
Traditionally, R2R controllers for semiconductor manufacturing are process-centric[2], meaning the R2R controllers are designed to solve the local control problems at a single step in the manufacturing process without aiming at the bigger picture of a series of steps.
For example, in a furnace deposition and CMP process flow, the majority of the post-CMP wafer-to-wafer thickness variation usually comes from variation in the pre-CMP thickness of wafers as they complete the deposition process in the furnace. The deposition process is complex, with many parameters available to adjust performance that also need to be controlled. A process-centric design philosophy will implement a multi-input-multi-output (MIMO) furnace controller [3] to minimize the wafer-to-wafer thickness variation locally before it can propagate downstream to the CMP process. An additional CMP control strategy would be designed to compensate for the post-CMP wafer thickness variation introduced by the CMP tool drift.
The complexity of the deposition process makes R2R control difficult. Adjusting the operating parameters requires the execution of complex experiments that consume significant time and resources. In addition, deposition furnaces are different from most other types of process equipment in that they are designed to process multiple lots of wafers loaded into a single carrier in each run. In contrast, the CMP process operates on one wafer at a time. The performance of a CMP tool on a given product wafer usually drifts relatively slowly over time, so control strategies typically operate at the lot level, adjusting polishing time for a subsequent lot based upon measured thickness of the previous lot. Lot level R2R control is a well-developed and widely accepted practice for CMP. It is possible to adjust polishing times for each individual wafer, but this requires thickness measurements of each wafer after deposition. The measurement overhead for such wafer-level control introduces prohibitive time and cost overhead.
Multistep R2R control
To address the issue of thickness variability without introducing unacceptable metrology overhead we have developed a multistep R2R control strategy using Rudolph Technologies' ProcessWORKS software. Essentially, this approach postpones compensation for post furnace wafer-to-wafer thickness variation until the CMP step, providing control for both steps. The strategy is based on our observation that most wafer-to-wafer, post-furnace thickness variation is a relatively well-behaved function of the wafer's location in the furnace carrier that can be approximated by a piecewise linear function (Figure 1). Thus it is possible to interpolate the likely thickness of each wafer based on sampled measurements of a few wafers in each lot, yielding a significant reduction in the overall metrology burden when compared to a conventional wafer-level control strategy. In this case we sampled 5 wafers in locations spread evenly through each lot. Likely thicknesses for unmeasured wafers were interpolated based on these sample measurements; CMP polishing times for each wafer were calculated based on the measured and interpolated thickness values. Post-CMP measurements of the thickness of the same 5 wafers were used to monitor and control CMP performance at the lot level. All calculations were handled automatically by the ProcessWORKS software.
Results
Implementation of the multistep R2R controller using ProcessWORKS is relatively straightforward; no programing is required. The operator defines the equation to calculate the output parameter, in this case polishing time, and configures the system interface with metrology and process equipment and factory control software. In our case, integration took three weeks and the controller was deployed in the factory five weeks after an initial requirements gathering meeting.
Figure 3 compares SPC charts before and one month after the controller was brought into production, showing a 72 percent improvement in Cpk for post CMP wafer thickness and the elimination of all out-of-limit excursions. The colors on the right side of the plot, after controller implementation, represent different CMP tools and make apparent the consistency of the improvements across all tools. After implementation of the controller, observations that the post-CMP thickness was also dependent on which furnace was used to process the wafer at the deposition step led to additional modifications in the R2R controller to include a correction for the furnace in polishing time calculations, yielding an additional 39 percent improvement in Cpk.
In addition to process performance gains, the multistep R2R controller saved an hour per day by eliminating the need for a daily tool monitoring run, reduced operator/engineering time for manual adjustments and extended preventive maintenance cycles
Conclusion
We have described the use of a multistep R2R process control strategy to reduce post CMP wafer-to-wafer thickness variability. It has successfully reduced the combined variability of the deposition and CMP processes without adding an unacceptable metrology burden. We were able to integrate the controller with the Vishay factory systems in three weeks, which allowed us to deploy the CMP controller within five weeks of the initial requirement gathering meeting. Since the deployment of this wafer-level CMP controller in production, the Cpk of the CMP process has increased by 72 percent with zero spec limit violations. The post-CMP wafer-to-wafer thickness variation has been reduced by 70 percent. We subsequently discovered that the post-CMP thickness is also dependent on which furnace was used to process the wafer at the deposition step and additional modifications to the R2R controller now use different values for different furnaces when calculating the polish times, improving Cpk by another 39 percent. Additional benefits of the controller included the elimination of nonproductive daily tool monitoring runs, reduction of engineering/operator time for manual adjustments and the extension of preventive maintenance cycles.