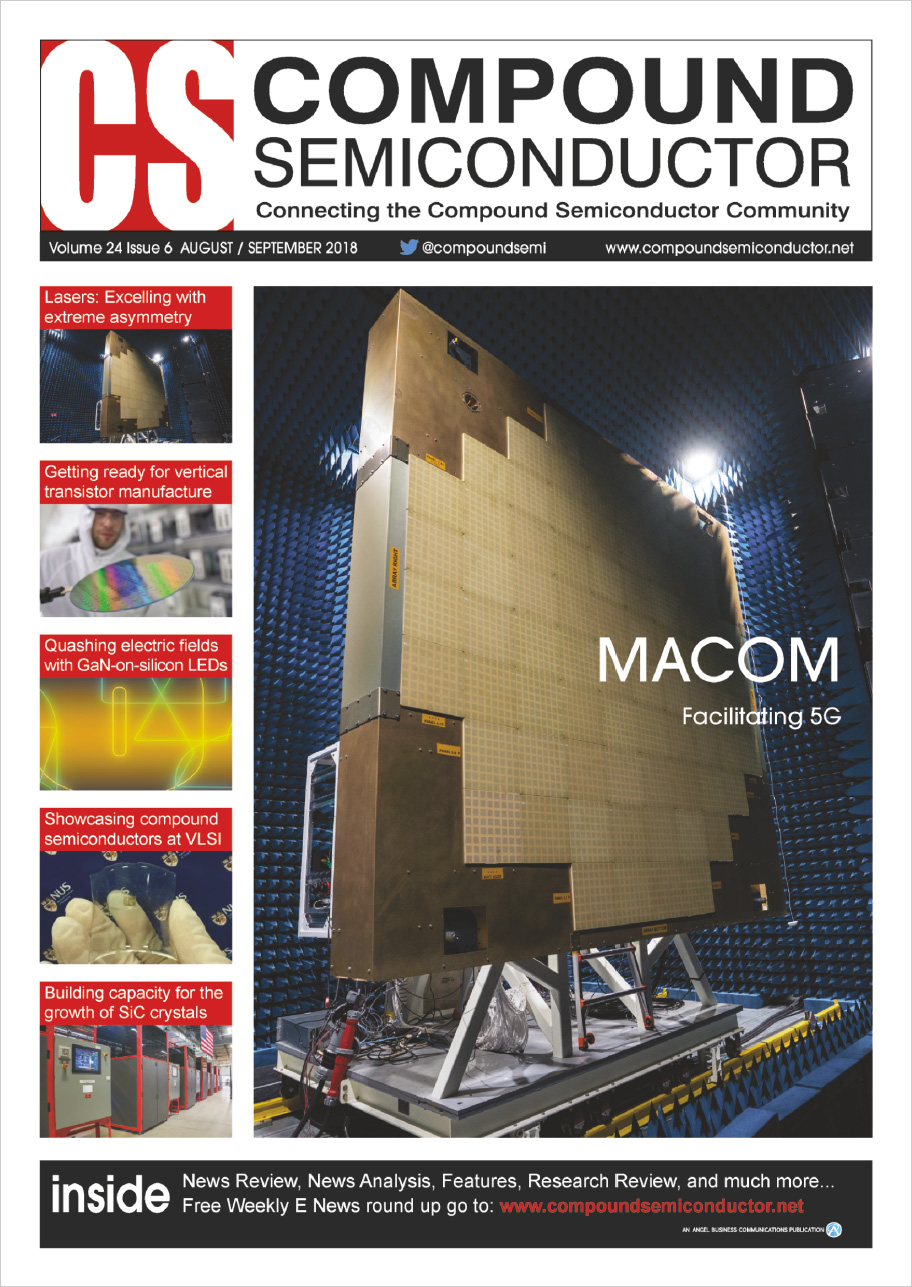
Building non-polar and semi-polar LEDs on silicon
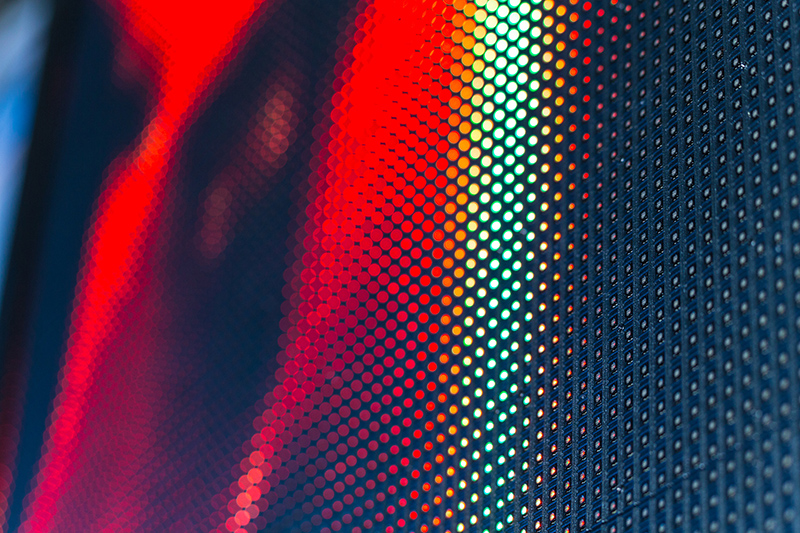
Of the billions of GaN LEDs made every year, the vast majority are produced by growing epilayers of nitrides on c-plane sapphire. It is an approach that's now relatively easy to take, but the LEDs that result suffer from two fundamental flaws: a reduced overlap of the electron and hole wavefunctions, due to a strong polarization field in the active region; and a low efficiency for the incorporation of indium in the InGaN quantum wells. Both these issues contribute to the "˜green-gap', a low efficiency for LEDs emitting in the green and yellow; and they hamper the development of full colour displays, laser diodes, and highbrightness sources for general lighting.
What's more, the strong polarization fields in the active region "“ a phenomenon that goes by the name of the quantum confined Stark effect "“ imposes serious limitations on Li-Fi, an emerging communication technology that uses light to transmit data over free space. Spatial separation of electron and hole wave functions that results from these fields leads to long carrier lifetimes: for blue LEDs it is tens of nanoseconds, and for green variants it is an order of magnitude higher. The lengthy lifetimes limit LED bandwidth to the megahertz range.
Figure 1. Select low-index crystallographic planes in group-III nitrides.
One promising approach to enhancing the modulation speed of the LEDs, and also increasing their efficiency in the green and yellow, is to switch growth from the polar orientation to one that is either semi-polar or non-polar. The former reduces the polarization fields, while the latter eliminates them completely (see Figure 1 for common non-polar and semi-polar planes).
For semi-polar planes, the angle made with the polar c-plane governs the extent that the electric field is reduced. When devices are made on semipolar (1101) and (1122), thanks to inclinations close to 60° with respect to the c-plane, the polarization discontinuity at InGaN/GaN interfaces is sufficiently small, aiding the fabrication of green devices with tolerable compositions of InGaN. Note that in theory, the weakening of the fields, which push emission to shorter wavelengths, is not the only benefit of semi-polar planes "“ they also promise to enhance the efficiency of indium incorporation.
What platform?
The ideal platforms for non-polar and semi-polar LEDs are native substrates with identical orientations. But natural limitations are making such structures prohibitively expensive for mass production. Today, HVPE and ammonothermal methods can produce relatively large GaN crystals, but these approaches are hindered by the strong tendency of GaN to grow in the polar (0001) direction. With HVPE it's possible to produce (0001)-oriented disks that are a few millimetres thick, limited by large internal stress; while the ammonothermal method yields hexagonal prisms that are a few centimetres thick, with a (0001) base plane (see Figure 2). In this case, crystal thickness is limited by the low growth rate. Due to these limitations, the non-polar and semi-polar substrates that are diced from (0001)-oriented boules are elongated rectangles with a width of no more than a few centimetres.
Figure 2. Comparison of the available GaN and silicon substrate sizes for growth of non-polar and semi-polar GaN (taking non-polar (1120) GaN as an example): (a) ammonothermal GaN, and (b) patterned silicon (110) substrate.
One promising alternative, which we are pursuing at Virginia Commonwealth University, VA, and the Otto-von-Guericke University in Germany, is to grow semi-polar and non-polar LEDs on patterned silicon. This approach has much to recommend, as silicon substrates are low in cost, available in large sizes, and allow the use of processes that are compatible with mature silicon technology. For example, a silicon platform could allow the combination of drive circuitry and LEDs on a single platform.
Many groups, both in academia and industry, have developed c-plane LEDs on silicon. A great deal of their efforts have focused on the development of stress compensating buffer layers, which mitigate a large tensile strain induced by the large thermal mismatch between silicon and GaN. Left unchecked, this strain causes the material to crack.
Unfortunately, none of the orientations of silicon can be directly employed to grow non-polar or semi-polar GaN LEDs. However, due to its epitaxial relationship with GaN, patterned silicon can provide a platform for growing GaN with various non-polar and semi-polar planes.
The key to producing non-polar and semi-polar orientations is the exposure of the {111} facets of a properly oriented silicon substrate for GaN nucleation (see Figure 3). As GaN grows epitaxially on silicon (111) in the c-direction, thanks to the epitaxial relationships GaN <0001>||silicon <111> and GaN <2110>||silicon <011>, it is possible to form: nonpolar (1100) (m-plane) and (1120) (a-plane) GaN on patterned silicon (112) and silicon (110) substrates, respectively; and semi-polar (1101), (1122), and (2021) GaN on patterned silicon substrates of different orientations.
We have undertaken experimental studies that confirm the theoretical predictions for complete elimination of the polarization field at the interfaces in nonpolar InGaN/GaN and GaN/AlGaN heterostructures, along with the substantial reduction in the semipolar varieties. Our photoluminescence spectra from (1100)-oriented 6 nm InGaN/GaN double heterostructures show no blue-shift with increasing excitation, suggesting an absence of the polarization fields and thus the elimination of the quantumconfined Stark effect. For semi-polar (1101) 6 nm In0.15Ga0.85N/GaN double heterostructures emitting in the blue, the shift to shorter wavelengths is just one-fifth of that for c-plane counterparts (see Figure 4). Note that similar results have been reported for other semi-polar orientations.
Recent experiments indicate that the benefits of the weaker fields are not limited to shorter radiative carrier recombination lifetimes, but extend to the dominance of radiative recombination by excitons "“ this is particularly attractive for high-efficiency LEDs and lasers. We have shown this to be the case in non-polar and semi-polar GaN/AlGaN systems, while teams at Cambridge and the University of Brunswick "“ Institute of Technology have identified this behaviour in InGaN/GaN heterostructures.
Figure 3. The growth geometry for non-polar (1120) (a) and (1100) (c) and semi-polar (1122) (b) and (1101) (d) and scanning electron microscope images for non-polar (1100) (e) and semi-polar (1101) (f) GaN on patterned silicon substrates.
The impact of piezoelectric fields on carrier lifetime is significant. Our efforts have revealed that switching from non-polar (1100) GaN/AlGaN to semi-polar (1101) lengthens the carrier lifetime from 100"“160 ps to 355 ps. Meanwhile, measurements at the University of Brunswick "“ Institute of Technology have shown that radiative recombination lifetimes in blue-emitting InGaN/GaN quantum wells formed on non-polar m- and a-planes and semi-polar (1122) and (2021) planes have radiative recombination lifetimes from 100 ps to 1 ns. These lifetimes are far shorter than those in c-plane quantum wells, and there is also a substantial reduction in non-radiative recombination.
However, when the indium content in the wells is high, semi-polar LEDs can be dogged by lengthy radiative recombination times. Measurements by a team at the University of California, Santa Barbara, have shown that in In0.36Ga0.64N/GaN quantum wells the radiative lifetime is 30 ns. This is attributed to the spatial separation of electrons and holes, due to an in-plane component of the electric field that arises from faceting of the growth front at the nanoscale.
Figure 4. Photoluminescence peak position, plotted as a function of photoexcited carrier density (excitation wavelength 380 nm) for polar (c-plane) and semi-polar (1101) plane 6 nm InGaN/GaN double heterostructures on c-sapphire and patterned silicon (001). The dashed lines indicate energy levels corresponding to energy diagrams shown.
So semi-polar and non-polar planes do not guarantee short radiative recombination lifetimes, and it is therefore imperative to understand the associated growth dynamics and fundamental limitations of the III-nitride material system in this context.
One of the merits of MOCVD growth of GaN on patterned silicon is that it can eliminate extended defects. Thanks to this, a team from Nagoya University, Japan, has been able to realise dislocation densities as low as 1à—105 cm"“2 in semi-polar (1122) GaN stripes by employing two-step selective growth on patterned silicon (113) substrates.
Figure 5. Comparison of defect distribution in (101) GaN grown on silicon (001) substrates with (a-c) wide-groove and (d-f) narrowgroove patterns: (a) and (d) scanning electron microscope images and (b) and (e) 10K cathodoluminescence images. Dark regions on cathodoluminescence images have high threading dislocation densities and bright regions dominate by near-band edge luminescence and/or emission from basal stacking faults. (c) and (f) GaN growth from silicon (111) sidewalls leads to threading dislocation propagation (solid blue lines) and growth front evolution (dashed lines). Note that the bottom GaN facet is in contact with the substrate surface.
We are following a similar path, investigating the growth of non-polar (1100) GaN on patterned silicon (112) substrates. With this approach, after GaN grows through the AlN buffer, it advances laterally along the GaN [0001] c+ direction "“ that is, the c+ wing. However, once GaN reaches the substrate surface, there is additional growth along the [0001] c− direction (c- wing) (see Figure 5). With this growth process, a fully coalesced surface is created with clear atomic steps.
Examination of this material reveals that dislocations are only generated near the GaN/silicon (111) sidewall interface, where the growth is initiated. There is a high density of basal stacking faults in c− wing regions, but the c+ wings are virtually free of extended defects.
Optimising the growth
During our efforts at developing non-polar GaN, we have found that the flow rate of NH3 can govern the characteristics of the GaN crystal. When growing non-polar (1100) GaN on patterned silicon (112) substrates, it is challenging to produce smooth m-plane surfaces with V/III ratios in excess of 700. That's due to the appearance of stable {1101} facets. To address this, we dropped the V/III ratio to about 100. A flat m-plane GaN surface resulted, thanks to the formation of top m-facets parallel to the substrate surface and the disappearance of {1101} facets at the meeting fronts.
A low V/III ratio is not ideal, because it is detrimental to the optical properties of GaN. So our solution has been to adopt a two-step approach: we start with a low-pressure (30 Torr) stage to ensure formation of the m-plane facets; and follow this with a high-pressure step (200 Torr), designed to improve optical quality. Room-temperature photoluminescence indicates that this two-step approach is successful. Emission intensity increases by a factor of three, and deep emission is suppressed considerably.
We have also investigated the spatial distribution of extended defects in our semi-polar (1101) GaN on patterned silicon (001) substrates. A key difference between this plane and the non-polar (1100) plane is that it is stable under a wide range of growth conditions. They include high V/III ratios and high reactor pressures, both of which are favourable for producing material with a high optical quality.
Similar to the growth of non-polar (1100) GaN on patterned silicon (112), the growth of semi-polar (1101) GaN on silicon (001) commences laterally along the c+ wing. The defective c− wing is far narrower than the c+ wing, due to the far lower growth rate in the [0001] direction and the limited supply of reagents during MOCVD growth.
When we use wide groove patterns "“ that is, those with a width of 10 μm or more "“ it prevents contact between the c+ wings of GaN and the opposing silicon (111) groove wall, and the threading dislocations propagate first along the c+ direction. However, as the growth proceeds, dislocations propagating in the vicinity of {1101} growth fronts bend under the action of image forces and then propagate in the basal plane, perpendicular to the [0001] growth direction. This causes many dislocations to terminate at the upper and the lower {1101} facets (see Figure 5).
For narrower grooves, such as those with a width of 3 μm, the c+ wings of GaN come in contact with the SiO2 masking layer on the opposite wall. This leads to the formation of basal stacking faults in both the c- and c+ wings. These faults may result from a combination of a concentration of strain near the contact region; and out-diffusion of oxygen and/or silicon from SiO2, followed by surface migration of the species.
In the narrow groove structures, some of the threading dislocations that propagate initially along the c+ direction are bent onto the basal plane with further growth, while those continuing along the c+ direction are terminated when they encounter an additional basal stacking fault row. The detailed mechanism for the interaction between the threading dislocations and the basal stacking faults requires further investigation, but we can cautiously speculate that there is a bending of the dislocations at the additional basal stacking fault row interface, which is in fact a boundary between the hexagonal and cubic phase materials. At this boundary, threading dislocations turn into misfit dislocations, which extend towards the top and bottom {1101} facets. This blocking of the threading dislocations by the basal stacking fault is highly beneficial, because it leads to regions that are virtually free from threading dislocations.
The regions of high optical quality that exist between the two basal stacking fault rows are clearly evident in near-field scanning optical microscopy images (see Figure 6). This technique suggests that the overall optical quality of semi-polar (1101) LEDs on patterned silicon (001) is comparable to that of highly optimized c-polar LEDs.
The challenges
Efforts associated with the growth of non-polar and semi-polar GaN on silicon have undoubtedly produced success. However, challenges remain, related to stress management, indium incorporation and the fabrication of devices.
Managing the stress in the structure is essential. Mirroring c-oriented GaN on planar silicon (111), there is a large tensile strain, which causes cracks to form in non-polar and semi-polar GaN epilayers on patterned silicon. One option for eliminating the cracks, which has already been pursued for GaN growth on planar silicon, is to employ either stress-compensating multilayer AlN/GaN buffer layers, AlGaN buffers with a stepor linearly graded aluminium composition, or AlGaN/GaN superlattices. An alternative is to undertake selected-area growth, using epitaxial structures with lateral sizes that are smaller than the separation between the cracks. Go down this route and light emitters can be no larger than the order of 100 μm "“ but that is sufficiently large for microLEDs.
Theoretically, switching from the c-plane to a semipolar plane should enhance indium incorporation. However, it is not clear if this really is the case. While some groups have reported that semi-polar (1122) and (2021) planes result in higher indium incorporation than the c-plane, others are claiming that the opposite is true. It is possible that these discrepancies are due to divergence in strain relaxation in the samples studied and/or indium clustering.
So far, there are not many reports of non-polar and semi-polar GaN LEDs. And those that exist tend to focus on either the elimination or the substantial reduction of the polarization field in the active regions. What is clearly missing is a detailed comparison of this class of device with industrial-grade, state-of-the-art c-polar LEDs.
Figure 6. Room temperature near-band edge emission measured by a near-field scanning optical microscope (a) and an atomic force microsopy image (b) of the narrow-groove pattern (1101) GaN sample.
Of the non-polar and semi-polar GaN LEDs that have been demonstrated, the majority are formed on the (1101) orientation. For example, a team at Aachen University, Germany, has produced a range of semi-polar (1101) InGaN-based LEDs on V-grooved patterned silicon (001) substrates. Those that emit in the blue produce a polarization-related wavelength shift of just 4.7 nm over a current density range from 5 A cm-2 to 100 A cm-2. However, green cousins have a blue-shift of around 100 nm, attributed to indium clustering in wells with an indium content of more than 30 percent.
One promising result from the team at Nagoya University is the fabrication of a blue InGaN/GaN laser structure, formed on un-coalesced (1101) GaN microstripes on silicon (001) substrate. This structure can produce an internal quantum efficiency exceeding 90 percent at high excitation levels. Such a high efficiency is attributed to the low dislocation density that is provided by the growth geometry.
The state of play
Our work has demonstrated that like epitaxial layer overgrowth, the merits of GaN growth on pattern silicon include a trimming of the density of extended defects, both dislocations and stacking faults. So far, much of our effort has been directed at studying the mechanisms governing defect generation and propagation in these structures. This has led to several interesting findings, including dislocation blocking with rows of stacking faults, and demonstrations of material with dislocation densities that are comparable to, or even lower than, those in the state-of-the-art c-polar structures "“ the benchmark is dislocation densities of the order of 108 cm-2.
What is encouraging is that when the structural quality of our active regions is sufficiently high, it could enable the fabrication of non-polar InGaN/GaN LEDs that are free from the perils of the quantum-confined Stark effect. And for semi-polar variants, this affliction is far less damaging than it is for conventional cousins, so devices have the potential to combine a high brightness with a short radiative recombination time.
Of all the different non-polar and semi-polar flavours of GaN on patterned silicon, it is the (1101)-oriented GaN on silicon (001) exhibits the best structural quality to date. Encouragingly, there are also reports of a higher indium incorporation efficiency on this plane. However, more data is needed to confirm this, and fulfilling the promise will also require the demonstrate of efficient green and yellow LEDs. And even if that happens, the ultimate success of this technology will lie in the hands of the LED industry, which may or may not explore this technology for general lighting.
To date, the pace of industrial LED development suggests that there is still more to come from c-plane LEDs. If that's the case, non-polar and semi-polar light emitters on patterned silicon will only serve niche applications. They include LiFi, which could grow considerably, and silicon photonics.