Fewer process steps, finer features
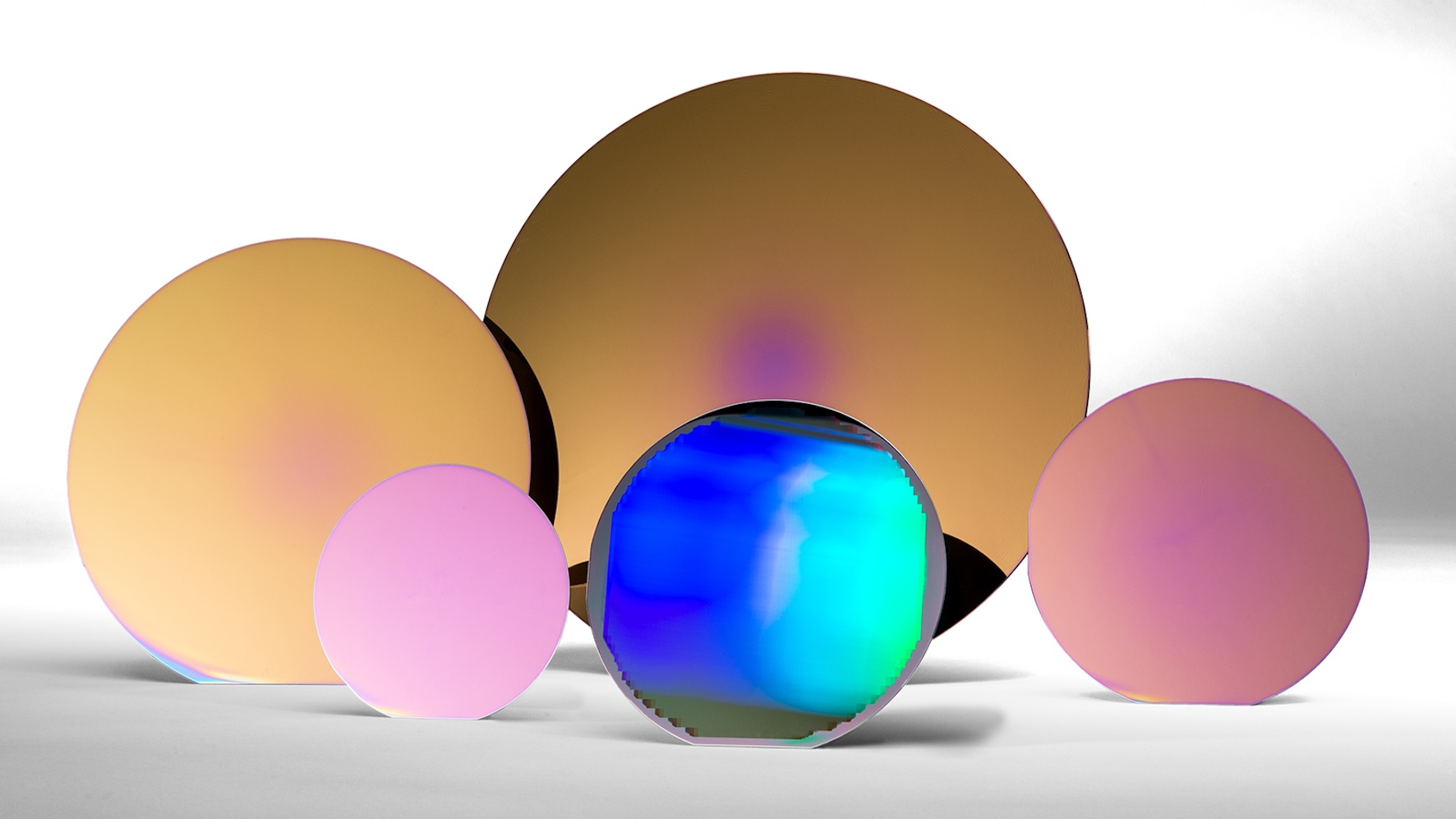
Scientists at the US Department of Energy's (DOE) Argonne National Laboratory are looking for commercial partners to license and develop a new material synthesis method that has the potential to reduce the number of semiconductor process steps and allow more intricate etch features.
The method known as sequential infiltration synthesis (SIS) was invented in 2010 during a lunchtime conversation between Argonne scientists Seth Darling and Jeffrey Elam and two of their postdoctoral researchers. The idea is based on atomic layer deposition (ALD) a thin film deposition technique that uses alternating chemical vapours to grow materials one atomic layer at a time.
"We said "‹"˜Wouldn't it be neat if we could grow one material inside another material like a polymer instead of on top of it?'" Darling said. "‹"It worked beautifully on the first try. Then we began imagining all of the different applications it could be used for."
Etching More Intricate Features
SIS is similar to ALD on a polymer surface, but in SIS the vapour is diffused into the polymer rather than on top of it, where it chemically binds with the polymer and eventually grows to create inorganic structures throughout the entire polymer bulk.
Using this technique, scientists can create robust coatings that can help the semiconductor manufacturing industry etch more intricate features, allowing them to become even smaller or to add extra storage and other capabilities. They can also tailor the shape of various metals, oxides and other inorganic materials by applying them to a polymer with SIS and then removing the remains of the polymer.
"You can take a pattern in a polymer, expose it to vapours and transform it from an organic material to an inorganic material," said Elam, director of Argonne's ALD research program, referring to the way the method can use polymers and a vapour to basically mold a new material with specific properties. "‹"It's a way to use a polymer pattern, and convert that pattern into virtually any inorganic material."
Because SIS can be applied to virtually any resist material and the infiltration of inorganic material can be tailored both chemically and quantitatively, compatibility is assured for nearly any etching recipe and substrate, they say. A process engineer can select an infiltrant that will provide strong etch resistance while simultaneously avoiding potential for poisoning of the ultimate devices.
Such flexibility is key when patterning compound semiconductors. Even more important, SIS provides a pathway to eliminate numerous process steps in a traditional fab associated with hard mask deposition and removal, which will minimise potential for damage to the thin, fragile substrates often used in high-frequency and power devices.
Deeper Grooves and Pattern Collapse
The technique also addresses a specific concern in the semiconductor manufacturing industry, pattern collapse, which means the collapse of tiny features used to create electrical components on a computer chip, rendering it useless.
When a pattern is etched on a silicon chip in the chip-making process, an etch-resistant surface is used as a protective coating to mask those regions you do not want to remove. But the etch-resistant coatings commonly used today wear away very quickly, which has prevented chip manufacturers from making components with deeply etched features, Darling said.
With SIS, inorganic vapour coatings can be engineered to provide greater protection of vertical features, allowing deeper etches and the integration of more components on each chip.
"Features on chips have gotten extremely small laterally, but sometimes you also want to make them tall," Darling said. "‹"You can't make a tall feature if your resist etches away quickly, but with SIS it's easy."
Solar Cells and LEDs
Similarly, the technique also has the potential to improve not only semiconductor manufacturing but also hard drive storage, solar cell efficiency, anti-reflective surfaces on optics and water-repellant car windshields.
By manipulating magnetic recording on hard drives or other storage devices, it is possible to increase storage while also getting smaller, Darling said.
Another possibility for the technology is to control how much light bounces off a glass or plastic surface. Using SIS, scientists can engineer surfaces to be almost entirely non-reflective. Using this strategy, scientists can improve performance of solar cells, LEDs and even eyeglasses.
"There are also a lot of applications in electronics," Elam said. "‹"You can use it to squeeze more memory in a smaller space, or to build faster microprocessors. SIS lithography is a promising strategy to maintain the technological progression and scaling of Moore's Law."
The team's research on the technology has been published in The Journal of Materials Chemistry, The Journal of Physical Chemistry, Advanced Materials and The Journal of Vacuum Science & Technology B.
Companies interested in using Argonne's expertise in SIS should contact partners@"‹anl."‹gov to learn more and discuss possible collaborations.