Linton Uses AI to manage crystal control processes
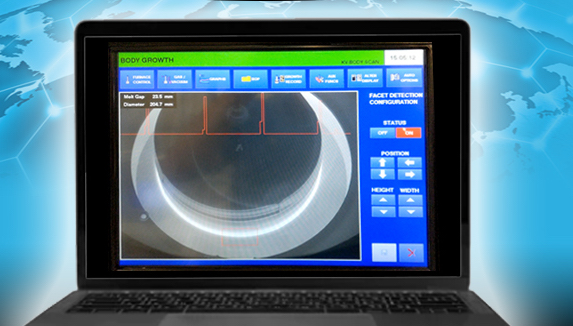
Upgrade provides an early warning system for when crystal structure loss is likely
Linton Crystal Technologies, a US-based developer of equipment for producing monocrystalline ingots for the solar, semiconductor and specialty materials industries, has announced its first use of AI techniques to manage crystal control processes.
The company has developed an early warning system for when crystal structure loss is likely. This is the company’s latest upgrade to its Kayex Intelligent Crystal Control System (KICCS) for its Czochralski (CZ) process crystal growers.
“With one operator overseeing many CZ growers at once, it’s not likely that structure loss will be detected immediately, or even in a timely manner. This results in a lot of wasted time, energy and material devoted to pulling a dead crystal,” explains Jeromy Tompkins, senior software engineer with Linton. “This upgrade essentially makes the machines smarter, so they can alert the operator when it seems the crystal has lost structure. The operator then has the ability to make an informed decision as to whether or not to stop the growing process early.”
The automatic facet detection feature uses the KrystalVision application within KICCS to draw data from real-time furnace images. Advanced techniques are used to analyze the stream, evaluating the statistical probability of structure loss based on facet presence and location. If structure loss is predicted, an alarm is sent to the operator’s control panel.
“In developing the update, we implemented algorithms for facet detection using traditional image processing and it worked well. However, the AI approach added an ability to locate facets that was unrivaled by the traditional approach,” says Tompkins. “I think this is a big step forward in facet detection and we also now have traction in AI, so we can make advancements with it fairly rapidly using the data we’ve collected.”
Linton recently hired Yiliang Shi, software engineer, to support the company’s advancements in machine learning and automation. This was the first project she worked on since joining the company. “We were all really excited to see the results of this project and the power of AI to achieve what traditional algorithms struggle with,” she says. “There are so many opportunities going forward because we’ll be able to draw upon both traditional and AI tools, based on the needs of the project.”
Automatic facet detection is among many upgrades Linton has planned for its control system; the company first introduced melt gap and power control upgrades.