Filtronic reaches phased array radar milestone
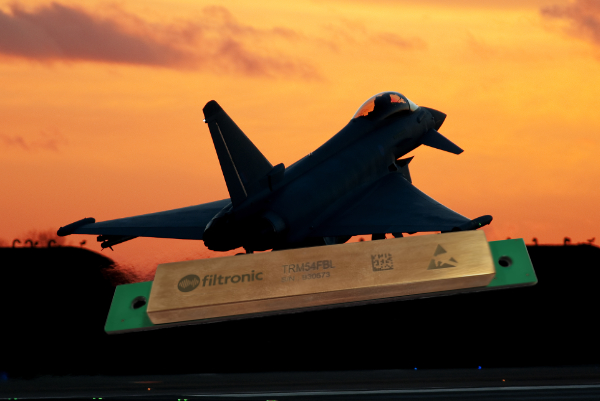
Company has manufactured and shipped more than 60k transmit and receive modules in three years to European defence OEM
Filtronic plc, a designer and manufacturer of RF, microwave, and mmWave products for the wireless telecoms and mission-critical communications markets, has announced that it has manufactured and shipped more than 60,000 transmit and receive modules (TRM) to a European defence OEM in just three years, under a specialist engineering and manufacturing services arrangement.
Filtronic produced six different variants of the TRM design, which are for use in an active electronically scanned phased array (AESA) radar system. This client recently awarded a special commendation to Filtronic in recognition of its outstanding contribution to strengthening the supply chain.
“The client made the strategic decision to dual source these TRM modules with Filtronic so that they could avoid the risks of single sourcing and could build a more resilient supply chain,” said Jerry Sanham, director of Business Development at Filtronic. “Their decision to appoint Filtronic was based on our demonstrated capability to provide a robust, high-quality and cost-effective solution. Since the first order, Filtronic has won multiple contracts with the same client and is now considered an integral supply chain partner.”
There are many challenges in manufacturing high-power TRMs for phased arrays, including mechanical and thermal considerations as well as the normal constraints associated with assembling a microwave subsystem to military standards. Filtronic has decades of experience designing and manufacturing its own products to the same rigorous quality standards.
Recent investments in hybrid assembly, advanced microwave test systems, and full product traceability have contributed to it being able to offer a high-quality, high security environment for volume manufacturing of hybrid microelectronics assemblies. Even with high-volume throughput, the production facility typically achieves first pass yields of more than 98 percent through continuous improvement and lean manufacturing. The comprehensive test facility can provide all the assurances that high quality, robust and reliable products are delivered to perform in critical military applications. Every product supplied are tagged with a unique ID which is logged throughout the proprietary end-to-end process control.