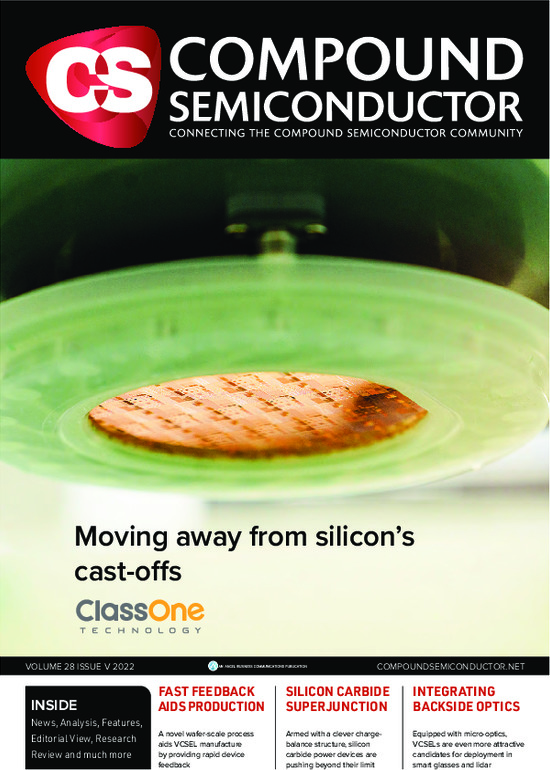
Moving away from silicon’s cast-offs
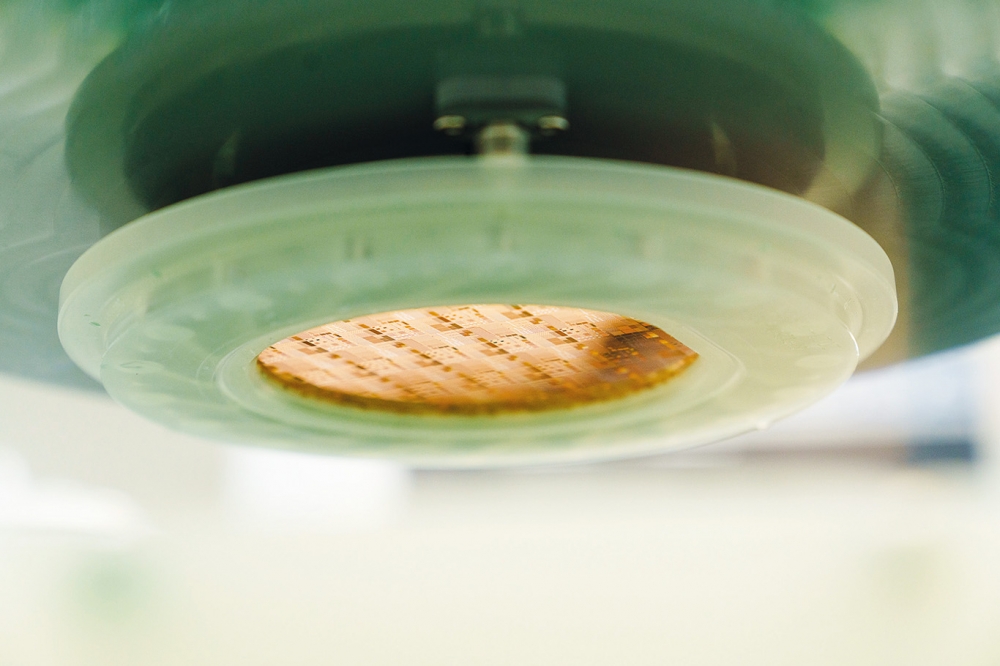
Instead of purchasing secondhand equipment from the silicon industry,
new compound semiconductor lines are investing in partnerships and
dedicated toolsets that will advance their capabilities
BY JOE GAUSTAD FROM CLASSONE TECHNOLOGY
WHAT DO YOU THINK is behind the current silicon chip shortage? Do you believe it is increased demand for PCs, driven by Covid-19? Or do you cite fab labour disruptions, the neon gas shortage from the war in Ukraine, the palladium shortage from banned Russian exports, or the exponential growth of IoT products?
Those who have given much thought to the cause of the current chip shortage argue that it’s not one factor, but a combination of them, which may influence one another. Simply blaming Covid does not stack up. While this has helped to accelerate the manufacturing deficit, the reality is that the silicon industry has been hacking away at a healthy level of spare capacity for many decades.
When evaluating this issue, it is tempting to just focus on the innovation in microelectronic technologies driven by Moore’s Law. But that restricts any analysis to simply logic and memory technologies. To really get to the bottom of what’s been going on, it’s critical to also consider the evolution of other semiconductor technologies, as well as the lack of investment in fab construction, tool investment, process development and labour force development.
Moore’s Law tech is defined as the leading node size for logic and memory technology. Those that play there need very deep pockets. Today, just a couple of companies are investing $30 billion or more to build fabs that can churn out chips at the 5 nm node or below. Supporting them is an ecosystem of tool and material suppliers that have developed the manufacturing technology for cutting-edge fabs to process wafers.
Relative distribution of chips in iPhone 13 Pro, per teardown by iFixit.
It is these IDMs, foundries, materials suppliers and tool manufacturers that are responsible for pushing the microelectronics industry forward at an incredible rate. And this leading edge is where almost all semiconductor capital investment exists.
Even in the last two years, leading-edge and near-leading-edge technology has accounted for 86 percent of semiconductor capital investment, according to IHS Markit. Due to this strong focus on the capital deployment that has pushed the Moore’s Law tech forward, a vacuum has been left in its wake that has opened the door to a range of alternative technologies.
These alternative technologies have benefitted from the approach of Moore’s Law tech leaders, which have shrunk nodes through innovation in device design and investment in new fabs, new tools and new process technology. As the proponents of Moore’s Law have marched from one node to another, their previous generation of tech and capital equipment has been sold on. Snapping it up have been the many players in the ‘More than Moore (MtM)’ arena, which encompasses all devices that exist outside of logic and memory, and includes makers of compound semiconductor chips.
Sectors that are within the MtM industry include those associated with RF, power, sensors, MEMS, photonics and analogue devices. While they evolve and develop in a more conservative fashion than Moore’s Law tech, that does not imply that they don’t make a crucial contribution to our everyday lives. These chips are an essential ingredient in everything from cars to toothbrushes. Even phones, which tend to have the latest generation of memory and logic on board, have more chips made with MtM technologies, such as RF, power, and sensors.
The ClassOne Trident Spray Solvent Tool provides modern and affordable batch wet processing.
Diverging toolsets
In 2022, we are seeing a shift in the interplay between those companies at the forefront of logic and memory, and those working in MtM industries. One factor at play is that leading-edge Moore’s Law technology is not downcycling capital at the same rates as before. But another big change is that MtM technology, which has becoming more important and more pervasive in all our electronic devices, is now so diverged from Moore’s Law tech that it requires its own specialized development. Most of the fabs that run MtM technology, including those producing compound semiconductor devices, are repurposed fabs that formerly existed on the Moore’s Law frontier. After purchasing these fabs, minimal changes were required before MtM manufacturing could begin.
However, today this route is not easy to pursue by the manufacturers of MtM technology. In the last few years, the number of repurposable fabs has fallen, as silicon fabs that are multiple generations behind TSMC and Samsung continue to churn out logic and memory chips. Highlighting this point is Intel’s 14 nm fabs, and foundries with 20 nm+ fabs, still operating in high-volume production. Due to this dearth of fab space, new fabs are being built specifically for MtM technology, such as Wolfspeed’s Mohawk Valley 200 mm SiC facility that opened earlier this year.
Historically, when a new MtM wafer fab opened or expanded, it would be kitted out with used tools, purchased and repurposed from a Moore’s Law ‘junk yard’. This inspired an entire industry of resellers and refurbishers, like Moov, that have aided efficient repurposing of fab equipment down the value chain from Moore’s Law tech to MtM technology. Today, many of these tools in existing MtM fabs are reaching the end of their life.
At ClassOne Technology – a provider of high-performance electroplating and wet surface preparation equipment to facilities using 200 mm and smaller wafers – we often hear of wet process and plating tools that have been running for 20 years or more. This has led many existing fabs to look for replacement equipment. At the same time, new fabs are looking for tools, a state-of-affairs that has forced MtM technology manufacturers to purchase new tools and partner with manufacturers in ways they have never done before.
As these MtM chipmakers grapple with this situation, we are on hand to offer a great deal of value to them. We offer the Batch Spray Trident system, which is a modern, cost-effective spray solvent and spray acid tool that can drop in as a direct replacement for aged tools. We also offer class-leading performance technology through our Solstice single-wafer platform, which is primarily serving compound semiconductor and other MtM customers.
By traditionally using refurbished tools, MtM technology has been bound by the design parameters of this capital. This restriction has not been faced by Moore’s Law tech, which has done a great job at overcoming bottlenecks associated with processes and materials. Unfortunately, technologies such as compound semiconductors face different bottlenecks and have differing needs. With MtM technology continuing to grow, more scrutiny is being placed on these bottlenecks, on efficiency, and on process optimization constraints.
One example of these factors at play has occurred at a MtM company that has needed to advance its gold-plating process efficiency. Working with us and a chemical vendor, it has succeeded in this endeavour. Efforts could draw on gold electroplating widely used in the silicon industry, although this washed out of the Moore’s Law Tech frontier more than a decade ago. Consequently, it has not been researched or optimized to the level of other materials, such as copper; and the interests of the largest of the big silicon-focused companies do not extend to these MtM domains.
The ClassOne Solstice single-wafer platform provides advanced electroplating and wet process technology.
Operating at the sweet spot
Against this backdrop we can be a gamechanger, as we occupy the sweet spot: we are large enough to support process development at our Technology Development Center; but we are not so large that only big Moore’s Law tech can access our capability. This opportunity excites us, and we are very keen to help grow an ecosystem of technology partnerships in the MtM technology segment.
As well as finding it hard to acquire used tools, MtM fabs are finding it tough to find experienced employees to run them and manage their facilities. This issue can be traced back to the actions of big semiconductor players, which are gobbling up talent at all levels to run their new fabs. This has forced MtM fabs to hire and train fresh graduates and new employees. Here we lend a hand, providing many of our customers with deep-dive training for their new employees on our tools and processes.
We are also assisting the smooth running of fabs through the launch of products designed for ease-of-maintenance and automated troubleshooting. Our technology uses modern software and algorithms to limit the need for human intervention.
MtM technology is on an upward trajectory, which must continue, given that the resulting devices are important to everyday life. Key to further progress is to follow in the footsteps of the Moore’s Law brigade, which has dedicated tool vendors, suppliers and fabs supporting the production of leading-edge memory and logic nodes. However, having a diversified ecosystem for MtM technologies is not, in itself, enough – there is a need for capital to build fabs; for tools that are specifically designed for unique challenges; and for technology partners who will help solve complex problems.
The good news is that there is an evolving ecosystem of solution providers focused in the MtM space, where we plan to be a model company. While the pandemic and other major events have disrupted global supply chains and taken the blame for the chip shortage, that should not obscure the reality that investment is essential for sustaining our lifestyles in MtM technologies.
ClassOne’s Technology Development Center has advanced metrology and processing capabilities used in joint development programmes and technology partnerships.