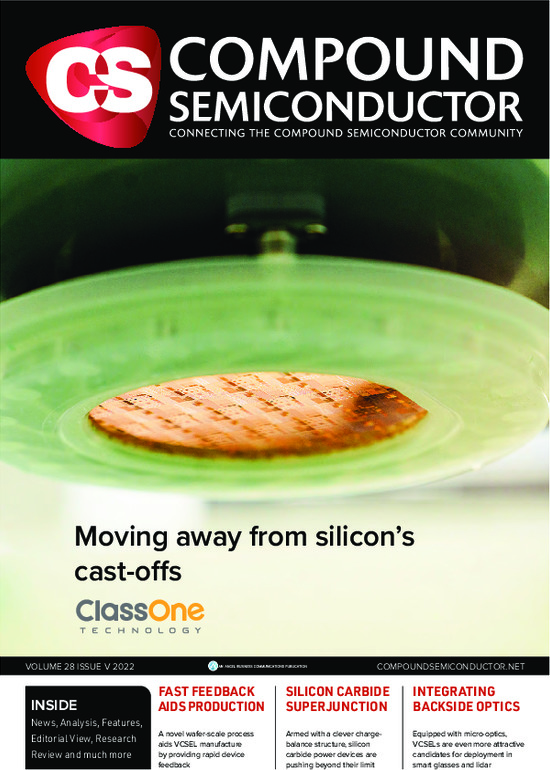
Move over MOCVD
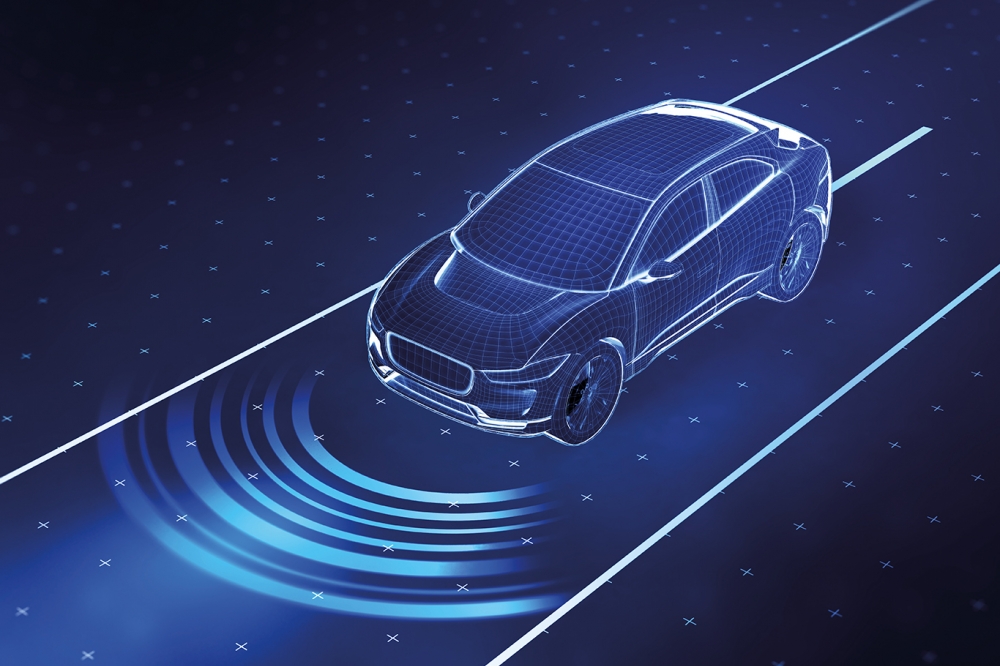
Thanks to its superior stability, MBE trumps MOCVD for the growth of long-wavelength VCSELs based on dilute nitrides
WHEN A DEVICE can do much more, it has a brighter future ahead. That’s certainly the case for the VCSEL. Initially it enjoyed much success as the optical source for transmitting data over short distances, and over the last few years sales have swelled to new highs, thanks to its deployment in the facial recognition systems found in smartphones. But even higher revenues are now on the horizon. They can be realised by expanding the spectral range of this surface emitter via the introduction of dilute nitrides, such as GaInAsN(Sb), that propel emission to 1300 nm and beyond. Sources operating in this domain are highly valued, being better suited to lidar and 3D sensing. That’s because light in this spectral range transmits through the glass display of the handset, and is intrinsically eye-safe, opening the door to the use of higher-power sources.
Today’s commercial VCSELs, which are based on either a GaAs or InGaAs active region and tend to emit at around 850 nm or 940 nm, respectively, are manufactured using MOCVD. But this mature growth technique, which dominates the production of III-V optical devices, is not necessarily the best option for producing VCSELs that feature quantum wells with a few percent of nitrogen. Despite decades of devoted effort, repeatable growth of dilute nitride layers with a controllable composition is still incredibly challenging by MOCVD.
History attests that a far better option is to use MBE to grow layers of dilute nitrides, partly because the lower temperatures associated with this technique ensure higher sticking coefficients for indium and antimony. Just over a decade ago, Solar Junction shot to fame by breaking the record for the efficiency of multi-junction solar cells by introducing low energy junctions made from dilute nitrides. This West-coast start-up developed commercial production processes for making these devices. And more recently, Array Photonics, a developer of lasers and photodetector arrays for infrared sensing applications, has been pursuing MBE for the production of its dilute nitride devices.
It is worth noting that the choice of reactor does not have to be an ‘either-or’ decision. There is the option of wafer transfer, allowing some of the epitaxial stack to be grown by MBE, while other regions are produced by another process, such as MOCVD. With a two-pronged approach the mirrors of the VCSEL may be grown by MOCVD, and the dilute nitride active region by MBE.
MBE’s merits
Thanks to its unique capabilities, there is much to like about MBE. It is a strong contender for the growth of all VCSELs, as it is capable of producing layers with exceptional uniformity and outstanding interface abruptness, due to the inherent atomic precision. In addition, it’s possible to produce high doping levels in p- and n-type material with high purity, thanks to the absence of hydrogen incorporation. What’s more, this form of epitaxy reaches a lower intrinsic background level than its rivals.
MBE is also renowned for its versatility. As well as playing a key role in the development of dilute nitrides structures, this form of epitaxy has been employed for decades for high-volume production of numerous epiwafers and various devices. MBE has been used within the RF/microwave industry by the likes of RFMD and Filtronic to produce pHEMTs; II-VI Laser Enterprise uses this growth process to make a range of lasers; and this epitaxial technique has been used to produce photodetectors, such as InP-based avalanche photodiodes and p-i-n structures. MBE reactors are also employed at the leading epiwafer providers, such as Intelligent Epitaxy Technology (IntelliEPI), EpiSolution and IQE’s facilities in the US and Singapore.
Exactly how MBE is employed within our community continues to evolve. During the last eight years or so, it has been demonstrated that MBE lends itself very well to the formation of highly sophisticated structures for various fields of optoelectronics, such as compound semiconductor devices containing phosphorous, antimonide or nitrogen.
At Riber, we have played a key role in supporting these efforts. There are now more than 35 installations of our MBE 6000 reactor, which accommodates multiple 6-inch wafers. The uptake of this tool has firmly established MBE as a viable option for producing RF/microwave device material, and for the manufacture of optoelectronic devices.
When device makers use MBE reactors in their foundries, they are able to benefit from stable, reproducible processes that can be maintained throughout a campaign that may last as long as a year or so. Those that are working there have epitaxial techniques that deliver a high yield, and are truly compatible with industrial production requirements, such as being fully automatic and having the capability to run ‘24/7’.
Demonstrating feasibility
For those that are considering developing production processes for dilute nitride VCSELs that involve the use of MBE, it should be noted that thanks to recent efforts, our MBE 6000 has been proven for the production of VCSEL structures, particularly for datacom applications. Results obtained by IntelliEPI have shown that this tool of ours can deliver excellent uniformity, in terms of output wavelength, across a full platen of four 6-inch wafers (see Figure 1).
Engineers at IntelliEPI have also demonstrated that with MBE, reproducibility can be close to 100 percent for the die-to-die output wavelength, for both high-specification 850 nm VCSELs for datacomms apps, and for 940 nm cousins that serve power 3D sensing. We attribute this very high level of reproducibility to exceptional thin-film uniformity provided by our correctly designed systems, such as our Riber MBE 6000.
Efforts at developing robust growth processes for producing dilute nitride VCSELs will be able to draw on a number of in-situ monitoring tools. Like MOCVD, MBE chambers can accommodate optical instrumentation that provides real-time monitoring of the growth process. Offering a diagnostic capability, these optical measurements can track the optical properties of the epiwafers, including their mirrors, and ensure that all wafers are precisely within the wavelength specification range. To assist process engineers, we have launched the EZ-CURVE – it provides in-situ curvature measurements and has shown promising results for monitoring the growth of VCSEL mirrors. Additional in-situ tools include those that provide measurements of the optical flux, reflectivity, pyrometry and the absorption band-edge temperature. Unlike MOCVD, it is also possible to track the evolution of the crystal structure, thanks to reflection high-energy electron diffraction. By combining this suite of insightful in-situ instruments with the intrinsic unsurpassed crystalline precision of MBE, this growth technique can address some of the traditional issues associated with the epitaxial growth of VCSEL structures on GaAs substrates by MOCVD. Switching from MOCVD to MBE increases the proportion of the wafer where there is a matching of the wavelength of the laser’s active region to the reflectivity sweet spot of the distributed Bragg reflector. In addition, the use of MBE addresses homogeneity issues and device processing yield losses, while trimming bow stemming from the GaAs/AlGaAs DBR structure.
The latest high-volume MBE reactor from Riber, the MBE 8000,
accommodates eight 6-inch wafers and produces an across-platen
uniformity that’s less than 0.5 percent. Epistructures produced by the
MBE 8000, which provides stable growth conditions over maintenance-free
campaigns that can last more than 12 months, feature abrupt interfaces
and have a high material purity, including the absence of hydrogen.
Seizing the opportunity
Against the backdrop of increasing VCSEL consumption, there is much promise for MBE within this industry. It has proven capability, demonstrated by the successes at IntelliEPI, and much promise for driving the commercial success of the dilute nitride VCSEL. Those that wish to try and dominate the long-wavelength VCSEL market may wish to consider our ultra-high capacity MBE 8000, launched last year and developed with the production of the VCSEL specifically in mind.
With the ability to accommodate eight 6-inch wafers, the MBE 8000 has twice the capacity of the MBE 6000. The first MBE 8000 is now undergoing final qualification to validate the highest uniformities, not just in terms of effusion sources, but also substrate temperature, across the largest deposition area available in MBE. Once qualified, this tool will strengthen the compelling case MBE makes in playing a critical role in the production of dilute nitride VCSELs.
Figure 1. (a) Normalized Fabry-Pérot dip wavelength versus radial distance from platen centre for the 15 x 3-inch, 7 x 4-inch, 9 x 4-inch and 4 x 6-inch platens in a Riber MBE 6000 reactor.
(b) Reflectivity maps and radial line scans of the Fabry-Pérot dip across 940 nm VCSEL structures grown on a 6-inch GaAs substrate in a Riber MBE 6000 reactor (4 × 6-inch). The Fabry-Pérot dip variation, below 1 nm, is limited by measurement accuracy. (c) Normalized stop-band centre wavelength versus radial distance from the platen centre for the 15 x 3-inch, 7 x 4-inch, 9 x 4-inch and 4 x 6-inch platens in a Riber 6000 MBE reactor.
(d) Reflectivity maps and radial line scans of the stop-band centre across 940 nm VCSEL structures grown on a 6-inch GaAs substrate in a Riber MBE 6000 reactor (4 × 6-inch). The stop-band centre variation is below 3 nm across the 6-inch wafer.
Further reading
† T. Sarmiento et al. Continuous-Wave Operation of GaAs-Based 1.5-µm GaInNAsSb VCSELs, IEEE Photon. Technol. Lett. 31 1607 (2019)
† M.G. Ebski et al. Baseline 1300 nm dilute nitride VCSELs OSA Continuum 3 1952 (2020)
† S Siala et al. 13xx-nm VCSEL arrays on GaAs for 3D sensing applications - Vertical-Cavity Surface-Emitting Lasers XXIV, Photonics West 2020
† J. Li et al. Highly Uniform VCSELs Grown by Multi-wafer Production MBE, CS MANTECH 2018
† Compound Semiconductor 2021, 6, 26