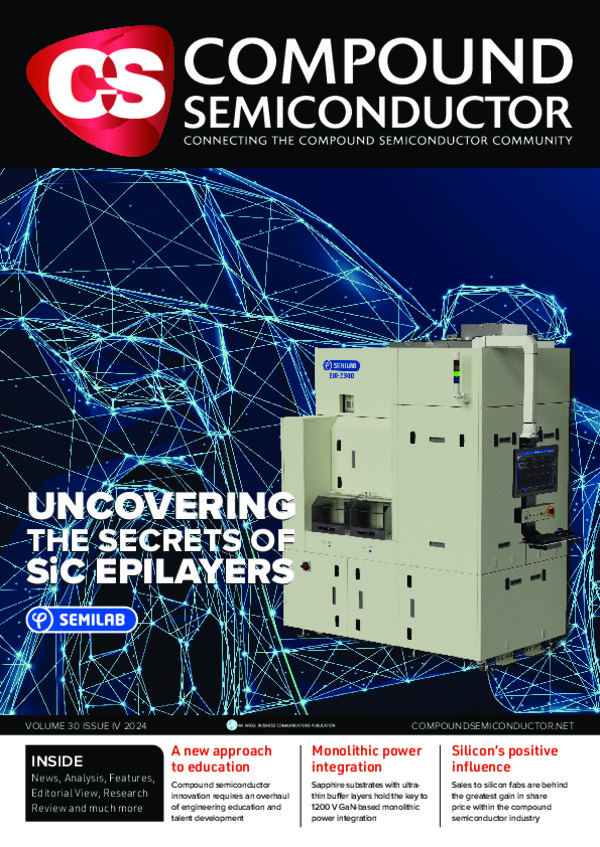
CS International: New vectors for the VCSEL
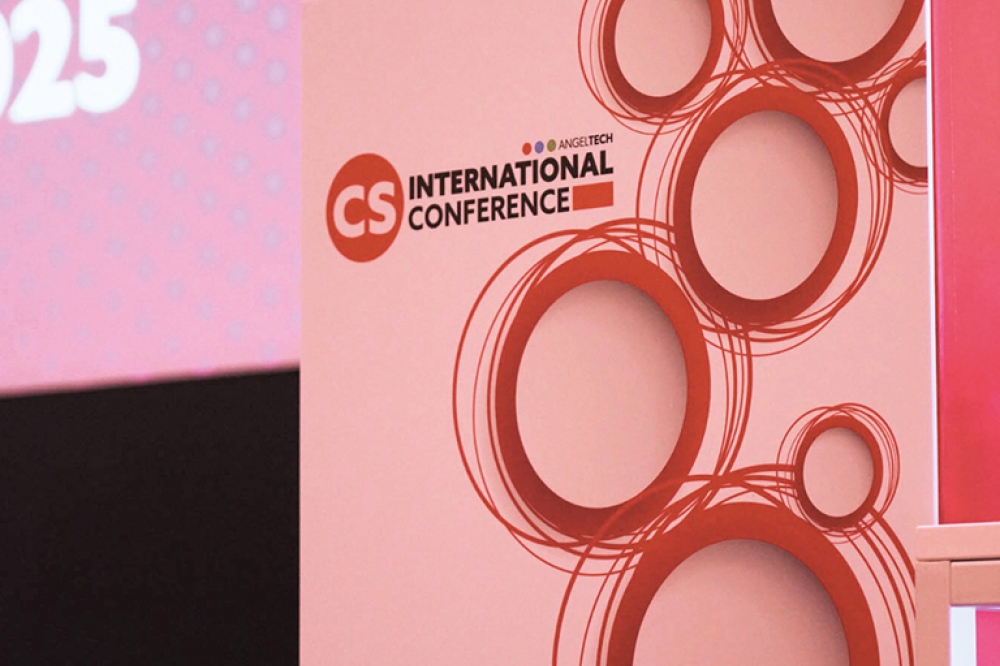
The VCSEL is assured of a promising future, with growth in established markets to continue alongside success in new applications.
BY RICHARD STEVENSON, EDITOR, COMPOUND SEMICONDUCTOR
What’s the dream of every chipmaker? It surely focuses around winning sales in growing, established markets. However, as any particular market may raise and fall, device makers will ideally increase revenue in large and existing markets while pursuing lucrative opportunities in new applications.
Based on a handful of presentations at this year’s CS International, held in Brussels on 16-17 April, this envious state-of-affairs is being enjoyed by makers of the VCSEL. According to Ali Jaffal, Technology & Market Analyst at Yole Group, established markets related to datacomms and smartphones will continue to grow over the coming years, during which time sales will increase in other areas. New opportunities for the VCSEL exist at slightly longer wavelengths that are approaching the ‘eye-safe’ domain, a topic outlined by Julien Boucart, Senior Director Product Management at Coherent, and there are plans to deploy VCSELs to significantly cut the energy associated with the production of batteries for electric vehicles (EVs), an idea championed by Roman Koerner, CTO of Trumpf Photonic Components.
As well as looking at what lies ahead, Jaffal provided some history of the commercial success of the VCSEL. He pointed out that communication applications provided the main driver for this surface emitter from its commercial launch in the mid 1990s until 2017, when Apple started to use this class of laser for face identification and proximity sensing. Strong uptake of this consumer application fuelled a hike in demand for the VCSEL, with production migrating from 100 mm to 150 mm GaAs-based wafers. Jaffal added: “For those of you wondering about 8-inch GaAs diameters, that’s basically for microLEDs.”
Apple has devoted much effort to reducing the size of the notch in the iPhone, as can be seen by comparing Pro Max models of the 13 and 14. For the 14, Apple moved away from the GaAs-based VCSEL to the edge-emitting InP laser. But for the 15, with an even smaller notch, it has reverted to using the GaAs-based VCSEL.
Yole is forecasting growth in established markets, along with many others. The lion’s share of sales will come from the mobile and consumer sector, which will grow at a modest rate from 2022 to 2028, increasing from $798 million to $974 million. Over that timeframe the second biggest market, telecom and infrastructure, will expand from $126 million to $232 million. The only other significant markets are automotive and mobility, rocketing from $4 million to $108 million from 2022 to 2028, and the industrial sector, increasing in value from $44 million to $78 million over that timeframe.
The small growth in the mobile and consumer sector between 2022 and 2028 results from decisions by Apple, the leading consumer of these sources on this sector. Other OEMs, such as Huawei and Honor, have much lower shares and volumes. Ali adds “We are not witnessing major VCSEL adoption from the Android camp in smartphones”.
The GaAs VCSEL is located in the notch of the smartphone – that’s the small, non-display area located at the top of the device.
“We know that the trend is to make this notch smaller,” remarked Jaffal, who questioned whether there will come a time when it is removed altogether. He explained that in 2022, the notch decreased in length to 21 mm in iPhone Pro models, a move that involved the introduction of InP edge-emitting lasers for the launch of the 14 Pro. As InP lasers operate at longer wavelengths than GaAs-based VCSELs, these edge-emitters could be incorporated behind the screen. But for all the 15 models, while the size of the notch has remained, the GaAs VCSEL has returned, with all the facial recognition optoelectronics miniaturised and incorporated within this space.
In the Yole presentation, Jaffal offered a number of explanations for this move by Apple. He pointed out that the supply chain for InP edge-emitters is not as established as it is for GaAs VCSELs, and the cost of the full modules is more expensive. In addition, it is more challenging to incorporate an InP laser beneath the display, than to place a VCSEL within the notch.
Yole Group’s 2022-2028 VCSEL market forecast. Source: VCSEL report, Yole Intelligence, 2023.
New generations of iPhone have also involved changes to the VCSEL-based lidar technology that’s on this smartphone’s rear side. For the family of iPhones spanning the 12 to 14 models, wire bonds connect this laser to the drive electronics. But these wires have been eliminated in the iPhone 15, thanks to the introduction of a flip-chip technology featuring a back-side emitting VCSEL.
All this increased functionality is realised while trimming costs, with the bill of materials falling by 36 percent, according to Jaffal. “Part of it comes from the VCSEL, but also big part of it comes from the image sensor.”
For the second biggest market, telecom and infrastructure, 850 nm VCSELs are used for datacoms over multi-mode fibre, both within racks and between them, with the devices supporting optical links of up to 100 m. Today, VCSELs are being deployed in 800G optical transceivers, with eight devices operating at 100G. Sales are driven mainly by AI applications. In future, datacomms will employ transceivers operating at 1.6T, using eight VCSELs operating at 200G. Such sources are being developed by the leading players, with Coherent already having reported results.
Yole Group is forecasting that the total shipment of VCSELs to the datacom market will increase at a compound annual growth rate of around 14 percent between 2023 and 2029. The majority of the production will continue to focus on 100 mm GaAs substrates, thanks to high yields and small device sizes realised with this format.
As well reducing the energy required to produce batteries for EVs,
VCSEL-based heating trim the space that is required to carry out this
task. Credit: Trumpf
Jaffal also spoke about the market where Yole is predicting the biggest compound annual growth rate for the VCSEL: automotive lidar. This expansion is driven by Chinese OEMs using Hesai’s AT128 lidar, featuring multi-junction GaAs VCSELs. Back in 2018, automobiles fitted with this technology tended to feature a single, forward-facing long-range lidar. By 2028, cars could be equipped with the combination of long-range lidar for front and rear, and short range-variants for left and right; and early into the next decade, they may incorporate as many as six units. Lidar might also be deployed inside the car, to monitor the driver and/or the passengers.
There are a number of options for the light source for lidar. For 2023, Yole has estimated that edge-emitters lasers occupied the largest share of the market, accounting for 45 percent, followed by VCSELs with 39 percent and fibre-lasers with 16 percent. Fast forward to 2033 and Yole forecasts that VCSELs will have crept ahead of edge-emitters, with 45 percent compared to 43 percent, while the share for the fibre laser will have fallen to 12 percent, due to its high cost and bulkiness.
Longer-wavelength opportunities
One of the biggest names in GaAs-based VCSELs is Coherent. It has now shipped more than 200 billion of them, according to Boucart, who pointed that the company’s roots in this technology date back to the 1990s. He explained that one of the commercial pioneers, Honeywell, is now part of Coherent via acquisitions by Finisar and then II-VI; and another trailblazer, Avalon Photonics, came into the company’s fold via Bookham, Oclaro and II-VI.
Boucart remarked that today the primary emission wavelengths for VCSEL products are 850 nm, for use in data communication, and 940 nm, for consumer applications. One of the major benefits of having a 940 nm source is that it operates within a spectral window where sunlight is filtered by the atmosphere. Due to the reduction in the strength of sunlight around 940 nm, low-cost silicon sensors can be used to detect signals produced by the VCSEL.
Engineers at Coherent are now starting to develop VCSELs at longer wavelengths, which overlap other spectral windows where the atmosphere filters sunlight. Moving to longer wavelengths can open up new applications, some of which may invoke concerns over eye-safety that are reduce by heading further into the infrared.
One longer-wavelength VCSEL that Boucart discussed is a 1130 nm emitter, produced on the company’s high-volume 150 mm line. This laser’s output power peaks at about 4 mW, and it has a power-conversion efficiency that can exceed 25 percent. Reliability is impressive, with a time to 1 percent failure of 1 million hours at a junction temperature of 70 °C.
To stabilise the polarisation of the emission, a grating has been integrated into these devices.
A noteworthy attribute of these lasers is their very high current densities, suitable for lidar. Using short pulses, current densities can reach up to 150 kA cm-2, while realising polarisation extinction ratios exceeding 10 dB.
Engineers at Coherent have also produced VCSELs at 1380 nm, by combining expertise in GaAs and InP. Emission at this eye-safe wavelength can be used to measure water absorption. Operating at 25 °C, these VCSELs produce up to 2.9 mW of power, and have a peak power-conversion-efficiency of 10 percent.
Adding junctions to Trumpf’s VCSELs boosts output power and efficiency. Credit: Trumpf
Better battery production
A promising option to help curb climate change is to increase the uptake of EVs. Going hand-in-hand with this, efforts must be directed at minimising the energy required to produce this form of transportation, as this will improve the environmental benefits of this vehicle.
Batteries are a key component in EVs, and producing them requires substantial energy. For every kWhr of battery, its production requires 30-55 kWhr, and in an EV with long-range capability the energy stored by the battery system can total 100 kWhr.
Analysis of the battery production process shows that almost half of the energy that’s consumed is used to power ovens. Heating drives the drying of a thick, wet slurry to create a lithium-containing coating on the thin metal foils that form electrodes in the batteries.
Koerner explained that while the convection-based oven drying process is simple, it has many weaknesses. Efficiency is just 10-20 percent, regulation and flexibility is limited, and the process takes up a lot of space, with ovens accounting for a 60 m-long section in a EV battery factory.
To address these concerns, Koerner and his co-workers are championing a switch to VCSEL-based drying. This move could deliver a hike in efficiency to more than 40 percent, increase flexibility, enable precise regulation, and slash the space required for heating, with a 10 m-long section of the factory adequate for this purpose. The VCSEL-based approach does have a downside, as it increases complexity, but only to what Koerner describes as “moderate”, as no optics are needed.
Heating would be provided by modules around 1 m by 1 m in size, populated by VCSELs with multiple junctions, to increase the output power of these emitters. As the working distance between the VCSELs and the foil is relatively short, there is no need for any optics.
“We can use a wavelength around 980 nanometres, which is quite efficient,” said Koerner, who added: “It’s perfectly absorbed by the metal foil.” He explained that the maximum power density for the heating process is limited by the foil, which must not melt.
Koerner described experiments to verify the approach, with an array of 50 million VCSELs positioned between 150 mm and 300 mm above a moving foil. These VCSELs, with a total output power of 5.4 kW, projected light over a 16.5 cm by 15 cm area, applying a power density to the foil of up to 8 W cm-2. This investigation determined good drying at 8 W cm-2, using an exposure time of 9 s and a belt speed of 1 m/minute. In production, there’s a need for a 60 m/minute belt speed, implying an exposure length of 9 m.
Simulations of the intensity profile produced by the 5.4 kW module, and not involving any optics, have been produced by engineers at Trumpf.
“The centre is very homogeneously illuminated, with an average light intensity of around 2.5 watts per square centimetre,” said Koerner, who pointed out that higher intensities were possible, with considerations governed by how much energy the foil can absorb. The homogeneity of the optical power produced by the module is ± 2 percent. “That’s very hard to achieve with other systems like fibre lasers,” remarked Koerner, who claimed that there are no dark spots in the intensity profile.
Using vast arrays of VCSELs to make modules for heating offers tremendous flexibility. The intensity of heating is easy to adjust, enabling pre-heating of the foil, followed by full heating at a later stage. And if a particular module is not providing enough power, it’s relatively easy to replace it with another.
Like many other VCSEL producers, Trumpf can increase the power produced by its VCSELs by adding more junctions, with electrons cascading through the device. For the heating of foils in an
EV battery production plant, VCSELs could be operated in continuous wave, using relative low current densities and an efficiency close to its peak value.
Koerner shared a comparison of the performance of VCSELs with a single junction and a triple junction. Increasing the number of junctions boosted the power-conversion efficiency from 49 percent to 62.5 percent.
“The downside is a higher voltage, which is sometimes a problem for consumer applications,” said Koerner, before adding that this is not a concern for industrial usage.
Comparisons have been made of the power and efficiency of arrays of 99 VCSELs, with either a single junction, two junctions or three junctions. Adding junctions increases both the total optical power and the electro-optical efficiency, with the peak of the later increasing from around 40 percent to 55 percent when moving from a single junction to a triple junction.
Koerner and his co-workers have also evaluated the reliability of their VCSEL-based heating modules. When delivering a total output power of around 4.3 kW, power drift is below 0.04 percent.
Accelerated lifetime tests have also produced very encouraging results, with VCSELs with a triple junction held at 145 °C running for more than 8,000 hours before their output power falls by 20 percent. For a junction temperature of 70 °C, and a maximum drive current of 7 mA, the mean-time-to-failure is more than 12 years.
Trumpf is planning to launch its laser-based heating modules to market in early 2025. This compelling product should increase the number of applications where the VCSEL can serve, and strengthen sales for the makers of this device.