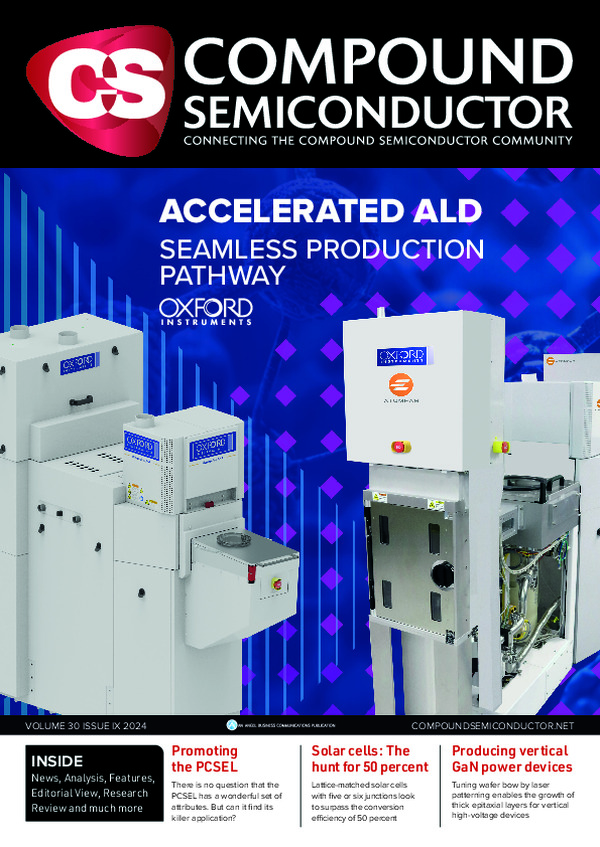
ALD: Speeding the pathway from development to production
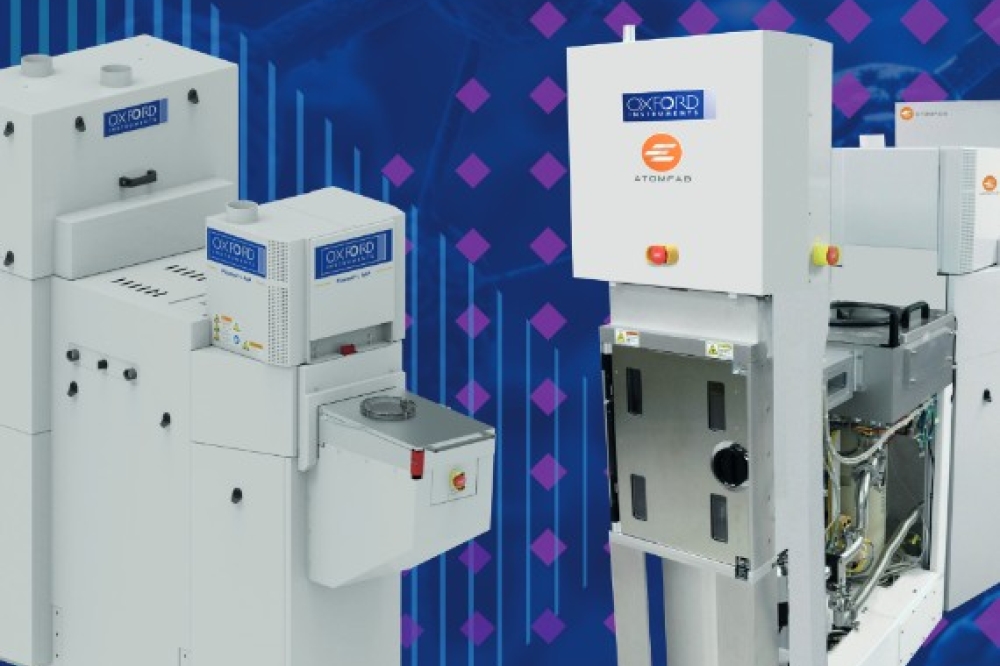
Oxford Instruments’ suite of ALD tools ensures a reliable process transfer from development to production
BY GRANT BALDWIN AND AILEEN O’MAHONY FROM OXFORD INSTRUMENTS PLASMA TECHNOLOGY
In any manufacturing environment, engineers face a critical challenge when moving a process on from prototype or development to volume production. Reproducing results obtained in a compound semiconductor device development lab at scale is not straightforward, due to the fundamental design of development systems tending to differ from that of production systems.
During the device development process, developers want as many options and capabilities as possible, as this widens their process window, while allowing them the opportunity to pull many levers when trying to nudge the process toward a desired result. But having the opportunity to play with superfluous parameters and process knobs is a double-edged sword, threatening to introduce risk in production environments, where more options mean more components to monitor, control and maintain. What’s really needed is to find a way that allows process engineers to benefit from system flexibility in development, without having to compromise production transferability.
At Oxford Instruments Plasma Technology, located on the outskirts of Bristol, UK, we offer a solution to this problem for those using atomic layer deposition (ALD). We have a complementary pair of systems within our ALD product range that combine, in a very innovative way, development flexibility with high-volume manufacturing repeatability and throughput. Read on to discover how we fulfil these disparate goals.
Development with PlasmaPro ASP
Our PlasmaPro ASP, launched in the last 18 months, is designed to give process engineers all the flexibility and capability to develop the industry’s most advanced high-quality ALD layers for research and development, with incredibly high rates and low damage.
Initially, we launched our PlasmaPro ASP into the quantum market. Here it offers a deposition rate that is 2-3 times higher than comparable ALD systems, and provides a process solution for superconducting nitrides, such as NbN and TiN. For those using rival tools, depositing superconducting thin films can take up to 12-15 hours, slowing down implementation in certain quantum applications.
When targeting deposition of these superconductors, we identified an ideal set of processes to launch our PlasmaPro ASP. Our new ALD system offers deposition rates of more than 25 nm hr-1 for NbN, and in excess of 35 nm hr-1 for TiN. Our PlasmaPro ASP provides the capability to tune film properties, such as stress and crystallinity, enabling engineers to dial in the desired properties of their deposited material.
After launching the PlasmaPro ASP with a suite of the most challenging thin films required for any application, we developed additional ALD films. By adding to this repertoire, we are able to give our customers a truly unique platform for ALD development.
130 nm conformal superconducting NbN deposited in 8:1 aspect ratio trench using PlasmaPro ASP. Trench etched using PlasmaPro 100 Estrelas in cryogenic mode.
Production with the Atomfab
Although high deposition rates provided by the PlasmaPro ASP enable a crucial breakthrough for quantum applications, such rates are not usually a critical requirement for ALD process development systems. So why did we design the PlasmaPro to deliver such high rates?
The answer is found in the innovative way that our development and production ALD systems – Atomfab – work together. This duo share the same genetics, including the same patented plasma source design and user interface, referred to as PTIQ. Thanks to this holistic product range concept, our PlasmaPro ASP benefits from a high deposition rate with process flexibility, as well as ease of process transferability from development to our Atomfab production-proven ALD system. By design, this transfer is incredibly straightforward and negates the need for process requalification at the production level.
We have demonstrated that processes developed on PlasmaPro ASP are easy to transfer and replicate on the Atomfab. This feature is tremendously beneficial to engineers who begin by developing a process to deposit an ALD film, before having to quickly ramp up production.
Since 2020 our Atomfab has been production-qualified throughout the world for ALD passivation of GaN HEMTs. When optimised to run a single plasma ALD process on up to 200 mm wafers, this tool provides a monthly throughput of more than 7,000 wafers for oxide passivation, and over 9,000 wafers for a nitride interface layer on GaN HEMTs for each ALD chamber on a cassette handler.
While throughput is crucially important for device fabrication, quality is also vital. Due to this, we are as innovative in our process development as we are in our product development. Our efforts in GaN HEMT device fabrication highlight this broad outlook. Here we have established a market-leading position in both ALD and atomic layer etch, as well as demonstrating a range of processes to control and optimise material interfaces to improve device performance.
One technique that we have developed, yielding excellent results by optimising the material interface, involves a pre-ALD plasma surface treatment, prior to oxide or nitride interfacial layer deposition. The processes work together to reduce the interface trap density and improve the GaN HEMT performance at a significantly reduced cost of ownership – it is more than four times lower in cost than the incumbent ALD solution. All this is accomplished whilst meeting our customers’ expectations in terms of system uptime, mean time to repair, mean time to clean, mean time between cleans, and mean time between assists.
Process flexibility data for PlasmaPro ASP and production quality data for Atomfab below for ALD
Accelerated development
Having the capability, to carry out ALD at high rates on a development system, opens up a world of new opportunities for applying ALD where previously not possible. As well as speeding up development, thicker ALD layers that were previously not thought possible can be developed, and ALD can be considered for new applications with a wider process application window. Once developed on the PlasmaPro ASP, processes can be seamlessly transferred to the Atomfab and ramped to production to enable ALD in high-volume device manufacturing. It is such an advantage to have a suite of products designed to achieve continuity between development and production phases, and arguably this kind of innovation is unique in its category, and with it being available in our technology portfolio, will now be accessible to all ALD users worldwide.