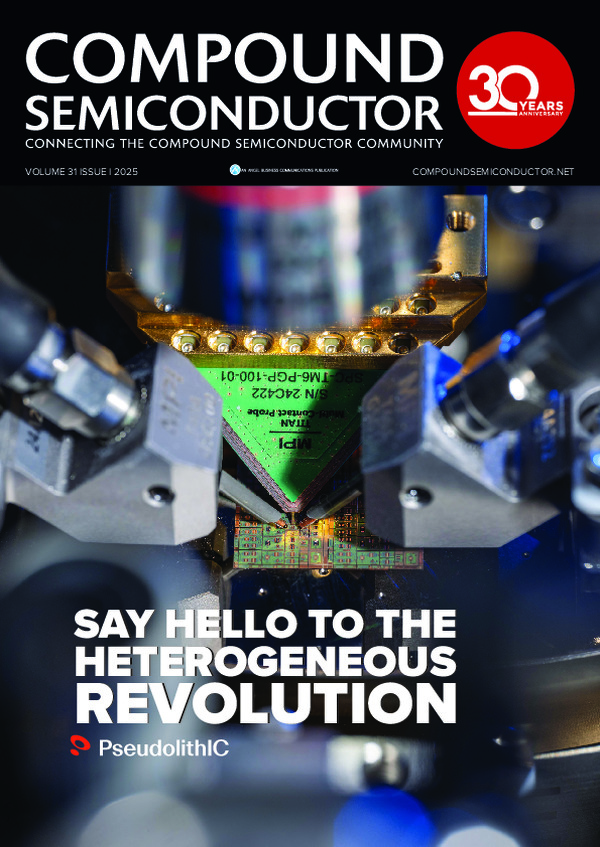
Gaining greater insight into the epitaxial process
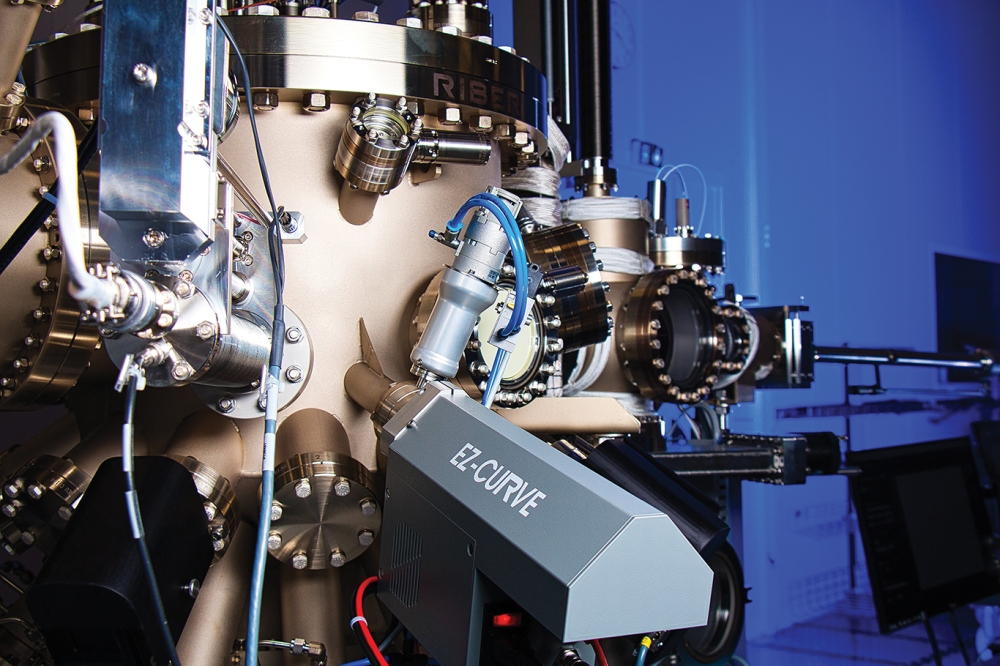
A new generation of in-situ tools enables engineers to delve far deeper into the details of their epitaxial processes.
BY ROMAIN BRUDER, YOURI ROUSSEAU AND ALEXANDRE ARNOULT FROM EPICENTRE, A JOINT LABORATORY BETWEEN LAAS-CNRS AND RIBER
The last 50 years has witnessed a substantial development in semiconductor thin-films technology. At times this advance has been gradual, and other times it’s been disruptive – but regardless of the rate of progress, there has been a continuous improvement in the equipment employed to grow these films. Thanks to this progress, epitaxial tools now have a high level of maturity, essential for supporting today’s semiconductor ecosystem, which is one of the most important industrial markets worldwide.
There is also a strategic aspect to this sector, highlighted by recent, ongoing geopolitical events. Within the global semiconductor industry, a number of ambitious industrial plans are underway, designed to create or strengthen local production capacities and improve supply chain resilience. Against this backdrop, a high production yield is critical to realising a good financial return for these new ventures.
Another trend, occurring over several decades, is a tightening of product specifications, in some cases by orders of magnitude. This reflects ever-more-demanding customer requirements that are behind the need for greater process control.
Some may argue that mastering the fabrication process and decreasing the risk of product non-conformity has always been a pre-requisite for a sustainable business model. However, for many working within the semiconductor industry, these requirements are more important than ever.
Over the years, operando and in-situ instrumentation have emerged in parallel in a variety of industrial fields. Both are increasingly deployed when producing thin films, to enhance the fabrication equipment and ‘augment’ them.
For the growth of thin films, the introduction of
instrumentation began with ‘traditional’ pressure and temperature measurement
sensors. This has now expanded to include optical techniques – both imaging and
spectroscopic – a move that enables the monitoring of more parameters, to
improve the performance and the consistency of the final
device.
Among the various steps necessary to process a raw wafer into a final device, epitaxy and deposition techniques at the wafer scale are critical: being at the beginning of the fabrication process, their success often determines process yield. At this stage, undetected flaws are seeds to future device failure; and any not-detected faulty epi-wafer that’s used in subsequent process steps squanders the production time of the corresponding equipment. Due to this, our company, MBE equipment manufacturer Riber, is an advocate of techniques that will enable ‘Smart Epitaxy’ equipment with advanced capabilities.
Of all the optical technologies that can probe thin films growth, one is particularly linked to the epitaxy of compound semiconductor materials onto substrates of a different nature: the curvature measurement. By quantifying the stress that is generated by a layer deposited onto a substrate, due to dissimilarities in crystalline lattice constants, the curvature measurement provides an accurate indication of a process’ dynamics and its stability. But that’s not all – curvature measurements indirectly reveal information associated with the composition and the thickness of the deposited layer.
Curvature tools have been on the market for several years. However, they have tended to be held back by an intrinsic difficulty linked to their sensitivity, which has often limited their application to highly strained material systems.
Overcoming this limitation is our curvature instrument that features innovative concepts. By improving the sensitivity of the measurement, our novel instrument is a game changer in in-situ real-time curvature measurements, for both epitaxy and a variety of other thin films processes.
Our tool is a culmination of fruitful, patented, collaborative work, undertaken in the joint laboratory project Epicentre, involving our team and researchers at the CNRS-LAAS laboratory in Toulouse. One of the goals of the Epicentre is to accelerate the development of in-situ instruments on MBE reactors to enable machine learning approaches for the epitaxy process.
Magnification inferred curvature
During the growth of epiwafers, stress and strain are
introduced, due to differences in lattice constants and thermal expansion
coefficients. These differences result in a deformation of the wafer, which can
be measured with our instrument that is based on a simple optical phenomenon
known as magnification inferred curvature. For this measurement, the wafer acts
as a deforming mirror, with its curvature altering the image of a bright object
made of white light spots. A camera collects the distorted image, with the
spacing of spots measured in real time.
By comparing spacings in the initial image and the distorted image, our instrument determines the curvature change – that is, the amount of deformation. This figure is related to the stress associated with the film that’s been added to the substrate (see Figure 1).
Figure 1. The magnification inferred curvature principle.
Applying this technique in situ, and monitoring the
curvature of the wafer in real time, allows us to track this characteristic on
a second-by-second basis. Note that while the magnification inferred curvature
equipment has been designed for epitaxy, it is also applicable to other thin-films
processes, such as PVD, CVD, and various vacuum treatment processes, such as
plasma etching and annealing.
We are keen to emphasise the following point: when using this monitoring tool, the curvature measurement need not be a goal in itself, and can rather be a means to follow, in real time, what is happening at the wafer surface. Monitoring may be useful, even when there is no specification related to the curvature of the epiwafer.
Proven results
One of the greatest benefits of our magnification inferred
curvature instrument is its sensitivity. We are certainly not the first to use
curvature to monitor a process, but we offer far greater sensitivity than the
previous techniques employed for the likes of highly strained films and
high-speed processes, where the curvature may vary significantly.
Our solution, emerging from the Epicentre laboratory, offers greatly enhanced sensitivity, thanks to its superior design. Armed with this attribute, our tool is capable of detecting incredibly low levels of lattice mismatch and very subtle phenomena (see Figures 2 and 3).
Figure 2. Curvature measurement during the growth of an
AlGaAs/GaAs superlattice on a GaAs substrate, to form a distributed Bragg
reflector. A lattice mismatch as low as just 0.046 percent can be detected.
There are a variety of situations where our instrument has
proved successful to monitor a process, even if it has not been purposely
deployed to meet a curvature specification. One example is flux calibrations
for MBE growth, which have been performed within 30 minutes. That’s far faster
than the traditional approach of using successive ex situ calibrations
via X-ray diffraction, a process that can last several days. The upshot is
significant savings in time and money, when MBE is used for high-volume production.
Another example is associated with automatic lattice-matching during MBE growth. This provides control of the composition of a ternary or quaternary alloy in real time to match the substrate lattice. By using the curvature signal as an input parameter, process engineers can instigate closed loop feedback on a cell temperature or a valve position to ensure that the grown layer always matches the underlying substrate. Taking this approach to growth minimises dislocations and enhances material quality.
The same approach can be adopted for stress engineering. When differences in thermal coefficients between the substrate and the film induce stress, it may be best to grow a layer with a controlled and desired curvature, a task aided by our instrument. Thanks to its exceptional sensitivity, once growth is over and the wafer cools down to room temperature, its curvature returns to its initial, pre-process level. This ensures that when the wafer’s removed from the deposition tool, it’s free from any additional bowing. That’s a great asset when subsequent processing steps demand flat, non-bowed wafers (see Figure 4).
Our tool has already seen widespread deployment. It has supported MBE with various substrates, including GaAs, silicon, GaSb and InP, and it has aided the growth of III-Vs, II-VIs, and oxides. In addition, it has been used during studies of the nitridation of silver films, realised by PVD.
Figure 3. Growth of InGaAs quantum dash in an InGaAsP
barrier. The growth of each quantum dash lasts just 4 s, and leads to a
modification of the curvature, clearly seen as steps in the signal. Courtesy of
A. Wilk, III-V Lab.
Curvature is just the beginning
One of the features of our instrument is its communication
module. Users can interface this with a lab management system, and integrate
curvature in a large-scale monitoring approach. It’s also possible to use the
curvature data for machine learning purposes.
We are developing specific software modules to compare traces to reference data, and to simulate, a priori, the trace of a theoretical structure. These modules will help to get good structures from the outset, and will accelerate growth recipe optimisation.
Figure 4. Stress engineering thanks to a curvature measurement. The growth process is carried out at a high temperature, with a fixed curvature slope that is calibrated with reference data and used as a PID input to enslave the indium cell temperature. When the process stops and the wafer cools down, the curvature signal enables monitoring of the wafer’s thermal relaxation, which gets back to its initial curvature at room temperature. The processed wafer is then as flat as it was before the process, with no added bowing. The X-ray diffraction plot shows a single peak for the substrate and the film, indicating a perfect match of lattice parameters.
Efforts at our Epicentre are now being directed at coupling our new curvature instrument to reflectivity or temperature monitoring. The promise of combining these different technologies in one platform is that it will offer great insight into non-equilibrium phenomena involved during growth. It is expected that the collected signal will help to finely tune the process and optimise the overall yield. In this scenario, it’s possible that ex situ characterisation will only be required for periodical control.
We are confident that this new generation of instruments will inject new life into the capabilities of in-situ instruments, by introducing new concepts that enhance sensitivity and flexibility. Thanks to advanced integration into the manufacturing equipment software, our new instrument can revolutionise growth tools, by augmenting their capacity to monitor and correct themselves. As the process is controlled in real time, deviations will be eliminated, leading to a dramatic hike in yield and far more efficient use of manufacturing equipment.
While the magnification inferred curvature is only a first building block towards smarter monitoring of growth processes, it will definitely open a new era for compound semiconductor manufacturing equipment.