BluGlass rises to MOCVD challenge
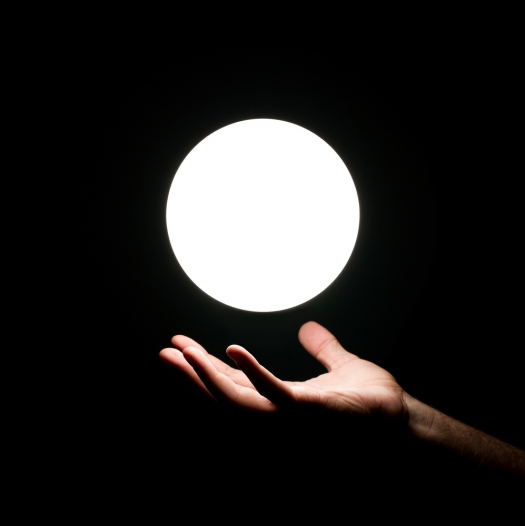
From LEDs to power electronics, BluGlass's plasma CVD process is set to ease fabrication and offer a cool alternative to MOCVD, reports Compound Semiconductor.
Remote plasma CVD is getting ready to challenge MOCVD in LED and power electronics fabrication.
Following last year's hefty injection of Aus$3 million (£1.67 million) in federal funds to demonstrate high efficiency, cheap GaN LEDs, Australia-based semiconductor process developer, BluGlass, is now revealing results.
In July, this year, the company claimed its best ever light output from a p-GaN layer, grown via its low temperature remote plasma CVD process (RPCVD), onto a MOCVD partial LED structure. And earlier this month, the company unveiled a scaled-up version of its RPCVD system that's set to accelerate the development of brighter LEDs.
The company has spent nearly a decade developing its low temperature process to grow GaN, and more recently, p-GaN layers on MOCVD structures. To achieve low temperature growth, the company replaces the ammonia source of an existing MOCVD system with nitrogen gas, passed through an electrical coil to generate a plasma.
Directly supplying nitrogen via a plasma allows the company to deposit layers at relatively low temperatures. Actual figures remain elusive, but BluGlass's aim is to match the temperatures used to grow MOCVD multi-quantum wells.
While the company has worked with Emcore/Veeco systems in the past, this time round it has retrofitted a larger Thomas Swan/ Aixtron system. As Bluglass chief technology officer, Ian Mann, says: "We haven't been trying to build our own system from the ground-up but, more simply, have been retrofitting the most common systems out there."
"This latest reactor is well known, is economical to run, and will be capable of generating a single 8 inch wafer," he adds.
To date, BluGlass has been primarily working with two inch sapphire and silicon substrates, but Mann and colleagues hope the new system will help to prove RPCVD at larger wafer sizes. "The reality is, for silicon, two inch substrates aren't relevant in the market and most people are going to silicon at larger scales," he says. "Thanks to our lower temperatures, we aim to have better control over cracking and bow in these larger wafers and we've had considerable interest in how this system is going to perform at these wafer sizes."
Mann also hopes the latest retrofit system will tackle the crucial issue of scaling. As he highlights, he and colleagues are always asked whether or not their plasma-based CVD development-sized systems can reliably scale to production processes.
"This system is our answer to that question," he says. "We aim to convince customers that we have taken what we've been doing on the smaller system and repeated this here, while at the same time improving performance."
And as Mann asserts that the latest Aixtron system isn't a world away from the full-scale systems populating today's production floors."The technology isn't dramatically different; the main difference is that production systems today are larger" he says. "So we feel quite comfortable that our latest system isn't far away from the final platform we are trying to develop."
With the second larger system installed, the BluGlass team is ready to scale up its RPCVD process for LED and power electronics markets [BluGlass].
Research to date has been primarily focused on depositing the RPCVD p-GaN layer onto the MOCVD-grown multi-quantum well layers. As Mann explains, the growth initiation of this layer and subsequent growth had proven a real challenge, so he and colleagues developed their existing reactor to operate with a higher density nitrogen plasma.
"This enhanced plasma system has formed a core part of our intellectual property and has proven critical to good growth," he says. "The way the MOCVD ends becomes the beginning of RPCVD growth, so we've made some subtle but simple changes to the final MOCVD [processes], which has helped ultimate device performance."
And with the growth of RPCVD layers on MOCVD templates in place, researchers are keen to use RPCVD to grow full structures, in much the same way as MOCVD is used to grow entire structures. This second larger system can only help.
"We've been very interested in trying to grow multi-quantum wells and p-GaN layers together in the same chamber," says Mann. "We've been very active on our p-GaN research, but with the larger system up and running, we can afford to push our research programmes in different directions, and this is something we are keen to put to the test."
Sapphire and silicon
But it's not all about silicon. As Mann emphasises, BluGlass's technology is intended to be 'substrate-agnostic' and right now, the bulk of the LED market is still fabricating structures on sapphire. Indeed manufacturers have been keen to find out exactly what the company's low temperature RPCVD process can do for multi-quantum well growth.
"With the low temperatures, you can incorporate more indium into the multi-quantum wells, which lets you fabricate LEDs emitting at longer green and yellow wavelengths," he says. "Developing quantum well technology has always been on the cards, and is funded by company's federal Grant. Our second system provides more opportunity to explore such avenues."
Crucially, BluGlass also intends to take its low temperature growth process to power electronics markets. As Mann highlights, almost all HEMT structures are grown on silicon, so manufacturers are grappling with many of the same issues as LED players, a fact he and colleagues hope to exploit.
"There is still this cracking and bowing of large wafers due to lattice and thermal mismatches between silicon and GaN," he says. "So a low temperature GaN on silicon platform could help power electronics manufacturers as well as LED [suppliers]."
And of course BluGlass's latest system - with its 8 inch wafer capacity - opens more doors to these markets. "Both GaN-on-silicon markets are looking towards larger substrates, LED [players] are looking at 8 inch sizes and power electronics developers are looking at six inch substrates," says Mann. "These people are expected to move to 8 inches in the future."