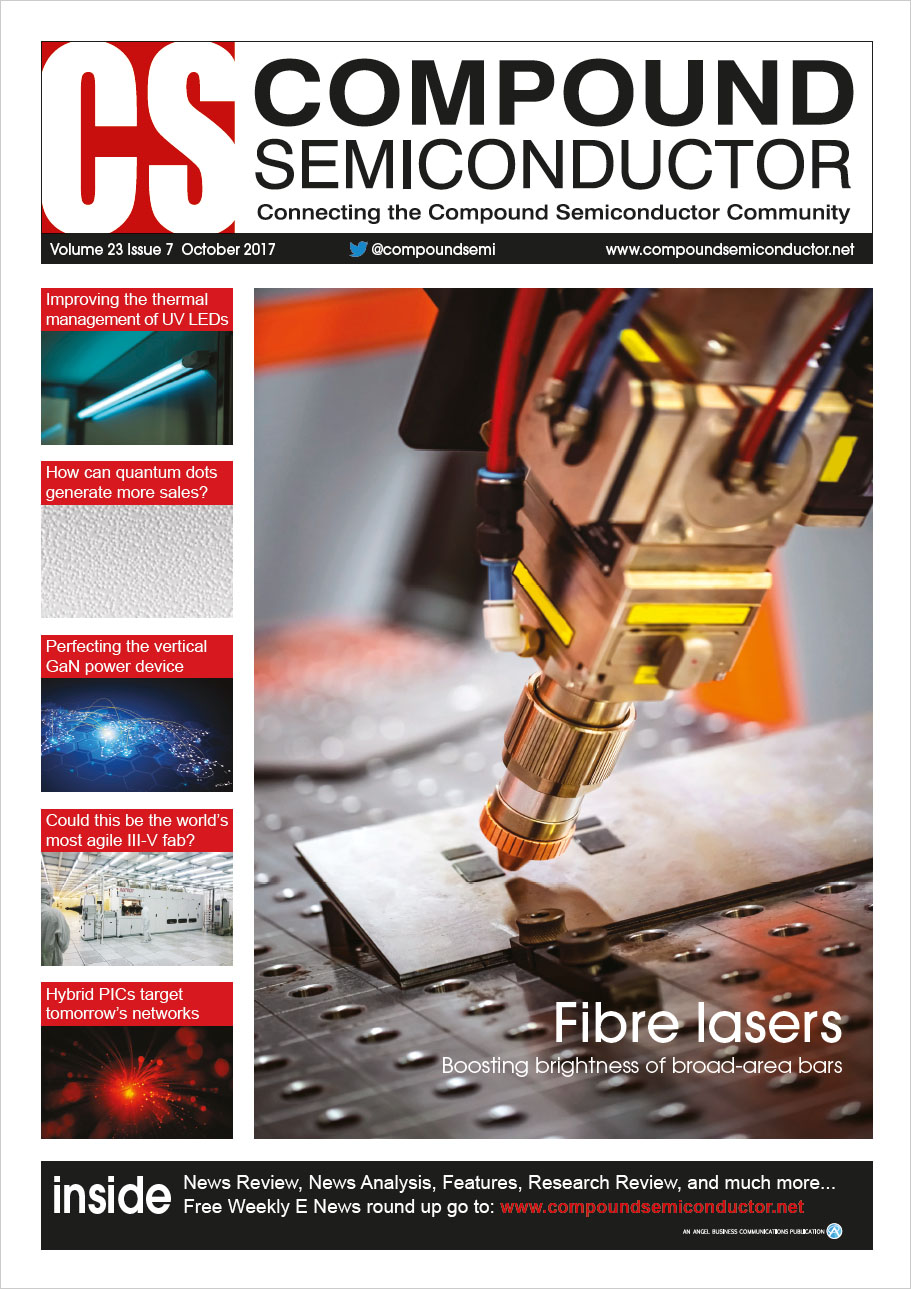
Accelerating GaN growth
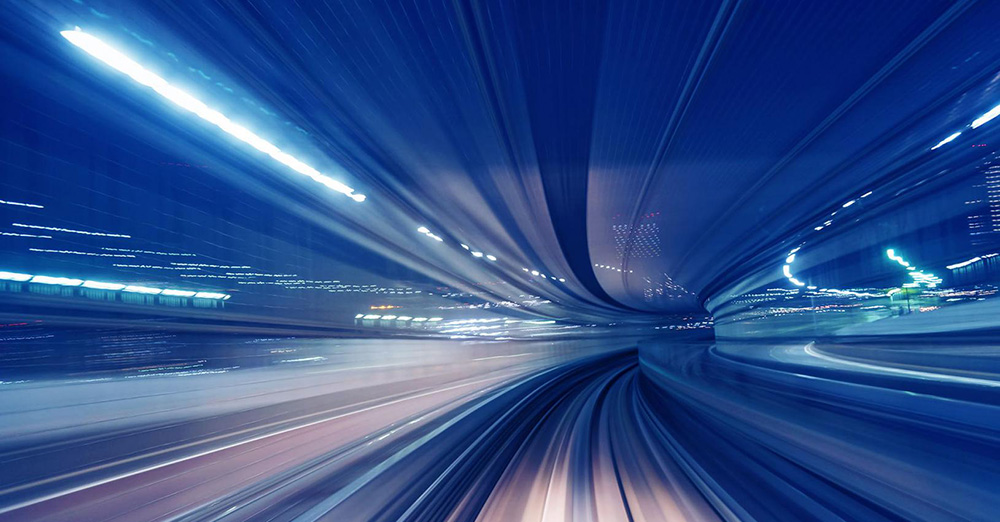
A gallium evaporator made from a porosity-controlled ceramic holds the key to very high GaN growth rates
THE GROWTH of sales of GaN power devices is held back by the absence of low-cost, large diameter, high-quality bulk GaN substrates. Today, the commercial production of GaN substrates produces material that is expensive, limited in size and availability. But that could all change, thanks to the speeding up of a novel gas process developed by a team at Toyota Central R&D Labs.
This team from Japan has just delivered a five-fold hike in growth rate by replacing a conventional crucible with a porosity-controlled TaC ceramic that provides a significant increase in the surface area of the gallium source.
GaN is grown by the team's halogen-free vapour phase epitaxy process, through the reaction of evaporated gallium and ammonia.
As hydrogen gas is the only by-product, growth runs can be longer than they are by HVPE, which is cut short by the generation of ammonium ash.
When the team were using a crucible for the GaN source, heating to 1590 K produced a gallium evaporation efficiency of only 30 percent.
Although higher efficiencies were possible by increasing the temperature and decreasing the pressure, these options were not pursued, as they would compromise the reliability and durability of the reactor components.
A fast, low-cost GaN growth process could help GaN power electronics to grab market share from the incumbent silicon devices
That's not the case when growing at around 200 μm/hour. In this regime, the GaN layer is mostly a single crystal, with relatively high quality, according to X-ray diffraction measurements.
The growth conditions at very high growth rates still need to be improved, as they currently lead to the creation of polycrystalline regions.
Efficiency of evaporation with the six-fin evaporator is estimated to be about 80 percent, a value that is believed to be very close to the practical limit.
To avoid this limitation, the team have concluded that the evaporator should be designed so that the fins cover the entire nitrogen flow channel in a manner that does not lead to a local saturation of the gallium vapour pressure.
The researchers also note that the level of the increase in growth rate is very similar to that for the increase in feed rate, indicating that it is the gallium feed rate that limits the growth rate for GaN. The feed rate is limited by the local saturation of gallium vapour pressure.
One implication of these values is that the growth rate is not just determined by the surface area: the evaporators have surface areas that are almost identical, but their growth rates are markedly different.
Growth rates of 481 μm/hour and 764 μm/hour were realised with the eight-fin and six-fin reactors, respectively. These values equate to an increase in GaN growth rate by a factor of 3.5 and 5.5, respectively.
TaC ceramics with pores that have diameters of 1-10 μm and a relatively high porosity of 2-5 percent formed the building material for two evaporators: one with eight radially aligned fins with an outer diameter of 30 mm and a height of 36.5 mm; and a second with six fins with an outer diameter of 35 mm and a height of 36.5 mm.
Instead, the team have focused on increasing the evaporation rate with the introduction of a fin-shaped evaporator, which uses a capillary force to draw molten gallium through pores of the TaC ceramic.