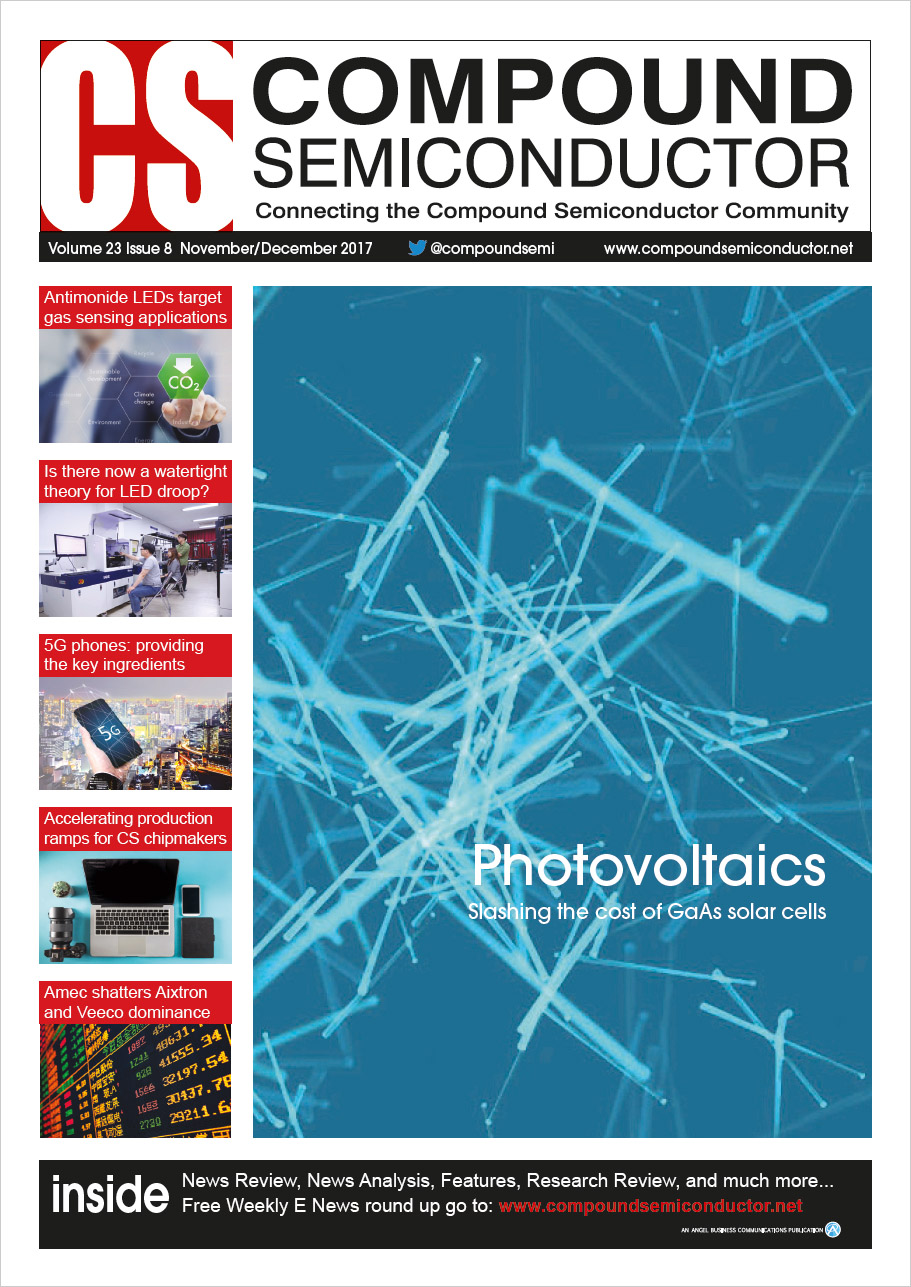
Accelerating the production ramp
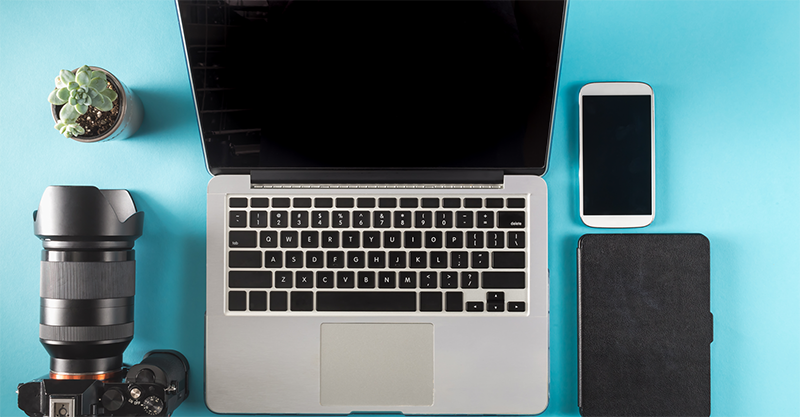
When customers come knocking at your door, wanting massive quantities of your products in just six months, can you quickly react, change, and deliver by the deadline? By Mario Faria, Ilia Kaplan, and Ariel Meyuhas from the Max Group
Marketing campaigns encourage us to go out and buy the latest gizmos and gadgets. For those of us that want to have the latest laptop, every two years a new model will come out and tempt us, sporting attractive functions and better performance. New generations of camera come around even faster, at typically every 18 months, while new iPhones are launched every year "“ and right now, even faster than this "“ and for Androids, less than a year is already the norm.
The rapidity of launches of electronics goods, often too much fanfare that drives healthy pre-orders, puts a great deal of pressure on component suppliers. They include the makers of compound semiconductor chips used for connectivity that have to ramp production fast without compromising product margins. And they cannot afford significant time-to-supply delays, as this could jeopardize their position as a top-tier supplier, by missing out on contracts in years that come. Avoid all this and it is still possible to run into problems: companies tend to deal with shorter cycles by over-stocking finished products, and when these don't sell, profit margins head south.
The good news, however, is that with a carefully planned approach it is possible to avoid all these pitfalls. And one manufacturer of compound semiconductor chips has recently done just that, thanks to support by our team at The MAX International Engineering Group, a company based on Old Tappan, NJ, that has expertise in operations improvement, new facility design and build, and management consulting. After working together, we ramped the factory output by 250 percent.
Figure 1: Daily detailed shift schedule for Production Managers
Our expertise has taught us that manufacturing agility is critical to achieving shorter time-to-supply cycles in environments where manufacturing takes place alongside development "“ a typical situation in a compound semiconductor fab. To realise sufficient manufacturing agility, often a culture change must take place, with a shift of emphasis away from a development-centric mentality, to one that focuses on manufacturing-centric practices.
Ideally both cultures are already co-existing during the development and ramp-to-volume phases in manufacturing. But if they are not, we work with clients, taking them on a managed and expedited path to benchmarked operational excellence and significantly shorter time-to-supply cycles.
During the last ten years, we have worked with many compound semiconductor manufacturers, deploying approaches to increase manufacturing agility. These methods focus on addressing the three key pillars required for any successful, high-volume compound semiconductor chipmaker: operational practice, engineering practice and organisational structure. Excelling in all three areas produces pillars that provide a foundation for growth, flexibility and a manufacturing-centric infrastructure. The result is a cohesive team, aligned around applicable key-performance indicators, that can create a very highly focused organisation that is underpinned by precision of teamwork, standard work methods and execution in planning, operations, and engineering.
Increasing operation efficiency
Our first step, associated with the first pillar, involved increasing the operational efficiencies of the compound semiconductor chipmaker. We began with this, because operational changes yield faster results than activities related to engineering or organizational changes. We assessed, made recommendations and implemented new approaches in many different areas, including those associated with: key-performance indicators; roles and responsibilities; work-in-progress management; factory management and supervisory effectiveness; line balance and dispatch; industrial engineering practice benchmarking; shift escalation, rounds, and passdowns; break management; hot and hold lot policies; and six-sigma and quality policies.
Figure 2. Dynamic Snapshot of Tools Idle with WIP "“ Highlights Equipment ready to process but missing inventory
All these areas are covered by our highly renowned and successful SuperKit tool, which we have perfected during its use in over 60 fabs all over the world. Using SuperKit, we were able to identify several opportunities to improve the management of the fab, and could recommend how to implement the solutions. In addition, we could manage the implementation of many of these suggestions for improvement.
To start, we established a shift agenda for supervisors and a clear production meeting agenda to followed by a detailed description of frequent routines to monitor constraint areas and toolsets. Figure 1 illustrates an example. Our customer was busy hiring and training new supervisors, operators, and technicians to be able to support their ramp. They relied on organically grown knowledge on how to run shifts, production meetings, and setting expectations on the production floor.
Figure 3. The use of MAX Group's Precision Maintenance Programs enabled a 24 percent improvement over a 12-month period in the output of critical PVD toolsets.
Gaps were discovered, highlighting little continuity work and standard work from shift to shift. We also observed that supervisors managed their shifts to their personal style and lacked common prioritization to daily key-performance indicators, and production meetings were not efficient and served as a forum to present information to management. All of these issues required change, with our SuperKit providing the ideal tool.
In any strong manufacturing organization, the use of key performance indicators drives a level of expectation. In the compound semiconductor fab we recently worked with, we focused efforts on implementing indicators that matter to those that are operating and maintaining the tools, and characterising wafers and devices. Here, key performance indicators are easy to establish, and they help to set a higher level of efficiency when it comes to manufacturing performance. In this case, the focus was directed at wafer output, with critical toolsets coming under scrutiny, using key performance indicators to monitor overall equipment effectiveness (OEE) losses and identify opportunities for improvement within work-in-progress inventory management.
Improving engineering and maintenance
Following our efforts at improving operational practices, we turned our attention to the second of these pillars, engineering and maintenance. In these realms changes are harder to implement, and the benefits take longer to appear. Working with the compound semiconductor chipmaker, we considered the availability of equipment for some critical process toolsets that are bottlenecks to production. Our efforts involved measuring and improving maintenance effectiveness, using our own Precision Maintenance Programs.
The two outcomes we sought were to increase the equipment availability, and to increase the coefficient of variation of availability "“ that is, the variability of availability. Success on both fronts led to higher output on critical PVD toolsets in the fab (see Figure 3).
Another way that we looked at availability involved applying our own scoring methodology specific to every preventative maintenance event. This gives the Perfect PM Score, or, for short, the P-Score. The P-Score categorizes planned maintenance work as follows: preventative maintenance planned or unplanned, target interval between preventative maintenances sustained or not, event achieved first time right or not, failures right after the event or not, and next planned event performed per target or not. For root cause analysis we used a 5Y methodology, a known method to derive cause-and-effect. We would drill-down to every category, and scrutinise cause and effect, before determining the corrective actions needed to deliver continuous improvement.
Figure 4. Fab Management Assessment: Highlights skills and alignment across organization, focus on gaps (red) as weakness of teams.
We have also made several recommendations related to equipment and maintenance practices. These vary from improving the engineering and technician skills of fab maintenance teams to the successful management of spare-parts; and the efficient leadership of the site, to take it from an R&D/engineering-centric mindset to one emphasizing high-volume manufacturing. To ensure effectiveness, we worked with the fab when defining the most important items for our team to focus on. Together, we developed a matrix of activities for us to deliver best-practices, and make sure that the fab adapted within its culture.
Enhancing organisational effectiveness
The third and final pillar for improving the capability of a fab to ramp production quickly and successfully is to excel with organisational effectiveness. We adopted a four-pronged strategy to ensure excellence in this regard. This involved: identifying organisational strengths and weaknesses; evaluating the leadership skills of the fab management team and making recommendations for improvement; suggesting a set of metrics to be adopted by senior management; and defining a roadmap to transform the organization from R&D to high-volume manufacturing "“ that is, to undergo a cultural change.
To undertake this assessment, we held discussions with the site manager, six senior managers, 14 mid-level managers, supervisors and individual contributors. We also observed many different types of meeting and witnessed decision-making processes and responses crisis and conflicts. What's more, we reviewed samples of key documents, including project plans, organisational charts, repeatability and reliability studies, and roadmaps.
Figure 5. Organization Agreement Matrix: A know methodology to identify where the organization lies and where it should be targeting to be based on the future state (ramp)
The company that we were working with fell short of this and suffered from weak and absent project management practices, which are needed to provide accountability and bring discipline to the organization. They are by no means alone, as many compound semiconductor companies focus heavily on R&D, while neglecting project management, a key requirement for successful ramping of production.
The final piece of the third pillar "“ organisational effectiveness "“ involved an assessment on project management skills. Successful chipmakers are good at managing and executing improvement activities.
By and large, those leading the compound semiconductor fab agreed on what they wanted. However, they couldn't identify a clear path to achieving this. Executing on this from required a combination of power tools, such as coercion and fiat, in conjunction with management tools, such as training and the use of measurement systems. Drawing on all of these tools enabled a move from agreement to cooperation.
A key finding that emerged from all of this effort is that the focus of the compound semiconductor fab was on R&D. That's not surprising, as it is a typical position for most compound semiconductor companies, which will eventually evolve from having an emphasis on technology to a balance between R&D and manufacturing. To drive a shift in culture, we placed the chipmaker into an agreement matrix, which is a chart that measures leadership, power, management, and cultural tools (see Figure 4). This chart helps us to identify where organizations fall short and where they should be targeting improvement. This revealed that the best way forward would involve the use of cultural tools (see Figure 5).
Changes implemented by the compound semiconductor chipmaker that we worked with will serve it well in an industry that is sure to grow, but will face challenges, as the release cycles for phones, tablets, laptops and cameras get shorter and shorter.
Figure 6. Project Results: 250% increase in wafer starts
By pairing with us, our client has increased the factory output by 250 percent (see Figure 6). This was accomplished during an 18-month period, where efforts were not just driven by the work with us, but also included a combined effort program to reduce risk. Ramping production faster is not the only beneficial outcome of our efforts with the chipmaker. They have also been able to trim their inventory level by 15 percent, benefit from sustainable or faster cycle times, and undertake a cultural change roadmap to sustained factory expansion while realising manufacturing capabilities never seen before.
R&D is a very important part of any compound semiconductor company "“ but to exploit the breakthroughs that are made there, there must also be an emphasis on implementing the best manufacturing practices, built on the three pillars of good operation practice, strong engineering practice, and having an effective organisational structure.