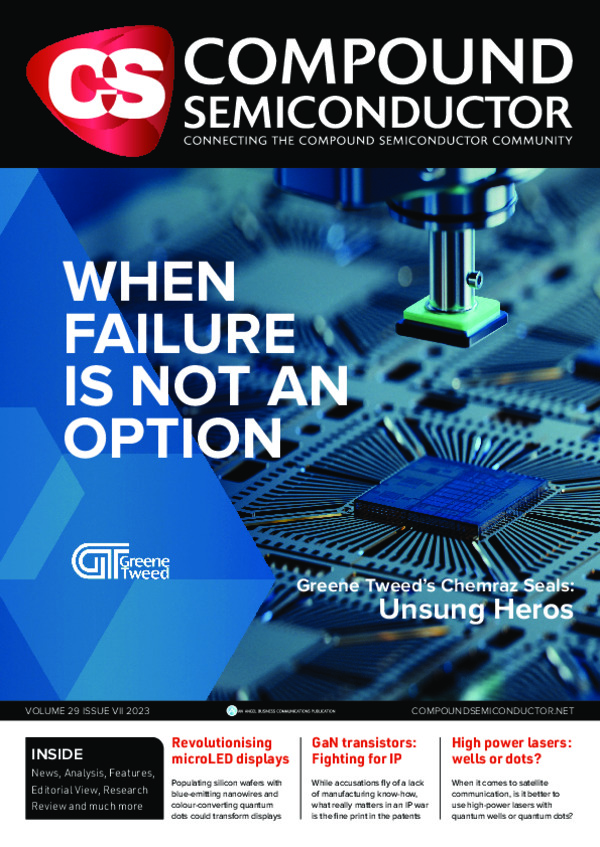
When failure is not an option
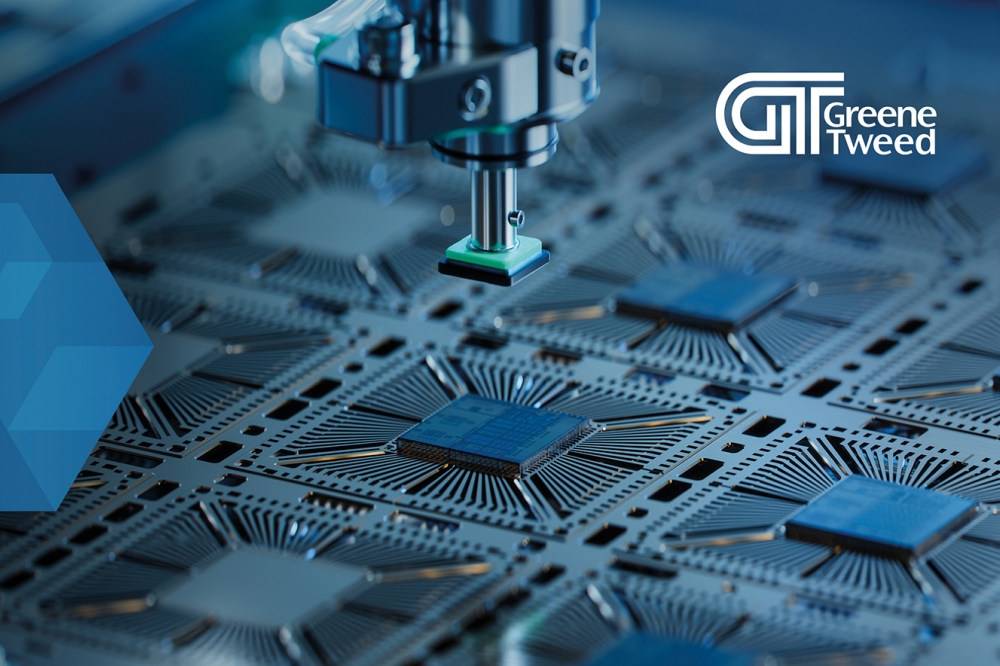
Greene Tweed engineers sealing solutions and structural components that outperform and outlast in the world’s harshest semiconductor manufacturing applications.
BY NICK MCNEAL, THYAG SADASIWAN AND PRAGATI VERMA FROM GREENE TWEED
Electric vehicles. Sensor-embedded Smart Devices. 5G and 6G connectivity. Quantum computing. What do they all have in common? They require chips made from compound semiconductors, handling the high voltages and powers that silicon can’t.
As the demand for compound semiconductors soars, what do the manufacturers of these devices need besides more deposition and etch tools, and more substrates? It’s a steady supply of some inconspicuous yet indispensable components that are critical for manufacturing new generations of compound semiconductor devices.
Chemraz Seals: Unsung Heroes
At Greene Tweed, we engineer sealing solutions that outperform and outlast in the world’s harshest semiconductor manufacturing applications. They are a remarkable example of what we do, working behind the scenes to empower the intricate machinery of chipmaking. For 160 years, we’ve been equipping critical sectors with materials and engineered components that deliver certainty during crucial operations.
For instance, our perfluoroelastomer (FFKM) Chemraz o-rings and sealing solutions meet the critical demands of modern chip fabrication. They are renowned for preventing contamination, while withstanding aggressive chemicals and extremely high temperatures.
For decades, we have been at the forefront of the complex FFKM production process. These high-performance materials need specific ingredients. Due to this, disruptions can occur when just a single ingredient is in short supply. During the last couple of years, an unexpected and tumultuous industry-wide supply crunch had gripped several FFKM ingredients. Exacerbating this situation, this supply shortage coincided with a global surge in the demand for chips. As a result, FFKM material was in short supply, just at the very moment when semiconductor manufacturers needed it to go into overdrive. This snared the FFKM industry in the epicentre of a perfect storm, where supply delays threatened to impede semiconductor availability and the resultant economic recovery.
If the recent silicon chip shortage has taught us anything, it’s the need to fortify supply chains for the components that are powering the intricate machinery of semiconductor manufacturing. Chipmakers are now acutely aware of how dependent the semiconductor industry is on FFKM seals, especially as they turn to more demanding processes that rely on ultraclean processing.
Greene Tweed was the first company in the US to use cleanroom manufacturing to produce our sealing solutions. We pioneered this move, because we intimately understand the significance of ultraclean operations in the semiconductor industry. We know that our seals have to perform in the harshest environments of modern semiconductor fabrication processes, where they are critical to improve uptime, reduce contamination and boost wafer yield.
Where second best isn’t good enough
Over the last couple of years, the demand for materials used to make SiC and GaN power devices has been soaring. As a result, sales of compound semiconductor substrate materials are set to more than double by 2027, according to Yole Intelligence. This French market analyst forecasts that the compound substrate material market will grow from $945 million in 2021 to $2.3 billion in 2027, equating to a compound annual growth rate of 17 percent.
To meet the growing demand for compound semiconductors, chipmakers need to step up manufacturing capacity and strengthen their supply chains for components such as FFKM seals, which are critical to manufacturing these chips. As a global leader in seals based on FFKM elastomers, we know second-best seals aren’t good enough in an industry as complex and challenging as semiconductor manufacturing. So, we have taken action to ensure a steady supply of our sealing solutions. This allows us to meet the burgeoning demand, while ensuring industry resilience and minimising the impact of any future disruptions on the supply of FFKM materials.
We realise that the dynamic and fast-growing landscape of the compound semiconductor industry demands strategic planning and foresight. To enable our customers to do this, we are proactively taking measures to create robust business continuity plans and ensure a steady and uninterrupted supply. Our efforts began by conducting comprehensive risk assessments, identifying vulnerabilities, and developing contingency plans to mitigate potential disruptions. Following this deep exploration, we have rolled out four major initiatives. They will help us navigate this turbulent terrain, circumvent future disruptions, and secure a regular supply – all critical initiatives for helping us to drive our semiconductor customers’ continued growth and success.
Our first initiative has been the building of strategic stockpiles of critical raw materials to prepare for the anticipated upturn. While securing raw materials is essential, it’s just one aspect of our multifaceted approach to ensuring supply. Our scientists are innovating, developing new products and reformulating existing ones to prepare for the ever-evolving regulations and shifting market dynamics.
We are proactively identifying risks from ingredients that are supply-constrained and mitigating them with more readily available feedstock materials. At the same time, we are working with supply chain partners to determine the potential impact of government reviews and supply crunch on their materials, chemicals and production processes. Simultaneously, we are working with our customers to develop and validate alternative compounds with superior technologies and significant benefits.
The second initiative is that while we are reformulating and developing new products, we take proactive measures to diversify our supply chain and reduce the risk of overreliance on a single supplier or region. We realise that setting up multiple FFKM factories is too capital-intensive and might not be feasible for our suppliers. That’s why we are leveraging multiple suppliers to build a resilient, adaptable supply chain that’s better equipped to navigate the challenges of an ever-evolving semiconductor landscape.
To do this, we are developing equivalent products that serve as alternatives to the original ones. We are carefully selecting compounds and sourcing raw materials for two equivalent products from different suppliers located in separate countries. For example, we are augmenting our supply chain by adding Chemraz G57. This is equivalent to Chemraz 657, and provides excellent plasma resistance in a variety of aggressive chemical environments.
Our third initiative is to spread our manufacturing footprint. We are strategically setting up factories in new locations all over the world, a move that helps us bring supply chain stability to our semiconductor customers. Our latest upcoming manufacturing facility is in Cheongju-si, Chungcheongbuk-do, Korea. Expected to be ready by the middle of next year, initially this facility will be dedicated to our highest-performing elastomer Chemraz product line, specifically formulated for semiconductor applications. By decentralising production and sourcing, we will be better equipped to manage supply crunches, overcome production bottlenecks, and maintain consistent deliveries to customers.
The last of our four key initiatives, which is being implemented in tandem with the expansion of manufacturing capacity, is a significant step-up in inventory optimisation. We are now building the right inventory, to meet future demand with industry-leading lead times. Coupled with our new facility, this initiative will help us to grow our capacity and capability, to better support the global demand for our products and bring enhanced supply chain stability to the semiconductor industry.
Back on track
The results of building our supply resiliency are already evident. We have been able to restore the standard pre-disruption level lead times that our customers enjoyed before geopolitical and regulatory events caused an unprecedented FFKM supply crunch. Getting supply times back on track is not only testament to our resilience, adaptability, and customer-centric approach – it’s also critical for supporting robust demand from the makers of compound semiconductor devices.
As we continue to forge ahead on this transformative journey, we are committed to keeping customer satisfaction and supply chain stability at the core of everything we do. We understand that our high-performance Chemraz seals do what other seals can’t do, and that the timely delivery of our products is essential for our customers’ success and continued growth.
Together with our customers and partners, we will continue to shape a resilient future that thrives on innovation and a custom collaborative approach that delivers certainty for compound semiconductor manufacturers’ fast-expanding crucial operations.
All your semiconductor sealing questions, answered
Do you need an elastomer o-ring or sealing solution that’s built to withstand aggressive liquids, gases, and plasma at the extreme temperatures found in the harshest semiconductor applications? Here are answers to the key sealing questions facing semiconductor manufacturers…
What kind of seals work best for semiconductor manufacturing processes?
Perfluoroelastomer (or FFKM) sealing material, known for its exceptional resistance to aggressive chemicals, extreme temperatures and plasma environments, is ideal for a manufacturing process as aggressive as semiconductor fabrication. Greene Tweed offers Chemraz sealing solutions, known for their exceptional resistance to extreme temperatures, chemicals and plasma environments.
What sets Greene Tweed’s Chemraz sealing solutions apart?
At Greene Tweed, we take pride in our Chemraz sealing solutions that are engineered to outperform and outlast in the world’s harshest environments. For 160 years, we’ve equipped critical sectors, including the semiconductor industry, with materials and engineered components that perform – no excuses, no exceptions. With the broadest temperature range and unmatched chemical resistance among all elastomeric materials, Chemraz is the prime choice for the most challenging semiconductor applications. Superior quality, precision engineering and customisability result in less downtime and higher wafer processing yields.
Can Greene Tweed customise seals to suit specific semiconductor applications?
Yes, at Greene Tweed we offer a range of sealing solutions that can be tailored to meet your specific requirements. Our engineering team works closely with semiconductor manufacturers to design custom seals that match equipment specifications and deliver optimised performance.
What kind of semiconductor manufacturing processes benefit from Greene Tweed’s Chemraz sealing solutions?
Chemraz FFKM sealing solutions are ideal for a wide range of semiconductor equipment, such as
• Conductor etch
• Dielectric etch
• PECVD
• ALD
• RTP
• Wet cleans
• Chamber seals
• Slit valve and BSVs
• Pendulum and gate valves
• Electrostatic chuck and pedestal barrier seals
• Chemical delivery
Can Greene Tweed’s sealing solutions withstand aggressive cleaning and etching chemistries?
Absolutely! Chemraz exhibits exceptional chemical resistance, making it highly compatible with aggressive cleaning and etching chemistries used in semiconductor fabrication. It remains stable even when exposed to harsh plasma environments and reactive chemicals, ensuring optimal performance and longevity.
I want to implement Greene Tweed’s latest sealing solutions in my semiconductor application. How can I start the process?
To explore the benefits of FFKM sealing solutions tailored to your semiconductor equipment, reach out to our expert team at Greene Tweed. Our engineers are ready to talk about your specifications and provide technical guidance. We’ll keep working to iterate, improve and deliver high-quality sealing solutions to elevate your semiconductor manufacturing process.