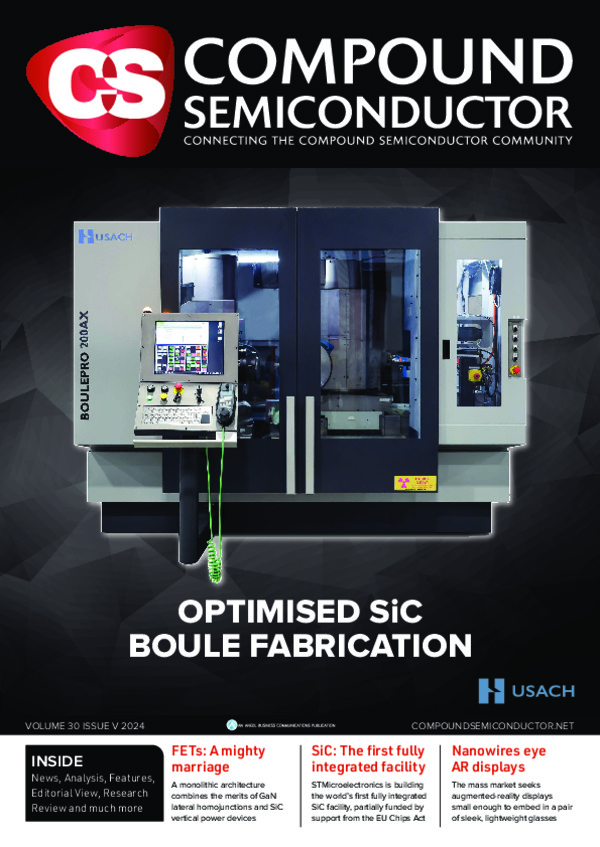
Optimised SiC boule fabrication

BY JAMES CARL FROM USACH
SALES OF SiC devices are rising fast, thanks to their increasing deployment in a wide array of applications, including electric vehicles and renewable energy systems. The uptake of these devices is driven by their superior properties, such as a higher thermal conductivity, greater efficiency, and the ability to operate at higher temperatures and voltages.
The ever-growing demand for SiC material and devices is motivating those working in this industry to innovate and enhance their production processes. Helping them in this endeavour is the BoulePro-200AX produced by our company, USACH. Designed to meet the evolving needs of the SiC industry, this industry-standard tool for fabricating boules is setting new benchmarks for efficiency and quality, while empowering manufacturers to meet the surging demand for high-quality materials. The valued strengths of the BoulePro-200AX make it an indispensable tool for every company striving to stay ahead in the dynamic SiC landscape.
Meeting growing demands
Historically, the leading producers of SiC substrates have been based in the US and Europe. But China is catching up fast, with its players making rapid advances in quantity, wafer size, and quality. Now the race is now on to establish readily available 200 mm material with a high quality that will provide chipmakers with the edge over their competition.
Illuminating boules with UV light exposes foreign polytypes.
The growth in the number of suppliers of SiC substrates, along with an increase in the size of this material, will help meet the rise in global demand. Ideally, against this backdrop there will be an increase in the range of applications where SiC serves, and a reduction in SiC substrate costs – goals where the BoulePro-200AX technology will play a pivotal role, by ensuring that the SiC boules are manufactured with high throughput to the highest standards of quality and precision.
To meet the increasing demand for our BoulePro-200AX, we have invested more than $720,000 in upgrading our facilities in Elgin, Illinois, a move that reflects our commitment to serving SiC manufacturers with cutting-edge technology and exceptional customer service. As part of this initiative, we have added 11 new assembly bays and more than 10,000 square feet of dedicated space, initiatives that boost our production capacity by up to 200 percent. Additionally, we have established a dedicated BoulePro demo/testing showroom, allowing our customers to see their machines in action and conduct part runoffs before delivery. These investments ensure that we are well-prepared to handle the growing interest in the BoulePro-200AX, which already has multiple units in operation running both 150 mm and 200 mm capable platforms. Over the coming months we have appointments in the diary for demonstrations with several potential customers.
Our facility upgrades are not just about increasing our capacity – they have also been introduced to enhance customer experience. Our new conference room and customer café provide a welcoming environment for our clients and help us foster stronger relationships and facilitate better communication. These improvements underscore our dedication to providing a comprehensive service that goes beyond just delivering a product, and reflect our commitment to ensuring our customers have all the support they need to maximise the benefits of the BoulePro-200AX.
The BoulePro200AX offers many advantages over conventional approaches for processing SiC material into pucks for producing substrates.
Exposing foreign polytypes
Recently, we have been collaborating with several SiC producers to integrate a module that detects foreign polytypes into the BoulePro. This addition allows operators to streamline and automate the identification and elimination of unwanted foreign polytypes during the grinding process. While the core methodology – using a UV lamp to highlight different polytypes – is well-established in the industry, integrating this capability into a grinding machine is a first.
During any stage of fabrication, the boule can be sent to the foreign polytype detection module. During inspection, the boule is held in the primary workhead on the seed side, and the module covers the workholding to block ambient light. The boule is rotated by the workhead inside the module containing both a UV light source and vision system that exposes and identifies the location of foreign polytypes, which are subsequently removed by additional grinding. This process can also be applied with the boule held on the dome side, to identify and remove polytypes located on the seed side.
Introducing the foreign polytype detection module, which enhances the SiC boule fabrication process by reducing the need for operator intervention, is part of our ongoing commitment to developing tools so that they remain at the cutting edge of technology. This is accomplished by anticipating future demands and providing customers with tools that will keep them competitive in a rapidly evolving market.
Speeding optimisation
As crystal growth technologies are highly proprietary, and for some producers have been developed in secret over decades, the as-grown boule can take many forms in terms of its geometry, defect location, and crystal orientation. Due to this, each customer that enters our facility brings material for a demonstration grind that requires a unique process development phase. Centred versus offset grinding, smaller or larger crystal orientation corrections, round versus non-round grinding, and the transfer of the boule from the primary chuck to the secondary chuck and vice versa during different stages of fabrication are just some of the factors that we need to consider when developing a particular customer recipe.
One new technology we are employing to streamline this process is a digital twin software package. The digital twin, an identical replica of the machine itself, allows complex sequences of events to be programmed and tested in advance of working with customer material. While there are several advantages to using the digital twin, optimisation of a particular customer material’s cycle time is a primary benefit and ultimately one of the main levers to driving down costs. As the machine movements in the digital twin are on a 1:1 time scale with reality, our team can explore different sequences of fabrication, while keeping in mind customer requirements, in digital space.
This trims costs and reduces the time it takes to come to an optimised recipe for a given set of as-grown boule conditions. As boules are highly valuable – they can be worth tens of thousands of dollars per boule, depending on height – it is easy to see the advantages of turning to digital space to support process optimisation.
The digital twin software package helps to streamline the processing of SiC.
Process methodology
Our fully automated BoulePro 200AX is already revolutionising SiC manufacturing by processing as-grown SiC boules into wafer-ready pucks without the need for gluing, external material setup, or manual intervention. This single setup machine is replacing multiple tools in the traditional boule fabrication process to create a more streamlined and efficient workflow.
Dramatically shortening the boule-to-puck conversion process is the BoulePro’s single-step, dual-plane compensation capability, enabled by integrating an X-ray diffraction tool. Compared with traditional methods, our BoulePro trims cycle time by up to nearly 95 percent, making it significantly more productive.
Additional strengths of the BoulePro are its automatic tool changers, and its flexible design, accommodating various boule geometries and customer requirements. These strengths make the 200AX the most efficient, flexible, and cost-effective tool for the growing SiC market.
To ensure that the boule is securely held during the grinding process, our tool employs advanced gripping techniques. Both workheads utilise vacuum technology to secure the part, while OD gripping jaws hold the outside of the part during face grinding. This dual support system enables aggressive grinding, shortening fabrication cycle times without damaging the part. In comparison, traditional methods are cumbersome, involving gluing the part to a spindle.
By eliminating the need for multiple machines, reducing the number of handling steps, and turning to automation and integration of advanced technologies, our BoulePro minimises the risk of inadvertent damage to the part and the potential for human error during processing. This leads to higher yields and better-quality products, which are critical for the demanding applications that rely on SiC substrates. The machine’s ability to perform all the necessary grinding operations in a single setup also trims the overall footprint of the manufacturing process, saving valuable space in production facilities.
The key benefits of our ground-breaking tool, including streamlined automation, enhanced process repeatability, reductions in costs and manufacturing footprint, and a higher level of accuracy, are listed in the text box “Six key strengths of the BoulePro 200AX”.
Expanding applications
As the BoulePro gains recognition in the SiC industry and gains ground as the preferred process tool for manufacturing SiC substrates, its applications are expanding. Note that its capability to identify crystalline structures and align them for specific purposes is not limited to SiC. The BoulePro can also serve in the silicon semiconductor space, where there are opportunities for this machine to shape single-crystal silicon at the ingot level, and process other silicon-based parts. One application that’s being explored is the pairing of the BoulePro with another machine tool in a fully automated cell to create critical parts for silicon crystal growth.
As other compound semiconductors garner more interest, such as the ultra-wide bandgap material AlN, the BoulePro is cementing its position as the fabrication machine of choice. Like SiC, AlN requires precise machining into wafer-ready pucks with specific orientations. The BoulePro’s configuration and expertise in handling hard, brittle, and stressed materials make it ideal for shaping as-grown crystals into ready-to-wafer forms.
Savings on multiple fronts are possible with the BoluePro200AX.
An industry standard
The widespread adoption of the BoulePro-200AX by leading SiC producers all over the world is underscoring its status as the premier solution for boule-to-puck conversion. From North America and Europe to emerging markets in Asia, this tool is setting benchmarks for efficiency, repeatability, and cost-effectiveness.
Its unparalleled efficiency is revolutionising traditional processes. The BoulePro streamlines production, reduces cycle times, and cuts operational costs by integrating automation, precision machining, and advanced materials handling. Consistent production of high-quality SiC pucks results, enabling manufacturers to meet stringent standards and customer demands confidently.
Thanks to its ground-breaking repeatability, the BoulePro-200AX ensures uniformity and consistency, essential traits for maintaining product integrity. Offering precise control over key parameters minimises part damage, safeguarding SiC products’ reputation and reliability.
The transformative potential of the BoulePro-200AX is well understood by our parent company, Hardinge, which recognises the challenges SiC producers face in post-growth boule fabrication, as well as the need for specialised machining expertise. Current Hardinge CEO Greg Knight understands the struggles of SiC fabrication well as he was formerly the CEO of GTAT, a SiC crystal growth company that was acquired by Onsemi.
As well as meeting their immediate needs, SiC manufacturers that invest in the BoulePro-200AX are positioning themselves for long-term success. Our tool’s advanced features and robust performance, coupled to our drive to continue to add innovative features and technologies to this platform, will ensure that it remains a critical component to produce SiC and other upcoming semiconductor materials for years to come.
Putting it succinctly, our BoulePro-200AX is more than just a machine – it’s a catalyst for progress in the SiC industry. Offering innovative design, comprehensive capabilities and proven results, this tool is an essential asset for any SiC manufacturer looking to stay competitive in a rapidly changing market. With the BoulePro-200AX, we are not just setting the standard; we are defining the future of SiC fabrication.