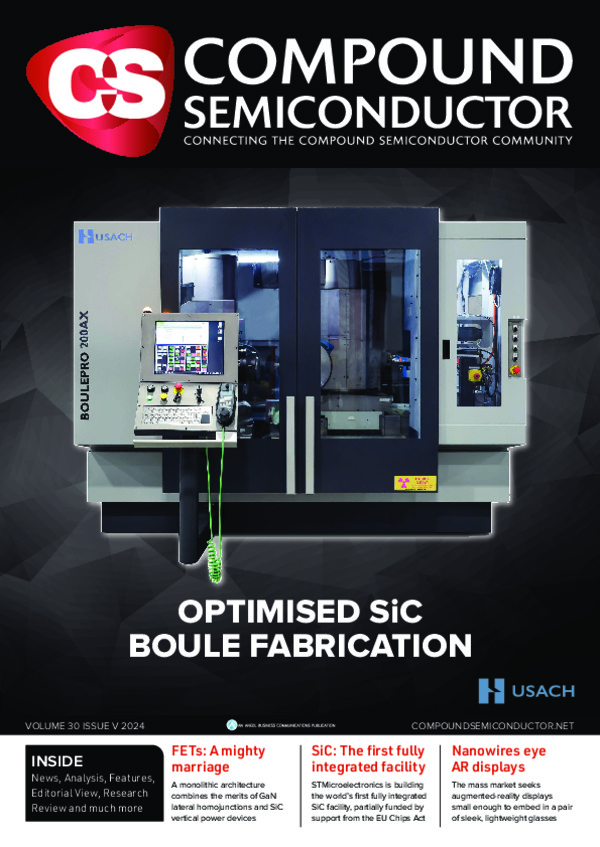
Printing microLED displays
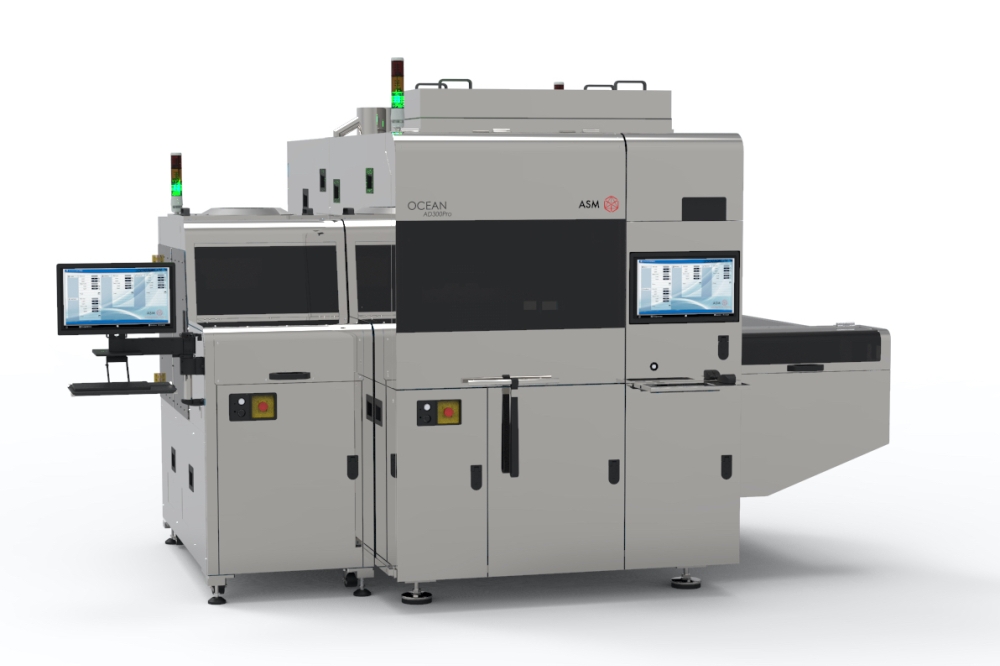
Populating cartridges with microLEDs to print emitters on backplanes promises to drive a revolution in display technology.
BY RICHARD STEVENSON, EDITOR, CS MAGAZINE
Displays based on the microLED have a great deal of potential, but face formidable challenges. The appeal of this technology is a combination of tremendous colour quality and brightness, an exceptional degree of ruggedness, and high levels of efficiency, which extend the battery life of portable devices. But producing this class of display involves positioning millions and millions of microLEDs on a backplane, followed by their connection to drive electronics – and transferring all these pixels with sufficient speed is far from trivial.
Despite several years of substantial investment, the two leading techniques for assembling microLED displays – pick-and-place and laser-based transfer – are struggling to make a significant impact. This leads one to wonder whether further effort on these fronts will reap reward. Or does it make more sense to pursue an alternative approach that avoids their weaknesses?
Arguing for the latter, and championing the production of displays with a printing process, is Reza Chaji, CEO of VueReal. He has much valuable experience in this sector, having previously led Ignis Innovation, a developer of technology that’s improved the uniformity and lifetime of pixels used in OLED displays. These advances now feature in LG’s OLED TVs.
In 2016, Chaji started VueReal, which has a 60-strong team that made a big splash at Display Week 2024. At this show, held in mid-May 2024, the company championed it printing technology and unveiled two complimentary technologies: dynamic quantum-dot patterning, and a method to increase the fidelity of displays with a liquid-crystal-on-silicon backplane.
The foundation for all this promise is VueReal’s proprietary cartridge technology, which allows microLEDs to be held very tightly before they are released to the display substrate by controlling electrostatic forces. The cartridges can also integrate sensors and other forms of chip, using a three-dimensional stacking approach.
“Our main focus has been on transfer – how to integrate devices from the original wafers onto the substrate with high yield, high throughput,” remarks Chaji. He argues that VueReal’s laser-free process is relatively simple and low in cost.
One option for producing displays with this company’s technology is to load the cartridge with one colour of microLED, print these devices, and then load and print with each of the two other primary colours. But it’s also possible to populate the cartridge with all three colours of microLED, an approach demonstrated by VueReal a couple of years ago.
Today, most of the company’s customers prefer to just load one colour of microLED onto the cartridge, as this approach offers greater control over colour uniformity and results in a higher yield. But as the printing process matures, Chaji expects customers to populate cartridges with red, green and blue microLEDs, to trim the time taken to produce displays.
The cartridges are capable of holding millions of microLEDs. “With one cartridge, we can populate 16 smartwatches,” says Chaji.
VueReal claims that its cartridge-based approach offers cost, yield, throughput and performance benefits over the leading alternative methods.
The problems of pick-and-place
Before developing the printing process, Chaji and his colleagues carefully considered the potential of both pick-and-place and laser-based transfer for high-volume production of displays. They reasoned that to make an impact, the process for transferring microLEDs to a backplane would have to be fast enough to allow this technology to be competitive with the manufacture of displays based on OLEDs, which are transferred to glass in less than 10 minutes. The team concluded that the transfer of microLEDs would have to involve multiple heads, leading to many moving parts and hampering alignment.
One advantage of printing over pick-and-place is speed, with the time taken to populate an area falling from between 15 and 25 seconds to less than 8 seconds. Another benefit is the efficient use of material. With pick-and-place, as well as laser-based transfer, microLEDs are taken from square-shaped areas, preventing many devices from ever being used. That’s not the case with the VueReal printing process, which uses near all of the wafer. What’s more, devices can be packed very close together – a spacing of less than 2 µm has been demonstrated.
Regardless of the transfer process, display manufacture is impeded by defects and non-uniformity in microLED wafers. But this is far less of a concern when using the VueReal approach, as losses are minimised by employing multiple, small cartridges, and scrutinising wafers with a combination of visual inspection, photoluminescence and selective electroluminescence. While some defects still get through, by driving down numbers the cost to address them is not prohibitive. “If you have hundreds of defects, it's easy to repair,” says Chaji.
What may raise an eyebrow to many within our industry is that most of the defects that engineers at VueReal encounter don't come from the microLEDs, but the backplane. To address this, the company has developed an inspection tool to expose those defects, so that they can be eliminated prior to transfer.
The allure of the laser
During considerations of laser-based transfer, Chaji and his colleagues concluded that a raster-based scanning approach fails to deliver sufficient throughput, and any attempts to address this with multiple beams requires incredibly complex optics. This led the team at VueReal to invent a patented solution involving a shadow mask and mass exposure. However, even with this refinement, laser-based approaches still involve substantial capital expenditure, high operating costs, and issues associated with material costs.
By addressing these weaknesses with its printing approach, VueReal’s technology is not just suitable for high-volume production. It is also better suited for making customised products, because the tool is easy to operate, and offers low maintenance and low capital expenditure.
At the heart of VueReal’s technology is the printing of microLEDs, which are loaded on a cartridge.
VueReal is not focusing on one particular market to promote its printing process. Instead, it views its user-friendly technology as suitable for the manufacture of many different products, including htose that serve in the automotive, consumer electronics and healthcare secrors. Note that the company’s patented technology also extends beyond microLED displays and is applicable to broader micro semiconductor products, such as micro-sensors.
VueReal is heavily engaged with many customers in the automotive market, where its printing technology can be used to make displays with various degrees of transparency. “MicroLEDs are inherently transparent,” says Chaji, adding that if an opaque display is required, that’s also possible.
The other markets offering the greatest potential today for VueReal are wearables and augmented-reality. For the latter, miniaturisation is in high demand, with an end goal of red, green and blue emitters sitting side-by-side at a 3 µm pitch.
Chaji believes that it’s going to take a long time to reach that target, and that the objective might be easier to realise with VueReal’s recently unveiled colour fusion technology. This combines slightly larger, more efficient microLEDs with liquid-crystal-on-silicon technology that enhances resolution. The result is a competitively priced, high-resolution display.
To help makers of displays based on the microLED trim their costs when adopting VueReal’s technology, the company offers many options to its customers. It can provide all the tools for manufacture, or just the printer, if a company is already active in producing displays. This accommodating approach will be welcomed with the microLED display industry, which must now step beyond hype and start making money.