Axus says CMP tool offers lowest cost of ownership
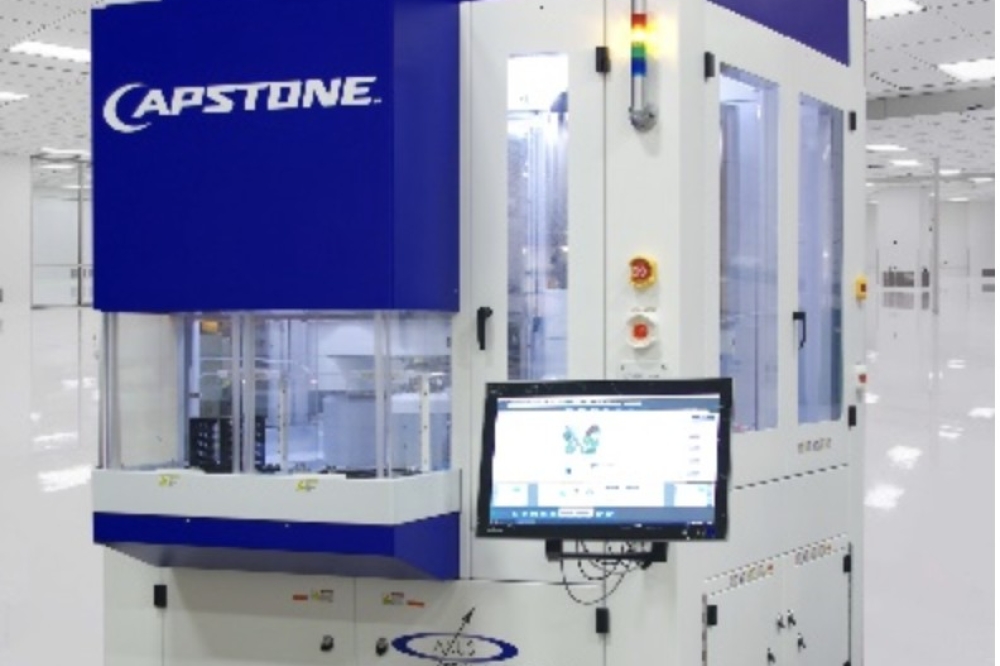
Axus Technology, a provider of chemical mechanical planarisation (CMP) equipment, has announced its Capstone CS200 platform tools offer the industry’s lowest cost of ownership (CoO) for CMP processes on 200mm SiC wafers.
The company says that compared to its closest competitor, the small-footprint Capstone delivers twice the throughput at less than half the total cost per wafer.
“Many 200mm fabs are looking to upgrade their installed base of CMP tools to products with leading-edge capability and functionality. Our ability to deliver industry-low CoO further underscores our strong market position and capacity to support this shift,” said Axus Technology CEO Dan Trojan.
He added: “Capstone features a streamlined workflow and integrated cleaning capability, so it requires half the process steps of older CMP tools. This allows customers to greatly lower their capex investment.”
Figures from the company say that compared to its closest competitor, Capstone offers throughput of 2.5x wafers per hour; 60 percent lower power consumption; 80 percent lower DI water consumption; 45 percent smaller footprint; 65 percent lower capex cost per wafe; and 50 percent lower total cost per wafer.
Another factor contributing to Capstone’s lower CoO is its built-in Process Temperature Control (PTC) technology, which enables processing at higher pressures and speeds without exceeding temperature limits of polishing pads and other sensitive components. This feature is vital for SiC and other materials with high hardness and planarisation challenges that necessitate more aggressive process conditions.
The company says it will be on hand to discuss CMP advantages further at the upcoming International Conference on Silicon Carbide and Related Materials (ICSCRM), Sept. 29-Oct. 4, at the Raleigh, Convention Center, North Carolina, USA.
Secure Your Hydrogen Supply
A study supply of high-purity hydrogen is critical to semiconductor fabrication. Supply chain interruptions are challenging manufacturers, leading to production slowdowns and stoppages. On-site hydrogen generation offers a scalable alternative for new and existing fabs, freeing the operator from dependence on delivered gas.Plant managers understand the critical role that hydrogen plays in semiconductor fabrication. That important job includes crystal growth, carrier gas, wafer annealing, and in the emerging Extreme UV Lithography (EUV) that will enable new generations of devices. As the vast need for semiconductors grows across all sectors of world economies, so does the need for high-purity hydrogen.
Take control with Nel on-site hydrogen generation.
Read more